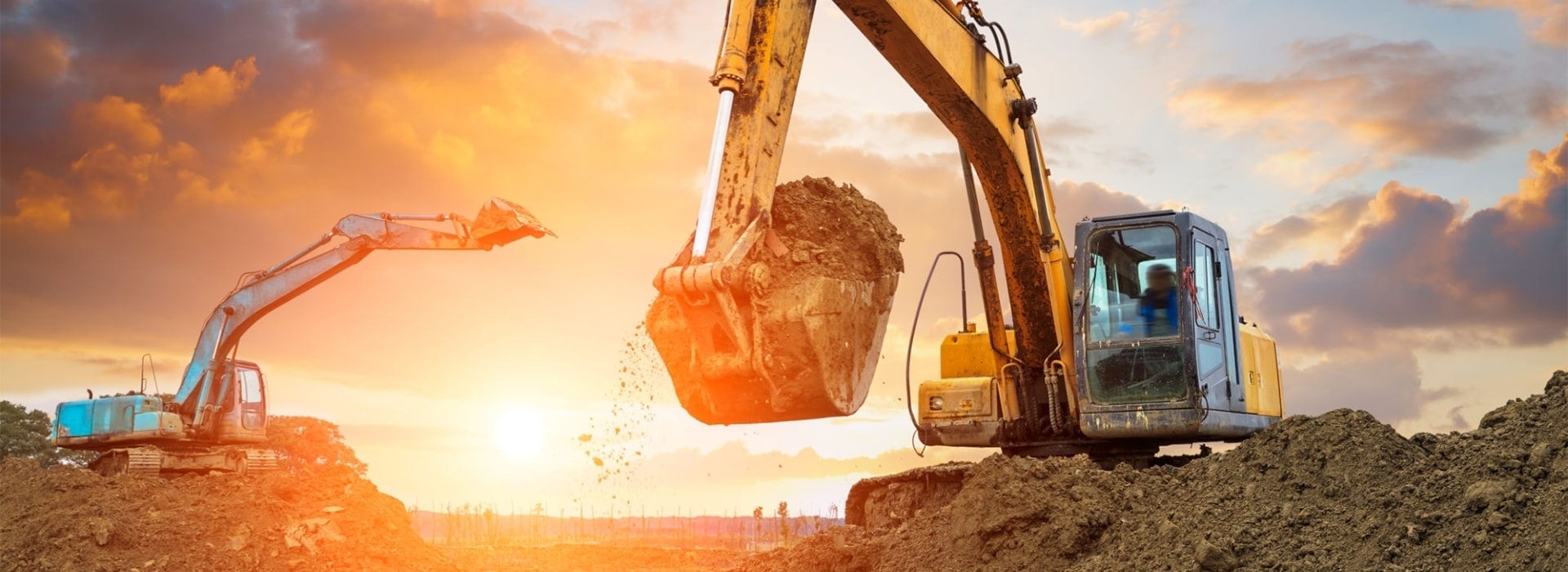
Comparative analysis of forged gear and cast gear
In mechanical manufacturing, gear are an indispensable key component in the transmission system. According to different production processes, gears can be divided into two categories: forged gears and cast gears. These two processes have their own advantages and disadvantages and show different performance characteristics in different application scenarios. The following is a detailed comparison of forged gears and cast gear in terms of material utilization, mechanical properties, manufacturing cost, production efficiency and scope of application.
一. Definition and basic principles
1. Forged gear
Forging is a processing method that causes plastic deformation of metal materials by applying pressure. Forged gear usually adopt a hot or cold forging process. The metal blank is heated and pressed into shape by die and then fine-processed to achieve the required dimensional accuracy and surface quality. Forging can significantly improve the strength and toughness of the material and is suitable for high-load and high-speed working environments.
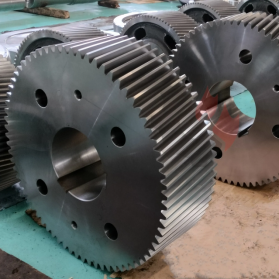
2. Casting gear
Casting is a process in which liquid metal is injected into a mold, cooled, and solidified. Casting gear are manufactured by sand casting or precision casting to complete the blank and then machined. The casting process can realize the manufacturing of parts with complex shapes, which is suitable for mass production and the production needs of large parts.
