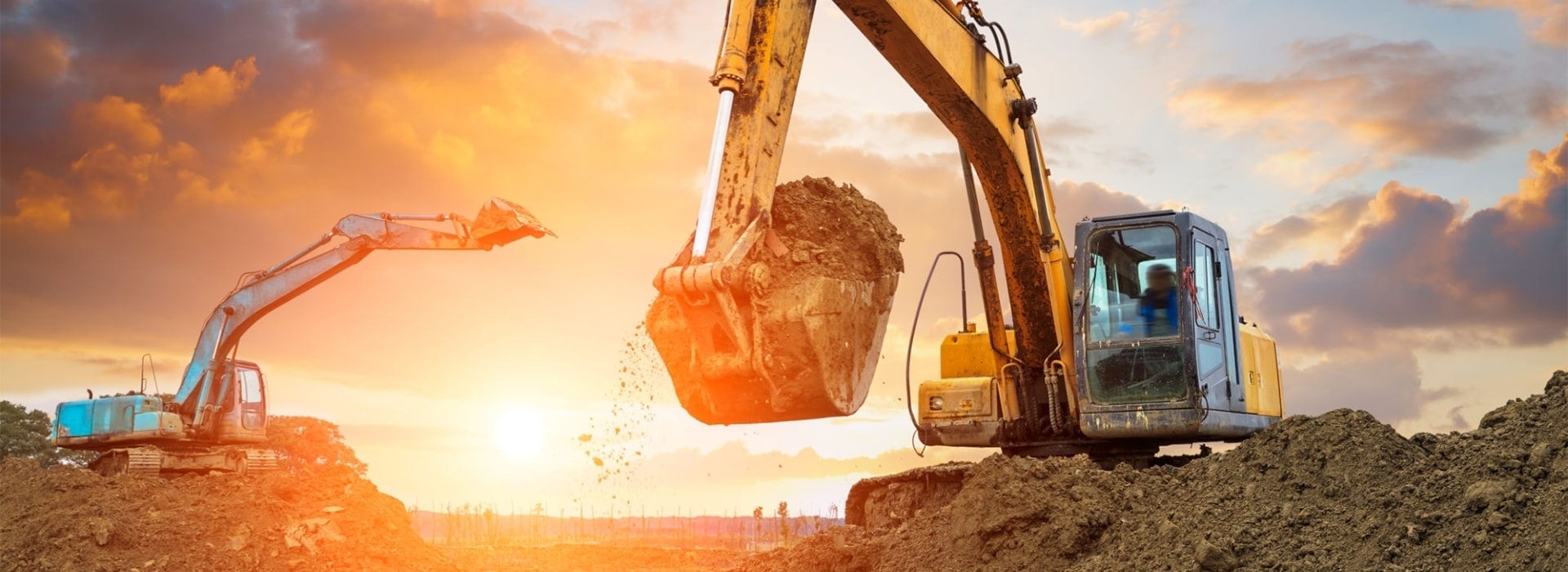
Key Points in Bearing Steel GCr15SiMn Forging
Forging is a crucial step in the production process of bearing steel, aimed at improving the material’s microstructure and mechanical properties through plastic deformation. Here are some key points regarding bearing steel GCr15SiMn forging:
1. Cooling requirements of GCr15SiMn steel during the forging:
Quick cooling at 700-850℃ (blast, spray water cooling, etc.).
Below 700℃, the transformation of austenite to pearlite begins, and the first eutectoid carbide precipitates along the grain boundary. Therefore, to prevent the formation of white spots and reduce the internal stress in the steel, it should be cooled slowly below 700℃. In production, the forgings can be placed in the sandbox for cooling, and the thickness of dry sand accumulated around the forgings is not less than 100mm and then covered with an insulation cover. The cooling time is 48-72 hours.
2. Macroscopic test of GCr15SiMn bearing steel:
YB9-68 stipulates that two samples are taken from each furnace of steel to check the macroscopic structure. There must be no shrinkage cavities, subcutaneous air pockets, white spots and overburning, and the central looseness must not exceed 1.5 levels (according to YB9-68 Figure 1, there are five levels in total). Generally, the porosity of steel with a diameter less than 100 should not exceed 1.0 level, and that of steel with a diameter greater than 100 should not exceed 2.0 level (5 levels according to Figure 2 of YB9-68). The deflection should not exceed two levels (2 levels according to Figure 3 of YB9-68).
3. Common quality problems of GCr15SiMn bearing steel forging: fibrous structure, network carbide, overheating, overburning, decarburization and white spots, mainly white spots and network carbides.
