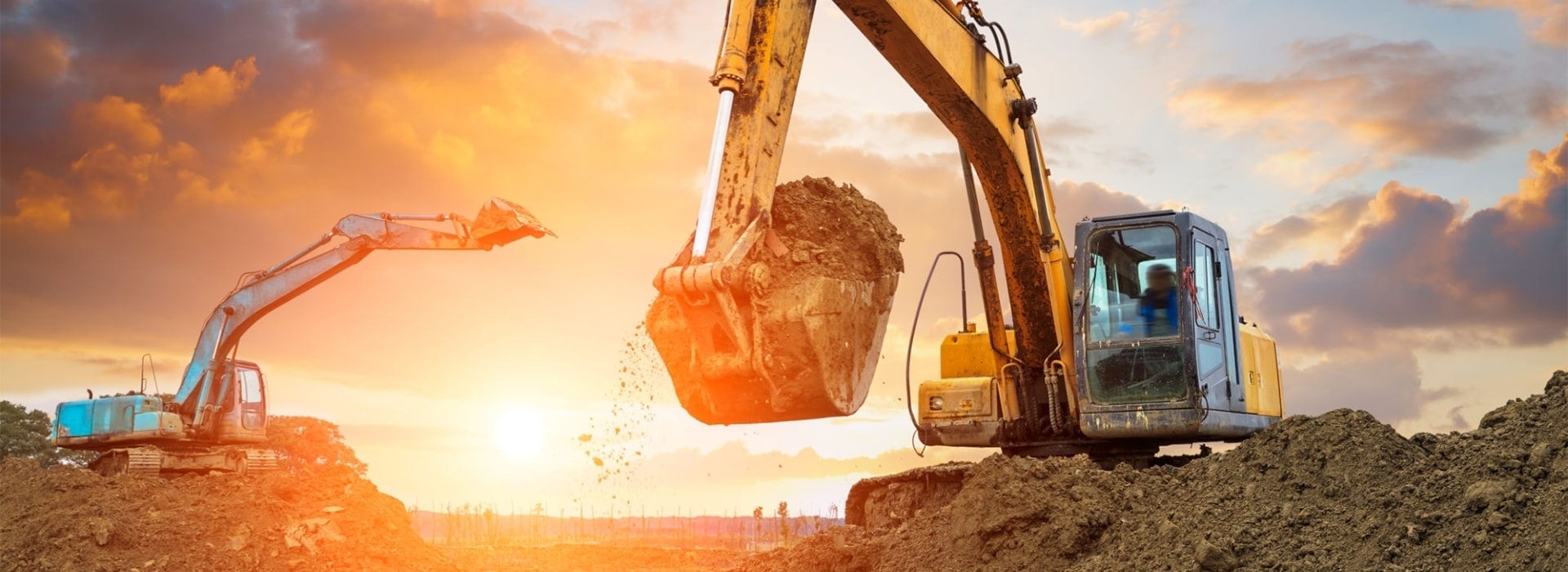
35CrMo wear resistant Gear reducer large Helical Gear Shaft
PRODUCT PARAMETERS
Description
一.Overview
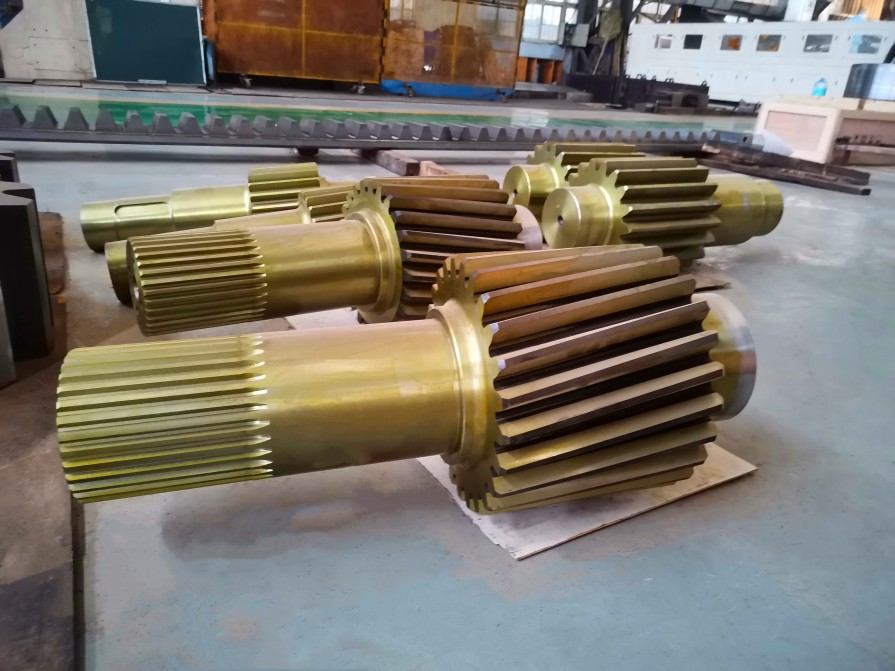
Module | 8-120 |
Tooth profile | Spur/Helical |
Heat treatment | Quenching,Tempering,Annealing,Normalizing |
Tooth treatment | Surface hardening,Surface carburizing,Surface nitriding |
Accuracy | 6-8 |
Helical gear shaft is a key transmission component used in large gear reducer, which is characterized in that the tooth lines of the gear are arranged in a spiral shape on the cylindrical surface. This design makes the helical gear contact smooth during meshing, low noise, and can withstand greater loads and provide higher transmission efficiency. Helical gear shafts are usually made of high-strength alloy steel and are precisely machined and heat treated to ensure excellent mechanical properties and long service life.
二.Features
1. High strength, more wear-resistant;
2. High transmission efficiency;
3. Smooth transmission, low noise;
4. High manufacturing requirements.
三.Production Process
1.Forging
The main reason for choosing forging as a manufacturing method for gear shaft blanks is that it can significantly improve the mechanical properties and reliability of parts:
For example, enhancing mechanical properties: During the forging process, the metal is processed by pressure at high temperature to make the internal structure more dense and the grains refined, which greatly improves the strength, toughness and fatigue resistance of the gear shaft.
