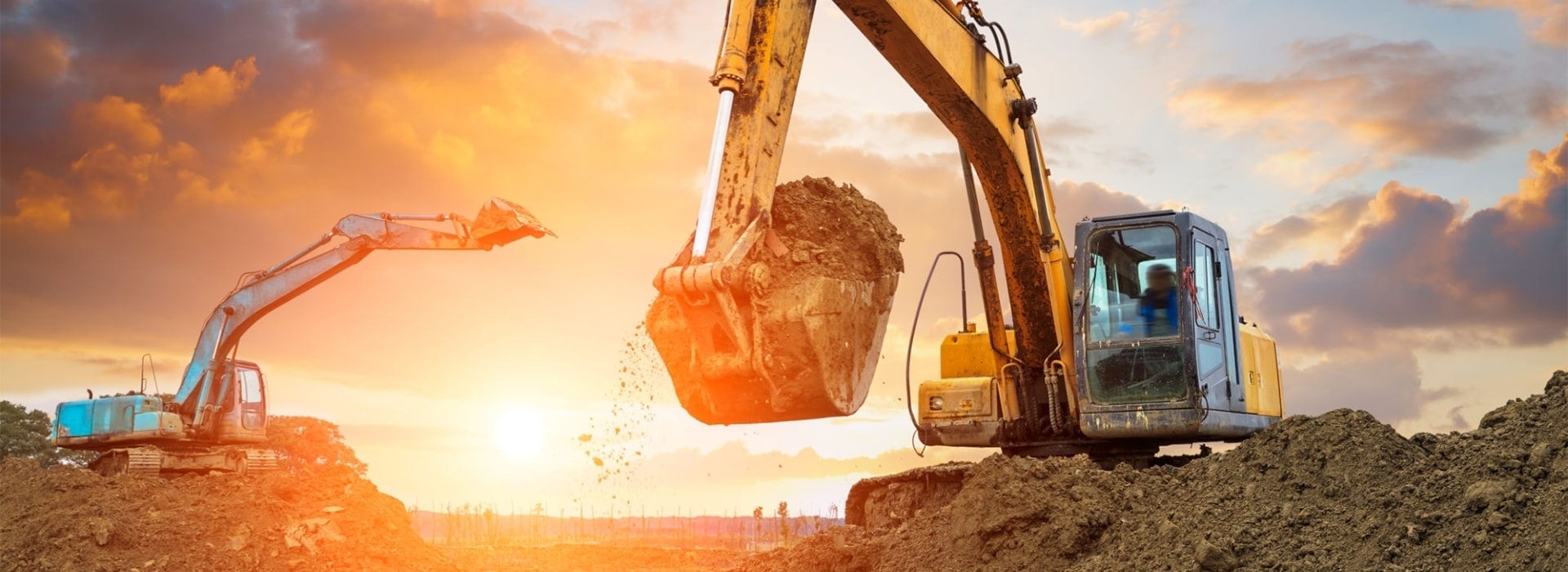
Mining Large Steel Casting Sheave wheel Custom Rope sheave
PRODUCT PARAMETERS
Description
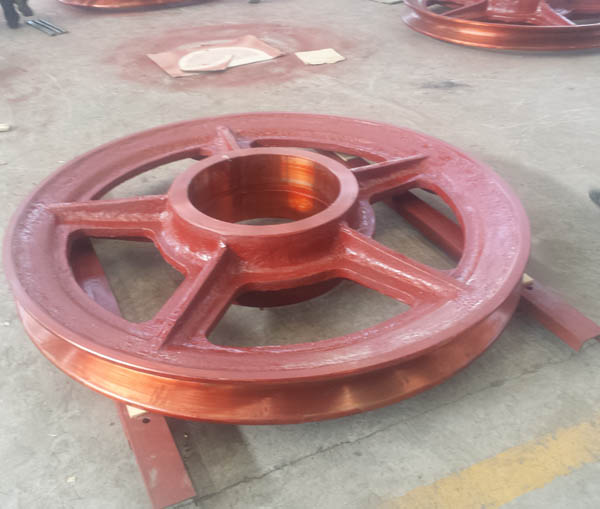
Overview of Casting Sheave
The cast rope wheel is a key component in mining excavators and cranes, mainly used to guide and support the wire rope to ensure the safety and efficiency of the operation. Its application improves the wear resistance and bearing capacity of the equipment, and reduces the maintenance frequency. The quality of the rope wheel directly affects the smoothness of the operation and the service life of the equipment, which is of great significance to improve the working efficiency and reduce the downtime. Therefore, in heavy machinery, high-quality casting rope wheels are indispensable.
Q | A | Q | A |
Product name | Sheave | Delivery time | 45-60Days |
Material | Cast Iron | Defect Control | UT, MT |
Certificate | ISO9001 | Color | Custom |
outer diameter | According to the drawings | weight (kg) | 200 |
Key steps in the production process of Sheave
Casting blank
First, prepare the mold according to the design drawings, select the appropriate metal materials such as cast steel or cast iron. The molten metal is poured into the mold, cooled and solidified, and removed to form a blank. This process requires strict control of the pouring temperature and speed to ensure the density and uniformity of the internal structure, to avoid porosity, cracks and other defects.
