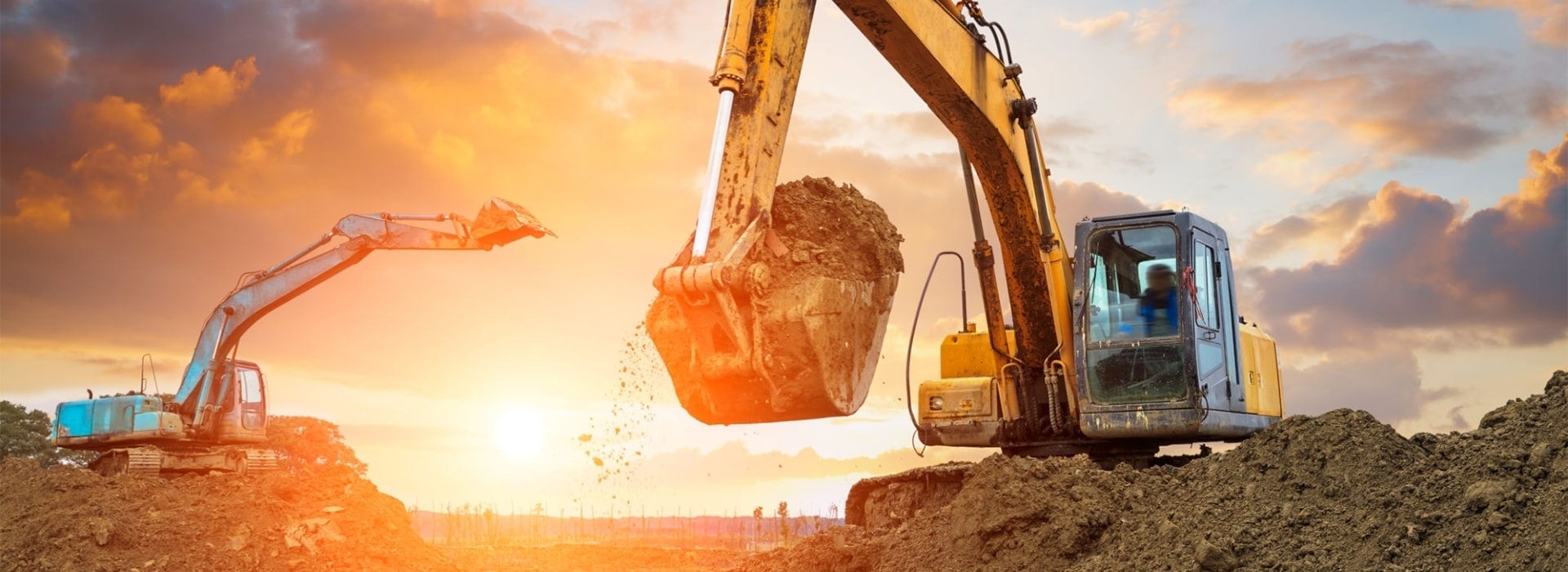
Welding ball mill spare parts Mill connection housing
PRODUCT PARAMETERS
Description
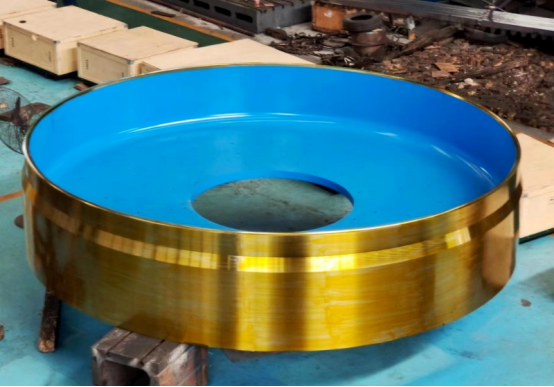
Processing process:
1. Forging
Heat the metal to a certain temperature and then forge it to eliminate defects such as pores and shrinkage in the cast metal, refine the metal grains, and make the structure dense, thereby improving strength, toughness and fatigue resistance. Forging can more accurately control the shape and size and reduce material waste. The surface of forged parts is usually rough and requires subsequent processing.
2. Rough machining
Rough machining is an important part of the mechanical manufacturing process. It is a preliminary processing of the forged blank to remove excess material and prepare for subsequent fine machining.
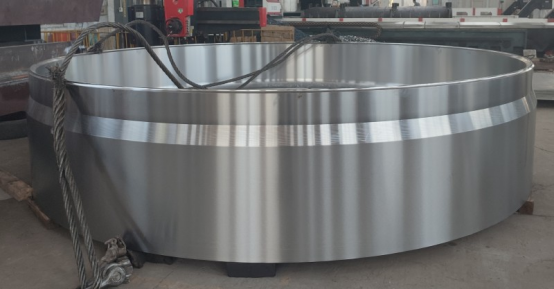
3. Flaw detection
After rough machining, we will perform flaw detection on the product to ensure that the parts meet the performance and safety standards.
4. Quenching and tempering
Quenching and tempering is a heat treatment process consisting of two steps: quenching and high-temperature tempering. It is mainly used to improve the comprehensive mechanical properties of the material (such as strength, hardness, toughness and wear resistance) and provide a good foundation for subsequent fine machining and final use.
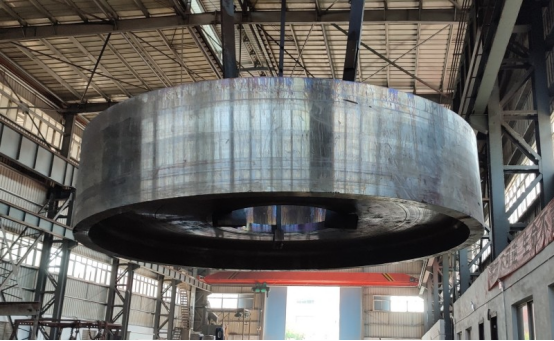
5. Semi-finishing
(1) Improve dimensional accuracy:
Semi-finishing can further reduce the dimensional deviation of the part and approach the final design size.
(2) Improve surface quality: The surface of the part after quenching and tempering may become rough due to heat treatment, and semi-finishing can make it smoother.
(3) Eliminate heat treatment deformation: The slight deformation that may occur during the quenching and tempering process can be corrected by semi-finishing to ensure the shape and position accuracy of the part.
(4) Reduce finishing allowance: Semi-finishing can remove most of the machining allowance, reduce the workload of subsequent finishing, and improve efficiency.
(5) Verify the quenching and tempering effect: During the semi-finishing process, the cutting performance can be used to determine whether the quenching and tempering treatment has achieved the expected effect.
6. Assembly welding
The outer ring is forged 42CrMo alloy steel, the web part is Q235, and the web thickness is 90mm. It needs to open a U-shaped groove for double-sided welding. The welding area is relatively long, with a diameter of 4.5 meters and a circumference of more than 14 meters. In order to reduce welding stress and deformation, staggered intermittent welding is required. At the same time, the entire workpiece must be heated to 200℃ before welding. The welders need to wear heat-insulating clothing. Due to the large amount of welding, when the welding is stopped in the middle, the entire workpiece needs to be placed in a heating furnace for insulation until the welding is completed. The entire workpiece is annealed and then UT flaw detection is performed on all welding positions.
7. UT
After the parts have been semi-finished and the dimensional accuracy and surface quality have been improved, further check whether there are defects inside the parts (such as cracks, pores, inclusions, etc.) to ensure the quality and reliability of the parts.