Ball Mill: A Comprehensive Analysis of Types, Parameters, and Maintenance
The ball mill is a crucial member of the mining machinery family and is widely used in ore crushing, building material production, and various chemical industries. It grinds materials into fine powder through its rotating cylinder and grinding media (such as steel balls or ceramic balls).
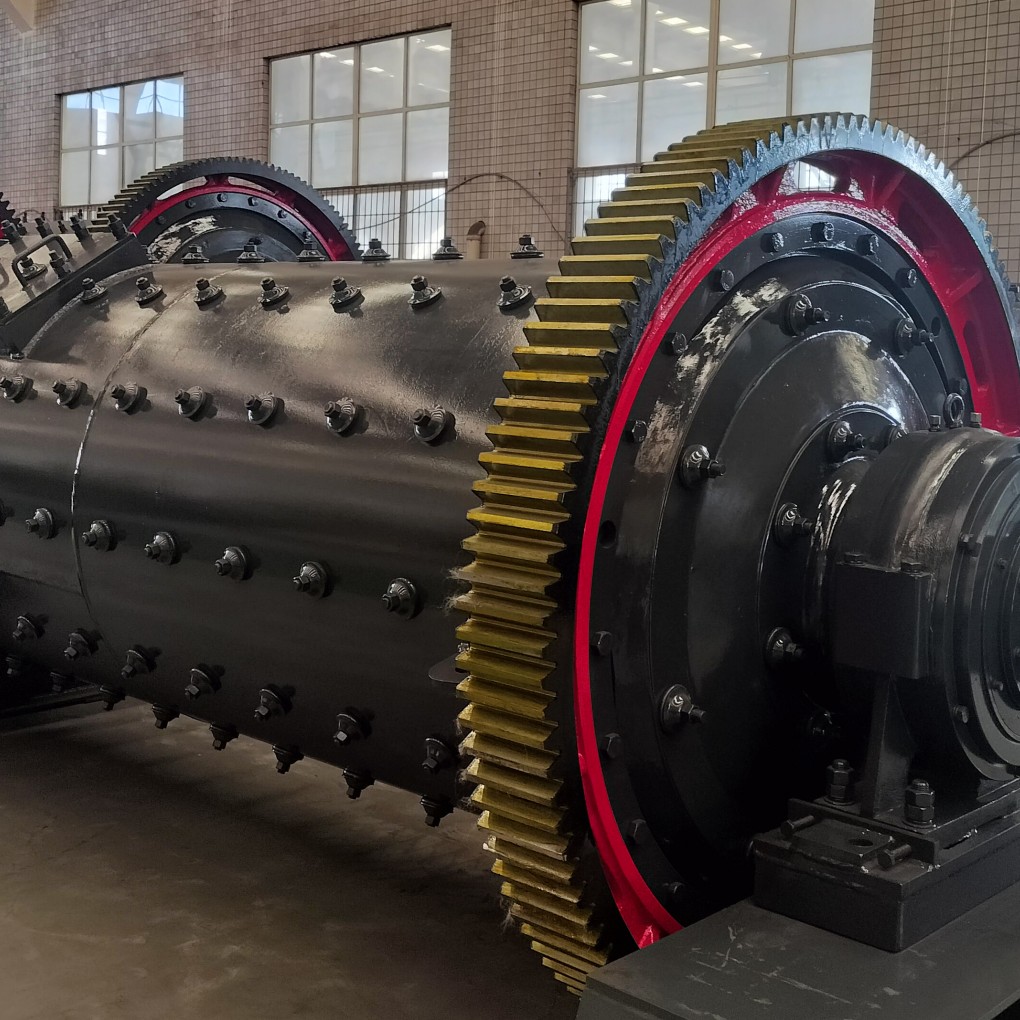
Main Types of Ball Mill
Ball mill can be classified into several main types based on their structural characteristics and application scenarios:
1.Grate Discharge Ball Mill:
Advantages:
The forced discharge design improves processing capacity.
Suitable for coarse grinding operations with high efficiency.
Disadvantages:
Complex structure, leading to higher maintenance costs.
Higher initial investment.
Applications: Initial grinding processes in metal mines.
2.Overflow Ball Mill:
Advantages:
Simplified structure without a grate plate, making it easier to maintain.
Suitable for fine grinding, producing uniform particle sizes.
Disadvantages:
Slower discharge speed, affecting processing capacity.
Applications: Fine grinding of non-metallic minerals.
