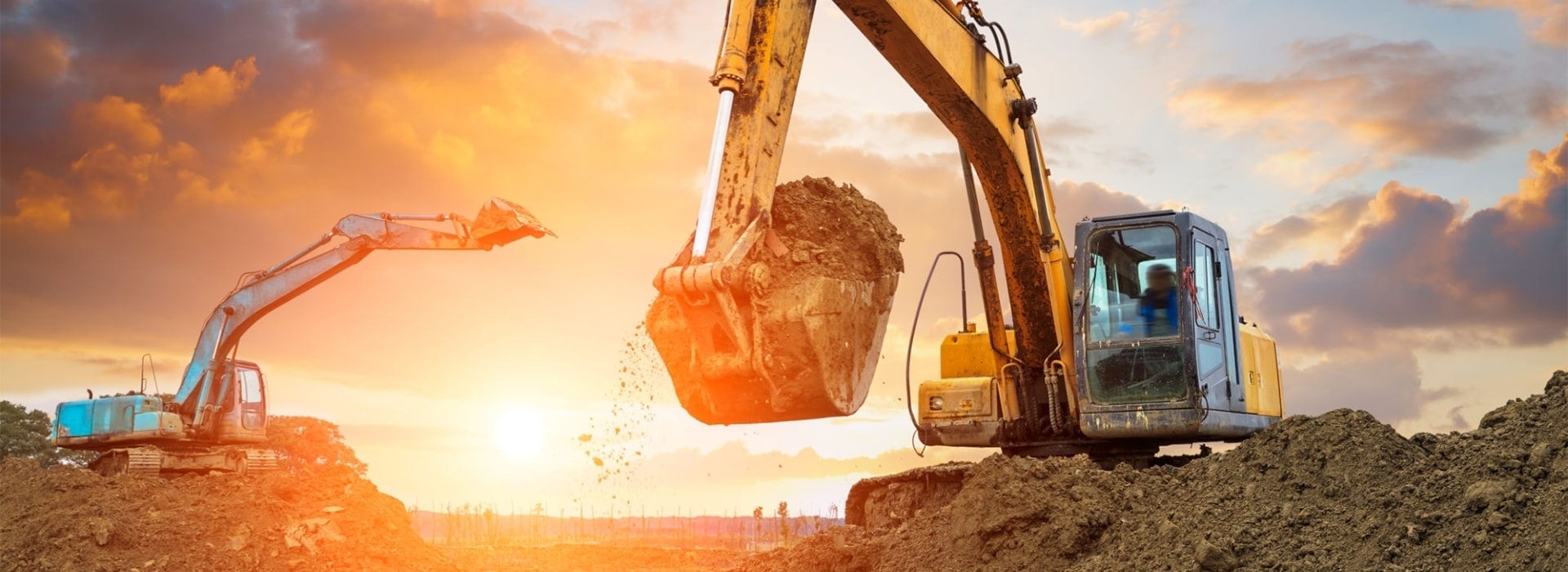
Rotary kiln:Common faults and cause analysis and maintenance strategies
The rotary kiln is one of the most essential equipment in industrial production and is widely used in cement, metallurgy, chemical industry and other fields. As the core device of a high-temperature process, the stable operation of the rotary kiln directly affects the production efficiency and product quality. Therefore, it is essential to carry out scientific and reasonable maintenance of the rotary kiln.
