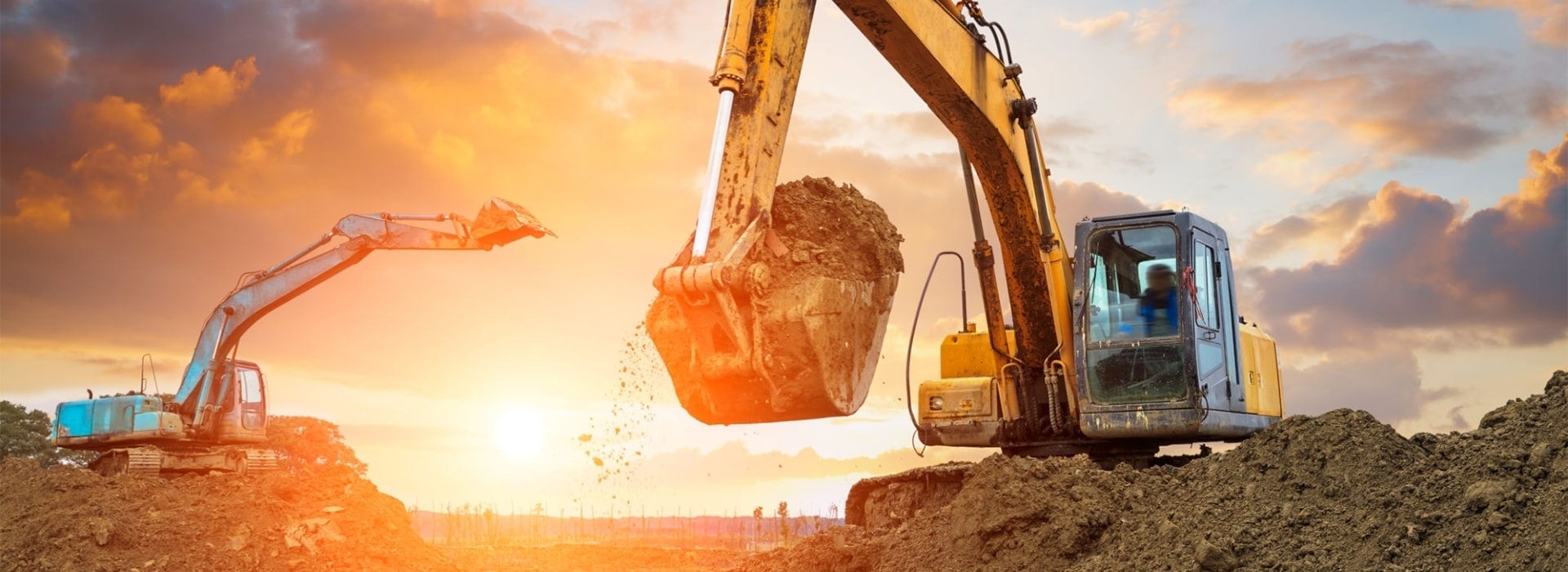
Rotary kiln Tire:Maintenance and care of rotary kiln tire
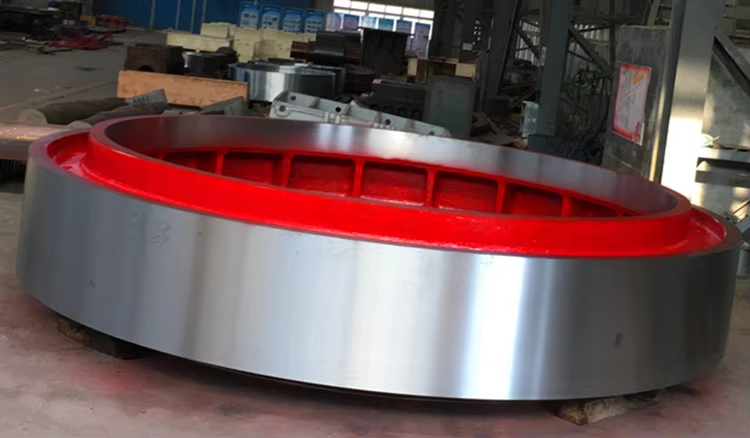
一. Basic structure and function of rotary kiln tire
1. Definition and function
The tire is a set of annular metal components installed on the outside of the Rotary kiln shell, usually made of high-strength cast steel or forged steel. Its main functions include:
Supporting function: It bears the weight of the Rotary kiln shell and its internal materials through contact with the tugboat.
