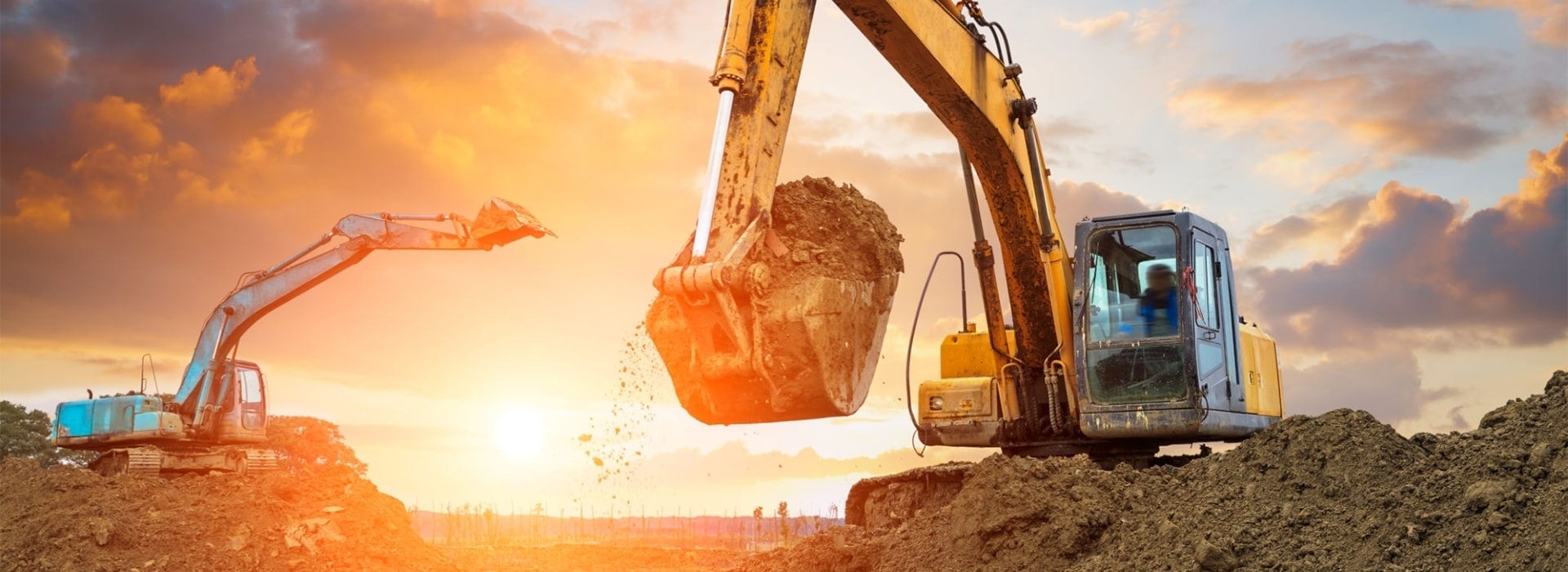
Non-standard alloy steel large Double helical gear shaft with cutting groove
PRODUCT PARAMETERS
Description
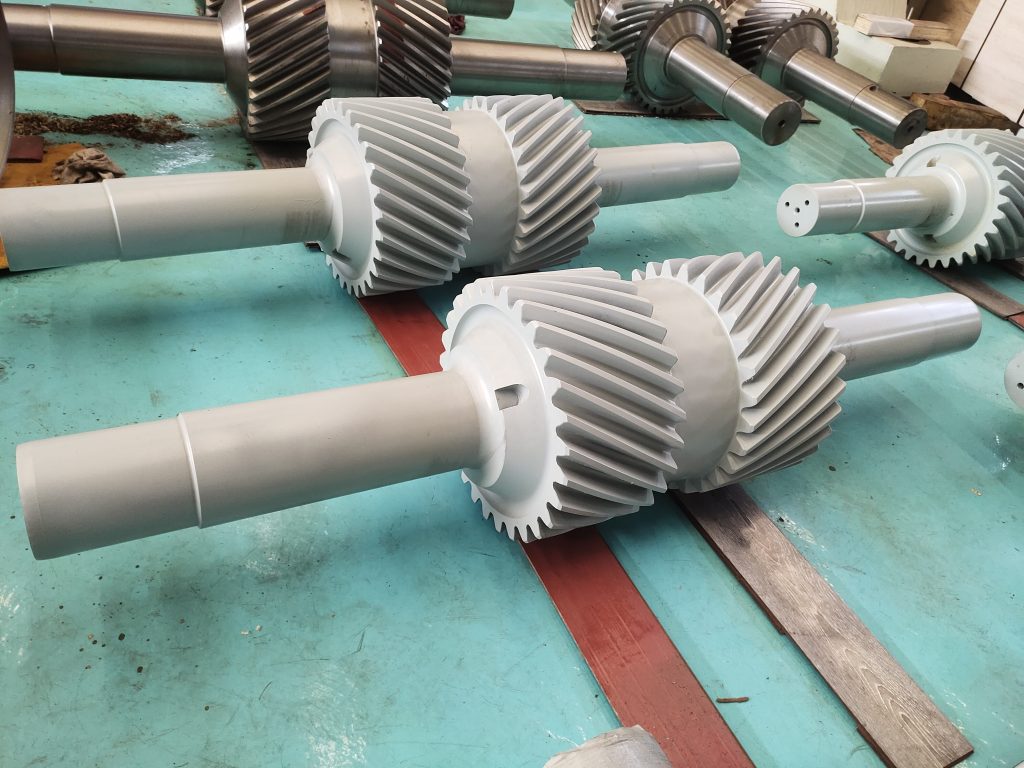
Overview of Double-helical gear shaft
Herringbone gear shaft (Double helical gear shaft) with cutting groove is widely used in mining machinery, mainly for efficient transmission of large torque and high load, to ensure the stable operation of heavy equipment. The retracting groove is designed to facilitate machining and maintenance, reduce stress concentration and extend service life. Its special structure effectively responds to the harsh conditions and high strength needs in mining operations, improves transmission efficiency, reduces the failure rate, and ensures the reliability and safety of mining and transportation equipment, which is an indispensable key component of mining machinery.
Q | A | Q | A |
Product name | Double-helical gear shaft | Delivery time | 75-90Days |
Material | Forged Iron | Defect Control | UT, MT |
Process | Forging +CNC machining+HT | Color | Custom |
outer diameter | According to the drawings | weight (kg) | 2680 |
Heat Treatment | Quenching & Tempering | Certificate | ISO9001 |
