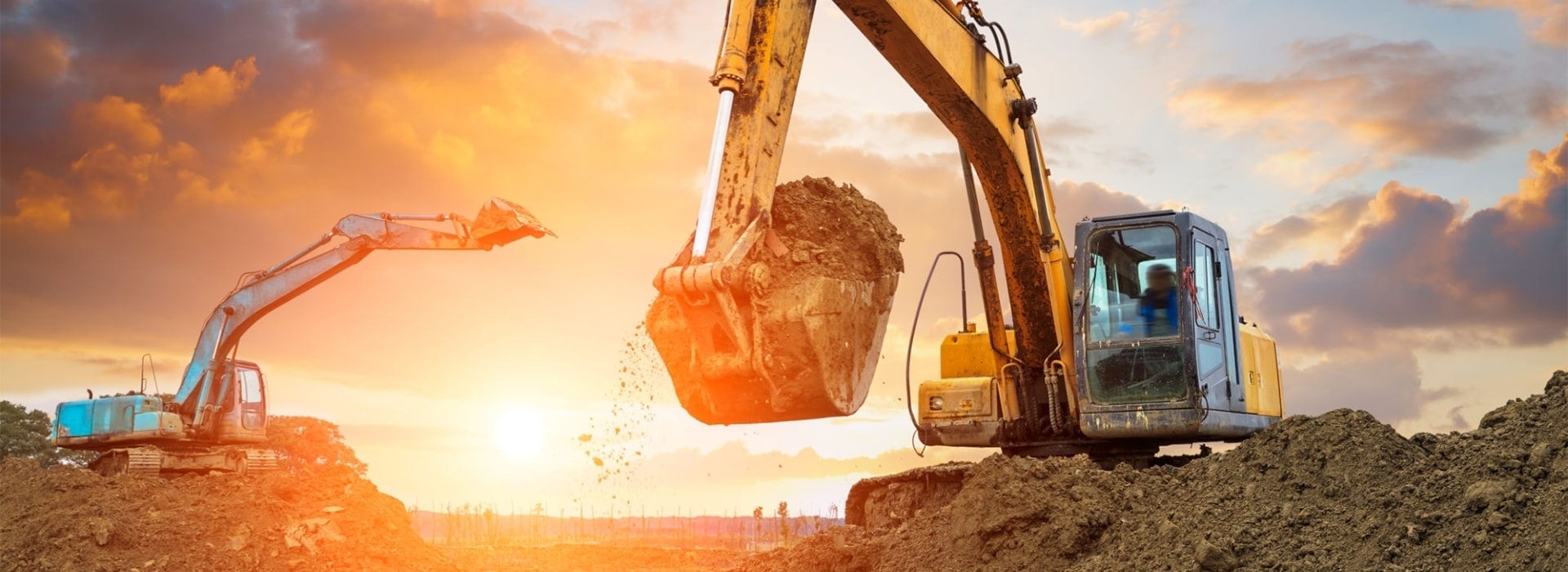
Casting segment ring gear for rotary kiln
PRODUCT PARAMETERS
Description
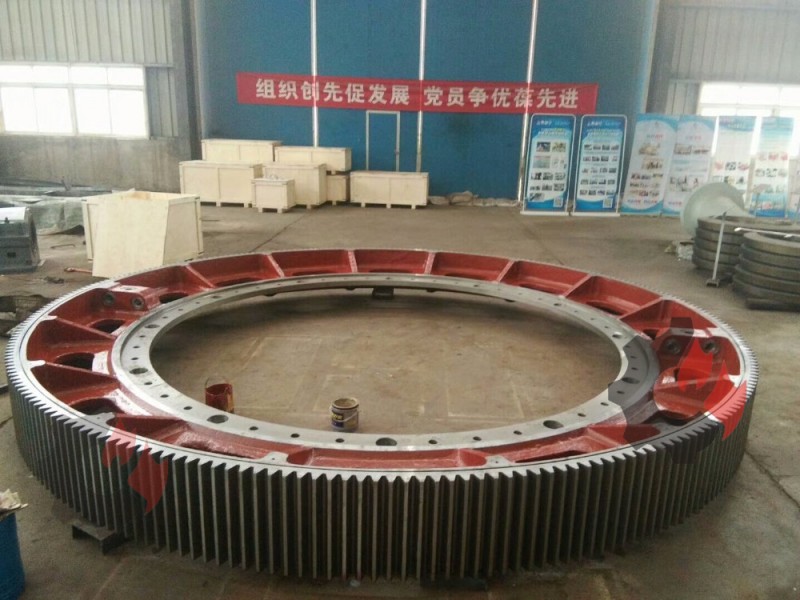
1: Mold making:
Confirm customer drawings and requirements. Make the sand mold or metal mold required for casting. This step requires high precision to ensure the accurate size of the casting.
