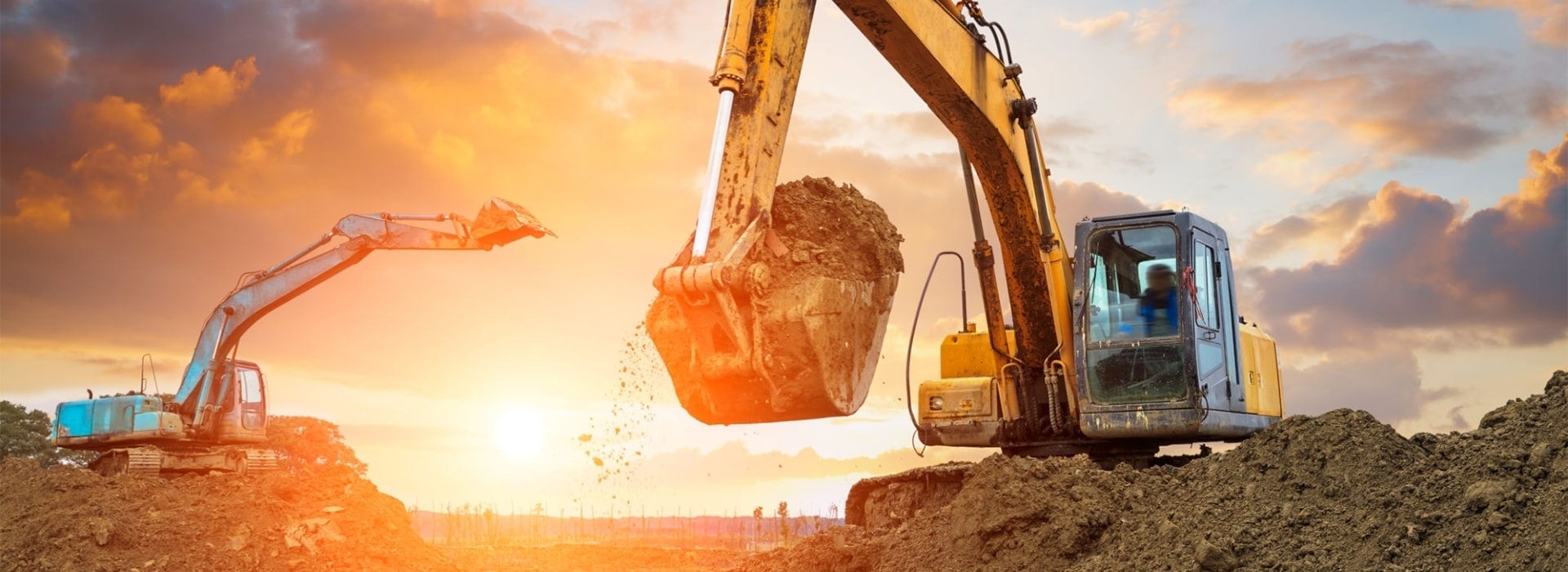
Custom Forging Large Roller Shell High Quality Briquetting Machine Roll Shell Dimpled Roller Shell
PRODUCT PARAMETERS
Description
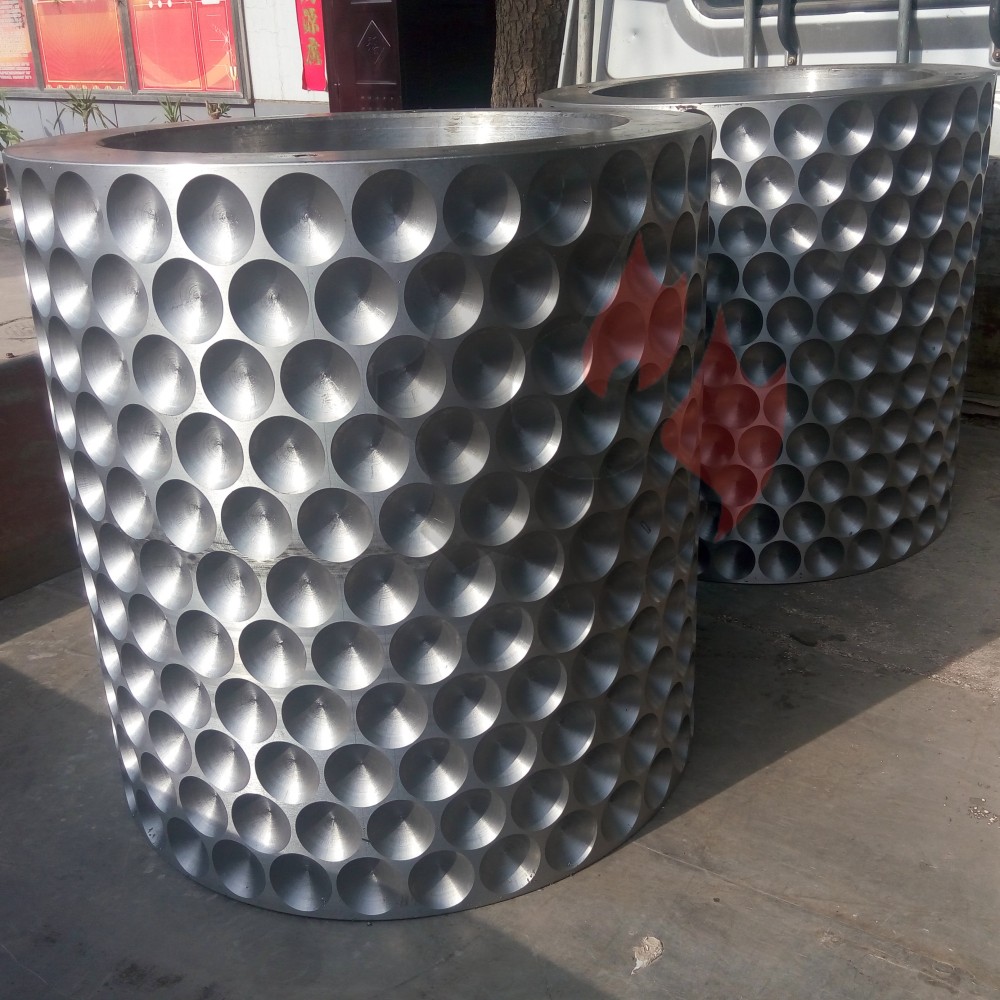
Overview of Roller Shell
The custom forged large roller shell plays a key role in the ball press, which is mainly used to compress various powder materials into balls or blocks. Its application improves the molding efficiency and finished product quality of the equipment. Through precision design and custom forging, the large roller shell has excellent wear resistance, strength and pressure resistance, which can effectively cope with high pressure conditions and wear problems. In addition, reasonable structural design can also reduce energy consumption, extend service life, reduce maintenance costs, and ensure stable and efficient operation of the ball press, which is crucial to improve production efficiency.
Q | A | Q | A |
Product name | Roller Shell | Delivery time | 45-60Days |
Material | 9Cr2Mo ,GCr15SiMn ,9Cr18Mo | Defect Control | UT, MT |
Application scenario | Magnesium plant, briquettes press, feed plant | Color | Custom |
outer diameter | According to the drawings | weight (kg) | 400 |
Heat Treatment | spheroidizing annealing | Certificate | ISO9001 |
Key steps in the production process of Roller Shell
Forging
Forging is the initial step in customizing the large roller shell by heating the selected material to the appropriate temperature and forging molding. This step not only determines the basic shape and size of the part, but also significantly affects its internal organizational structure and mechanical properties. In the forging process, the heating temperature, forging strength and speed must be strictly controlled to ensure uniform material density, reduce internal defects, and enhance mechanical strength and toughness. High quality forging lays a solid foundation for subsequent processing.
