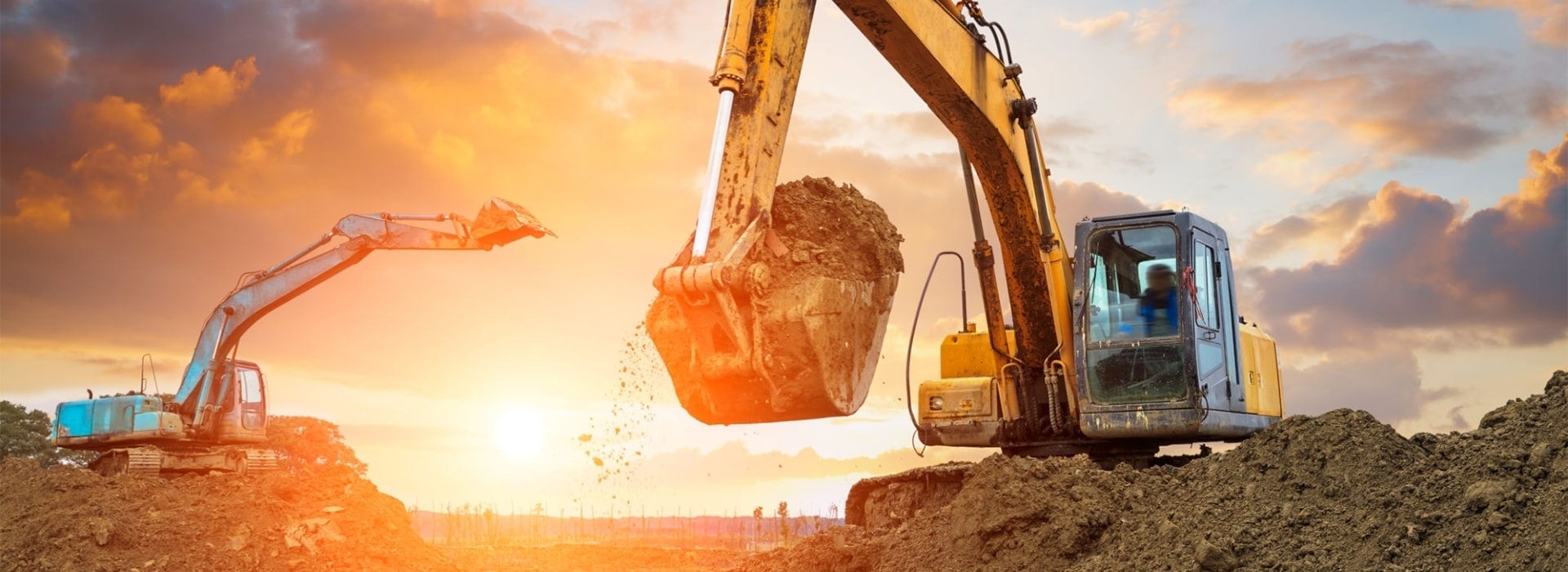
High quality casting large helical gear wheel
PRODUCT PARAMETERS
Description
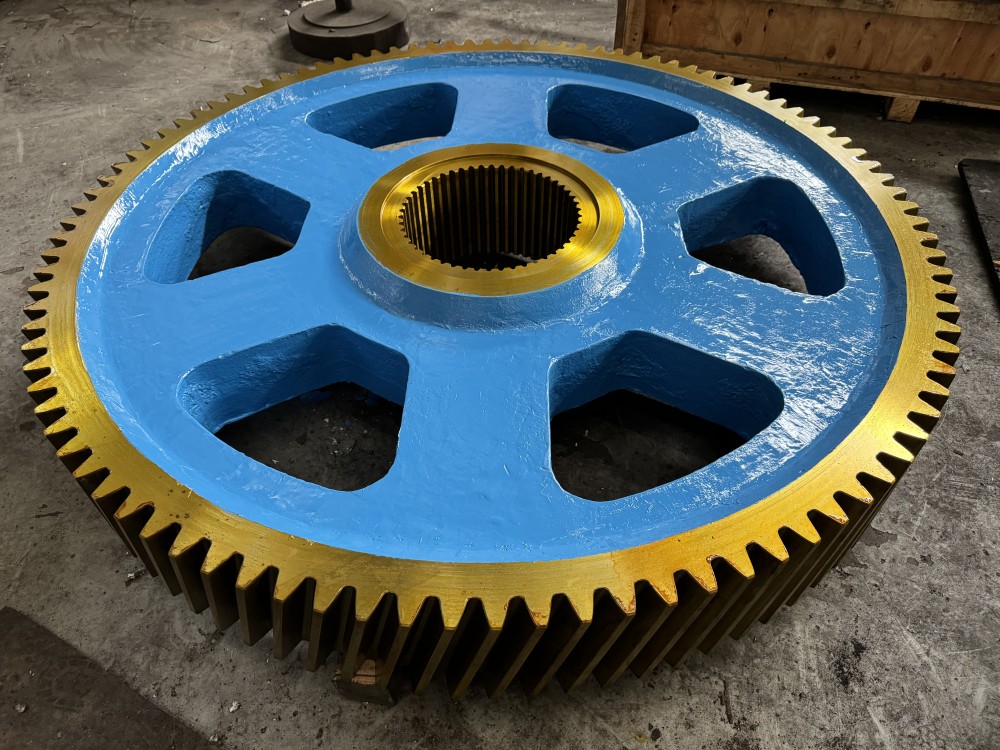
Casting gear wheel production process:
1. Mold making
For the blanks of large cast iron gears, sand casting is one of the most commonly used casting methods. The mold can be made of wood, metal or other high-temperature resistant materials to withstand the pressure and temperature of molten metal.
2. Melting and pouring
The selected metal material (such as cast iron, steel, etc.) is placed in a furnace and heated above its melting point to become liquid. The molten metal is then poured into the pre-prepared sand mold or metal mold through a pouring system. In this process, it is necessary to ensure that the metal liquid evenly fills the cavity in the mold to avoid bubbles or inclusions.
3. Solidification and cooling