2: Material preparation:
Select suitable raw materials. Commonly used ones are ZG310-570, ZG340-640, etc. These materials have good mechanical properties and wear resistance. Prepare the smelting furnace, additives and other auxiliary materials.
3: Melting and pouring:
Put the selected raw materials into an arc furnace or induction furnace for smelting, and add necessary alloy elements to adjust the chemical composition.
When the molten iron reaches the appropriate temperature (usually around 1500℃), remove the slag and deoxidize, and then inject the pure molten iron into the pre-prepared sand mold or metal mold.
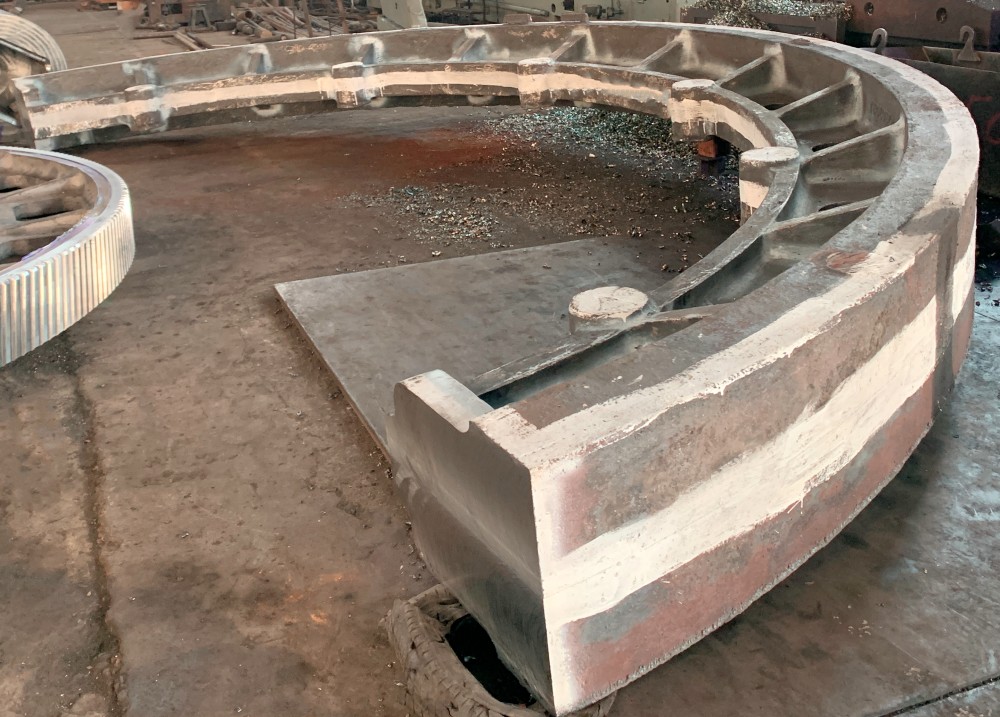
4: Cooling and mold opening:
After pouring, wait for the casting to cool naturally to room temperature. It is important to control the cooling speed in this process. Too fast may cause internal stress to increase and affect product quality.
After cooling, open the mold and take out the casting.
5: Cleaning and heat treatment:
Clean the sand, scale and other impurities on the surface of the casting, and conduct a preliminary inspection of the casting.
According to the material type and product requirements, select appropriate heat treatment processes, such as normalizing, annealing, quenching and tempering, etc., to improve the organizational structure and mechanical properties of the casting.
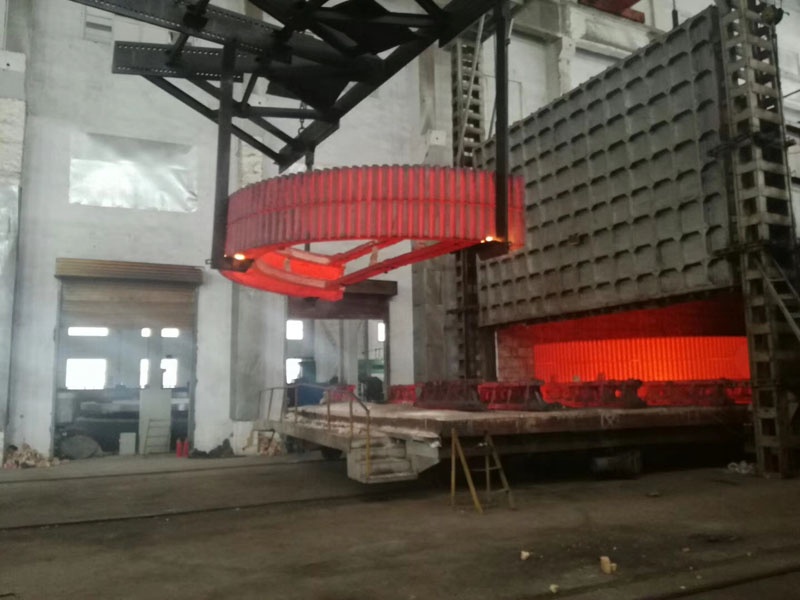
6: Roughing and finishing:
Rough machining of the heat-treated castings to remove excess materials close to the design size.