Reducing material defects: Compared with casting, forging can effectively eliminate internal defects such as pores and shrinkage, ensure the uniformity and consistency of the material, and thus improve the quality of the final product.
High dimensional accuracy: Although the forged parts still need to be machined to the final size, the forged blank is relatively close to the finished shape, which reduces the amount of subsequent processing and helps to maintain better dimensional stability.
Adapt to high-intensity working environment: Forged gear shafts are particularly suitable for heavy loads, impact loads and occasions requiring high reliability, such as heavy machinery.
2.Rough machining
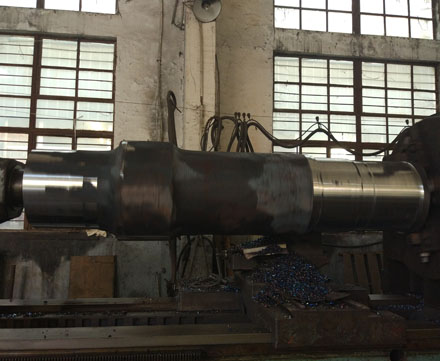
The main reason for choosing forging as a manufacturing method for gear shaft blanks is that it can significantly improve the mechanical properties and reliability of parts:
For example, enhancing mechanical properties: During the forging process, the metal is processed by pressure at high temperature to make the internal structure more dense and the grains refined, which greatly improves the strength, toughness and fatigue resistance of the gear shaft.
Reducing material defects: Compared with casting, forging can effectively eliminate internal defects such as pores and shrinkage, ensure the uniformity and consistency of the material, and thus improve the quality of the final product.
High dimensional accuracy: Although the forged parts still need to be machined to the final size, the forged blank is relatively close to the finished shape, which reduces the amount of subsequent processing and helps to maintain better dimensional stability.
