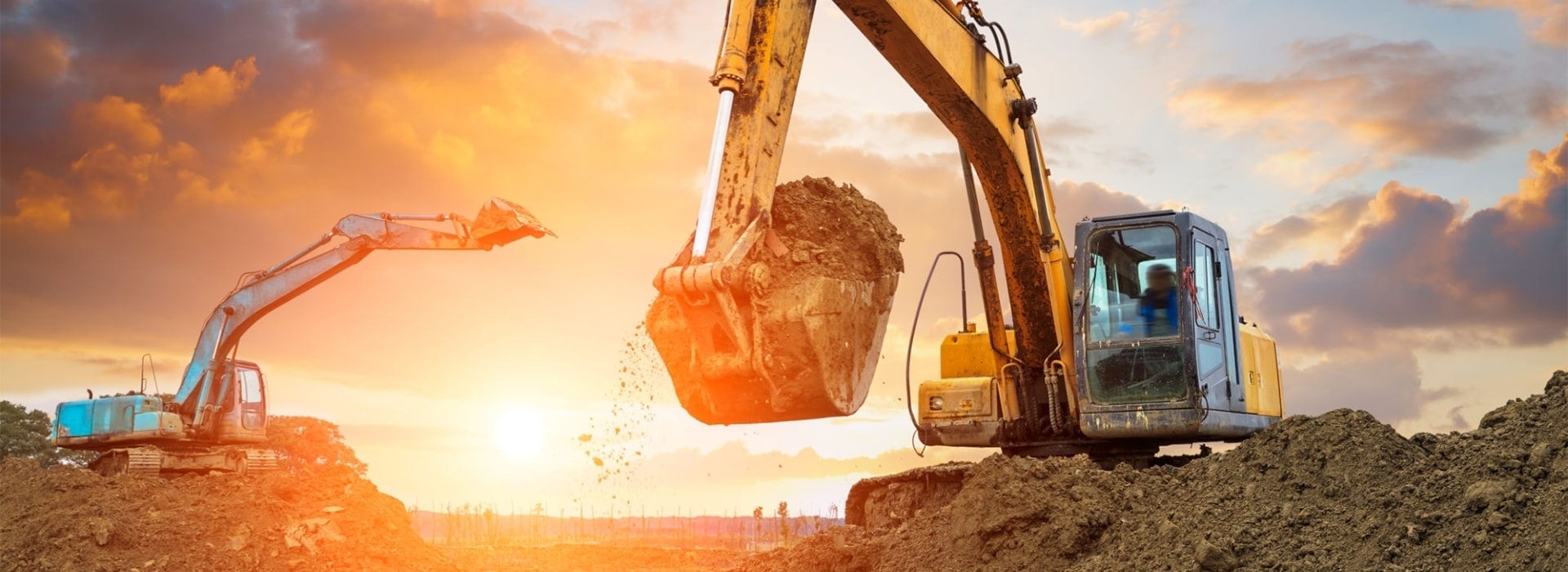
Comparative analysis of forging support roller and casting support roller
In industrial production, a rotary kiln is a key piece of equipment widely used in cement, metallurgy, chemical industry and other industries. As an essential component to support and drive the rotary kiln, the performance of the support roller directly affects the operating efficiency and stability of the whole system. According to the different manufacturing processes, the support roller can be divided into two categories: forged support roller and cast support roller.
一.Definition and basic principle
1. Forged support roller
A forged support roller is made by heating the metal billet at a high temperature and applying pressure to make it plastically deformed. This process can significantly improve the internal structure of the metal and improve the strength, toughness and wear resistance of the material. A forged support roller usually adopts a hot forging or cold forging process, combined with subsequent finishing, to complete the final forming.
