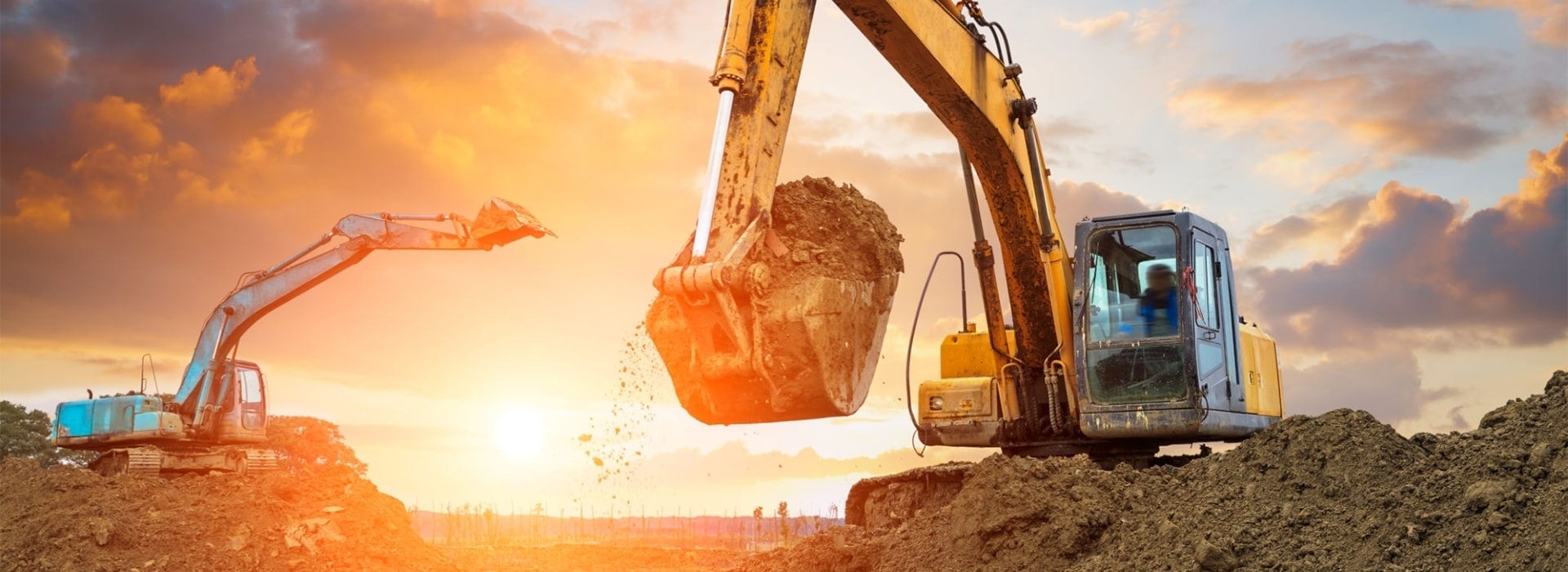
Nonstand custom long forging crankshaft
PRODUCT PARAMETERS
Description
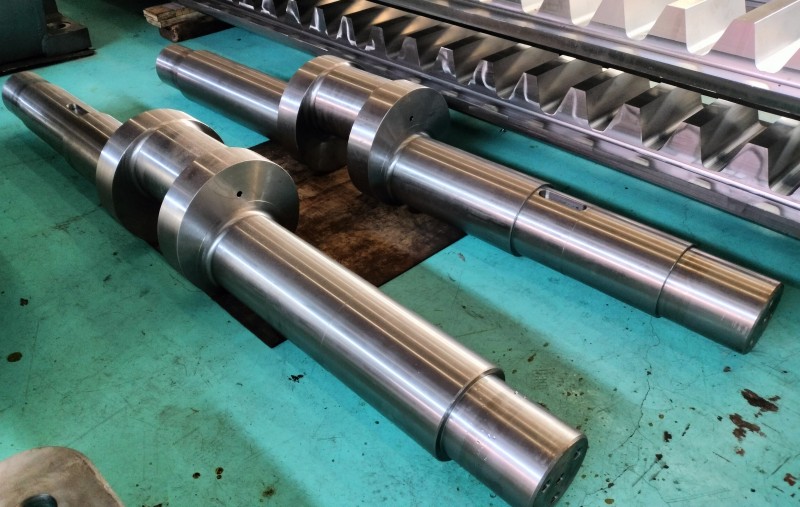
General processing flow of crankshaft:
1. Material selection and preparation
Material selection: Select suitable steel according to design requirements, usually high-strength alloy steel, such as 42CrMo, etc.
Cutting: Cut the selected raw materials according to the predetermined length.
2. Preliminary forging or casting
For some large or complex eccentric shafts, it may be necessary to form them by forging or casting.
