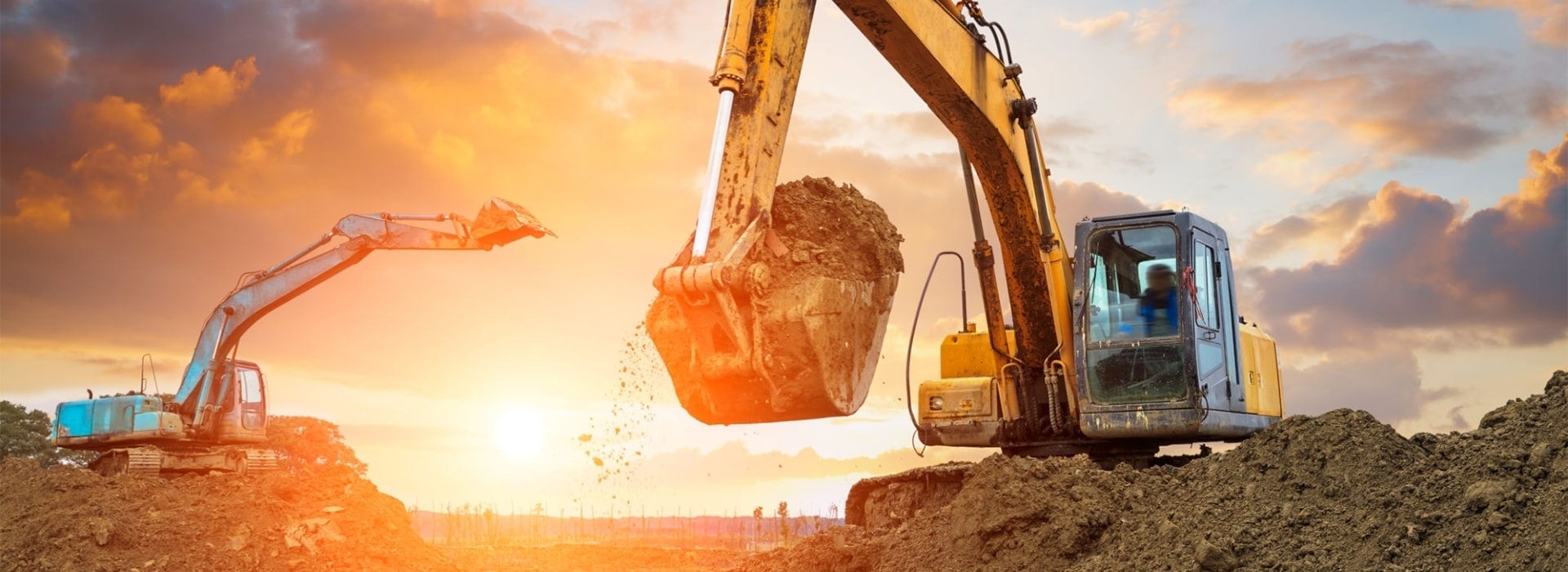
Custom large diameter rolling steel hot forging ring
PRODUCT PARAMETERS
Description
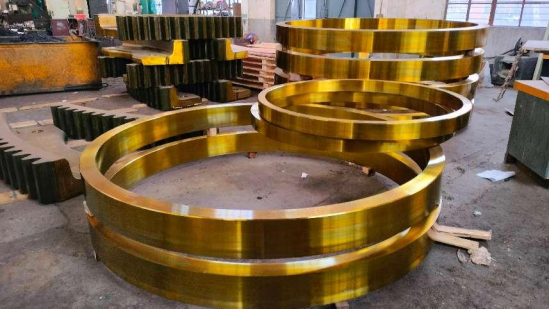
Which mining equipment are forged rings used in: crushers, mills, conveying equipment, screening equipment, lifting equipment, drilling equipment
Crushers: In equipment such as jaw crushers and cone crushers, forged rings may be used in the rotor part or as supports and connectors. They help to achieve efficient crushing of ore and can withstand huge pressure and impact.
Mills: Forged rings are also used in certain key parts of equipment such as ball mills and autogenous mills. For example, as support rings at both ends of the mill cylinder, or as fasteners connecting different parts, ensuring that the mill can operate stably and grind ore effectively.
Conveying equipment: In belt conveyors and other types of material handling systems, forged rings can be used to manufacture roller assemblies. These rollers support and drive the conveyor belt, and are crucial to the efficiency and stability of the entire conveying system.
Screening equipment: In screening devices such as vibrating screens, forged rings can be used to enhance structural strength, especially in those places where they need to withstand heavy loads and frequent vibrations.
Lifting equipment: In heavy machinery such as mine hoists, forged rings are used as part of drums or other key components to ensure safe and reliable lifting of personnel or materials.
Drilling equipment: In some large drilling rigs, forged rings may also be used in rotating heads or other parts that require high wear resistance and impact resistance.
Forged ring processing procedures
1. Material preparation: Select suitable metal materials and make preliminary cuts to form a blank suitable for forging.
2.Heating: Heat the blank to an appropriate temperature, which usually needs to reach above the recrystallization temperature of the metal to facilitate subsequent plastic deformation. The heating process is completed in a special heating furnace.
3.Upsetting: The heated blank is changed in shape and size by upsetting to prepare for the subsequent punching and expansion.