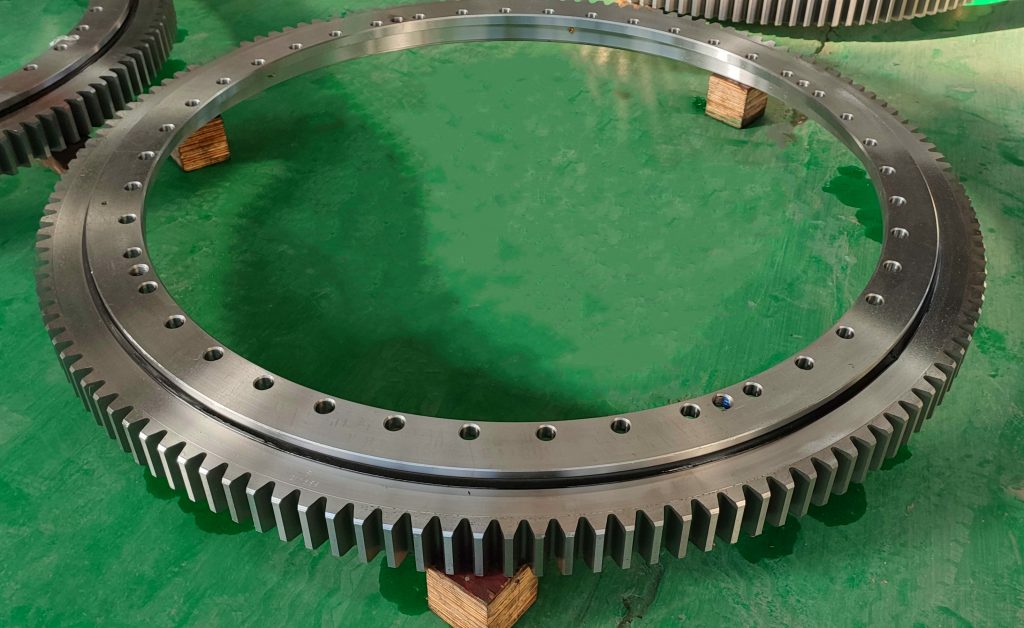
Slewing Bearing
GCr15SiMn steel is susceptible to white spots and is most likely to form white spots below 250°C. The presence of white spots has a highly adverse effect on the performance of steel. It reduces the mechanical properties of steel, causes cracking of parts during quenching during heat treatment, and causes breakage of parts during use. Therefore, it is absolutely not allowed. For forging bearing steel GCr15SiMn , the key to avoiding the generation of white spots is to formulate reasonable post-forging cooling and heat treatment specifications.
Network carbides are formed during the cooling process after forging, and subsequent annealing and tempering cannot eliminate them. The network carbides retained in the quenching and tempering structure of bearing parts sharply reduce their strength and toughness.
The influence of network carbide level on impact toughness:
Network level | Ɑk(Kgf.m/cm2) | |||||
1 | 2 | 3 | 4 | 5 | Average | |
<2 Class | 10.30 | 10.50 | 10.10 | 11.70 | 8.12 | 10.24 |
2~4 Class | 6.25 | 5.90 | 5.20 | 6.60 | – | 5.99 |
Network carbides are caused by slow cooling during forging bearing steel GCr15SiMn. To avoid that condition, they should be cooled quickly after forging, significantly shortening the residence time between Acm-A1. This is the temperature at which a large amount of secondary carbides precipitate along the A grain boundary. When the cooling rate is more significant than 100℃/s, the forging has only slight or no network carbides because the fast cooling rate can inhibit the precipitation of network carbides. Therefore, air cooling or spray cooling is generally used.
The stop-forging temperature also has a particular influence on the network carbide. Under the same cooling conditions, the stop-forging temperature is different, and the size, sealing degree and thickness of the produced carbides are different. When the stop-forging temperature is too high, the size of the network is significant due to the coarse grains. If the stop forging temperature is higher than the temperature at which the carbides are dissolved but not precipitated when the cooling speed is slow, the carbides have sufficient precipitation time before A1, so it is easier to form a wholly sealed network. However, if the stop forging temperature is too low, it is easy to cause fracture and carbide banding. Therefore, the final temperature of GCr15SiMn bearing steel forging should be controlled at 800-850℃.
If the carbide network structure level of the steel is unqualified, normalizing can be used to eliminate the network carbides before annealing. Using normalizing to prevent the improvement of network carbides will bring new problems. Since carbides are not completely dissolved during normalizing, aggregation of undissolved carbides will occur to a certain extent. These carbides will grow further during the annealing process, which will become coarse carbides in the spheroidized annealing structure, resulting in uneven carbide particle size in the original structure, reducing the quality of the spheroidized structure, and having an adverse effect on the material structure and fatigue life. Therefore, it is essential to avoid the appearance of network structure after forging. The heating curve of bearing steel GCr15SiMn forging is as the follows:
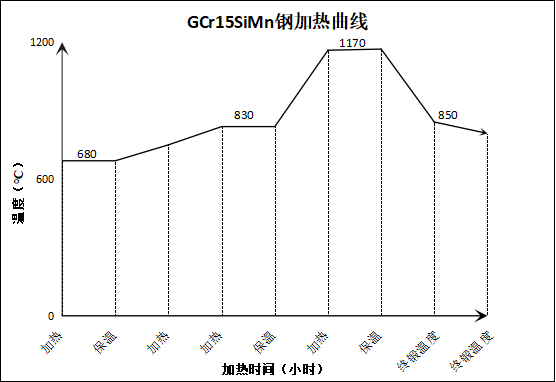
If you need bearing, don’t hesitate to get in touch with luoyang wangli heavy machinery Co.,ltd: lulu@citicwl.com