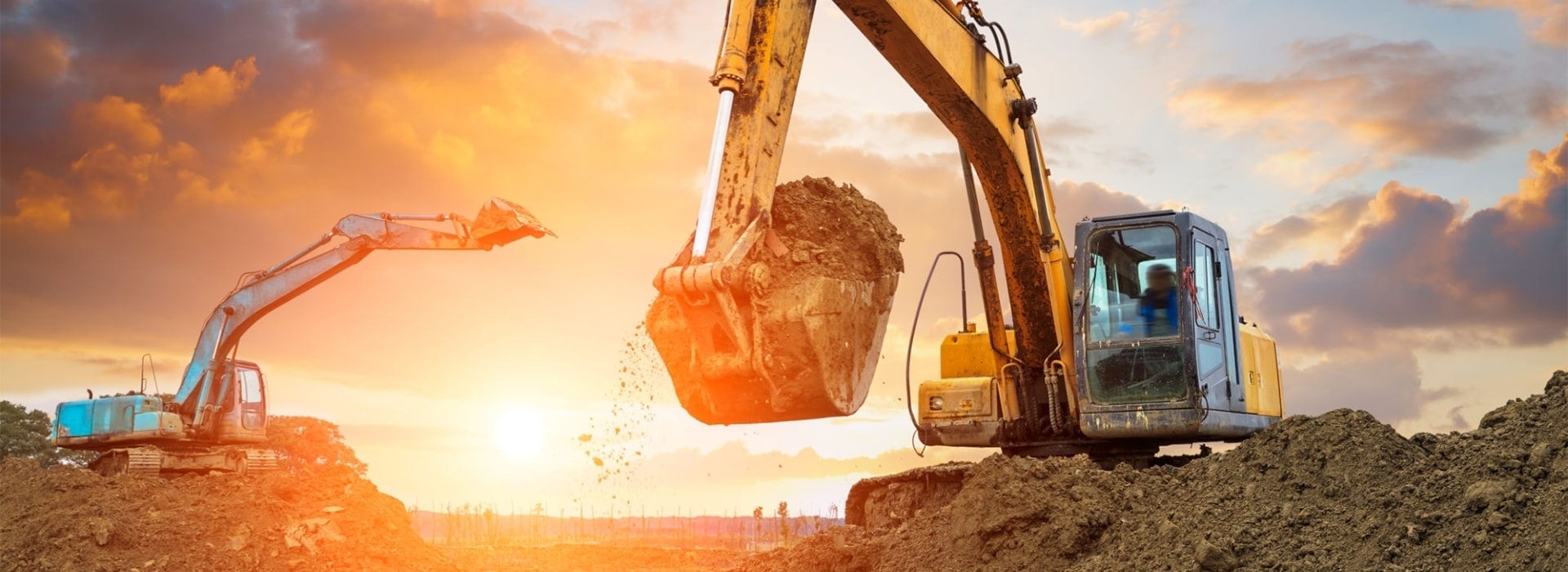
Custom casting large diameter herringbone gear
PRODUCT PARAMETERS
Description
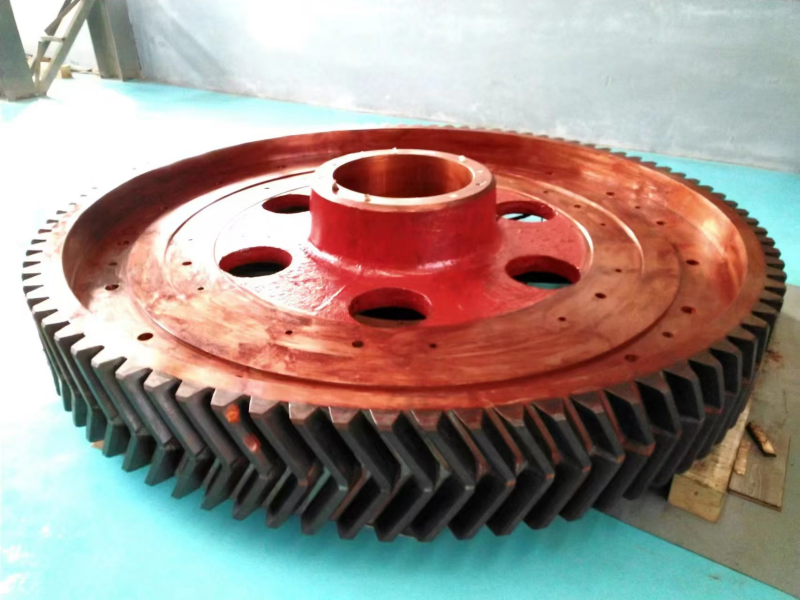
Processing process: herringbone gear
1. Design and mold making
Design: Design the specific parameters of the herringbone gear according to the use requirements, including modulus, pressure angle, helix angle, etc.