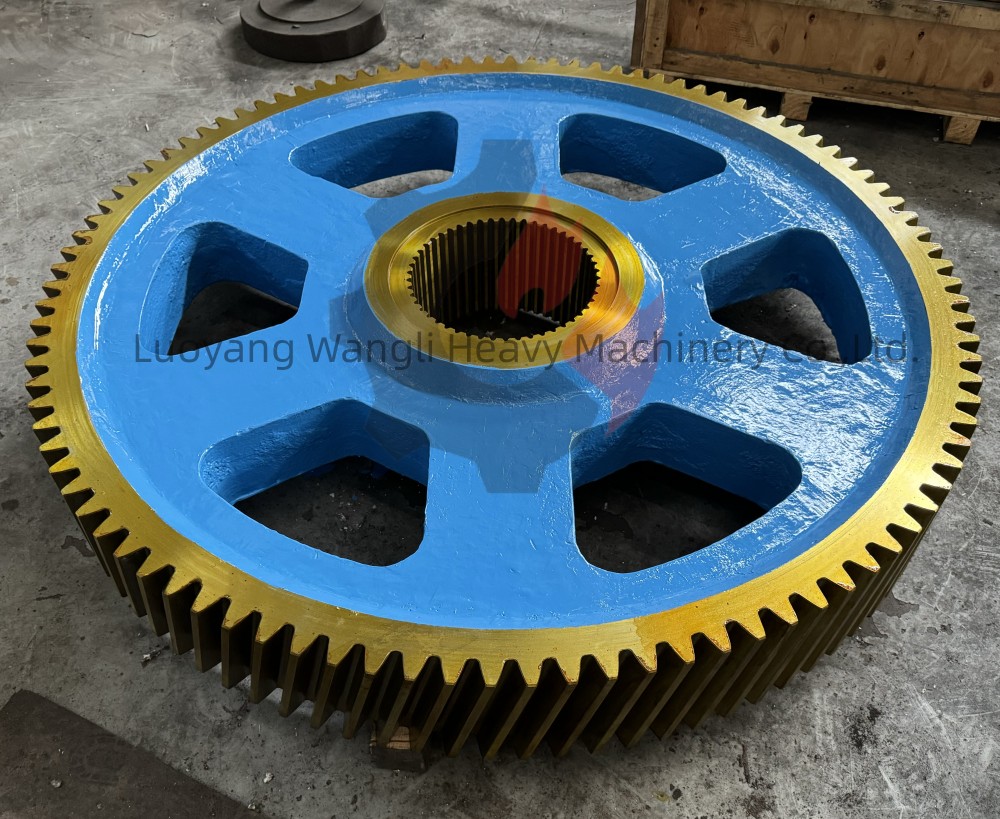
二. Comparison of mechanical properties
1. Strength and toughness
Due to the rearrangement and densification of their internal grain structure, forged gear have higher tensile strength, yield strength, and impact toughness. These characteristics make forged gear more suitable for high loads, high-impact forces and frequent start-stop conditions.
Although the performance of cast gear can be improved by optimizing the alloy composition, the overall strength and toughness are slightly inferior to those of forged gear due to possible defects such as pores and shrinkage inside.
2. Wear resistance and fatigue life
Forged gear have better material density and uniformity of organization and show better wear and fatigue resistance, especially under long-term operation or high-stress cycle conditions.
Cast gear have relatively low wear resistance and fatigue life due to the possible microscopic defects inside. However, they can still meet the requirements in some low-load or non-critical applications.
三. Material utilization and manufacturing cost
1. Material utilization
The forging process requires a large margin for subsequent processing, so there is a lot of material waste, mainly when producing large-sized gear, the material utilization rate is low.
The casting process can directly form a blank close to the final shape according to the design, reducing the amount of subsequent processing and thereby improving material utilization.
2. Manufacturing cost
The manufacturing cost of forged gear is high, especially for small or medium-sized gear, because the forging equipment investment is significant, the energy consumption is high, and complex mold development and maintenance are required.
The cost of cast gear is relatively low, especially in mass production or the manufacture of complex-shaped parts; its economic advantages are obvious.
四. Production efficiency and flexibility
1. Production efficiency
The forging process is suitable for small and medium-sized batch production, especially the manufacture of standardized gear. However, when faced with complex geometries or oversized gear, the forging efficiency will be limited.
The casting process is very suitable for mass production, especially for the manufacture of gear with complex structures or unique shapes. In addition, the development of modern precision casting technology has further improved the quality and precision of castings.
2. Design flexibility
The forging process is limited in its adaptability to part shapes and makes it difficult to meet the needs of complex structures.
The casting process has extremely high design flexibility and can realize the manufacture of parts of almost any shape, providing more possibilities for product innovation.
五. Scope of application and typical applications
1. Application of forged gear
Forged gear are widely used in the automotive industry, aerospace, wind power generation and other fields. For example, most gear in automobile gearboxes use forging technology to ensure their reliability in high-speed operation and high-torque transmission.
In the wind power industry, key gear in spindle gearboxes also use forging technology to cope with harsh working environments and long-term operation requirements.
2. Application of cast gears
Cast gear are often used in construction machinery, mining equipment, ship propulsion systems and other fields. For example, the gear in the excavator’s crawler drive usually use casting technology because they do not require high precision but have strict restrictions on size and weight.
Cast gear are also highly cost-effective in some low-cost and low-precision application scenarios (such as agricultural machinery).
Forged gear and cast gear have their advantages, and the specific choice should be weighed according to actual needs. If you pursue high strength, high toughness and long life, you should give priority to forged gear; if you focus on cost control, design flexibility and mass production capacity, cast gear are more advantageous. In the future, with the continuous emergence of new materials and new processes, the two processes are expected to find a better balance between performance and economy and promote the development of the gear manufacturing industry to a higher level.