After pouring, the metal will gradually cool and solidify in the mold. In order to ensure the quality of the casting, it is crucial to control the cooling rate. Rapid cooling may lead to increased internal stress, while slow cooling helps to reduce this stress, but may lead to a longer production cycle.
4. Demolding and cleaning
When the casting is completely cooled, it is removed from the mold and the sand or other residues attached to the surface are removed. This process may require the use of knocking, sandblasting or chemical cleaning.
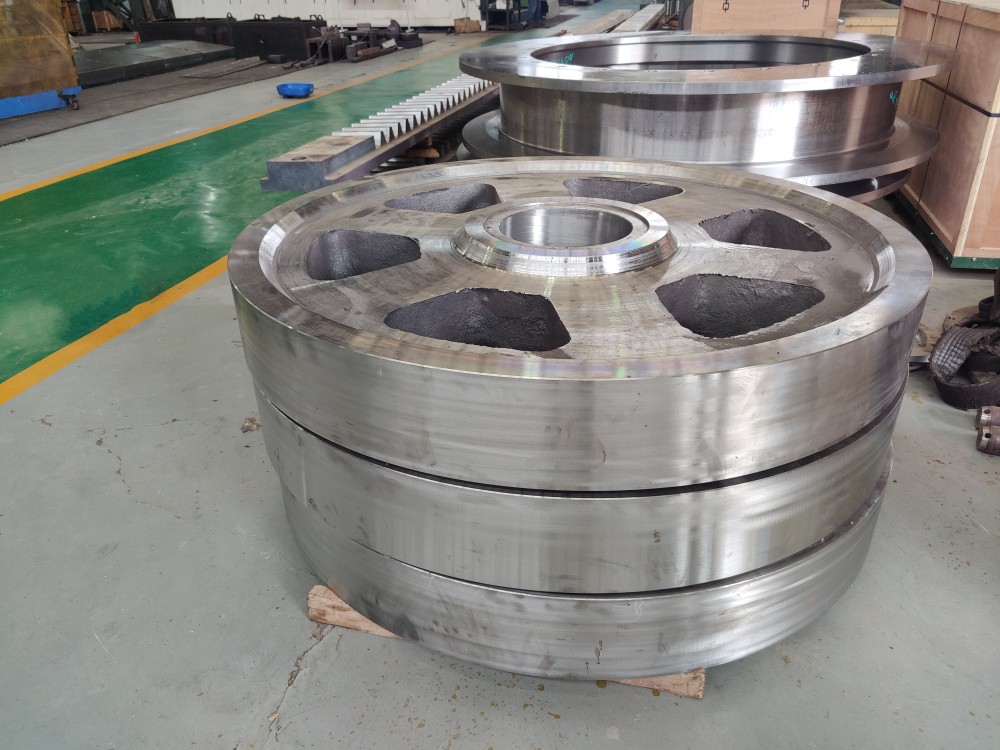
5. Rough machining
The preliminary machining stage mainly involves rough machining of the casting, such as turning, milling, etc., to remove excess material and bring the workpiece close to the final design size. This step also includes the precise positioning of key parts (such as apertures, end faces, etc.).