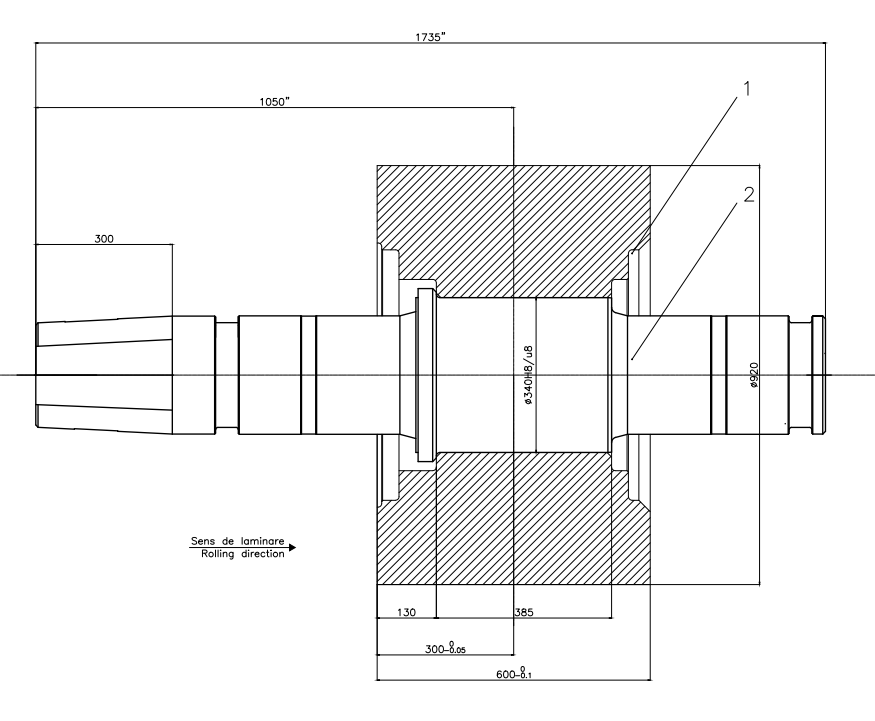
2. Cast support roller
Cast support roller are made by injecting liquid metal into the mold, cooling, and solidifying it. The casting process can realize the one-time molding of parts with complex shapes, which is suitable for mass production and the manufacture of large parts. The cast roller achieves the required dimensional accuracy and surface quality after machining.
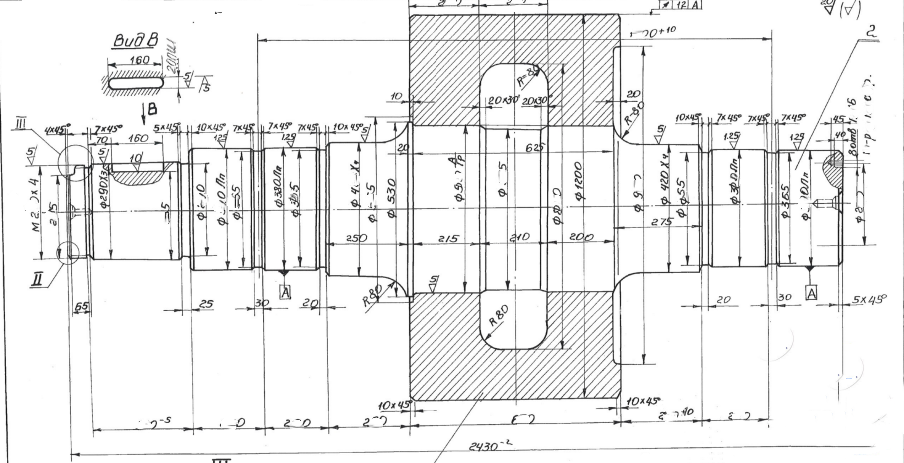
二. Comparison of material properties
1. Strength and toughness
Forged support roller: Because the metal grains are rearranged and densified during the forging process, the forged support roller has higher tensile strength, yield strength and impact toughness. These characteristics make the forged support roller more suitable for working environments with high loads, high-impact forces and frequent starts and stops.