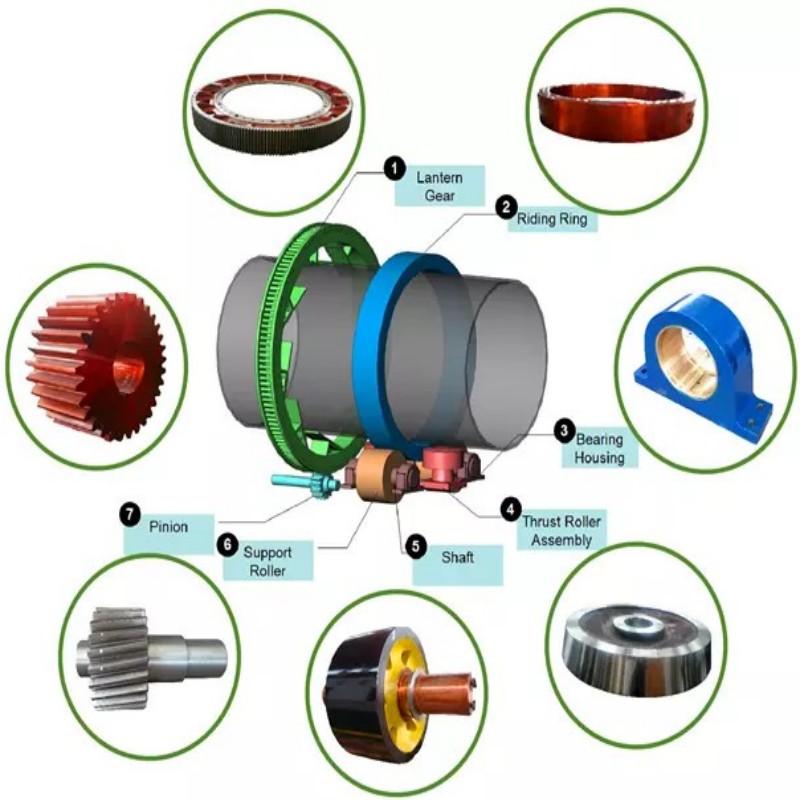
一. Working principle of rotary kiln
The rotary kiln is a continuous heat treatment equipment. Its basic structure includes a cylinder, a support device (Kiln Trunnion and a side roller), a transmission device and a combustion system. When working, the material enters from one end of the kiln, is heated by high temperature in the slowly rotating kiln body, and is discharged from the other end after completing the physical or chemical reaction. The main functions of the rotary kiln include:
Calcination: In cement production, the rotary kiln is used for calcining raw materials into clinker.
Drying: Remove moisture from the material by high temperature.
Reduction or oxidation: Rotary kilns are often used in the metallurgical industry to reduce or oxidize ores.
Incineration: In the chemical industry, rotary kilns can be used for the incineration of waste.
Because rotary kilns are in a long-term, high-temperature, high-load working environment, their key components are prone to wear, deformation or damage, so regular maintenance is required to ensure the equipment’s normal operation.
二. Common faults and causes of rotary kilns
(1)Kiln body deformation
Phenomenon: The kiln body is bent, or the ovality increases.
Cause:
Long-term high temperature leads to a decrease in material performance.
Improper adjustment of the support device (Kiln Trunnion) causes an uneven force on the kiln body.
Too much ring or material accumulation in the kiln increases the load on the kiln body.
Effect: Kiln body deformation will aggravate the wear of the Kiln Trunnion and roller and may cause the kiln body to break in severe cases.
(2)Wear of Kiln Trunnion and roller
Phenomenon: Grooves or pits appear on the surface of the Kiln Trunnion, and the contact surface of the roller is severely worn.
Cause:
Poor lubrication between the Kiln Trunnion and the roller.
The center line of the kiln body is offset, resulting in excessive local pressure.
The material hardness is insufficient, or the manufacturing precision is not high.
Impact: Excessive wear of the Kiln Trunnion and roller will increase the vibration of the kiln body and even cause shutdown accidents.