Production process of Double-helical gear shaft
Forging
Material selection: Usually use high-quality carbon steel or alloy steel, these materials have good mechanical properties and weldability.
The steel is heated to the appropriate temperature (usually around 1200°C) to soften it for molding. Forging and pressing the heated steel by means of hydraulic press or hammering to form a preliminary shape. This step can eliminate internal defects, refine grain structure, and improve material strength.
Rough Machining
In the roughing stage, the numerical control lathe is used for preliminary forming of the blank, including cutting out the basic shape and reserving the slot position. The aim is to remove excess material and achieve close to the design size, while ensuring the exact position of the retracting slot. This process requires accurate calculation of cutting parameters to avoid excessive cutting resulting in material waste or insufficient cutting affecting the quality of finishing.
Heat treatment
Heat treatment is an important step to improve the mechanical properties of herringbone gear shaft, usually including quenching and tempering processes. Hardness and toughness are enhanced by rapidly cooling the workpiece after heating to a specific temperature (quenching), and then heating it again at a lower temperature for a period of time (tempering). Reasonable selection of heat treatment process parameters is very important to prevent deformation and cracking.
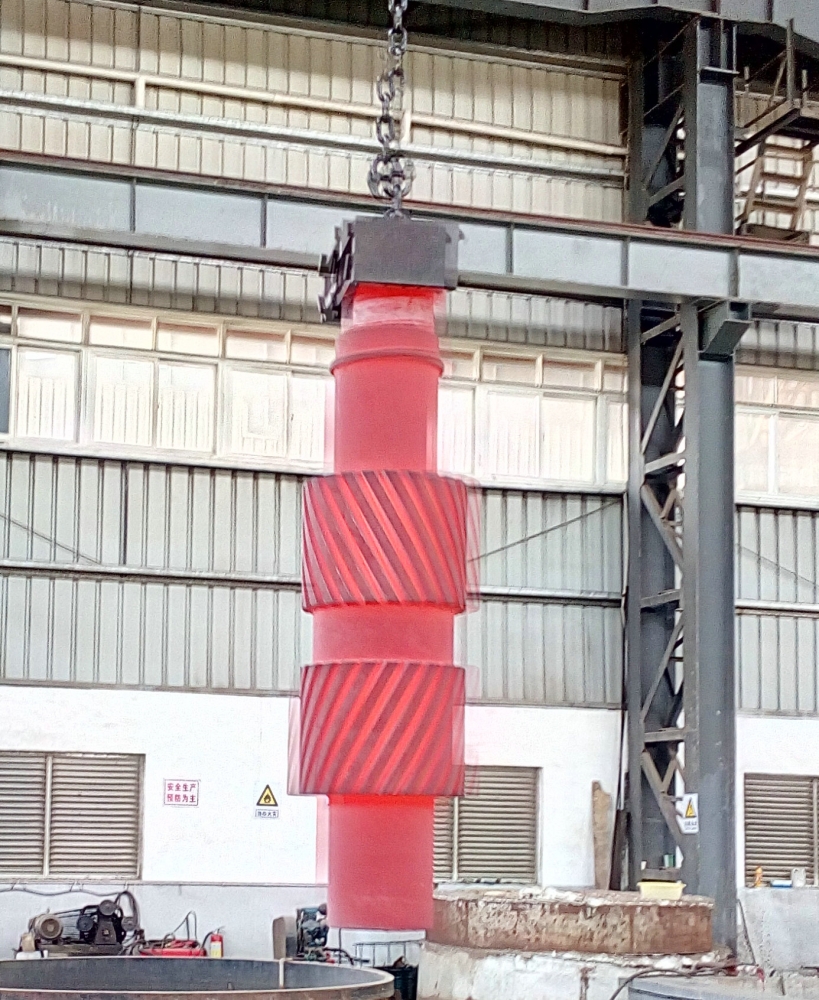
Finishing Machining
Enter the finishing process, the use of high-precision grinding machine and special gear processing equipment to fine machining the gear part, and precisely make the tool groove. This step focuses on improving the surface finish and dimensional accuracy, especially the gear profile accuracy and the shape tolerance of the retracting groove. This process requires rigorous quality monitoring to ensure that the final product meets design criteria and functional requirements.
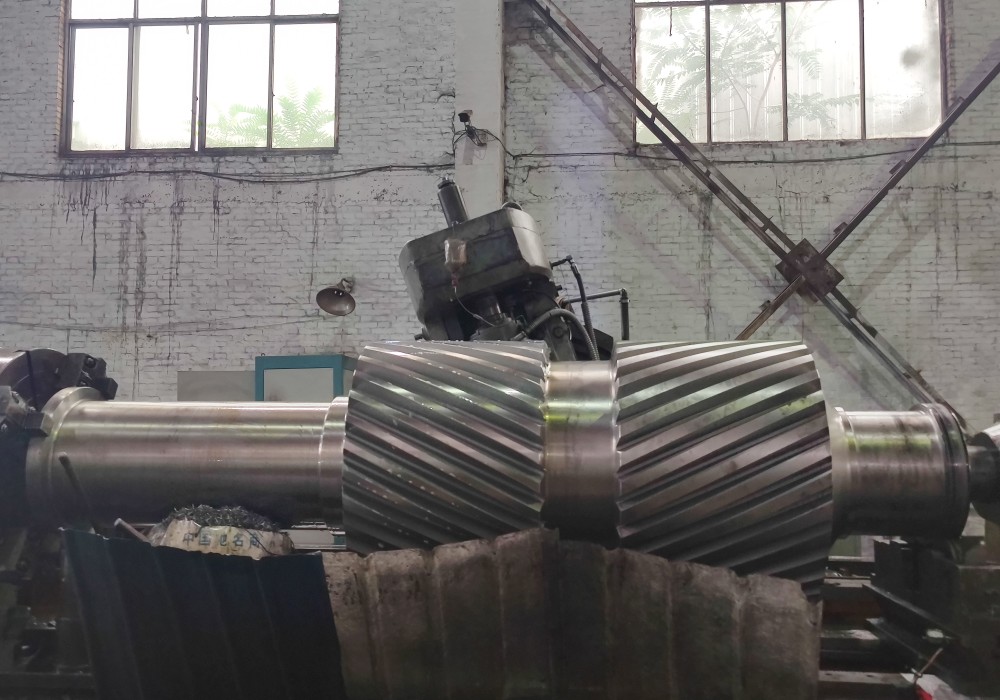
Package of Double-helical gear shaft
Cleaning treatment to remove surface impurities, anti-rust treatment to prevent oxidation, the selection of appropriate packaging materials such as wooden boxes or cartons, and add anti-shock cushion protection, and finally identify product information and handling precautions to ensure transportation safety.