Mold making: Make the mold for casting according to the design drawings. For complex shapes such as herringbone gears, precision casting or lost wax casting is usually used to ensure accuracy.
2. Casting
Raw material preparation: Select suitable metal materials (such as cast iron, cast steel, etc.) and prepare smelting equipment.
Smelting and pouring: Put the selected metal material into the furnace to melt, and then pour the molten metal into the pre-prepared mold through the pouring system.
Cooling and demolding: After the metal cools and solidifies, open the mold and take out the casting.
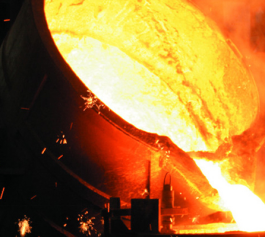
3. Preliminary cleaning and inspection
Cleaning: Remove sand, burrs and other impurities on the surface of the casting.
Inspection: Check whether the casting has defects, such as pores, cracks, etc., and perform necessary repairs.
4. Rough machining
Rough turning: Perform preliminary turning on the casting to form a rough outline in preparation for subsequent finishing.
Reference surface machining: Determine the machining reference surface to facilitate positioning and clamping in subsequent processes.
5. Heat treatment
Normalizing/annealing: Improve the internal structure of the casting, eliminate internal stress, and improve subsequent processing performance.
Quenching and tempering: According to the requirements of the final use, quenching and tempering may be required to enhance hardness and wear resistance.
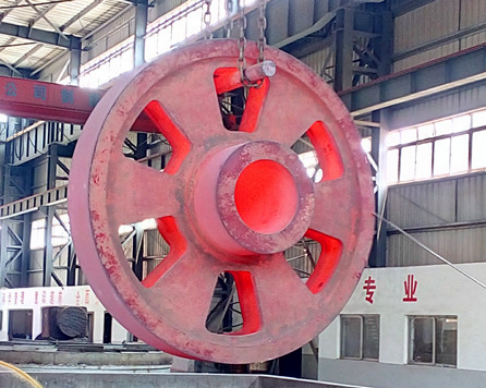
6. Finishing
Fine turning: Further precise machining of the outer circle, end face and inner hole to ensure that the dimensional accuracy of each part meets the design requirements.
Tooth processing:
Gear hobbing/gear shaping: Use a special gear hobbing machine or gear shaping machine to machine the single-sided helical gear part.
Herring gear special machine tool processing: Complete the processing of the other side of the helical gear to ensure that the helical teeth on both sides are accurately connected to form a herringbone shape. This step requires extremely high positioning accuracy and synchronous control capabilities.
Shaving or grinding: To improve the tooth surface finish and contact accuracy, shaving or grinding can be performed.
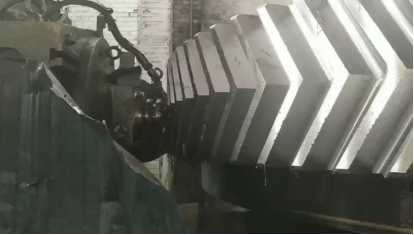
7. Surface treatment
Anti-corrosion treatment: Galvanizing, phosphating and other surface treatments are performed as needed to improve corrosion resistance.