6. Heat treatment
Heat treatment is to improve the mechanical properties of the gear, such as hardness, wear resistance and toughness. Depending on the requirements, a variety of heat treatment processes such as quenching and tempering may be used.
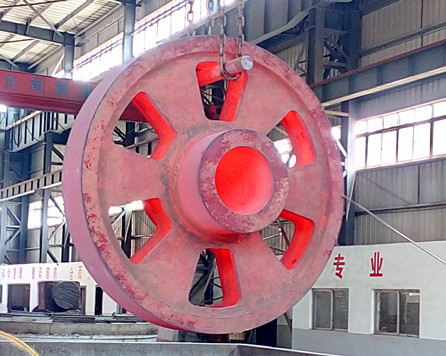
7. Finishing
After heat treatment, further finishing steps such as grinding and lapping are usually required to achieve the final design accuracy and surface finish.
8. Gear cutting
If the tooth shape is not directly formed during casting, it is necessary to use special machine tools (such as hobbing machines, gear shaping machines, etc.) to cut the gear at this stage to form a precise tooth shape.
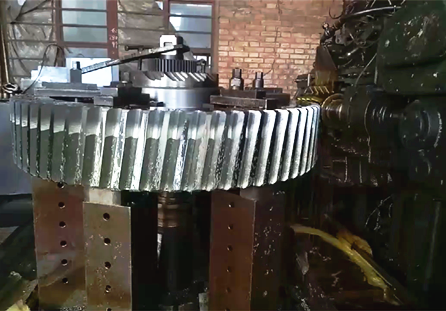
9. Surface treatment and inspection
The final step is to perform surface treatment (such as plating, coating, etc.) on the gear to enhance its corrosion resistance or aesthetics, and conduct comprehensive quality inspection to ensure that the product meets all technical specifications.
Key points to consider when choosing a casting process:
1: Sand casting is preferred:
Sand casting is the most commonly used casting method and is suitable for castings of various shapes and sizes. It has the advantages of low cost, simple production process and short production cycle.
When the wet mold cannot meet the requirements, clay sand surface dry sand mold, dry sand mold or other types of sand molds can be considered.
2: Consider the production batch:
If it is a factory with mass production, conditions should be created to adopt technologically advanced modeling and core making methods to improve efficiency and quality.
For small batches or single-piece production, manual modeling may be more flexible and economical.
3: Adapt to the accuracy and surface finish requirements of castings:
If there are high requirements for the accuracy and surface finish of castings, high-precision casting methods such as precision casting (such as investment casting) or pressure die casting can be selected.
Although these methods have a large initial investment, they can provide better dimensional accuracy and surface quality.
4: Choose a method that matches the factory conditions:
The factory should choose the most suitable casting process based on its own equipment conditions, employee skill level and other factors.
For example, if you have an efficient high-pressure molding machine production line, it is suitable for fast and high-precision molding production.
5: Take economic benefits into account:
It is necessary to evaluate the cost-effectiveness of each casting method, including initial investment, operating costs, mold life, etc.
For processes such as low-pressure casting, die casting, centrifugal casting, etc., which have expensive equipment and molds, they are usually only suitable for mass production because these processes can reflect good economic benefits in large-scale production.
6: Special performance requirements:
According to the specific application environment and performance requirements of the casting (such as heat resistance, wear resistance, mechanical strength, etc.), select the corresponding material and casting process.
Some alloys can only be processed by specific casting processes, such as investment casting is suitable for casting refractory alloys.