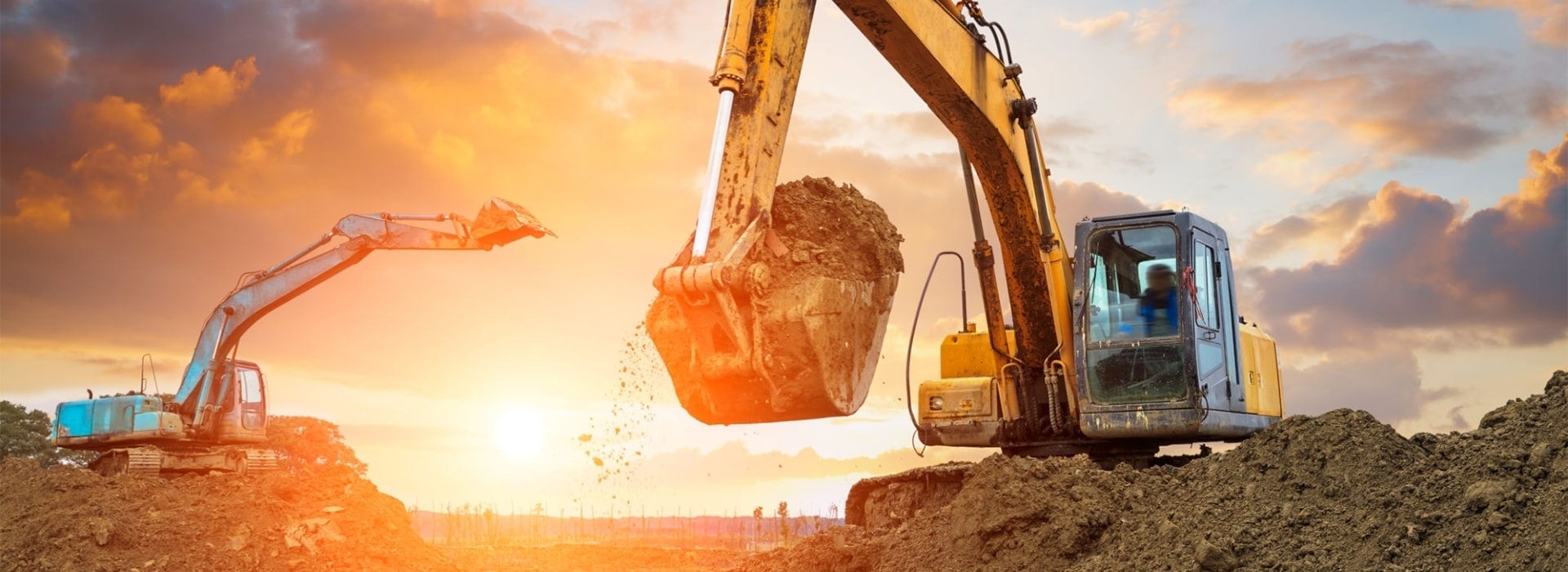
Casting is mainly divided into two categories: sand casting and special casting
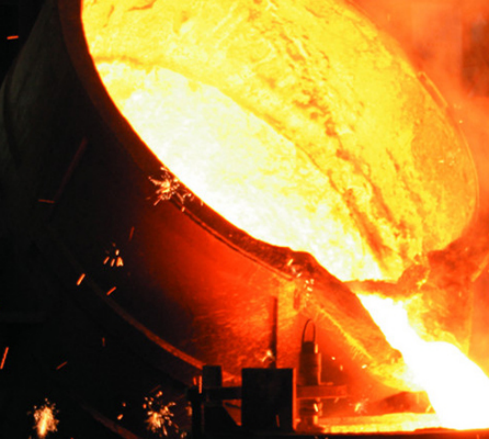
1 Ordinary sand casting, using sand as a mold material, is also called sand casting, sand casting, including wet sand mold, dry sand mold and chemical hardening sand mold, but not all sand can be used for casting. The advantage is that the cost is low because the sand used in the mold can be reused; the disadvantage is that the mold is time-consuming to make, the mold itself cannot be reused, and must be destroyed to obtain the finished product.