Casting roller: Although the performance can be improved by optimizing the alloy composition, defects such as pores and shrinkage may exist inside the cast roller, resulting in its overall strength and toughness being slightly inferior to that of the forged support roller.
2. Wear resistance and fatigue life
Forged support roller: Due to its good material density and uniformity of structure, the forged support roller shows better wear and fatigue resistance, especially under long-term operation or high-stress cycle conditions.
Casting support roller: Due to the possible microscopic defects inside the cast support roller, its wear resistance and fatigue life are relatively low. However, it can still meet the requirements in some low-load or non-critical applications.
3. High-temperature resistance
Forged support roller: The forging process effectively improves the material’s high-temperature resistance so that it can maintain high mechanical properties and stability in a high-temperature environment.
Casting support roller: The high-temperature resistance of the cast support roller depends on the type of material used and its internal structure. Although modern casting technology can enhance the high-temperature resistance by adding unique alloy elements, it may still be affected by internal defects.
三. Manufacturing process comparison
1. Production process flow
Forged support roller: The forging process includes heating, forging, cooling, heat treatment and finishing steps. This process requires a significant initial investment (such as forging equipment, mold development, etc.) and high energy consumption.
Casting support roller: The casting process mainly includes smelting, pouring, cooling, cleaning and machining. Compared with forging, it requires relatively low equipment and less initial investment.
2. Material utilization rate
Forged support roller: The forging process requires a large margin for subsequent processing, so there is a lot of material waste; mainly, when producing large-sized support support roller, the material utilization rate is low.
Casting support support roller: The casting process can directly form a blank close to the final shape according to the design, reducing the amount of subsequent processing thereby improving material utilization.
3. Production efficiency
Forged support roller: The forging process is suitable for small and medium-sized batch production, especially the manufacture of standardized support support roller. However, when faced with complex geometric shapes or oversized support support roller, the forging efficiency will be limited.
Casting support support roller: The casting process is very suitable for mass production, especially for the manufacture of support support roller with complex structures or unique shapes. In addition, the development of modern precision casting technology has further improved the quality and precision of castings.
4. Design flexibility
Forged support roller: The forging process is limited in its adaptability to the shape of parts and makes it difficult to meet the needs of complex structures.
Casting support support roller: The casting process has extremely high design flexibility and can realize the manufacture of parts of almost any shape, providing more possibilities for product innovation.
四. Cost-effectiveness analysis
1. Manufacturing cost
Forged support roller: The manufacturing cost of forged support support roller is relatively high, especially for small or medium-sized support support roller, because the forging equipment investment is significant, the energy consumption is high, and complex mold development and maintenance are required.
Casting roller: The cost of cast support roller is relatively low, especially in mass production or the manufacture of complex-shaped parts. Its economic advantage is obvious.
2. Maintenance cost
Forged support roller: Due to its high strength and high wear resistance, forged support support roller experience less wear during use, low maintenance frequency, and low long-term operation costs.
Casting roller: Due to possible internal defects, the service life of cast support roller is relatively short. They need to be inspected and replaced regularly, which increases the maintenance cost.
3. Comprehensive cost performance
For high-load, high-speed or long-term operation scenarios, forged support support roller have higher comprehensive cost performance due to their excellent performance and long service life.
In low-cost and low-precision applications, cast support roller are more competitive with their lower manufacturing costs and flexible design capabilities.
五. Scope of application and typical applications
1. Application of forged support support roller
Forged support support roller are widely used as key supporting components under high load and high-temperature conditions, such as cement rotary kilns and metallurgical rotary kilns. In the cement industry, the operating stability of the rotary kiln is directly related to production efficiency and product quality, so forged support support roller are usually selected to ensure their reliability and durability.
In steel smelting, rotary kilns need to withstand extreme temperature changes and heavy loads, so forged support support roller have become the preferred solution.