3.Heat treatment
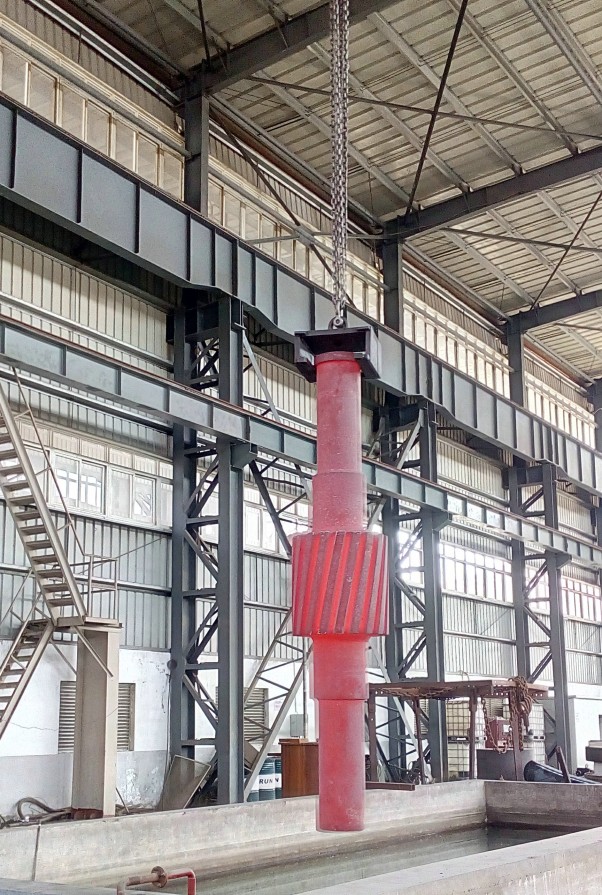
We believe that 80% of the life of mechanical products depends on hot processing
Our eight metal material experts form a team to control our raw material’s internal quality and mechanical properties from the source,in this way to improve our products’ service life.We have a professional senior engineer team with more than years experience on material,hot and cold processing.
4.Hobbing
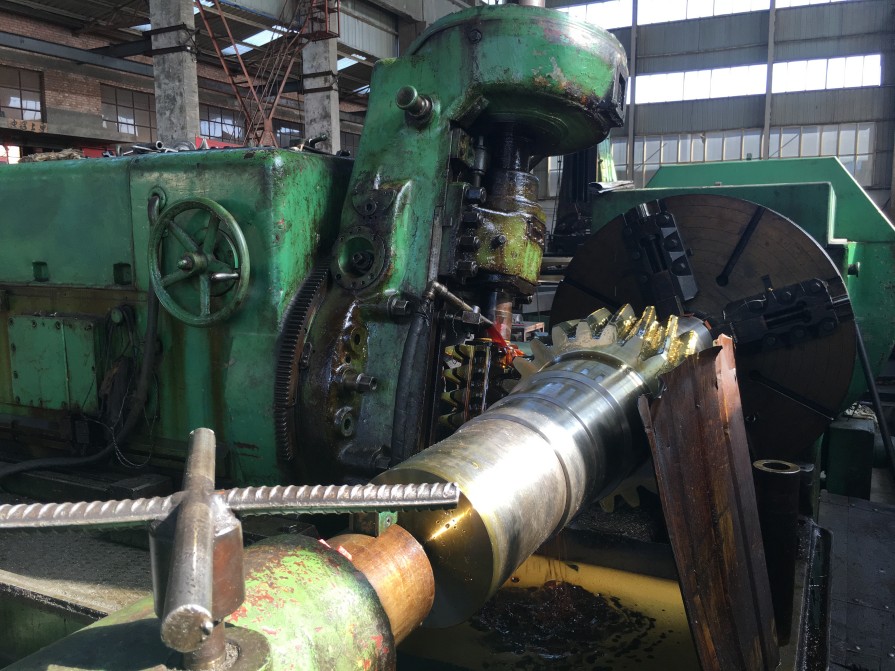
Hobbing of large helical gear shafts is a key process in the manufacturing process. It uses a special hobbing machine to precisely process the gears. This process not only determines the final accuracy and surface quality of the gears, but also directly affects the efficiency and stability of the mechanical transmission system. High-quality hobbing technology can ensure the wear resistance and long life of the gears under high-load working conditions, which is of great significance to improving the overall performance of mechanical equipment. In addition, precise hobbing can also reduce noise and vibration and improve running stability.
