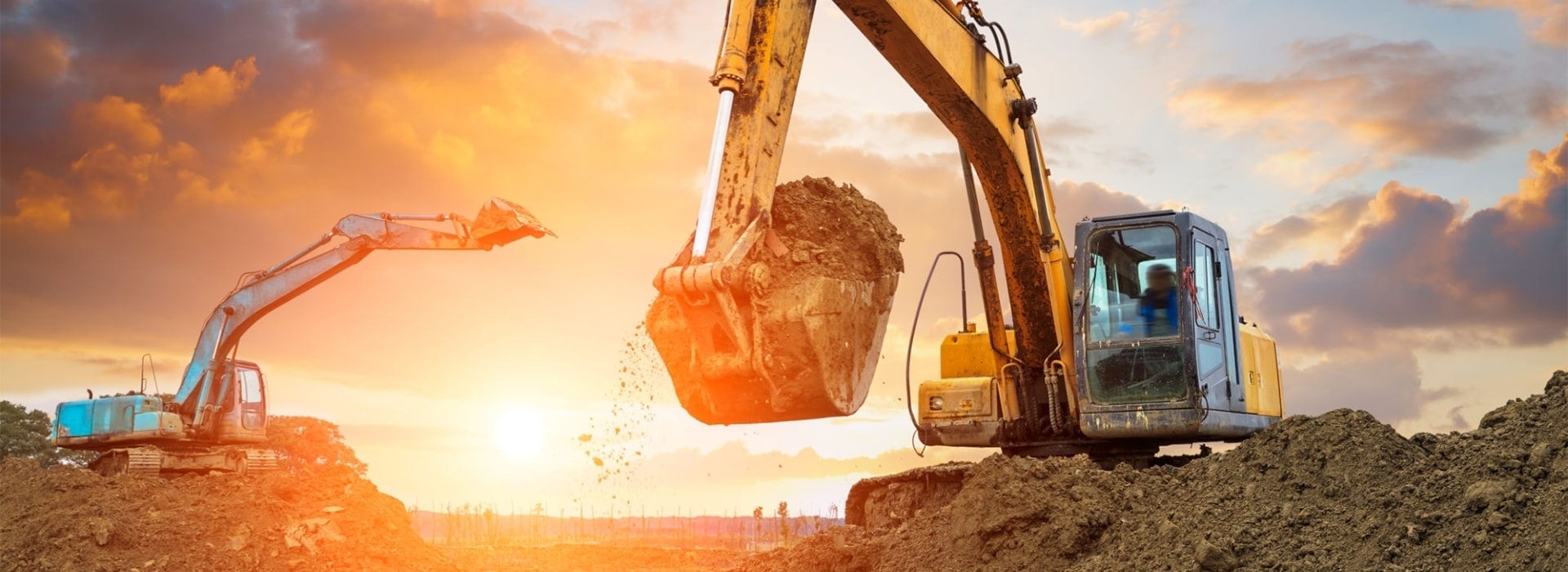
Casting + Forging construction spur gear is used for mining machinery
Forging & casting of construction spur gear has a widely use in mining equipment.
Spur gears with an alloy-plus forging construction are usually utilized in a variety of heavy equipment, including mining equipment. This manufacturing process combines the benefits of two different methods. Casting allows the creating of intricate designs and larger dimensions, and forging increases the durability and wear-resistant characteristics of the product. This makes it suitable for applications that need high load and wear, such as transmission systems in mining equipment.