Guiding function: Ensure that the kiln body maintains the correct centerline position during rotation to avoid deviation or shaking.
Heat dissipation: Since the wheel band is in direct contact with the kiln body, it can effectively disperse the heat on its surface and prevent local overheating from causing deformation.
2. Structural features
The rotary kiln tire usually consists of the following parts:
Main body: The rotary kiln tires main body is a cylindrical or slightly tapered ring structure, and the outer surface is precisely processed to ensure good contact with the support roller.
Connectors: The rotary kiln tire is fixed to the kiln body by bolts or other fasteners to ensure its firmness and reliability.
Cooling device: To reduce the impact of a high-temperature environment on the rotary kiln tire, some high-end designs will be equipped with water-cooling or air-cooling systems to extend their service life.
The rotary kiln tire design must consider strength, rigidity and heat resistance to adapt to the rotary kiln’s long-term high-temperature and high-load working conditions.
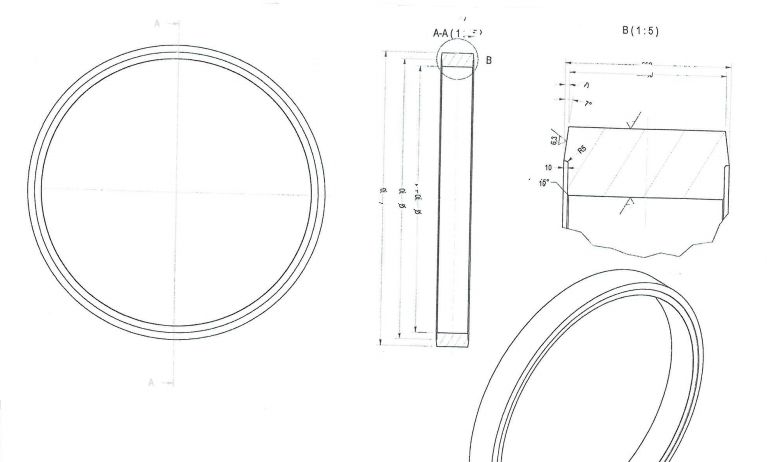
二. Common faults and causes of rotary kiln tire
Although the rotary kiln tire has high strength and wear resistance, it may still fail due to various factors during long-term operation. The following are several standard rotary kiln tires problems and their causes:
1. Wear of rotary kiln tires
Phenomenon: grooves, pits or uneven wear on the outer surface of the rotary kiln tire.
Cause:
Poor lubrication between the support roller and the rotary kiln tire leads to increased dry friction.
The center line of the kiln body is offset, causing excessive force on the rotary kiln tire locally.
The hardness of the wheel tire material is insufficient, or the manufacturing precision is not high.
Effect: Wear of the rotary kiln tires will reduce the contact surface of the support roller, increase vibration and noise, and even cause shutdown accidents in severe cases.
2. Deformation of rotary kiln tire
Phenomenon: The ovality of the rotary kiln tire increases or bends locally.
Cause:
Long-term high temperature causes the material performance to deteriorate and permanent deformation occurs.
Improper adjustment of the support device causes an uneven force on the kiln body.
Too much ringing or accumulation of materials in the kiln increases the load on the rotary kiln tire.
Effect: Deformation of the rotary kiln tire will aggravate the wear of the support roller and may also cause the kiln body to shake or tilt.
3. Loose rotary kiln tire
Phenomenon: The connecting bolts between the rotary kiln tire and the kiln body are loose or broken.
Cause:
The screw bolt preload is insufficient or not checked regularly.
The bolts creep in high-temperature environments, resulting in a loose connection.
The kiln body vibrates too much, causing an impact on the connecting parts.
Influence: A loose rotary kiln tire will affect the stability of the kiln body and increase the risk of failure.
4. Overheating of rotary kiln tire
Phenomenon: The surface temperature of the rotary kiln tire rises abnormally and even turns red.
Cause:
The cooling system fails or is designed unreasonably.
The flame distribution in the kiln body is uneven, resulting in local overheating.
The rotary kiln tire has poor contact with the tugboat, generating additional friction heat.
Influence: Overheating of the rotary kiln tire will accelerate material aging and shorten its service life.
三. Maintenance strategy of rotary kiln tire
In order to extend the service life of the rotary kiln tire and reduce the failure rate, a scientific and reasonable maintenance strategy must be formulated. The following are several standard maintenance methods:
1. Preventive maintenance
Check the rotary kiln tire status regularly, including surface wear, the tightness of the connecting bolts, and the cooling system’s operation status.