5.Test
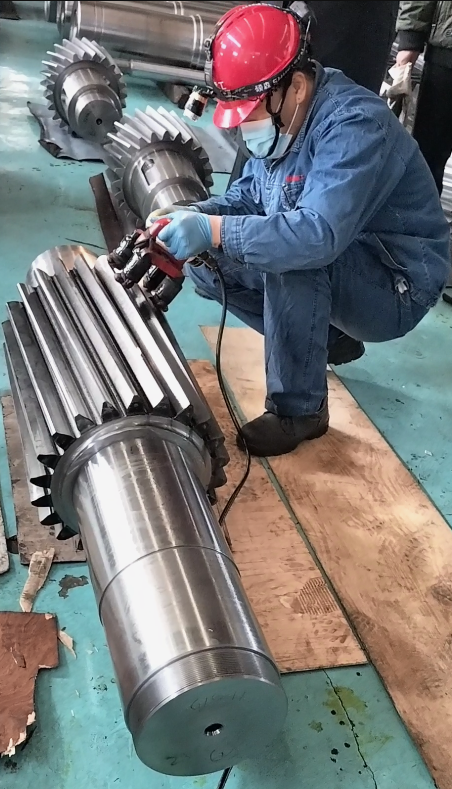
It is of vital importance to inspect the processed large gear shafts. First, ensure that their dimensional accuracy and shape tolerance meet the design requirements to ensure accurate matching with other mechanical parts. Secondly, through inspection, the material characteristics and surface quality of the gear shaft can be verified to avoid potential defects that affect the service life and performance. In addition, the inspection process can also find errors or deficiencies that may occur in the manufacturing process, provide a basis for process improvement, and ultimately ensure the reliability, safety and efficiency of the gear shaft in actual application. This is not only related to the overall operating efficiency of the equipment, but also directly affects the maintenance cost and production safety.
四.FAQ
1.What kind of packing do you have? –Our packing is suitable for export, usually plywood cases.
2.Can you issue the drawings?–We can according to customer’s parameters to issue the drawings.
3.Do you accept third party inspection?–Yes.
REQUEST A QUOTE
RELATED PRODUCTS
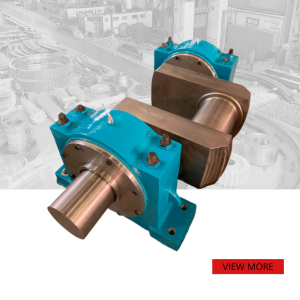
Custom eccentric shaft with bearing seat
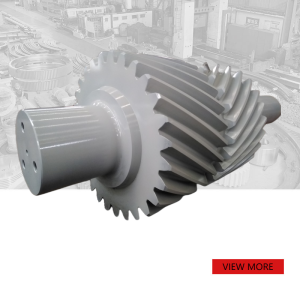
forging double helical gear shaft
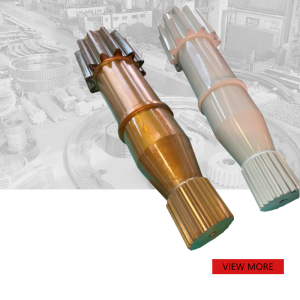
Custom forged 42CrMo large modulus gear shaft
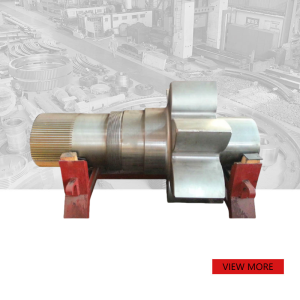
4340 OEM Big Pinion Shaft Spur Toothed Forging Carbon Steel Spur Large Module Gear Shaft
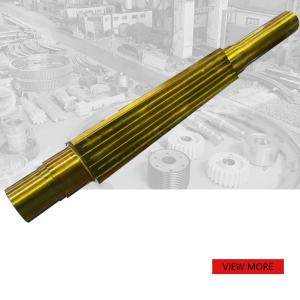
Customized AISI4140 heavy duty hammer crusher Rotor Shaft
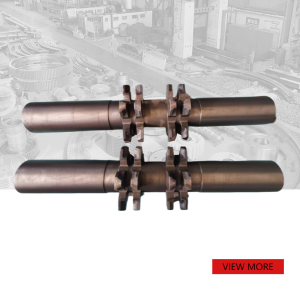