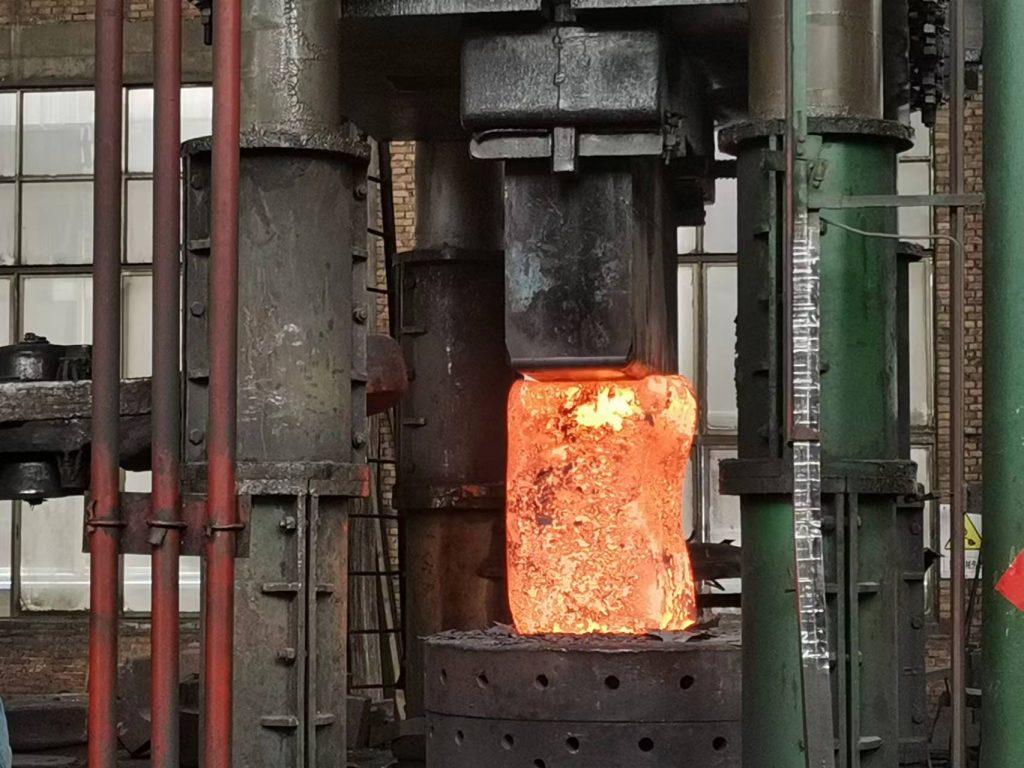
Spheroidizing annealing
Spheroidizing annealing is an important part of heat treatment of large roller shell after forging, aiming to spheroidize carbide in the material and improve the microstructure through a specific heating and slow cooling process. This process can improve the machinability of the material and reduce tool wear in subsequent machining. At the same time, spheroidizing annealing can also relieve internal stress, prevent deformation or cracking of the workpiece, and provide a more stable and easy to process material basis for the following precision machining.
Milling machining
Milling is the process of precision cutting for specific functional areas of large roller shells (such as ball and socket), using special milling cutters to complete the processing of complex shapes. This step requires high-precision machine tools and specialized programming techniques to ensure the accuracy of ball and socket position, dimensions and surface finish. The quality of milling ball socket directly affects the working efficiency of the ball press and the quality of the finished product. Strict process control and online inspection means are particularly important in this process to ensure that each ball and socket meets high standards of technical requirements.
