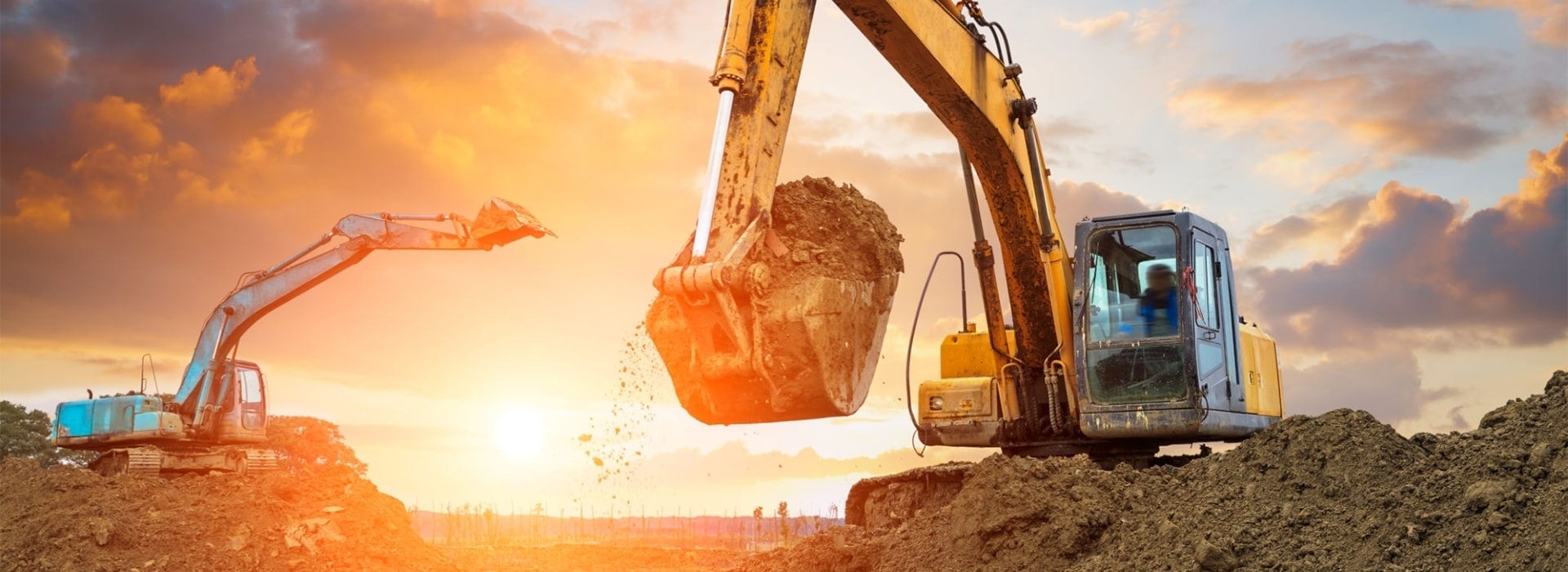
Nonstandard custom forging steel large flange shaft
PRODUCT PARAMETERS
Description
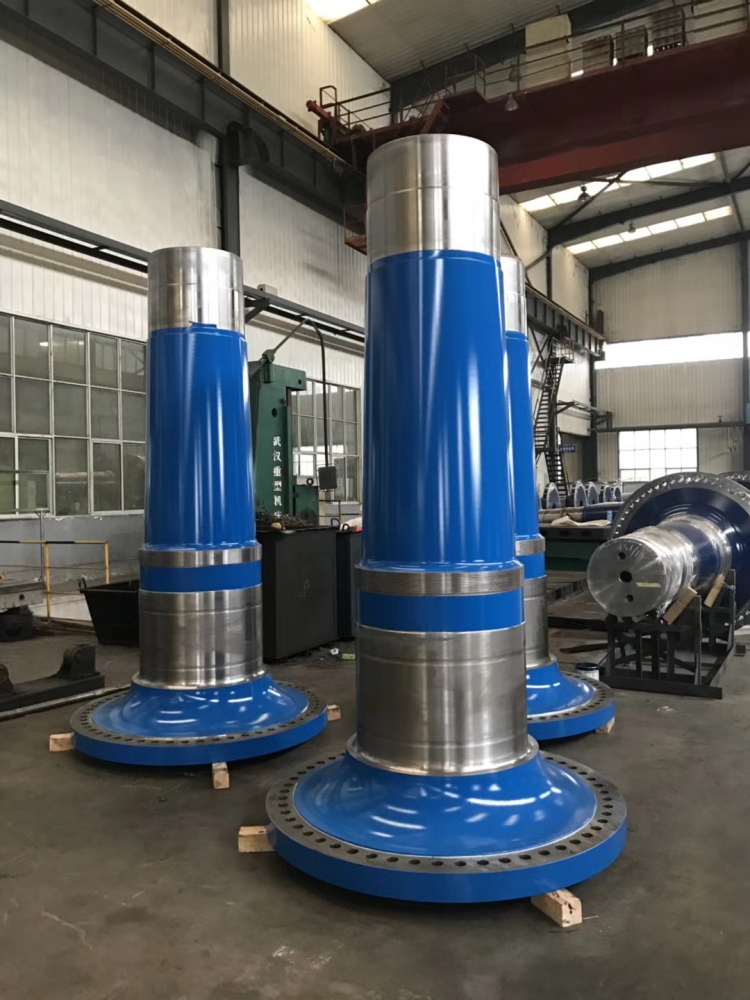
Flange shaft Product Description
1. Blank preparation (forging)
Raw material selection: Select appropriate steel (such as carbon steel, alloy steel) according to design requirements.