4.Punching: Punch a hole in the center of the blank to form a preliminary ring structure of the material.
5.Free forging expansion: The ring blank is further expanded using the horse bar expansion method. This method is suitable for small batches and small ring production.
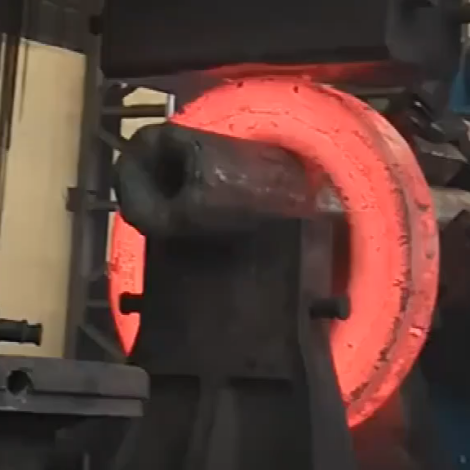
6.Ring rolling: This is the main method for manufacturing large and high-quality rings in modern times. The ring rolling machine is used to continuously and partially plastically deform the ring, gradually expanding the diameter and reducing the wall thickness while maintaining a precise cross-sectional profile.
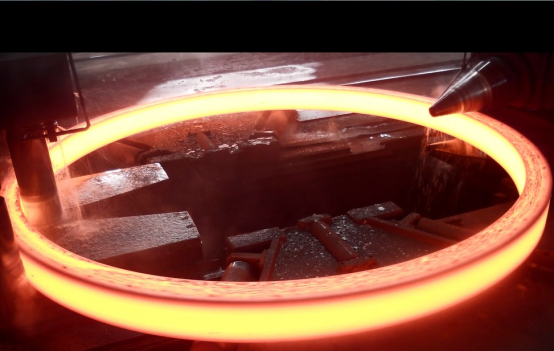
7.Heat treatment: In order to improve the mechanical properties of forged rings, such as hardness, strength and toughness, it is usually necessary to heat treat them, including quenching, tempering and other processes.
8.Machining: According to design requirements, forged rings may need to be machined by turning, drilling, grinding and other machining to achieve precise size and shape.
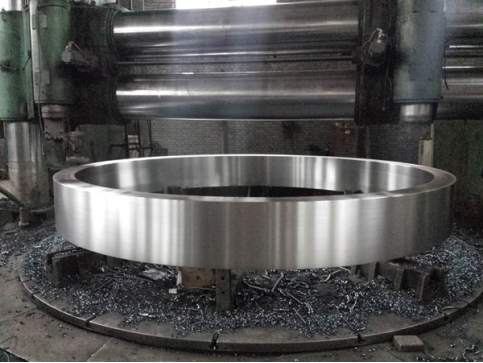
9.Surface treatment: To improve corrosion resistance or aesthetics, the surface of forged rings may need to be shot peened, polished or other types of surface treatment.
10.Quality inspection: The last step is to conduct physical and chemical testing and finished product inspection on the finished product to ensure that the forged ring meets the specified standards and requirements.
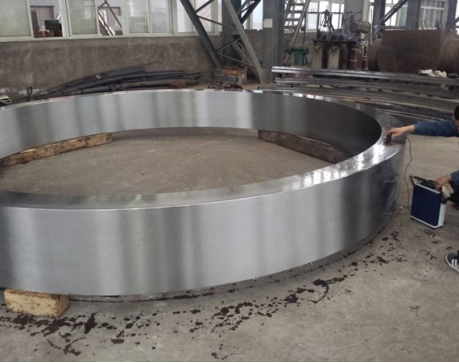
From what aspects to extend the service life of forged rings: material selection, manufacturing process, use and maintenance
1. Improve materials:
Select high-strength and high-toughness materials such as alloy steel, stainless steel, etc.
For specific working environments (such as corrosive environments), corrosion-resistant materials can be selected or the materials can be surface treated (such as galvanizing, chrome plating, PVD coating, etc.).
2. Reduce surface roughness:
Reduce the roughness of the forging ring surface through finishing methods (such as grinding, polishing, etc.) to reduce friction and wear.
Implement mirror grinding to make the surface very smooth (Ra=0.04~0.025μm).
3. Surface strengthening treatment:
Use physical vapor deposition (PVD), chemical vapor deposition (CVD) and other technologies to add wear-resistant coating to the surface of the forging ring.
Perform nitriding treatment to improve surface hardness and wear resistance.
4. Optimize design:
Consider the working conditions of the forging ring in the design stage to ensure its reasonable structure and avoid stress concentration points.
Consider factors that facilitate maintenance and replacement during design.
5. Correct installation and commissioning:
Ensure that the forging ring is correctly installed in the equipment to avoid additional wear caused by improper installation.
Regularly check and adjust the matching clearance of related components to ensure smooth operation.
6. Regular care and maintenance:
Establish a complete maintenance plan, check the forging ring status regularly, and find potential problems in time.
Lubricate the forging ring as needed to reduce the loss caused by friction.
7. Operating specifications:
Operators should operate the equipment strictly in accordance with the operating procedures to avoid damage caused by overload or misoperation.
Avoid long-term use under extreme temperature and humidity conditions, which may accelerate the aging and failure of materials.
8. Monitoring and early warning:
Use modern monitoring technology to monitor the working status of the forging ring in real time and warn of possible problems in time.