3.Batch Ball Mill:
Advantages:
Can stop feeding for cleaning or replacing grinding media within a certain time.
Ideal for small-scale production and laboratory research.
Disadvantages:
Low production efficiency, unsuitable for large-scale production.
Applications: Laboratory experiments or small-batch production.
4.Continuous Ball Mill:
Advantages:
Capable of continuous feeding and discharging, enabling large-scale production.
High level of automation with simple operation.
Disadvantages:
Large equipment size, requiring significant floor space.
Higher investment costs.
Applications: Industrial-scale mineral processing.
Overview of Key Technical Parameters
Understanding the technical parameters of ball mills is essential for selecting the appropriate equipment. Below is a comparison table of technical parameters for different types of ball mills:
Parameter Name | Small Ball Mill | Medium Ball Mill | Large Ball Mill |
Cylinder Diameter (mm) | 900 | 1830 | 4500 |
Cylinder Length (mm) | 1800 | 3000 | 6000 |
Production Capacity (t/h) | 0.65-2 | 4.5-12 | 100-120 |
Main Motor Power (kW) | 18.5 | 110 | 1800 |
These parameters highlight the differences in processing capacity, energy consumption, and other aspects, helping users make informed decisions based on their specific needs.
Daily Maintenance and Care
To ensure the long-term stable operation of a ball mill, regular maintenance and care are indispensable. Here are some basic maintenance tips:
1.Gear Inspection:
Regularly check the wear condition of gears and lubricate or replace them as needed.
Use high-quality lubricants to reduce friction and extend gear life.
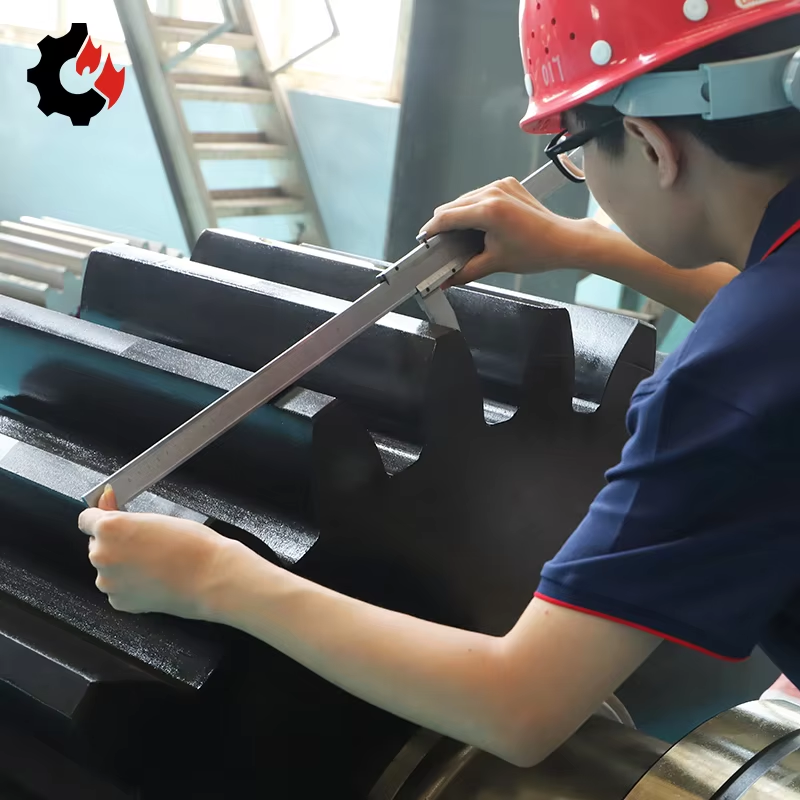
2.Cleaning:
Regularly clean residual material inside the cylinder to prevent blockages that could affect efficiency.
Inspect seals to ensure they are intact and prevent dust from entering, which could impact machine performance.
3.Safe Operation:
Follow operating procedures strictly and avoid overloading the machine.
Before performing any maintenance, always disconnect the power supply and take necessary safety precautions.
4.Monitoring Systems:
Utilize modern monitoring technologies to track the operating status of the ball mill in real-time and detect potential issues promptly.
Regularly inspect and adjust components according to the equipment’s user manual.
The ball mill plays an indispensable role in various industries as an important piece of industrial equipment. By gaining a deeper understanding of its types, technical parameters, and maintenance requirements, not only can we choose the most suitable products, but we can also effectively enhance the service life and operational efficiency of the equipment.