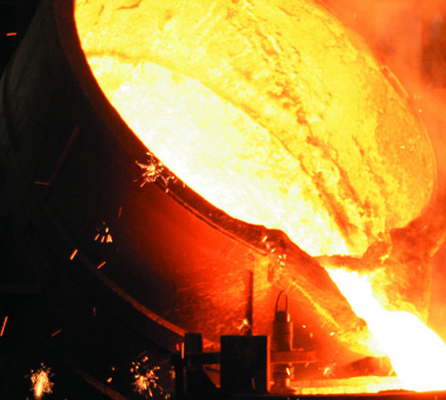
Roughing
After the preliminary inspection, the blank enters the roughing stage, and the basic shape of the rope wheel is processed using lathes, milling machines and other equipment, including cutting excess parts and forming a rough outline. The aim is to provide an accurate base shape for subsequent processes, while removing surface irregularities and defects to ensure that the dimensions basically meet the requirements.
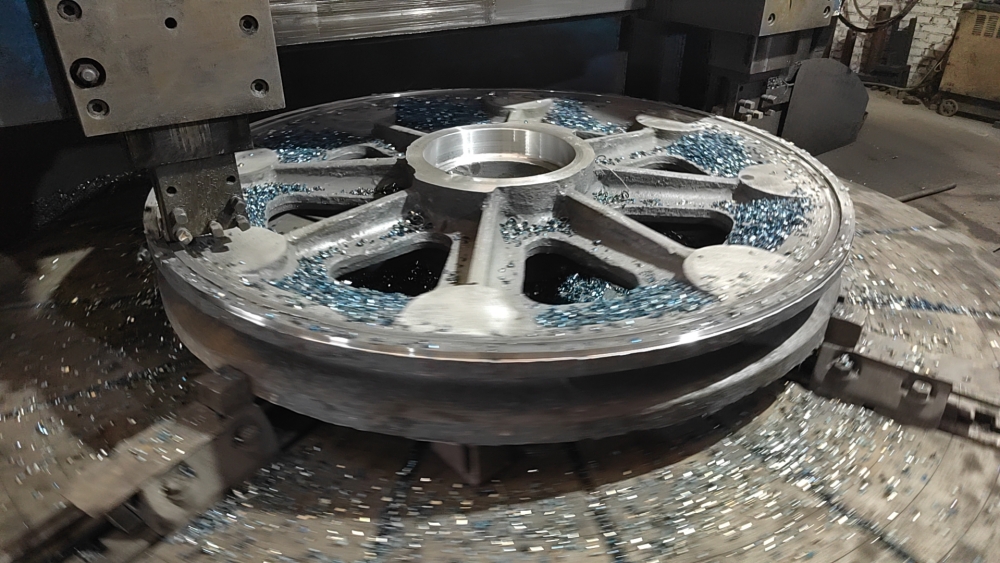
Heat treatment
The roughed rope wheel needs to be heat treated to improve its mechanical properties, usually including quenching and tempering. Brittleness is reduced by heating to a specific temperature and holding it for a period of time, then rapidly cooling (quenching), followed by slow heating (tempering). This step increases the hardness and toughness of the rope wheel, making it more resistant to wear and impact.
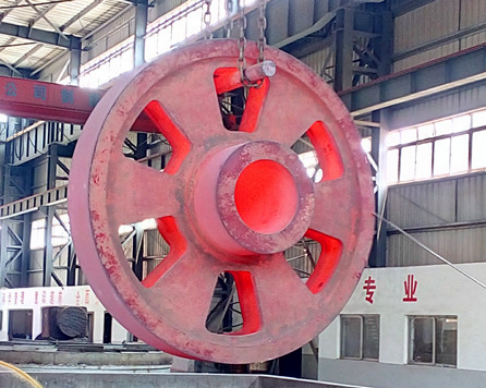
Finishing
After the heat treatment is completed, the rope wheel enters the finishing stage, and the key parts such as the rope groove are finely machined using precision machine tools to ensure high precision size and finish. This process is essential to achieve a good fit between the rope wheel and the wire rope, which directly affects the smoothness of operation and service life. The final product is subject to strict tolerances.
Surface treatment
The final step is surface treatment, designed to enhance the corrosion resistance and beauty of the rope wheel. Common methods include electroplating, spray painting or special protective coating. Surface treatment can not only effectively prevent the erosion of the external environment on the rope wheel, but also reduce the coefficient of friction, extend the service life, and make the product look more professional. Select an appropriate processing method based on the actual application environment.
Package of Casting Sheave
The rope wheel is packed in wooden cases, and the interior is fixed with foam or foam plastic to prevent collision damage during transportation. The wooden box is reinforced with iron bars to ensure the stability of the structure and marked with warning signs to ensure transportation safety.
