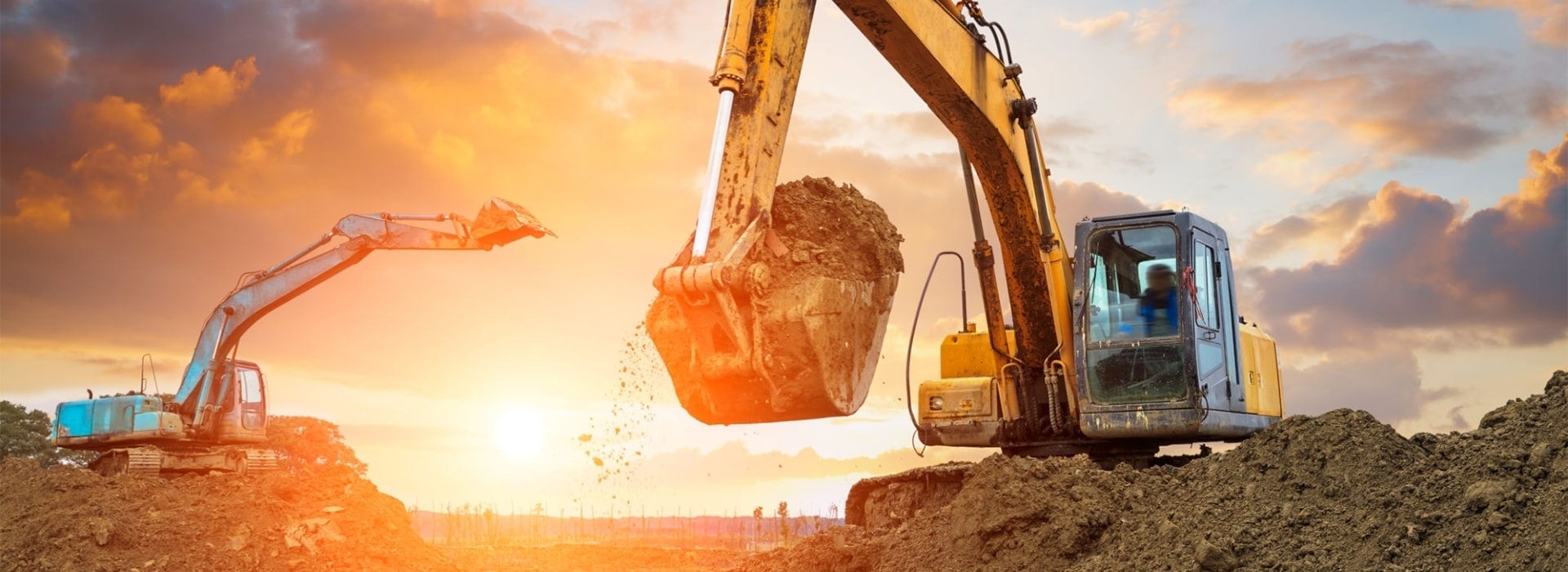
Optimization design and fatigue life analysis of large-module gear shaft
With the development of industrial technology, the requirements for mechanical transmission systems are increasing day by day, especially in equipment working under heavy load and high-speed operation conditions. As one of the key components, the performance of large-module gear shafts directly affects the reliability and efficiency of the entire system. This article will explore how to improve the fatigue resistance and service life of gear shaft by improving design parameters (such as tooth shape, material selection, etc.).
1. Optimization of tooth shape design
Tooth shape is one of the important factors that determine gear performance. Although the traditional involute tooth shape is widely used, it may have stress concentration problems under certain specific working conditions. In recent years, researchers have proposed a variety of new tooth shape design schemes to improve contact stress distribution, reduce local stress peaks, and thus extend the service life of gear shafts. For example, the use of variable curvature tooth shape or asymmetric tooth shape can effectively reduce the maximum bending stress at the root of the tooth while maintaining high transmission efficiency. In addition, through the accurate calculation and simulation of the tooth surface contact state under different construction conditions, the tooth profile parameters can be further optimized to ensure the optimal stress distribution under various load conditions.