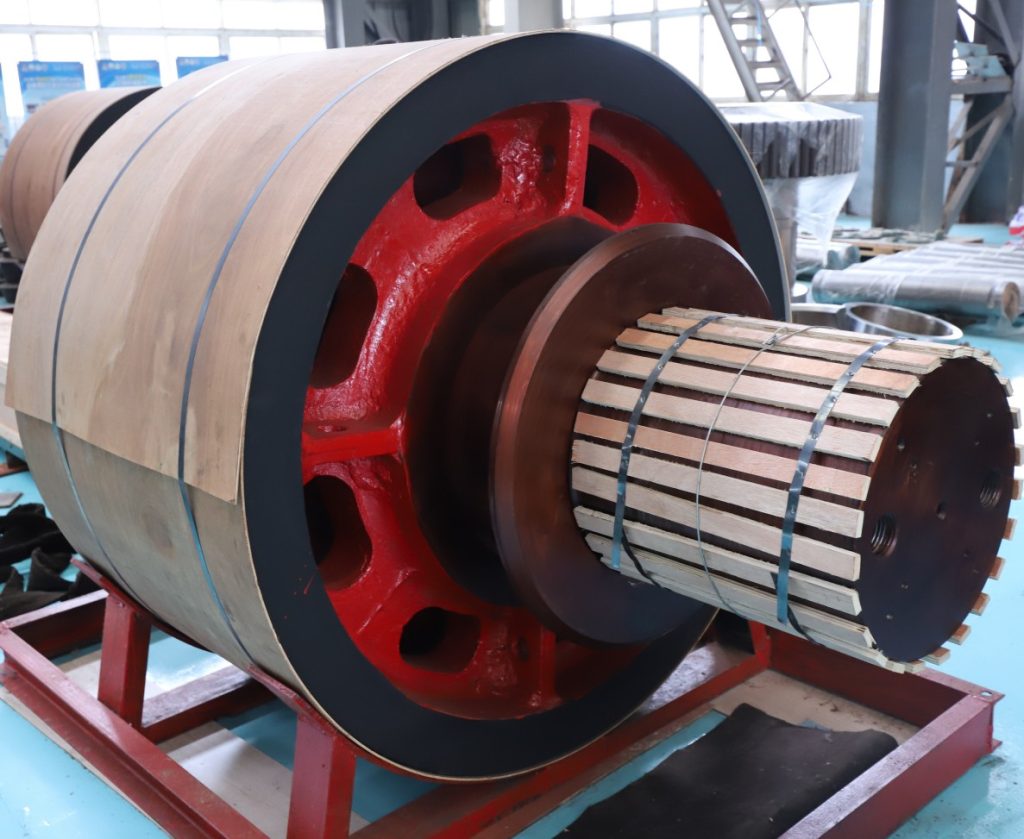
(3)Refractory material peeling
Phenomenon: Refractory bricks or castables in the kiln fall off, exposing the metal shell.
Cause:
Poor quality of refractory materials or unqualified construction technology.
Frequent temperature fluctuations lead to concentrated thermal stress.
Uneven distribution of flames in the kiln and local overheating.
Impact: Refractory material peeling accelerates the corrosion of the kiln shell and shortens the equipment’s life.
(4)Failure of sealing device
Phenomenon: Air leakage and ash leakage at the head or tail of the kiln.
Cause:
Aging or damage of sealing materials.
Improper design or improper installation of sealing devices.
Kiln body shaking or deformation leads to increased sealing gap.
Impact: Failure of sealing will not only cause energy loss, but also pollute the environment.
(5)Transmission system failure
Phenomenon: Abnormal noise of reducer, poor gear meshing or motor overload.
Cause:
Insufficient or deteriorated lubricating oil.
Gear pair wear or tooth surface fatigue.
Deviation of drive shaft concentricity.
Impact: Failure of the drive system may cause the entire production line to stop working.
三. Maintenance strategy of rotary kiln
In order to extend the service life of the rotary kiln and reduce the failure rate, a scientific and reasonable maintenance strategy must be formulated. The following are several standard maintenance methods:
1. Preventive maintenance
Check the status of key components regularly, such as the straightness of the kiln body, the wear of the Kiln Trunnion and roller, and the integrity of the refractory materials.
Perform daily monitoring of auxiliary systems such as lubricating oil and cooling water to ensure their regular operation.
Develop a detailed maintenance plan and perform various maintenance tasks on a periodic basis.
2. Predictive maintenance
Use sensors and data analysis technology to monitor the operating status of the equipment in real-time.
Detect potential problems in advance through vibration analysis, temperature detection and acoustic diagnosis.