Heating: Heat the steel to the plastic deformation temperature (usually 1000~1250°C) to make it have good forgeability.
Forging: Use free forging or die forging process to forge the steel into a blank close to the shape of the flange shaft.
Forging can refine the grains and improve the strength, toughness and fatigue performance of the material.
Cooling and correction: Natural cooling or controlled cooling after forging, and preliminary correction of the blank to ensure the basic shape.
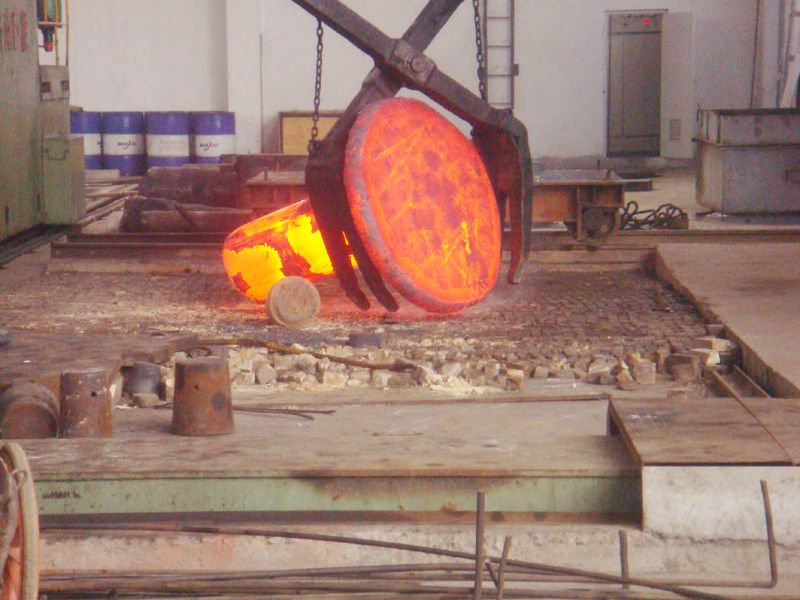
2. Rough machining
Turning: Preliminary cutting of the outer circle, end face and step part of the flange shaft to remove excess material.
Process the basic contour of the shaft and the plane of the flange.
Drilling/boring: Process the center hole or other mounting holes at one or both ends of the shaft.
If the flange shaft needs to be matched with bearings or seals, the inner hole needs to be processed.
Milling:
If there are keyways, threaded holes or other complex structures on the flange, use a milling machine for processing.
Deburring:
Remove burrs and flash generated during forging and rough machining.
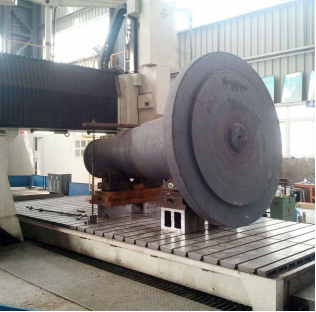
3. Heat treatment
Normalizing:
Heat the flange shaft after rough machining to above the critical temperature (usually 850~950°C), and then cool it in air.
The purpose is to uniform the structure, eliminate internal stress and improve cutting performance.
Quenching and tempering (optional):
For flange shafts with high strength requirements, quenching + high-temperature tempering treatment is performed.
Improve the comprehensive mechanical properties (strength, toughness and wear resistance) of the material.
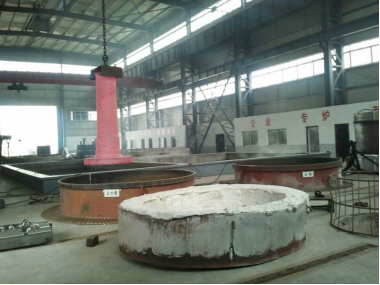
Surface hardening (optional):
Enhance the hardness and wear resistance of the flange shaft surface through induction quenching or carburizing treatment.
4. Finishing
Fine turning:
High-precision turning of the outer circle, flange plane and other key parts of the shaft to ensure dimensional accuracy and surface roughness.
Grinding:
Use an external cylindrical grinder or an internal cylindrical grinder to perform precision grinding on the key parts of the shaft (such as the mating surface and the bearing seat).
Countersinking/reaming:
Finely process the mounting holes of the flange shaft to ensure the matching accuracy.