Carry out daily monitoring of auxiliary systems such as lubricating oil and cooling water to ensure their regular operation.
Develop a detailed maintenance plan and perform various maintenance tasks in a cycle.
2. Predictive maintenance
Use sensors and data analysis technology to monitor the operating status of the rotary kiln tire in real-time.
Detect potential problems in advance through vibration analysis, temperature detection and acoustic diagnosis.
Establish a fault prediction model based on historical data to achieve precise maintenance.
3. Corrective maintenance
Take timely measures to repair the rotary kiln tire after the rotary kiln tires fails.
Replace or repair damaged parts to restore their original performance.
Analyze the cause of the failure, improve related designs or operating procedures, and avoid similar problems from happening again.
4. Improvement Maintenance
Propose optimization plans for defects or deficiencies in existing equipment.
Introduce new technologies, new materials or new processes to improve the overall performance of the rotary kiln tire.
Revise and improve operating procedures to improve the technical level of employees.

四. Specific maintenance methods for rotary kiln tire
1. Surface inspection and treatment
Visual inspection: Regularly observe whether there are cracks, pits or other damage on the surface of the rotary kiln tires. If problems are found, they should be recorded and handled in a timely manner.
Grinding repair: For minor wear or scratches, a grinding machine can be used for local grinding to restore surface flatness.
Coating protection: Spray a protective layer (such as ceramic coating or high-temperature resistant paint) on the surface of the rotary kiln tire to enhance its corrosion resistance and wear resistance.
2. Connection bolt management
Regular tightening: According to the maintenance plan, regularly check and tighten the connection bolts between the rotary kiln tire and the kiln body to ensure that their preload meets the requirements.
Replace aging bolts: Older or damaged bolts caused by high temperature or vibration should be replaced as soon as possible.
Anti-loosening measures: Use double nuts, spring washers or other anti-loosening devices to prevent bolts from loosening.
3. Cooling system maintenance
Water cooling system: Check whether the cooling water pipeline is unobstructed and whether the water pump and valve are working correctly. Clean the scale or impurities in the pipeline regularly to ensure the cooling effect.
Air cooling system: Clean the fan blades and filter to ensure smooth air circulation. Check the operating status of the fan motor to avoid cooling failure due to malfunction.
Temperature monitoring: Install temperature sensors to monitor the surface temperature of the rotary kiln tire in real time. Once the set value is exceeded, take cooling measures immediately.
4. Lubrication management
Choose the right lubricant: According to the working conditions, select a special grease that is resistant to high temperature and oxidation to ensure that a good lubricating film is formed between the support roller and the rotary kiln tire.
Add grease regularly: Add grease regularly according to the maintenance plan to avoid dry friction caused by insufficient lubrication.
Clean old oil stains: Regularly remove old oil stains and impurities on the surface of the rotary kiln tires to keep the contact surface clean.
5. Centerline correction
Measure straightness: Use a laser measuring instrument or other tools to regularly check the centerline position of the kiln body to ensure that its deviation is within the allowable range.
Adjust the position of the tug: If the kiln body is found to be offset, the centerline can be corrected by adjusting the position of the support roller.
Eliminate accumulation: Clean the rings or accumulations in the kiln in time to reduce the load on the rotary kiln tire.
五. Best practices for rotary kiln tire maintenance
1. Establish a sound management system
Develop a detailed maintenance manual to clarify the responsible persons and time nodes for each task.
Implement the “point inspection and scheduled maintenance” system to combine daily inspection with regular maintenance.
Establish equipment files to record the content and results of each maintenance to provide a basis for subsequent analysis.
2. Strengthen personnel training
Organize technical personnel to participate in professional training to learn advanced maintenance technology and management concepts.
Regularly carry out internal exchange activities to share experiences and lessons and improve the overall level of the team.
Strengthen safety awareness education to eliminate illegal operations.
3. Introduce intelligent technology
Equipped with an online monitoring system to collect the operating parameters of the rotary kiln tire in real time.
With the help of a big data analysis platform, hidden fault hazards are discovered.
Apply remote diagnostic tools to achieve expert remote guidance and technical support.
4. Focus on environmental protection and energy saving
Optimize the design of the cooling system to reduce energy consumption and emissions.
Improve sealing performance and reduce heat loss caused by air leakage.
Recycle waste heat resources for preheating raw materials or other purposes.