2. Application of cast support roller
Cast support roller are often used in construction machinery, mining equipment, ship propulsion systems and other fields. For example, the support support roller in the excavator’s crawler drive usually adopt the casting process because they do not require high precision but have strict restrictions on size and weight.
In some low-cost and low-precision application scenarios (such as agricultural machinery), cast support roller also have a high cost-effectiveness.
六. Future development trends
1. Future trends of forged support support roller
Precision forging technology: By applying digital and intelligent technologies, precision forging will pay more attention to automated production and real-time monitoring to achieve higher production accuracy and lower scrap rates.
Research and development of new materials: The application of high-performance materials (such as high-strength steel and high-temperature resistant alloys) in forged support support roller will gradually increase to meet the needs under extreme working conditions.
Green manufacturing: Forging companies will promote the development of green manufacturing and reduce environmental impact by improving equipment, optimizing process flow and adopting clean energy.
2. Future trends of cast support roller
Precision casting technology: By introducing additive manufacturing (3D printing) technology and advanced surface treatment technology, the dimensional accuracy and surface quality of cast support roller will be significantly improved.
Environmental regulations drive technology upgrade: Foundry companies will increase investment in environmental protection technologies and develop low-emission and low-energy casting processes.
Intelligent transformation: By building smart factories, the production process can be visualized, controlled and optimized, thereby improving production efficiency and product quality.
3. Common development direction
Integration of digitalization and informatization: Whether it is forging or casting, digitalization and informatization will become the core driving force for future development. Establishing an industrial Internet platform can facilitate information sharing and collaborative innovation in upstream and downstream industrial chains.
Green and low-carbon development: Driven by the global carbon neutrality goal, the support roller manufacturing industry will pay more attention to environmental protection and sustainable development and reduce resource waste and pollutant emissions.
High-end and internationalization: As my country’s manufacturing industry moves towards high-end, both forged support support roller and cast support support roller will develop in the direction of high precision and high performance while expanding the international market and enhancing global competitiveness.
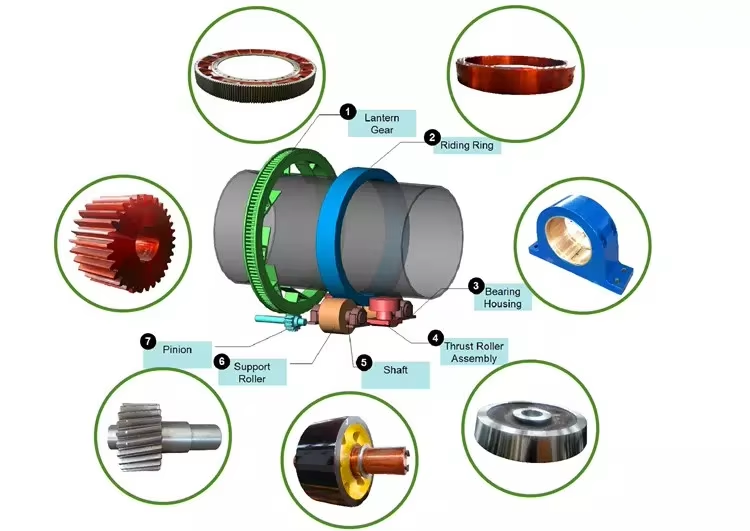
Forged support support roller and cast support roller each have unique advantages and limitations. Forged support support roller are known for their high strength, toughness and long life and are suitable for key application scenarios with high load, high speed or long-term operation. Cast support roller, with their low cost and high design flexibility, occupy an important position in mass production and complex shape parts manufacturing.
In the future, with the advancement of technology and changes in market demand, the two processes will continue to deepen innovation and development. By strengthening technological research and development, optimizing production processes and promoting intelligent transformation, forged support support roller and cast supporting support support roller will play a more significant role in their respective fields and provide more reliable solutions for industrial production.