Gear hobbing/gear shaping (if there is a gear structure):
If the flange shaft has a gear structure, the tooth profile needs to be processed.
Tapping/countersinking:
Process threaded holes or countersinking surfaces on the flange for mounting bolts or other components.
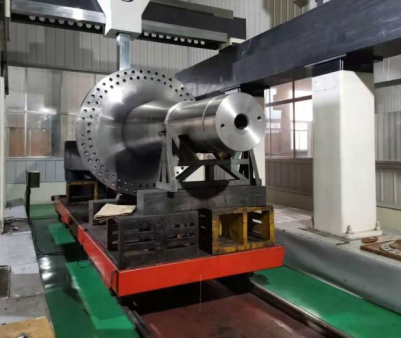
5. Quality inspection
Dimension inspection:
Use tools such as calipers, micrometers, and three-dimensional coordinate measuring machines to check whether the dimensions of the flange shaft meet the requirements of the drawings.
Surface roughness inspection:
Use a roughness meter to check the surface roughness of key parts.
Non-destructive testing (NDT):
Perform ultrasonic testing (UT), magnetic particle testing (MT), or penetrant testing (PT) to ensure that there are no defects inside and on the surface.
Hardness testing:
Test whether the hardness of the flange shaft meets the design requirements.
Dynamic balancing test (if high-speed rotation is required):
Perform dynamic balancing test on the flange shaft to ensure smooth operation.
6. Surface treatment (optional)
Coating:
According to the requirements of the use environment, the flange shaft is subjected to anti-corrosion treatment (such as galvanizing, nickel plating or spraying).
Oxidation treatment:
Anodize the aluminum alloy flange shaft to improve corrosion resistance and wear resistance.
Shot peening:
Shot peening is performed on key parts to improve fatigue strength.
7. Assembly and packaging
Assembly:
If the flange shaft needs to be pre-assembled with other components (such as bearings, seals), the assembly is completed at this stage.
Packaging:
After the finished product is subjected to anti-rust treatment, it is protected with special packaging materials to prevent damage during transportation.
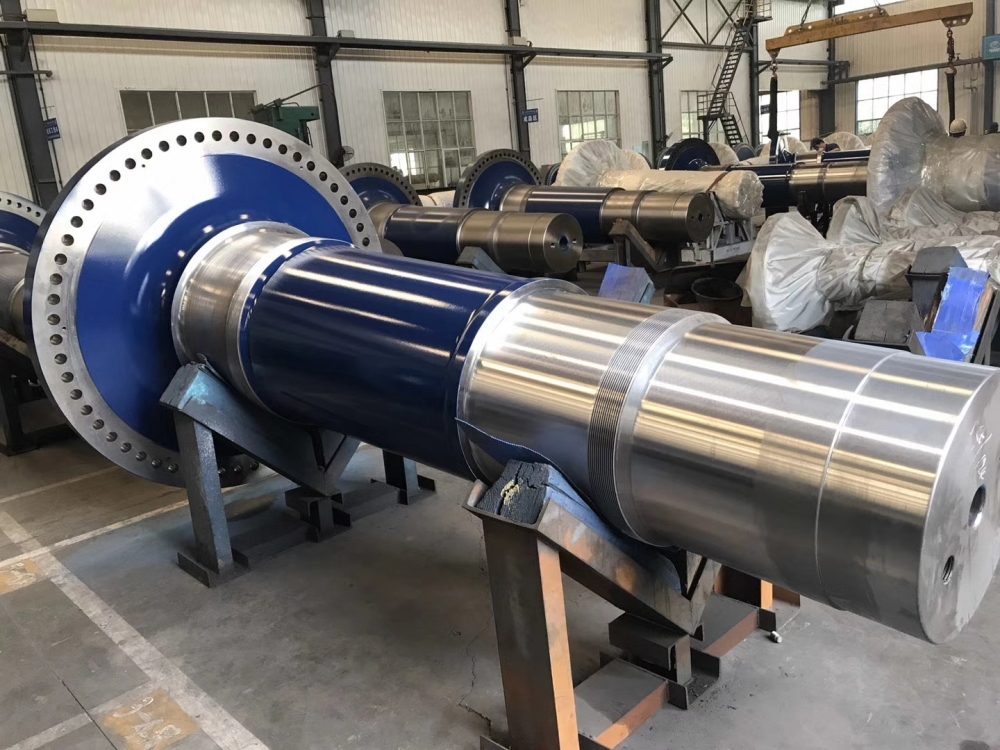
Characteristics of forged flange shaft processing
1.High strength and high toughness: The forging process makes the internal structure of the material more compact and has excellent mechanical properties.
2.High precision requirements: Flange shafts are usually used in transmission or connection occasions, and their dimensional accuracy and surface quality are required to be high.
3.Complex geometric shapes: Flange shafts may contain multiple structures such as steps, keyways, threaded holes, etc., which are difficult to process.
4.Combination of multiple processes: From blank preparation to final processing, multiple processes such as forging, heat treatment, and cutting are involved.