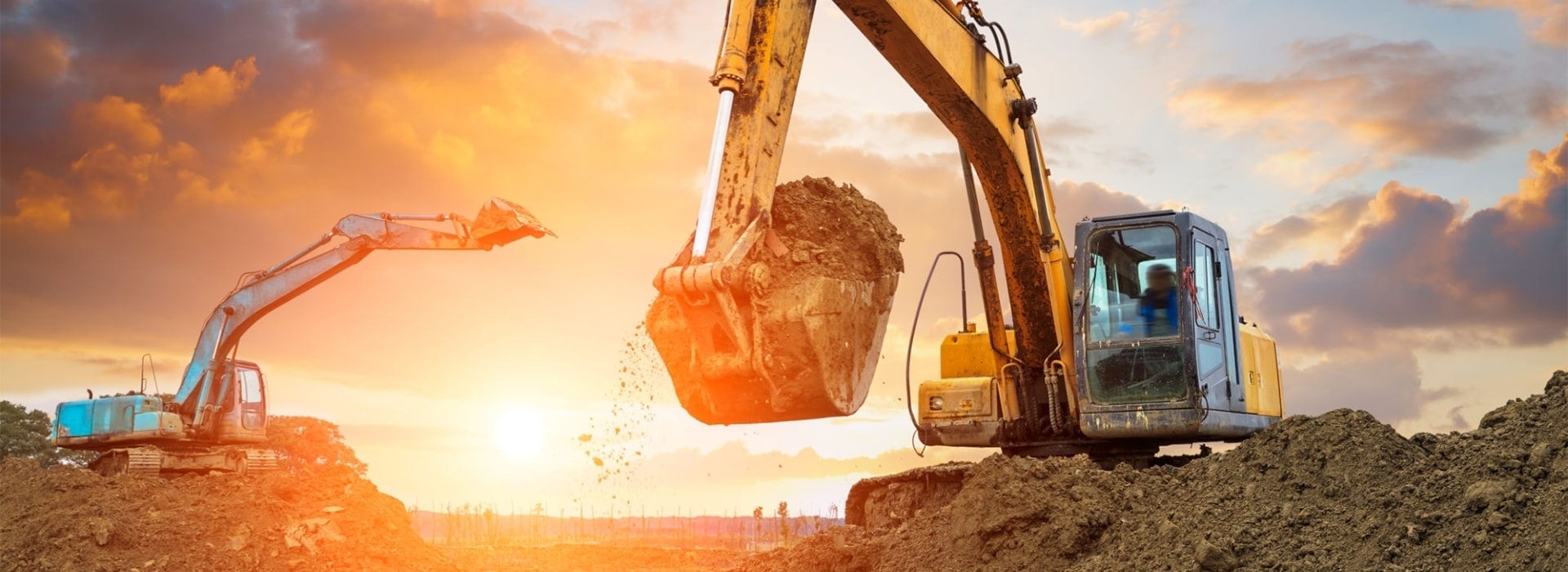
Bevel gears: Application and advantages of bevel gears in mining machinery
In the modern industrial system, mining machinery is an indispensable and essential part. Whether it is coal mining, metal ore excavation or non-metallic mineral processing, mining machinery plays a core role. As one of the key components of the transmission system, bevel gears play a vital role in mining machinery and equipment with their unique structure and performance.
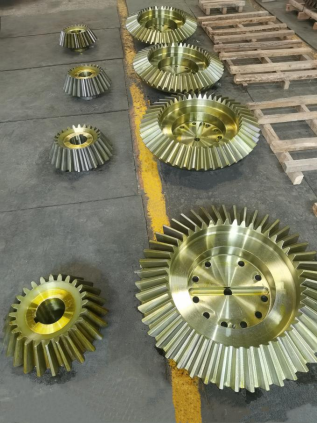
一.Characteristics of bevel gears and their advantages in mining machinery
1. Efficient power transmission
Bevel gears can achieve large-angle power conversion in a small space, which is particularly important for mining machinery. For example, in equipment such as crushers and mills, bevel gears can convert the horizontal power output of motors or reducers into vertical power to meet the operation requirements of the equipment.
Mining machinery usually needs to handle a large amount of materials, so the efficiency of the transmission system is exceptionally high. Bevel gears can significantly improve the overall performance of the equipment with their compact design and efficient transmission capacity. Compared with other types of gears, bevel gears require a smaller volume and lighter weight when transmitting the same power, which makes it an ideal choice for mining machinery.
2. High precision and stability
The design of bevel gears requires extremely high manufacturing precision to ensure good contact between the tooth surfaces and reduce vibration and noise. In mining machinery, this high precision and stability are essential to improve production efficiency and reduce maintenance costs.
Mining machinery often operates under extreme conditions, such as high temperature, high pressure and high load. The precision manufacturing process of bevel gears ensures its reliability and stability under these conditions. For example, by optimizing the tooth design and surface treatment technology, bevel gears can effectively reduce the impact and wear during the meshing process, thereby extending the service life.