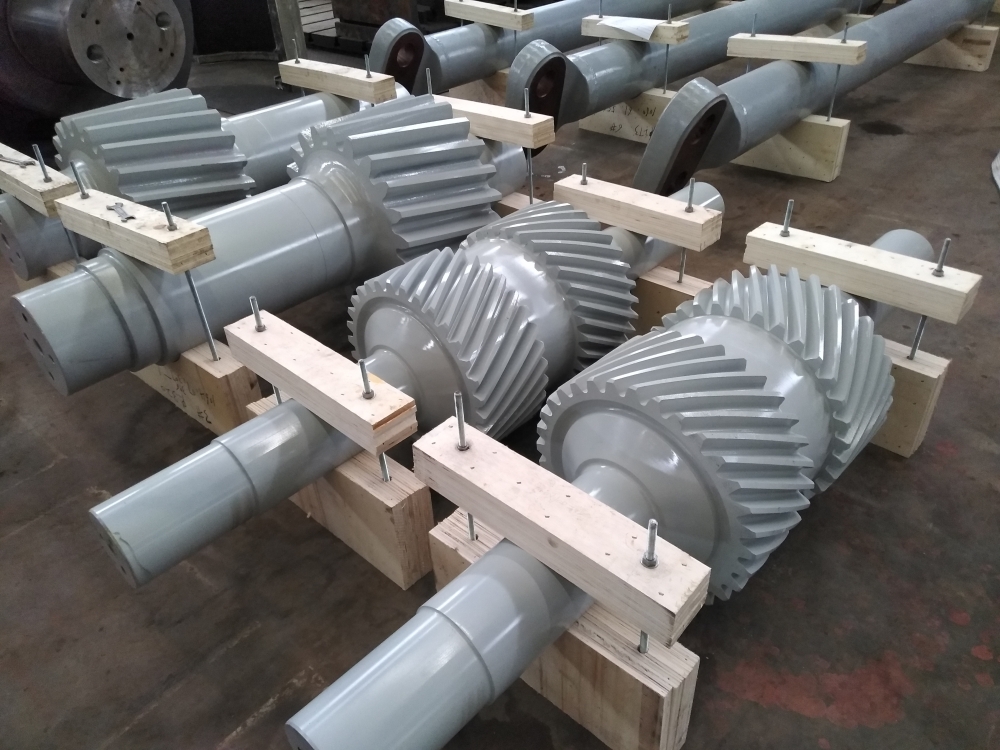
FAQs of Double-helical gear shaft
1.What is the accuracy grade you can achieve? –6-8
2.What kind of payment terms do you have? –T/T & L/C
3.Are you subject to third-party testing?-Yes
4. What’s your ship method?– By sea. By rail. By air.
REQUEST A QUOTE
RELATED PRODUCTS
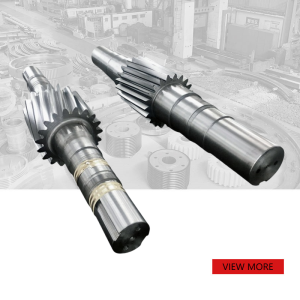
Mining custom forging large module helical gear shaft
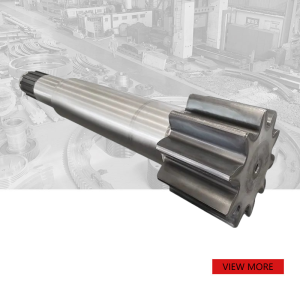
Spur gear shaft forging high quality large diameter surface quenched
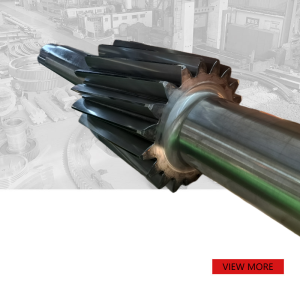
Custom Forged 42CrMo Non-standard Gear Shaft
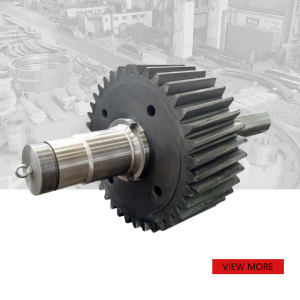
Spur gear shaft forging high quality large diameter Ball Mill
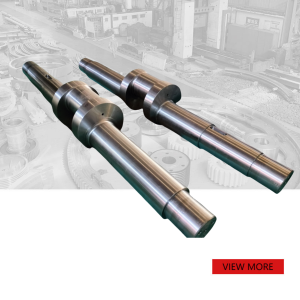
Nonstand custom long forging crankshaft
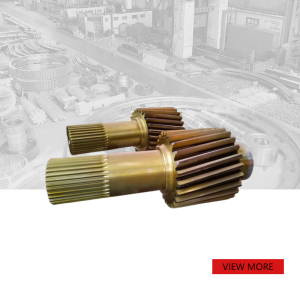