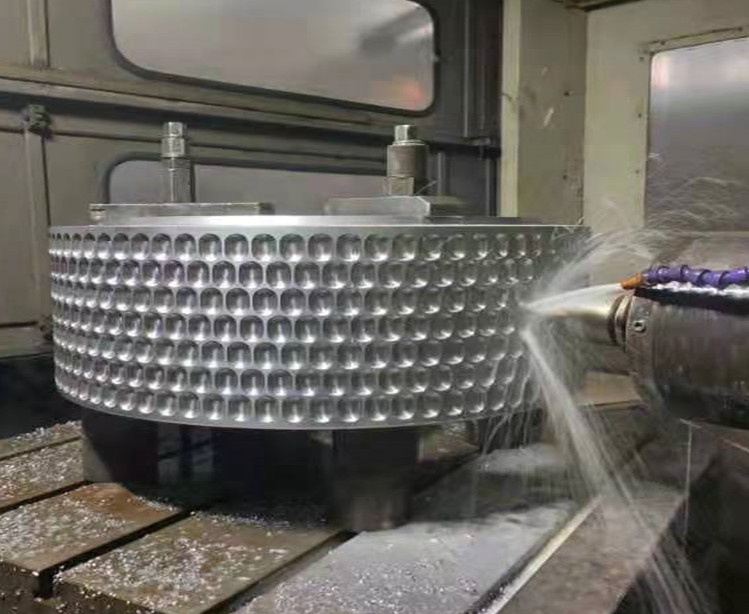
No oxidation heating quenching
Non-oxidation heating quenching is the core step to improve the hardness and wear resistance of the surface of the large roller shell, using the rapid heating and quenching technology under the protection of special atmosphere. This method avoids the oxidation and decarbonization problems that may be caused by traditional heating methods, and keeps the surface of the part pure. By precisely controlling the heating rate, holding time and cooling medium, the ideal quenching effect can be obtained to enhance the wear resistance and service life of the parts. No oxidation heating quenching is essential to meet the long-term stable operation of the ball press under high pressure and harsh environment.
Inspect of Roller Shell
The inspection of custom forged large roller shell mainly includes appearance inspection, dimensional accuracy inspection and internal quality evaluation. First, the appearance inspection should ensure that the surface is free of cracks, folds, and other defects. Next, dimensional measurements are carried out using precision measuring tools to verify that they meet the design requirements. Internal quality is assessed by non-destructive testing methods such as ultrasonic or magnetic particle testing to confirm that there are no hidden defects inside. In addition, depending on the specific application requirements, hardness testing and chemical composition analysis may be required to ensure that the material properties meet the requirements of the expected operating conditions. These steps together ensure the quality and reliability of the large roller shell.
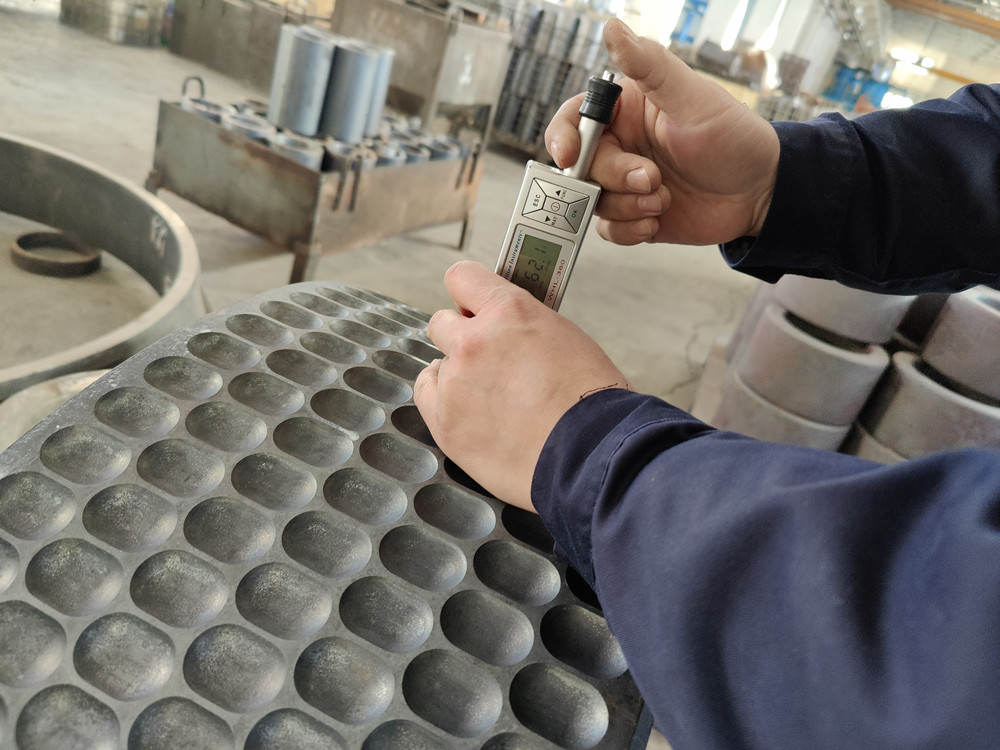
FAQS of Roller Shell
1.How long is the lead time?