3. Wear resistance and impact resistance
Mining machinery usually operates in harsh environments and is subjected to large loads and impact forces. Bevel gears are made of high-quality alloy steel materials and are heat-treated. They have excellent wear resistance and impact resistance and can adapt to high-intensity working conditions.
For example, in the crushing operations of some open-pit coal mines, bevel gears need to withstand substantial impact forces and repeated vibrations. To this end, manufacturers usually choose high-performance alloy steel materials and further enhance their hardness and toughness through carburizing quenching or nitriding. These measures ensure that the bevel gears can maintain stable performance in long-term use.
4. Compact design
Compared to other types of gears, bevel gears have a more compact structure and can complete complex power transmission tasks in a limited space. This feature makes them very suitable for use in mining machinery in scenarios where there are strict restrictions on volume and weight.
For example, in some miniaturized mining equipment, the design of bevel gears needs to take into account both compactness and functionality. By optimizing tooth profile parameters and using lightweight materials, manufacturers have successfully achieved miniaturization of bevel gears while retaining their excellent performance.
5. Versatility
Bevel gears are not only suitable for single vertical power transmission but can also be used in combination with other types of gears to form complex transmission systems. For example, in the differential of mining transport vehicles, bevel gears often work with different gears to achieve power distribution and steering functions.
The complexity of mining machinery determines that its transmission system needs to be highly flexible and scalable. The versatility of bevel gears just meets this demand, making it a core component of the transmission system of mining machinery.
二. Typical applications of bevel gears in mining machinery
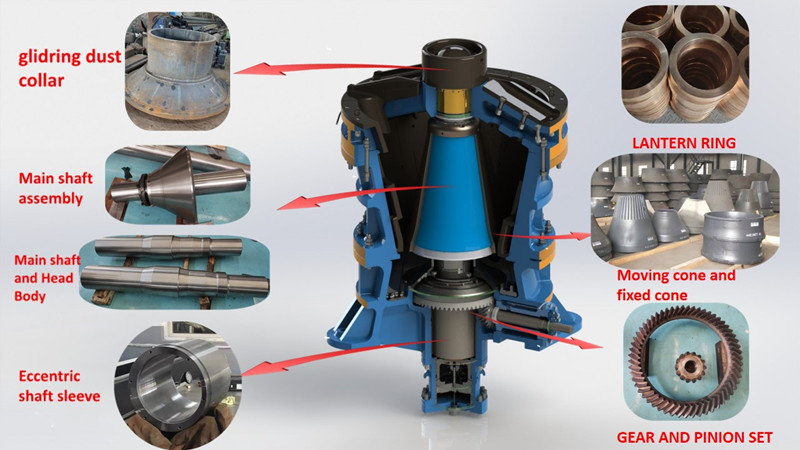
1. Crusher
A crusher is one of the most common equipment in mining machinery, used to crush large pieces of ore into smaller particles. In the transmission system of the crusher, bevel gears are usually used to connect the main motor and the rotor in the crushing chamber. Since bevel gears can withstand high torque and impact loads, they are very suitable for this working condition.
Specific case: In the crushing operation of a large open-pit coal mine, a jaw crusher uses a bevel gear transmission system. The system converts the horizontal power of the motor into vertical torque through bevel gears, driving the movable jaw in the crushing chamber to reciprocate. The high load capacity and stability of the bevel gear ensure that the crusher maintains efficient operation during long-term operation.
2. Mill
The mill is a key equipment for further grinding the crushed ore into powder. In the transmission system of the mill, bevel gears are often used to connect the reducer and the cylinder drive device. Since the grinding process requires long-term continuous operation, the high reliability and long-life characteristics of the bevel gear are critical.
Specific case: In the ball mill of a gold ore beneficiation plant, bevel gears are used as the main transmission components. The bevel gear transmits the power output of the motor to the cylinder so that the ore is repeatedly impacted and ground in the cylinder. After long-term operation verification, the bevel gear has shown extremely high durability and a low failure rate, which significantly improves the grinding efficiency.
3. Conveying equipment
Mining conveying equipment (such as belt conveyors, scraper conveyors, etc.) needs to transfer power from the drive device to the roller or chain. In this case, the bevel gear can realize the power conversion in the horizontal and vertical directions to ensure the stable operation of the conveying system.
Specific case: In the belt conveyor system of an iron mine, the bevel gear is installed in the drive station to transfer the power of the motor to the roller. Even under full load, the bevel gear can still maintain stable operation, effectively avoiding downtime accidents caused by overload.
4. Drilling equipment
Drilling equipment is used for the exploration and development of underground mines. Among these equipment, bevel gears are often used to connect the rotating drill bit and the drive motor to ensure that the drill bit can work generally at different angles.
Specific case: In a deep hole drilling project of a copper mine, bevel gears are used as transmission components of the drill rod drive system. Due to the considerable drilling depth and complex geological conditions, bevel gears must withstand extremely high torque and impact forces. After optimized design, bevel gears successfully met the project requirements and greatly improved drilling efficiency.
5. Loaders and excavators
Loaders and excavators are heavy equipment commonly used in mine construction. Bevel gears are widely used in their slewing mechanisms and walking mechanisms to achieve precise power transmission and flexible motion control.
