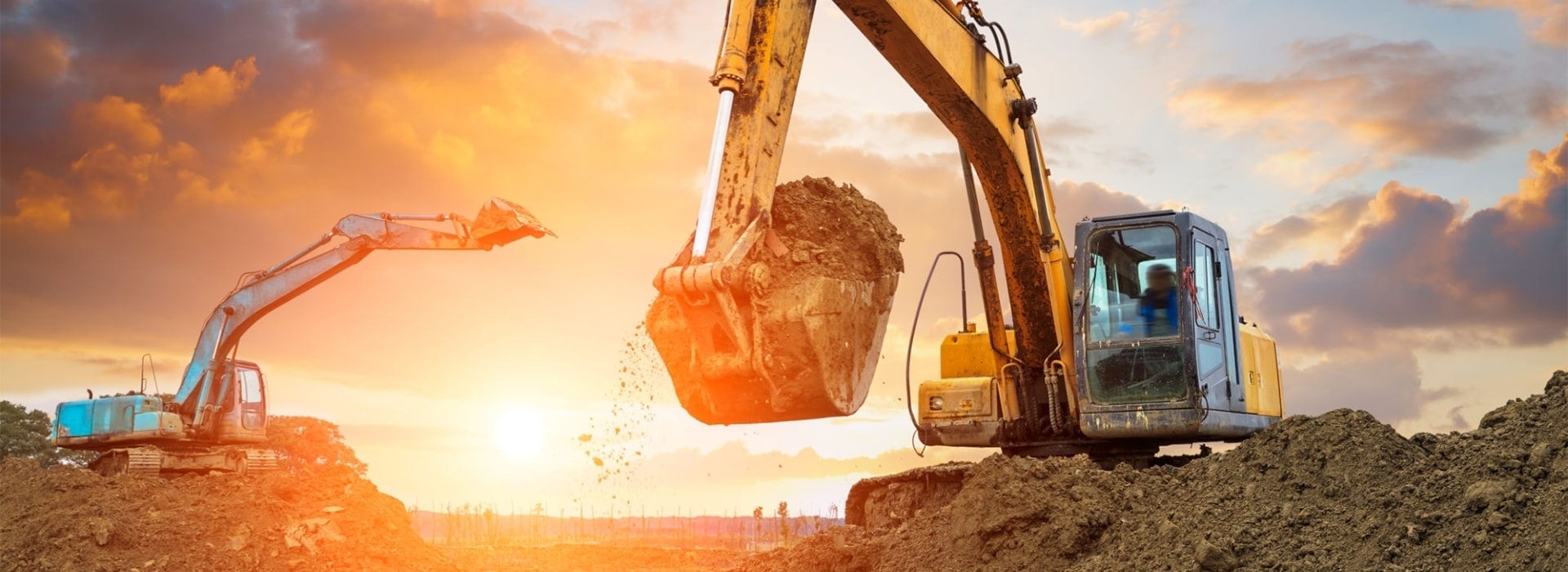
Enhancing Cement Kiln Efficiency: Cast Steel vs. Alloy Steel Ring Gear
Introduction
In modern industrial production, cement kilns are one of the key equipment, and their operating efficiency directly affects the economic benefits and environmental protection level of the enterprise. As an important part of the transmission system, the performance of the ring gear is crucial to ensure the efficient and stable operation of the cement kiln. This article will explore the impact of different materials (especially cast steel and alloy steel) on the wear resistance and fatigue resistance of cement kiln ring gear, and analyze how to improve the overall equipment efficiency by optimizing material selection.