Fine machining, including turning, grinding and other processes, especially the tooth-shaped part, requires the use of special equipment for precision machining to ensure that the accuracy meets the requirements.
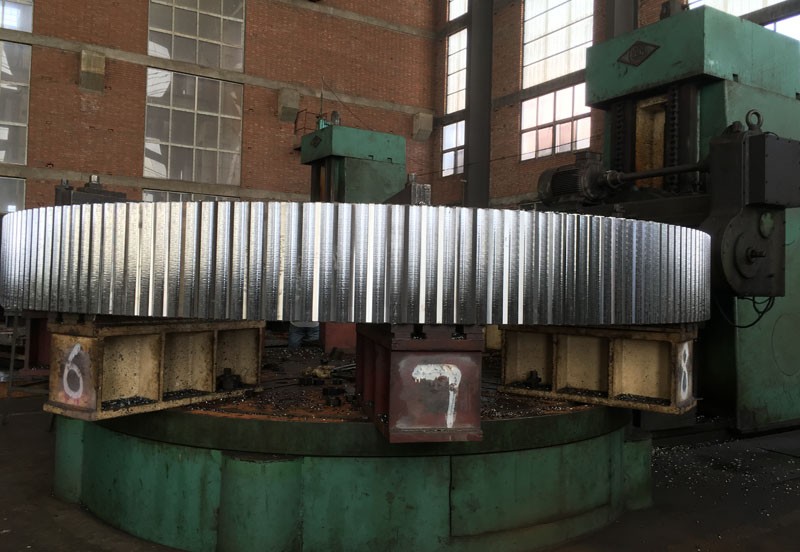
7: Inspection and testing:
After the processing is completed, a comprehensive quality inspection is carried out, including dimensional inspection, hardness test, flaw detection inspection, etc., to ensure that there are no defects such as cracks and pores.
If necessary, a load test is carried out to verify whether its working performance meets the design standards.
8: Surface treatment and painting:
Finally, the finished product is surface treated according to customer needs, such as spray painting, anti-corrosion treatment, etc., to enhance corrosion resistance and aesthetics.
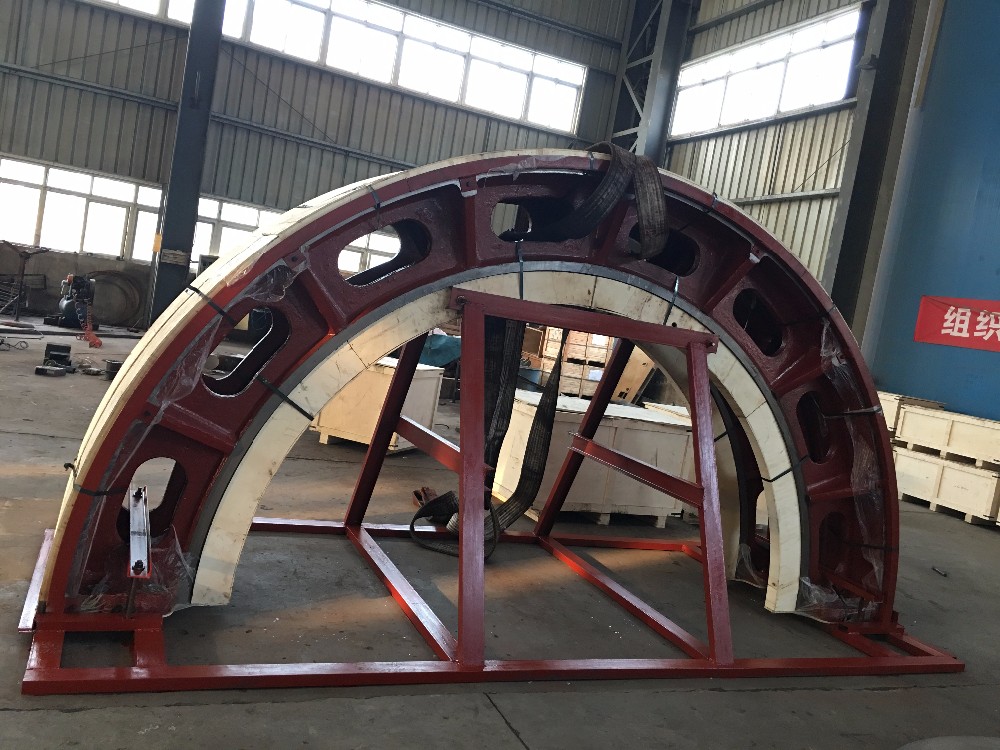
How to prevent early damage to the large ring gear?