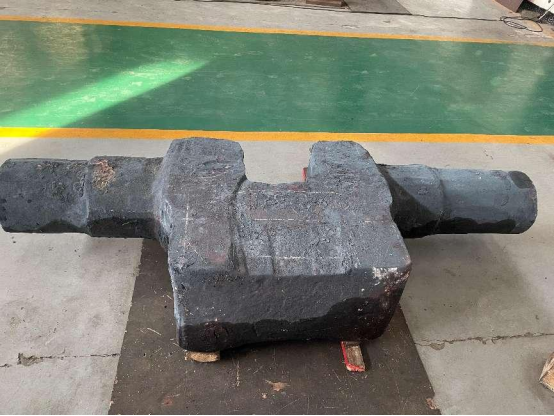
3. Rough turning
Rough machining: Preliminary turning of the crankshaft on a lathe to remove excess material and form a rough outline. The center hole is also drilled in this step.
Inspection: Check whether the dimensions after rough machining meet the process requirements.
4. Heat treatment
Quenching and tempering: In order to improve the hardness and wear resistance of the eccentric shaft, it is usually quenched and tempered. The specific heat treatment parameters depend on the material used.
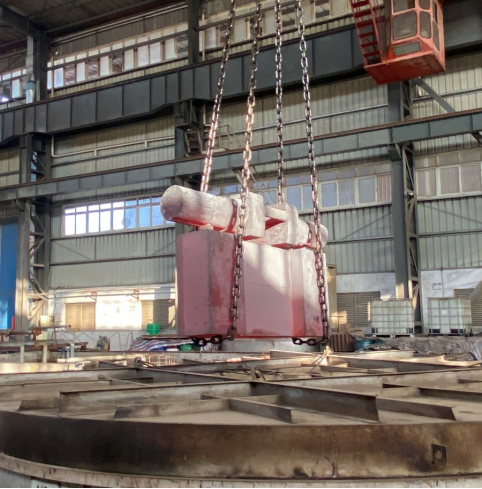
5. Semi-finishing turning
After heat treatment, semi-finishing turning is performed to further refine the dimensional accuracy of each part and prepare for subsequent processing.
6. Eccentric part processing
Eccentric positioning: Use special fixtures or chucks to properly fix the workpiece so as to accurately process the eccentric part.
Precision grinding: For the key surfaces of the eccentric shaft, especially the eccentric part, high-precision grinders are used for fine grinding to ensure dimensional accuracy and surface finish.
7. Final finishing
Depending on the specific design requirements, additional finishing steps may be required, such as keyway milling, thread processing, etc.
8. Surface treatment
It may involve surface hardening treatments such as chrome plating and nitriding to enhance corrosion resistance and wear resistance.
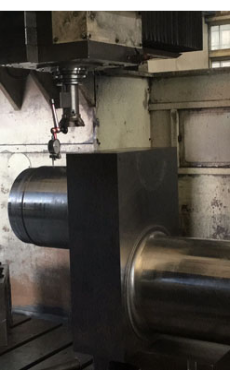
9. Inspection and testing
Dimension inspection: Use tools such as three-coordinate measuring machines for comprehensive dimensional inspection.
Nondestructive testing: such as magnetic particle testing, ultrasonic testing, etc., to check whether there are cracks or other defects inside.
Dynamic balancing test: Especially for eccentric shafts running at high speed, dynamic balancing correction must be performed.
10.Package
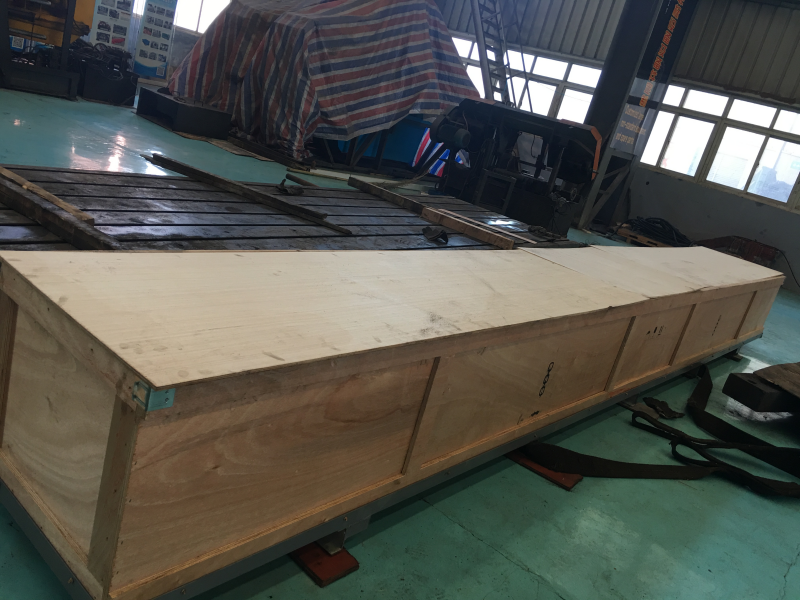
According to the requirements of customers, we apply anti-rust oil to the whole product for anti-rust treatment. In addition, we can also paint the products according to the needs of customers to prevent rust. And then it goes into a fumigation-free plywood box.
Usage
Application scenarios of eccentric shafts: What mining equipment are they mainly used on
1. Vibrating scree
2. Crusher
3. Vibrating feeder
4. Sand washing machine
5. Conveyor (specific type)
6. Dewatering screen
7. Other auxiliary equipment