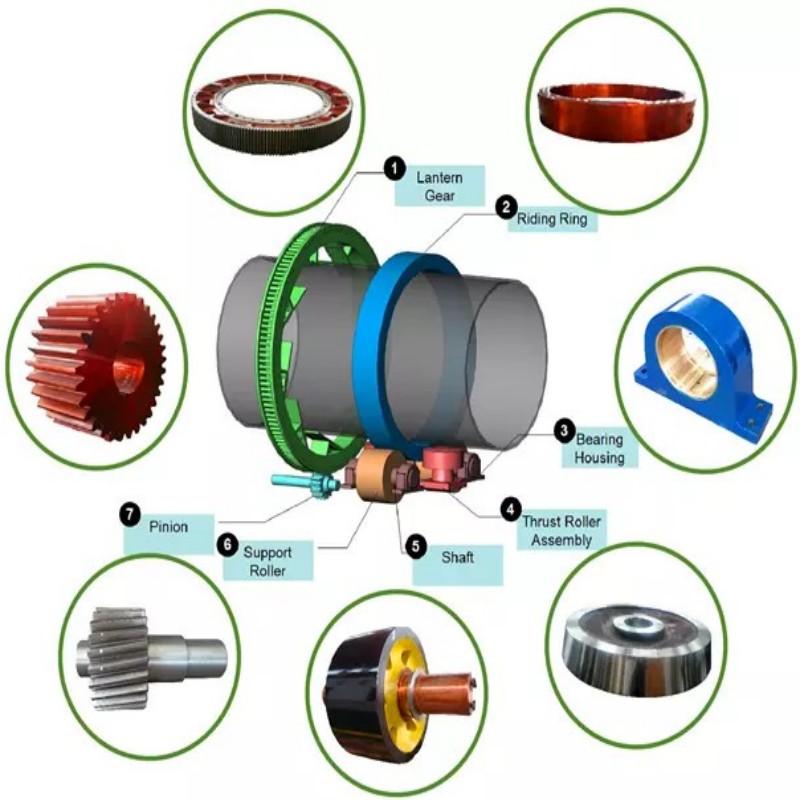
Material basis and background
Cement kiln ring gear are in a high temperature and high load working environment for a long time, requiring excellent wear resistance and fatigue resistance. Traditionally, cast steel has been widely used in ring gear manufacturing due to its good casting performance and mechanical strength. However, with the development of technology, alloy steel has gradually become an alternative with its higher hardness and better toughness.
Cast steel:
Cast steel occupies an important position in many industrial applications due to its excellent formability and cost-effectiveness. However, its relatively low hardness and wear resistance limit its service life under extreme conditions.
Alloy steel:
Alloy steel improves its physical and mechanical properties by adding elements such as chromium, molybdenum, and nickel. These alloying elements can not only significantly improve the hardness and wear resistance of the material, but also enhance its ability to resist fatigue damage.
Wear resistance comparison
Wear resistance is an important indicator to measure the service life of the ring gear. Experiments show that under the same working conditions, alloy steel ring gear have a longer service life than cast steel ring gear. This is because the alloying elements in alloy steel can form a hard phase and effectively resist wear. In addition, appropriate heat treatment processes can further improve the surface hardness of alloy steel, thereby extending the working life of the ring gear.
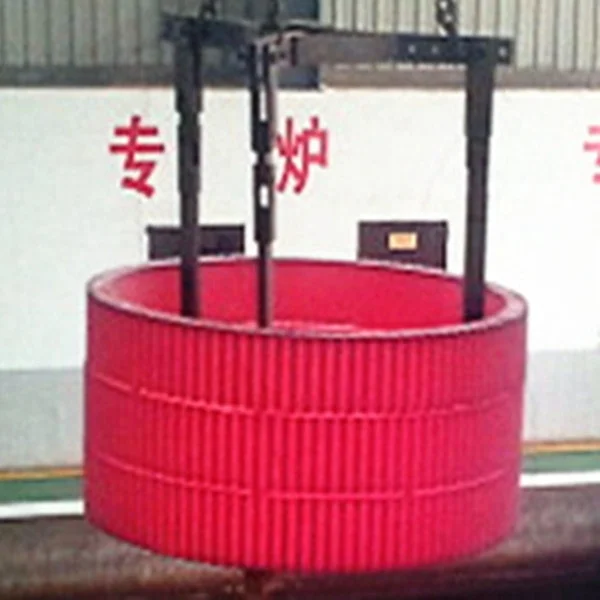
Fatigue resistance analysis
Fatigue damage is one of the main causes of ring gear failure. Due to the continuous alternating loads during the operation of cement kilns, the ring gear is prone to cracks and eventually breaks. Studies have shown that alloy steel can better disperse stress and reduce local stress concentration due to its more uniform internal microstructure, thus showing stronger fatigue resistance.
Actual case study
During the upgrade of its production line, a large cement production enterprise replaced the original cast steel ring gear with a specially heat-treated alloy steel ring gear. The results showed that the new ring gear not only improved the transmission efficiency and reduced the maintenance frequency, but also greatly extended the service life and reduced the operating cost.
Future Outlook
With the continuous development of new materials and technologies, cement kiln ring gear in the future are expected to achieve higher performance. For example, the application of nanotechnology may further improve the wear resistance and fatigue resistance of alloy steel; 3D printing technology provides new possibilities for the customized production of complex-shaped ring gear.
In short, optimizing the selection of cement kiln ring gear materials is one of the key steps to improve the overall performance of equipment. Enterprises should choose the material solution that best suits them based on actual needs and technical conditions to achieve the best economic and social benefits.