1.1 Sand mold (core) casting method: wet sand mold, resin self-hardening sand mold, water glass sand mold, dry mold and surface dry mold, solid mold casting, negative pressure molding.
1.2 Sand core manufacturing method: It is selected according to the size, shape, production batch and specific production conditions of the sand core. In production, it can be generally divided into manual core making and machine core making.
2 Special casting, according to the molding materials, can be divided into two categories: special casting with natural mineral sand and stone as the main molding materials (such as investment casting, clay casting, shell casting, negative pressure casting, solid casting, ceramic casting, etc.) and special casting with metal as the main casting material (such as metal mold casting, pressure casting, continuous casting, low pressure casting, centrifugal casting, etc.).
2.1 Metal mold casting method
The mold is made of metal with a higher melting point than the raw material. It is subdivided into gravity casting, low pressure casting and high pressure casting.
Due to the melting point of the mold, the metal that can be cast is also limited.
2.2 Lost wax casting method
This method can be outer film casting and solid casting.
First, the object to be cast is replicated in wax, then immersed in a pool containing ceramic (or silica sol) and left to dry, so that the wax replica is covered with a layer of ceramic outer film. The steps are repeated until the outer film is sufficient to support the casting process (about 1/4 inch to 1/8 inch), then the wax in the mold is melted and the mold is removed. The mold needs to be heated several times to increase its hardness before it can be used for casting.
This method has good accuracy and can be used for casting high-melting-point metals (such as titanium). However, due to the high price of ceramics and the need for multiple heating and complex production, the cost is quite expensive.
[2]Molding process
1.Gravity casting: sand casting, hard mold casting. Relying on the metal’s own gravity to pour the molten metal into the mold cavity.
2.Pressure casting: low-pressure casting, high-pressure casting. Relying on additional pressure to instantly press the molten metal into the casting cavity.
The casting process usually includes
① Preparation of casting mold (container for making liquid metal into solid casting). Casting mold can be divided into sand mold, metal mold, ceramic mold, mud mold, graphite mold, etc. according to the materials used. It can be divided into disposable mold, semi-permanent mold and permanent mold according to the number of times used. The quality of casting mold preparation is the main factor affecting the quality of castings;
② Melting and pouring of casting metal. Casting metal (casting alloy) mainly includes various types of cast iron, cast steel and cast non-ferrous metals and alloys;
③ Casting treatment and inspection. Casting treatment includes removing foreign matter from the core and casting surface, cutting off the pouring riser, grinding burrs and seams and other protrusions, as well as heat treatment, shaping, rust prevention and rough processing.
The casting process can be divided into three basic parts, namely casting metal preparation, casting mold preparation and casting treatment. Casting metal refers to the metal material used for casting castings in casting production. It is an alloy composed of a metal element as the main component and other metals or non-metallic elements. It is usually called casting alloy, mainly cast iron, cast steel and casting non-ferrous alloys.
Metal smelting is not just simple melting, but also includes the smelting process, so that the metal poured into the mold meets the expected requirements in terms of temperature, chemical composition and purity. To this end, various inspections and tests for the purpose of quality control must be carried out during the smelting process, and the liquid metal can only be poured after reaching various specified indicators. Sometimes, in order to meet higher requirements, the molten metal must be treated outside the furnace after leaving the furnace, such as desulfurization, vacuum degassing, refining outside the furnace, inoculation or metamorphic treatment, etc. Commonly used equipment for smelting metals include cupolas, electric arc furnaces, induction furnaces, resistance furnaces, reverberatory furnaces, etc.