Establish a fault prediction model based on historical data to achieve precise maintenance.
3. Corrective maintenance
Take timely measures to repair the equipment after a failure.
Replace or repair the damaged parts to restore their original performance.
Analyze the cause of the failure, improve the relevant design or operation process, and avoid similar problems from happening again.
4. Improvement Maintenance
Propose optimization plans for defects or deficiencies in existing equipment.
Introduce new technologies, new materials or new processes to improve the overall performance of the equipment.
Revise and improve the operating procedures to improve the technical level of employees.
四. Specific maintenance methods for rotary kilns
1. Kiln body maintenance
Straightness adjustment: Regularly measure the centerline position of the kiln body and adjust the position of the Kiln Trunnion if necessary to keep it running smoothly.
Refractory repair: For slightly peeled refractory materials, spraying or local repair methods can be used; when seriously damaged, the kiln needs to be stopped for comprehensive replacement.
Anti-corrosion treatment: Paint or spray a protective layer on the exposed metal shell to prevent corrosion.
2. Support device maintenance
Kiln Trunnion lubrication: Select appropriate grease, regularly add and clean old oil stains.
Roller inspection: Observe whether there are cracks or pits on the roller’s surface and repair them in time if problems are found.
thrust roller adjustment: Adjust the position and pressure of the thrust roller appropriately according to the movement of the kiln body.
3. Transmission system maintenance
Gear inspection: Regularly check the meshing state of the gears and remove impurities on the tooth surface.
Lubricant management: Replace the lubricant on time and keep the oil level within the specified range.
Motor maintenance: Check the insulation of the motor windings, bearing lubrication, etc., to ensure its regular operation.
4. Sealing device maintenance
Sealing material replacement: Regularly check the wear of the sealing device and replace aging or damaged seals as soon as possible.
Seal gap adjustment: Adjust the seal gap appropriately according to the kiln body’s actual operating status to ensure the sealing effect.
Dust prevention measures: Install dust covers or baffles at the sealing parts to reduce dust intrusion.
5. Combustion system maintenance
Nozzle cleaning: Regularly clean the burner nozzle to prevent blockage or biased burning.
Flame monitoring: Use infrared cameras or other detection equipment to monitor the flame shape and temperature distribution.
Fuel switching: Reasonably adjust the fuel type and ratio according to production needs to optimize the combustion effect.
五. Best practices for rotary kiln maintenance
1. Establish a sound management system
Develop a detailed maintenance manual to clarify the responsible persons and time nodes for each task.
Implement the “spot inspection and scheduled maintenance” system to combine daily inspection with regular maintenance.
Establish equipment files to record the content and results of each maintenance to provide a basis for subsequent analysis.
2. Strengthen personnel training
Organize technical personnel to participate in professional training to learn advanced maintenance technology and management concepts.
Regularly carry out internal exchange activities to share experiences and lessons and improve the overall level of the team.
Strengthen safety awareness education and eliminate illegal operations.
3. Introduce intelligent technology
Equipped with an online monitoring system to collect equipment operating parameters in real-time.
With the help of a big data analysis platform, hidden fault hazards are discovered.
Apply remote diagnostic tools to achieve expert remote guidance and technical support.
4. Focus on environmental protection and energy saving
Optimize the combustion process to reduce energy consumption and emissions.
Improve sealing performance and reduce heat loss caused by air leakage.
Recycle waste heat resources for preheating raw materials or other purposes.
As the core equipment of a high-temperature process, the maintenance of a rotary kiln is directly related to the economic benefits and social responsibility of the enterprise. Through in-depth analysis of common faults and causes of rotary kilns, combined with scientific and reasonable maintenance strategies and specific implementation methods, the failure rate can be effectively reduced, the equipment life can be extended, and production efficiency can be improved. In the future, with the widespread application of intelligent technology, the maintenance of rotary kilns will be more accurate and efficient, injecting new vitality into industrial production. Enterprises should keep up with the trend of technological development, continuously innovate management models, and promote the maintenance of rotary kilns to a higher level.