1: Material selection and heat treatment:
Select high-strength, wear-resistant alloy steel as the manufacturing material, and use appropriate heat treatment (such as quenching and tempering) to improve its hardness and toughness, thereby enhancing fatigue resistance.
2: Optimized design:
Consider stress concentration issues during the design phase, use smooth transition designs to disperse stress as much as possible, and avoid sharp corners or sudden changes in structures.
Use tools such as finite element analysis (FEA) to predict potential high stress areas and strengthen the design in these areas.
3: Precision processing and assembly:
Ensuring the machining accuracy of the large ring gear and its mating parts (such as pinions), especially the tooth profile accuracy, is very important to reduce additional stress during operation.
During the installation process, accurate alignment must be ensured to avoid excessive local wear caused by misalignment.
4: Effective lubrication:
Using the right lubricant and changing the lubricant regularly according to the equipment manufacturer’s recommendations can significantly reduce friction and wear by maintaining good lubrication conditions.
Check the effectiveness of the lubrication system regularly to ensure that there is sufficient oil and no contamination.
5: Regular inspection and maintenance:
Establish a comprehensive inspection and maintenance plan, and regularly conduct visual inspections, flaw detection, and wear assessments on the ring gear.
Repair minor problems found in a timely manner to prevent them from turning into serious failures.
6: Control the working environment:
Minimize the entry of dust and particles into the working area of the gear ring, as these impurities will accelerate wear.
Maintain a suitable working temperature. Too high or too low temperature may affect material properties and cause early damage.
7: Reasonable operation:
Avoid overloading, operate the equipment according to design parameters, and reduce unnecessary shock and vibration.
The starting and stopping process is smooth, avoiding instantaneous high load caused by sudden braking or rapid starting.
REQUEST A QUOTE
RELATED PRODUCTS
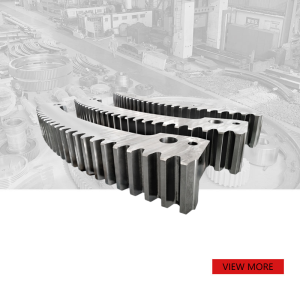
35CrMo Forging Mining large dimeter 12 Segment Arc Tooth
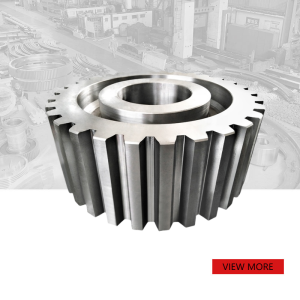
Spur gear forging high quality large diameter pinion gear
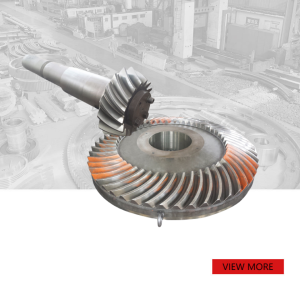
Forging high quality Large diameter Bevel gear
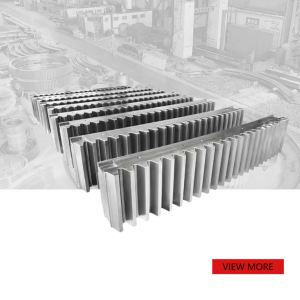
Customized 35CrMo forged steel segmented large diameter ring gear
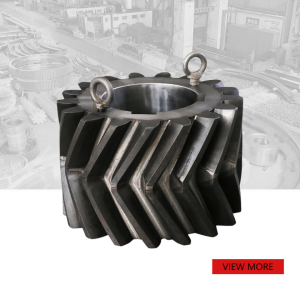
Custom forging double helical gear
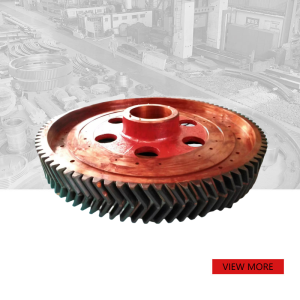