Advantages:
1. It can produce parts with complex shapes, especially blanks with complex inner cavities;
2.It has wide adaptability. All metal materials commonly used in industry can be cast, ranging from a few grams to hundreds of tons;
3.The raw materials are widely available and inexpensive, such as scrap steel, scrap parts, and chips;
4.The shape and size of the castings are very close to the parts, which reduces the amount of cutting and belongs to non-cutting processing;
5.It is widely used. 40%~70% of agricultural machinery and 70%~80% of the weight of machine tools are castings.
Disadvantages:
1. The mechanical properties are not as good as forgings, such as coarse organization and many defects;
2.In sand casting, single-piece and small-batch production has high labor intensity for workers;
3.The quality of castings is unstable, there are many processes, and the influencing factors are complex, which is easy to produce many defects.
Casting defects have an important impact on the quality of castings. Therefore, in order to lay a good foundation for the selection of casting alloys and casting methods, we should start with the quality of castings and combine the formation and prevention of the main defects of castings.
Casting product
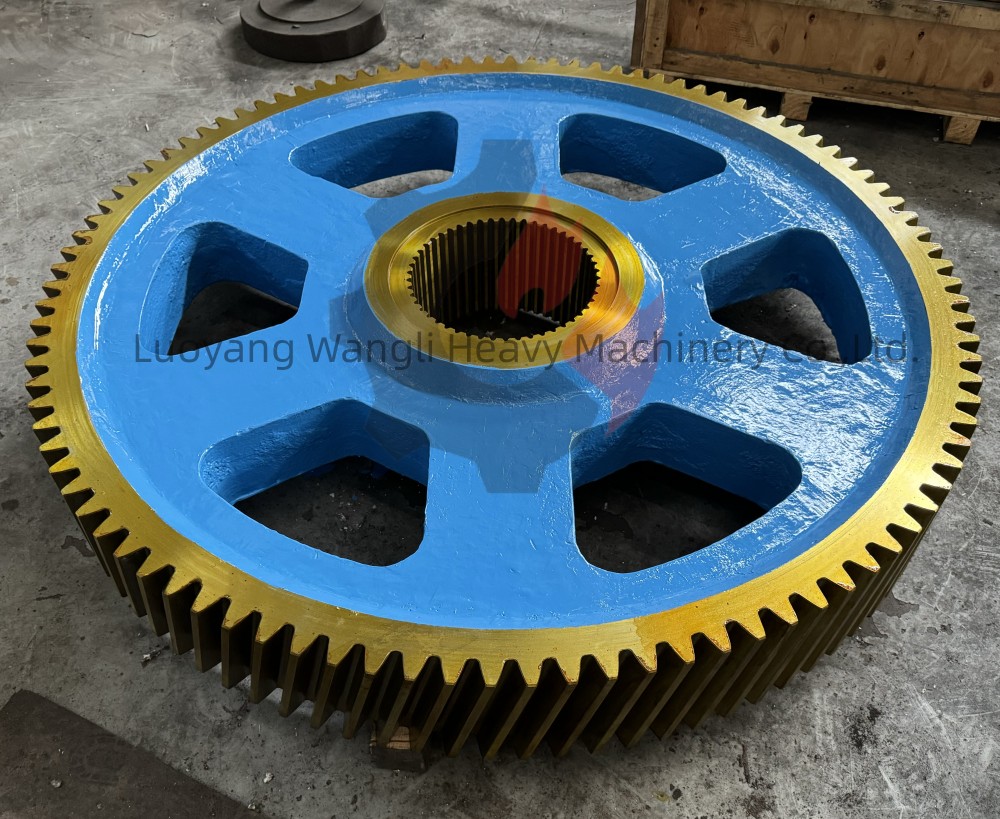
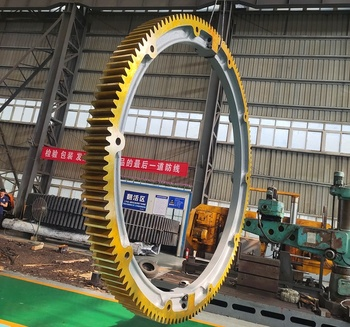