Other surface strengthening treatments: such as nitriding, etc., to increase wear resistance and fatigue resistance.
8. Final inspection and testing
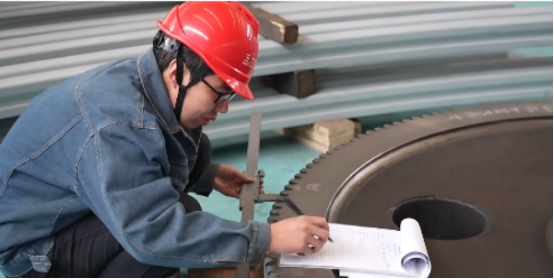
Dimension inspection: Comprehensive dimensional inspection is performed using tools such as three-coordinate measuring machines.
Non-destructive testing: Such as magnetic particle testing, ultrasonic testing, etc., to check whether there are cracks or other defects inside.
Dynamic balancing test (if applicable): Especially for high-speed gears, dynamic balancing correction must be performed.
Several major difficulties and reasons faced in the processing of herringbone gear without undercut grooves:
- Limited processing space
Difficulty: No undercut groove means that the processing tools (such as milling cutters, gear shaping cutters, etc.) cannot exit through the undercut groove after completing the processing of a tooth groove, and must be fed and exited in a limited space.
Solution:
Adopt a multi-step processing method: separate roughing and finishing, first use a larger cutting depth for roughing, and then use a smaller cutting depth for finishing, gradually approaching the final size.
Use special tools: Design or select special tools suitable for processing without undercut grooves, such as milling cutters or gear shaping cutters with special geometric shapes to ensure that the tools can work normally in a small space. - High processing accuracy requirements
Difficulty: The helical teeth on the left and right sides of the herringbone gear must be precisely symmetrical, and the parameters such as tooth shape, tooth pitch, and tooth thickness must strictly meet the design requirements, otherwise it will cause problems such as unbalanced axial force and increased noise.
Solution:
Precision measurement and correction: During the processing, high-precision measuring equipment (such as three-coordinate measuring machine, gear measuring center) is used for real-time monitoring to ensure the processing accuracy of each tooth groove.
Optimize processing technology: Use advanced CNC machine tools and automated processing technology to ensure stability and repeatability during the processing and reduce human errors. - Tool wear and life issues
Difficulty: Due to the design without back-off groove, the tool will be subjected to greater friction and impact every time it feeds and exits, resulting in faster tool wear and shortened life.
Solution:
Choose wear-resistant materials: Use high-strength and high-hardness tool materials (such as cemented carbide, ceramics, etc.), and perform surface coating treatment (such as TiN, TiAlN, etc.) to improve the wear resistance and impact resistance of the tool.
Optimize cutting parameters: Reasonably select cutting speed, feed rate and cutting depth to avoid excessive cutting load and extend tool life. - Low processing efficiency
Difficulty: The processing method without undercut usually requires more processes and longer time, especially when processing herringbone gears with large modulus or multiple teeth, the processing efficiency will be significantly reduced.
Solution:
Using efficient processing methods: such as four-axis linkage CNC machine tools, end milling side milling finishing, etc., can improve processing efficiency and reduce processing time.
Segment processing: Divide the entire gear shaft into multiple parts for processing, and assemble each part after processing separately, which can simplify the processing process and improve efficiency. - Heat treatment deformation control
Difficulty: Herringbone gear shafts usually need to undergo heat treatment processes such as quenching and tempering to improve their strength and hardness. However, deformation may occur during the heat treatment process, affecting the accuracy and fit of the gear.
Solution:
Optimize the heat treatment process: Select appropriate heat treatment process parameters (such as heating temperature, holding time, cooling rate, etc.), and reduce deformation by preheating, graded quenching, etc.