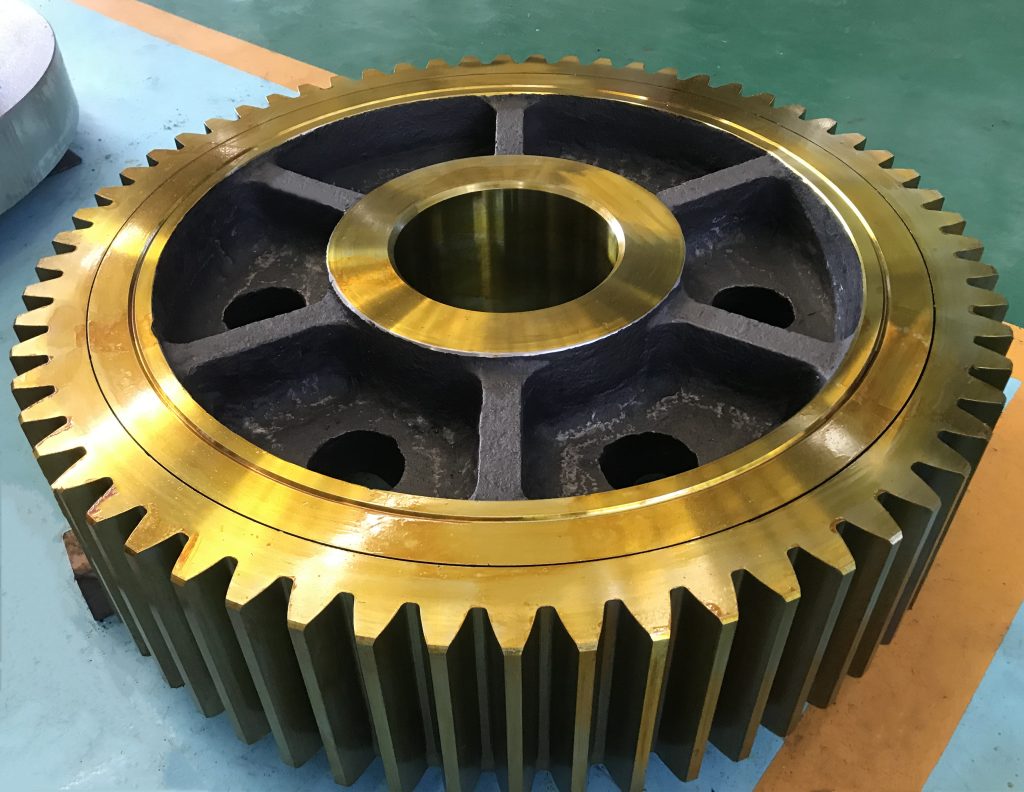
When mining, spur gears have straight teeth parallel to a circular axis. They transfer motion between parallel shafts and are commonly utilized in gearbox systems, conveyors, and other parallel shaft applications.
Utilizing the casting process in conjunction with the forging procedure, spur gears that have superior mechanical properties can be fabricated. These properties are vital for ensuring the durability and efficiency of key equipment utilized for mining. It is important to remember that the exact procedure that is to be employed should be determined based on the particular requirements of the specific application, along with costs and the technologies available.
The combination of casting and forging processes combines the advantages of two methods for production. It is suitable for manufacturing parts with complex shapes and requires high performance. These are the advantages of this method:
1. Flexible Design Casting allows the creation of complex geometric shapes and internal features that are difficult to make by forging them on their own. Casting blanks with intricate contours and specific features are possible to be produced.
2. Enhancing the strength and toughness of Materials Forging can improve the physical properties of materials, such as toughness, stability, and wear resistance, by enhancing the quality of metal grains and removing internal imperfections. This is vital in situations that require intense pressure and impact.
3. Utilize the material efficiently. When compared to forging itself, casting the first time can reduce the amount of raw materials used, as casting is able to more precisely control the shape of the final product and reduce the need to process it further.
4. The casting process can be used to manufacture components of any size, including small precision components as large as heavy-duty equipment parts. When castings are turned into forgings, properties are possible without compromising the size.
5. Improved Surface Quality: Although casting itself may produce a smooth surface, following the steps of forging will improve its quality. Surface reduces imperfections on the surface as well as speeds the finalization process.
6. Cost-effectiveness: For certain scenarios that require massive production of complex-shaped parts, casting and forging processes can perform better than any one method. They may reduce the cost of manufacturing without sacrificing quality.
7. Modifications to Special Materials Certain materials and alloys, due to their properties, are difficult to form when forging. First, by casting and after forging, these alloys can also be formed efficiently according to their intended shape and purpose.
In the final analysis, casting and forging can be highly efficient methods of production. They are specifically designed to work with parts that have intricate designs and performance requirements, like bevel gears used in mining equipment. This procedure not only assures the quality and performance of the items but also assists in reducing production costs to some degree.
If you need heavy spur gear, don’t hesitate to get in touch with luoyang wangli heavy machinery co.,ltd: lulu@citicwl.com