Specific case: At an open-pit mining site in a coal mine, a large excavator is equipped with a high-performance bevel gear transmission system. The system is responsible for transmitting the power of the engine to the slewing platform and crawler drive. The high precision and reliability of the bevel gear ensure the efficient operation of the excavator in complex terrain.
三. Selection and matching of bevel gears
When selecting suitable bevel gears in mining machinery, the following factors need to be considered comprehensively:
1. Load capacity
According to the actual working conditions of the equipment, calculate the required torque and power and select a bevel gear model that can meet the load requirements. For example, for heavy-duty crushers, large-modulus, high-strength bevel gears should be chosen; for light-duty conveying equipment, smaller bevel gears can be selected to reduce costs.
2. Installation space
The size of the bevel gear must match the installation space of the equipment. If space is limited, bevel gears with miniaturized design should be preferred. For example, in some compact grinding mills, the diameter of the bevel gear can be reduced by optimizing the tooth shape design, thereby saving installation space.
3. Materials and heat treatment
The materials and heat treatment processes of bevel gears directly affect their performance. In mining machinery, high-strength alloy steel is usually selected and carburized, quenched or nitrided to enhance its wear resistance and fatigue resistance. In addition, for specific working conditions (such as high-temperature environments), heat-resistant steel or stainless steel materials can also be used to manufacture bevel gears.
4. Lubrication method
Good lubrication is the key to ensuring the regular operation of bevel gears. In mining machinery, an oil bath lubrication or forced lubrication system is usually used to ensure that the gears are always in the best working condition. For example, in some high-speed and high-load applications, independent lubricating oil pumps and filters can be equipped to improve the lubrication effect further.
5. Noise and vibration control
In order to reduce the noise and vibration generated by the bevel gear during operation, the following measures can be taken:
Optimize the tooth shape design, increase the tooth surface contact area, and reduce the meshing impact.
Increase the tooth surface hardness and reduce the abnormal noise caused by wear.
Adjust the assembly accuracy to ensure that the gear center distance and pressure angle meet the design requirements.
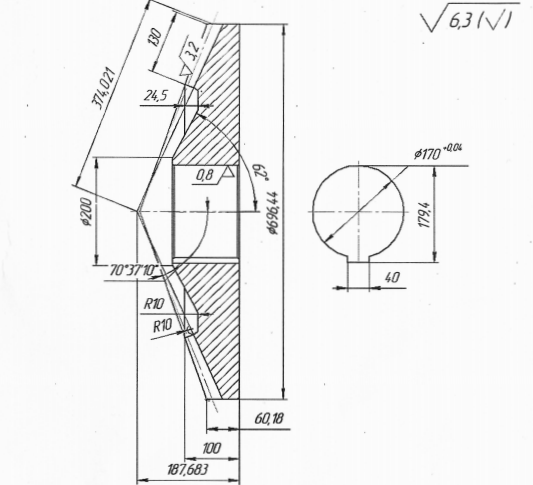
四.Maintenance and care of bevel gears
In order to extend the service life of bevel gears and ensure their regular operation, they must be maintained and serviced regularly. The following are some common maintenance points:
1.Regular inspection
Check whether there is wear, cracks or other damage on the gear surface. Once a problem is found, the damaged parts should be repaired or replaced in time.
Observe the tooth surface contact to ensure regular meshing. If the tooth surface is found to be overloaded or pitting, the assembly parameters need to be adjusted, or the gear needs to be replaced.
Check whether the radial runout and end face runout of the gear exceeds the standard. Gears that exceed the allowable range may cause abnormal vibration and noise and need to be corrected or replaced in time.
2.Lubrication management
Replace the lubricating oil regularly and keep the oil level within the specified range. It is recommended to check the oil quality once a quarter and shorten the oil change cycle according to the actual situation.
Use lubricating oil products that meet the requirements to avoid gear damage due to poor lubrication. For example, in low-temperature environments, gear oil with excellent low-temperature performance should be selected; in high-temperature environments, synthetic oil with strong antioxidant ability should be selected.
3.Temperature monitoring
Monitor the temperature changes during the operation of the bevel gear to prevent overheating. Under normal circumstances, the operating temperature of the bevel gear should not exceed 80℃.
If abnormal temperature rise is found, the cause should be found in time and corresponding measures should be taken. For example, it may be caused by insufficient lubrication, cooling system failure or excessive load.
4.Cleaning and protection
Regularly clean the dust and debris around the gear to prevent foreign matter from entering the meshing area. Especially in open-pit mining environments, sand and debris are easy to adhere to the surface of the gear, affecting its regular operation.
For bevel gears working in harsh environments, protective covers need to be installed to reduce the influence of external factors. For example, a sealing device can be set on the outside of the gearbox to prevent the intrusion of moisture and corrosive gases.
5.Spare parts reserve
According to the frequency of equipment use and operating environment, a certain number of spare bevel gears should be reasonably reserved so that damaged parts can be replaced in time.
Establish a complete spare parts management system to ensure the quality and availability of spare parts. For example, take inventory regularly and eliminate expired or unqualified spare parts.