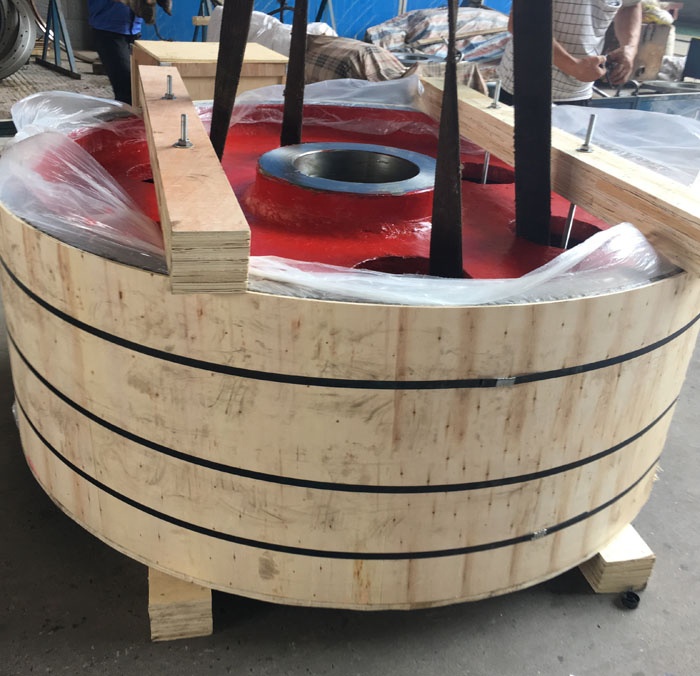
FAQS of Sheave
1.How long is the lead time?
The lead time for standard products is usually 45-60 Days, depending on the number and complexity of the order. For urgent orders, we can also arrange urgent production to shorten the delivery time as much as possible. We will make a detailed production plan according to your needs and communicate the progress in time.
2. Do you provide customized service?
Yes, we offer a full range of customized services to design and manufacture non-standard gears according to your special needs. Whether it is size, material or surface treatment requirements, we are flexible to ensure that we provide you with the most suitable solution. Please provide detailed technical specifications so that we can quote accurately.
3.How do you guarantee the quality?
We implement a total quality management system, from raw material procurement to finished products, every link is strictly tested. Advanced equipment such as hardness tester is used for accurate measurement, and strict heat treatment process is implemented to ensure the quality of each product is stable and reliable.
4.What are the choices of materials produced in your factory?
We offer a wide selection of materials, including cast iron, cast steel and alloy steel, depending on your application needs. Each material has its own specific mechanical properties, such as wear resistance, strength and toughness. We can recommend the most suitable materials according to your specific requirements.
REQUEST A QUOTE
RELATED PRODUCTS
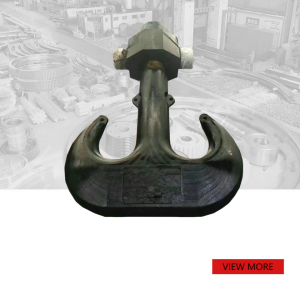
Custom forged alloy steel large crane hook
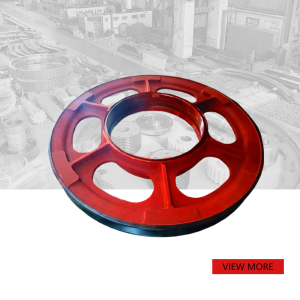
Casting large diameter wear resistant pulley mining dragline
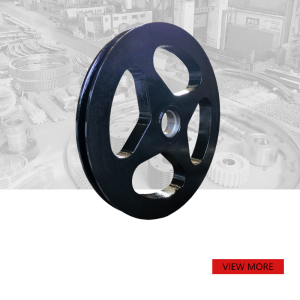
Forging rope wheel for Crane
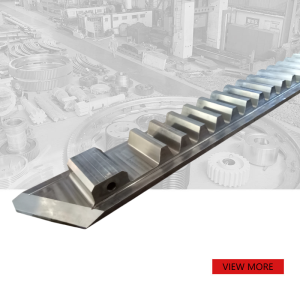
Large mining machinery forging large module helical gear rack
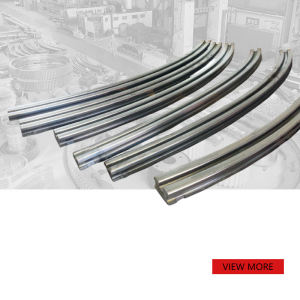
Forging wear-resistant mining machinery spare parts Segment Rail
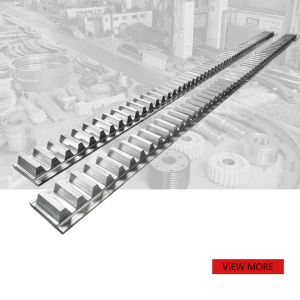