The lead time for standard products is usually 45-60 Days, depending on the number and complexity of the order. For urgent orders, we can also arrange urgent production to shorten the delivery time as much as possible. We will make a detailed production plan according to your needs and communicate the progress in time.
2. Do you provide customized service?
Yes, we offer a full range of customized services to design and manufacture non-standard gears according to your special needs. Whether it is size, material or surface treatment requirements, we are flexible to ensure that we provide you with the most suitable solution. Please provide detailed technical specifications so that we can quote accurately.
3.How do you guarantee the quality?
We implement a total quality management system, from raw material procurement to finished products, every link is strictly tested. Advanced equipment such as hardness tester is used for accurate measurement, and strict heat treatment process is implemented to ensure the quality of each product is stable and reliable.
4.What are the choices of materials produced in your factory?
We offer a wide selection of materials, including cast iron, cast steel and alloy steel, depending on your application needs. Each material has its own specific mechanical properties, such as wear resistance, strength and toughness. We can recommend the most suitable materials according to your specific requirements.
REQUEST A QUOTE
RELATED PRODUCTS
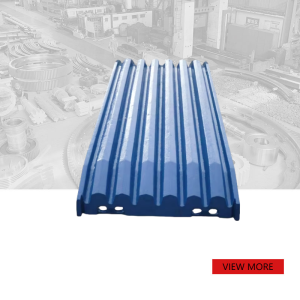
Mining Machinery parts Casting Jaw Crusher Jaw Plates
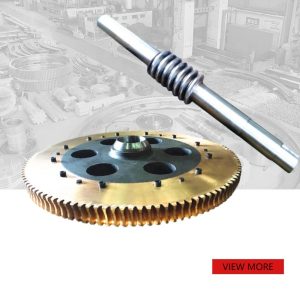
Mining machinery bronze & alloy steel Worm & Worm gear
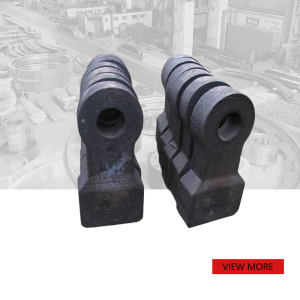
Customized High-chromium Alloy Steel Large Cast Crusher Hammer
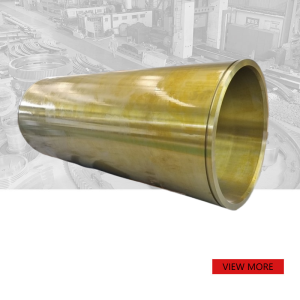
Custom forging large Hydraulic cylinder body
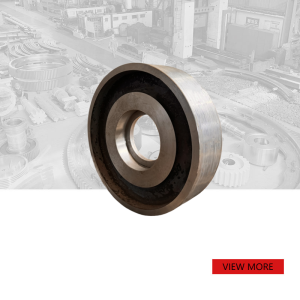
Non-standard alloy steel large diameter Casting wheel
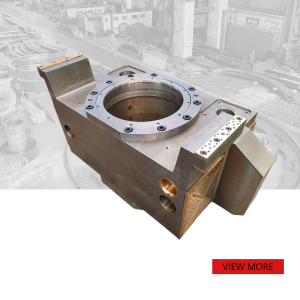