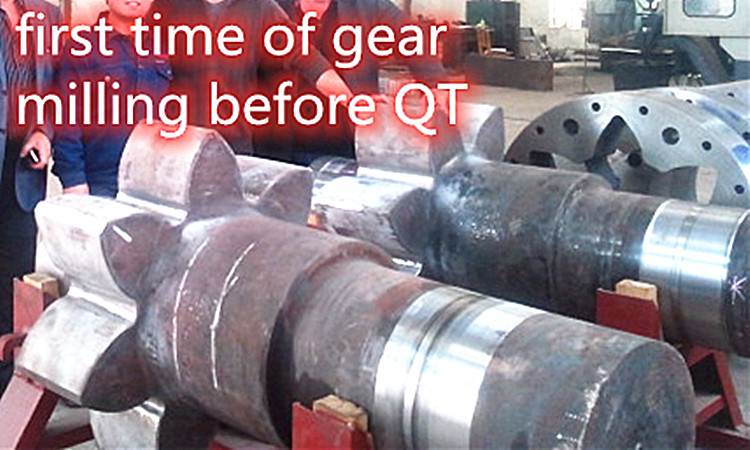
Wangli large-module gear shaft
2. Material selection and processing
Material selection is crucial to improving the fatigue resistance of gear shaft. High-strength alloy steel is widely used in the manufacture of large-module gear shaft due to its excellent mechanical properties. However, the strength of the material itself is not enough to ensure long-term stable working performance, and a reasonable heat treatment process cannot be ignored. Quenching and tempering can significantly improve the hardness and toughness of steel, but too high hardness may lead to increased brittleness, so it is necessary to adjust the process parameters according to the specific application scenario. In recent years, the application of surface modification technologies (such as nitriding, carburizing, etc.) has become more and more common.
3. Fatigue life prediction and evaluation
In order to accurately evaluate the actual service life of the gear shaft, a reliable fatigue life prediction model must be established. Based on the fracture mechanics theory and combined with finite element analysis (FEA), the stress field of the gear shaft under complex working conditions can be accurately simulated, and the fatigue crack propagation rate and remaining life can be predicted accordingly. At the same time, considering the possible random load fluctuations in the actual working environment, it is also an effective means to introduce probability statistics methods to evaluate the fatigue life probabilistically. Through the accumulation of a large amount of experimental data and data analysis, the life prediction model can be gradually improved to provide a scientific basis for design optimization.
4. Experimental verification and case analysis
Theoretical research is important, but experimental verification is also indispensable. By conducting bench tests on the physical prototype of the optimized design scheme, its performance under real working conditions can be directly observed, and first-hand data can be obtained for subsequent improvements. Taking a heavy machinery manufacturer as an example, after optimizing the design of a large-module gear shaft in one of its key equipment, after multiple iterations of improvement and rigorous testing, the service life was finally increased by about 30% compared with the original design. This not only proves the effectiveness of the above optimization measures, but also provides valuable experience for the development of similar products.
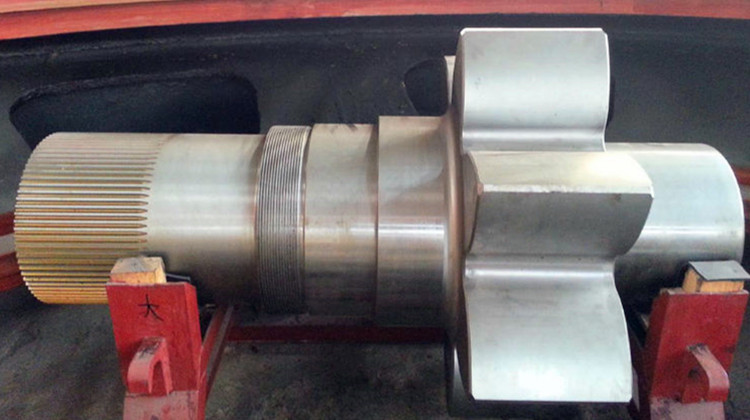
Wangli large-module gear shaft
In short, through the comprehensive optimization of tooth shape design, material selection and processing, combined with advanced fatigue life prediction technology, the fatigue resistance and service life of large-module gear shafts can be significantly improved to meet the needs of modern industry for high-performance transmission systems. Future research directions will also include more refined design methods, the application of new materials, and the development of intelligent monitoring technology, in order to further reduce costs and improve economic benefits while ensuring the safe operation of equipment.If you need to purchase large module gear shaft, please contact wl02@citicwl.com.