Subsequent correction: Perform necessary correction processes after heat treatment, such as grinding, honing, etc., to restore the accuracy of the gear. - Difficulty in assembly and debugging
Difficulty: The design without undercut makes the assembly and debugging of the gear shaft more complicated, especially for large or high-precision herringbone gear shafts. When assembling, it is necessary to ensure the coaxiality, parallelism and centering of each component.
Solution:
Use precision assembly tools: such as laser centering instrument, dial indicator, etc. to ensure the precise centering of the gear shaft with other components.
Step-by-step assembly: Divide the gear shaft into multiple parts for step-by-step assembly, and conduct strict inspection and adjustment at each step to ensure the final assembly quality. - High cost
Difficulty: Due to the difficulty of processing the herringbone gear shaft without undercut, the required equipment, tools, processes and technical requirements are high, resulting in a significant increase in manufacturing costs.
Solution:
Optimize design: Under the premise of meeting functional requirements, simplify the design as much as possible, reduce unnecessary complex structures, and reduce manufacturing difficulty and cost.
Batch production: Share fixed costs through batch production to reduce the manufacturing cost of each unit product. - High technical requirements
Difficulty: The processing of herringbone gear shafts without undercut grooves requires high-level technicians and rich experience, especially in programming, operation and debugging, which requires high skills of workers.
Solution:
Training and technical support: Provide professional training and technical support for workers to ensure that they master advanced processing technology and operating skills.
Introduction of automated and intelligent equipment: Use CNC machine tools with high automation and intelligent control systems to reduce dependence on manual operation and improve processing quality and efficiency.
REQUEST A QUOTE
RELATED PRODUCTS
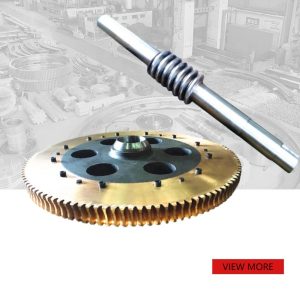
Mining machinery bronze & alloy steel Worm & Worm gear
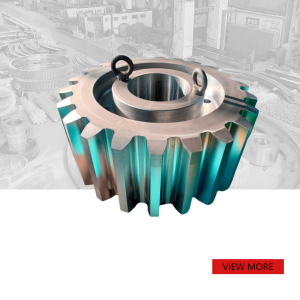
Forging cuatomized 42CrMo large module mining machinery Spur Gear
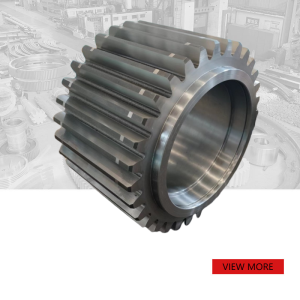
Customized wear-resistant 42CrMo forging spur gear
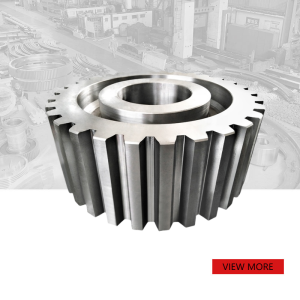
Spur gear forging high quality large diameter pinion gear
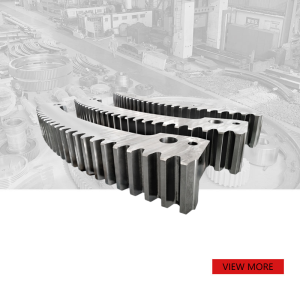
35CrMo Forging Mining large dimeter 12 Segment Arc Tooth
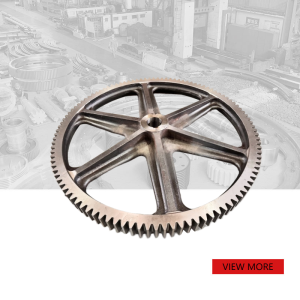