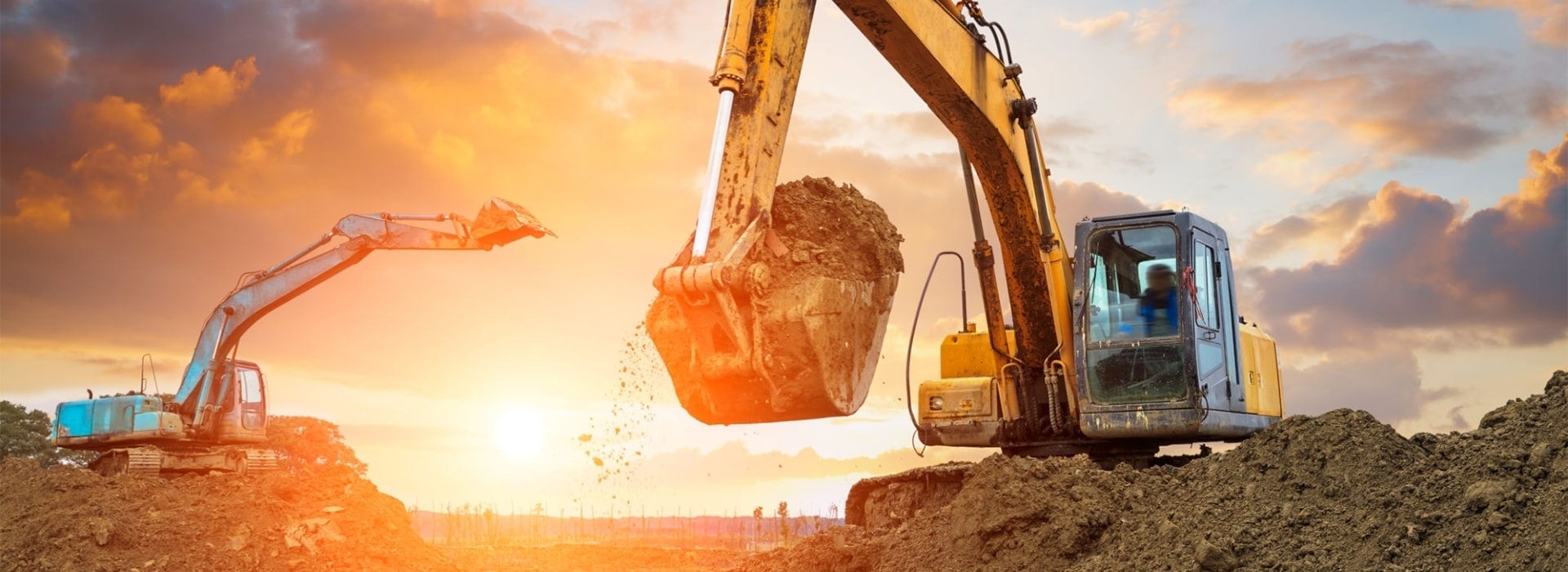
Non-standard alloy steel large diameter Casting wheel
PRODUCT PARAMETERS
Description
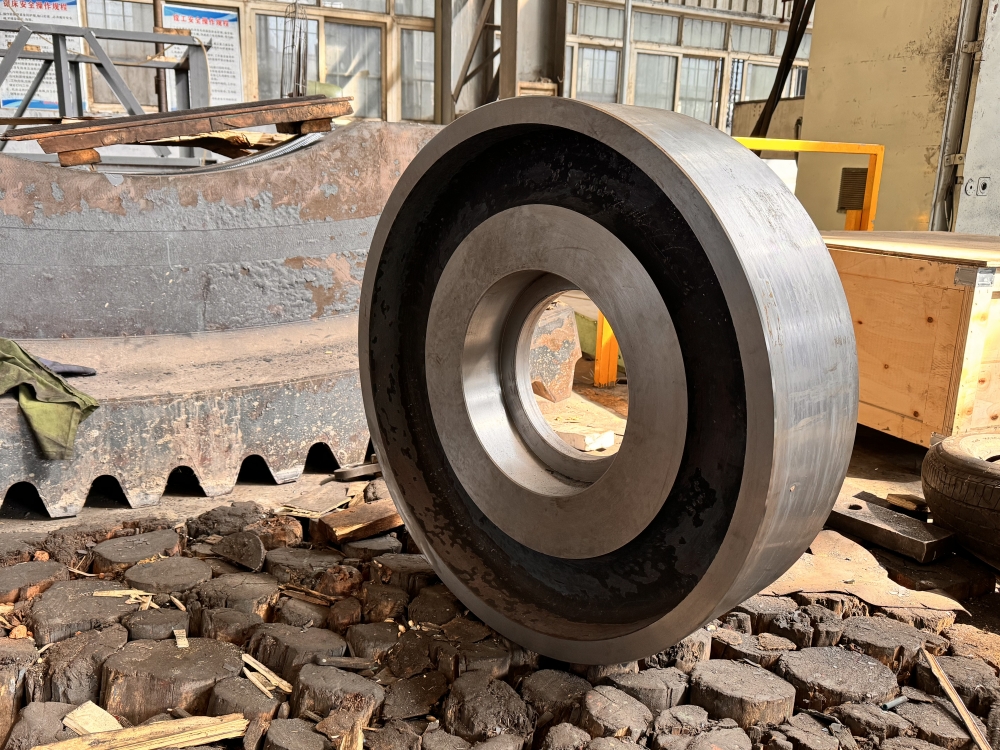
Overview of Casting wheel
Cast wheel play a vital role in the mechanical transmission system, whose main function is to transmit power and motion through the meshing of teeth. Compared with other manufacturing processes, casting is particularly suitable for the production of complex shapes and large sizes of gears, with the advantages of cost-effective and fast production efficiency. The cast gear can withstand high loads and stresses, ensuring the stability and reliability of the mechanical system.
Q | A | Q | A |
Product name | Casting wheel | Delivery time | 45-60Days |
Material | Cast iron 230-450 | Defect Control | UT, MT |
Process | Casting +CNC machining+HT | Color | Custom |
outer diameter | According to the drawings | weight (kg) | 600 |
Heat Treatment | Quenching & Tempering | Certificate | ISO9001 |
Production process of Casting wheel
Casting
Casting blank production is the basis of the whole process, first prepare the mold according to the design drawing. Commonly used casting methods include sand casting, precision casting and so on. At this stage, a suitable material (such as cast iron or cast steel) needs to be selected, the molten metal is poured into the mold, and the basic shape of the gear is formed after cooling. This step requires strict control of the pouring temperature and speed to ensure the quality of the casting.
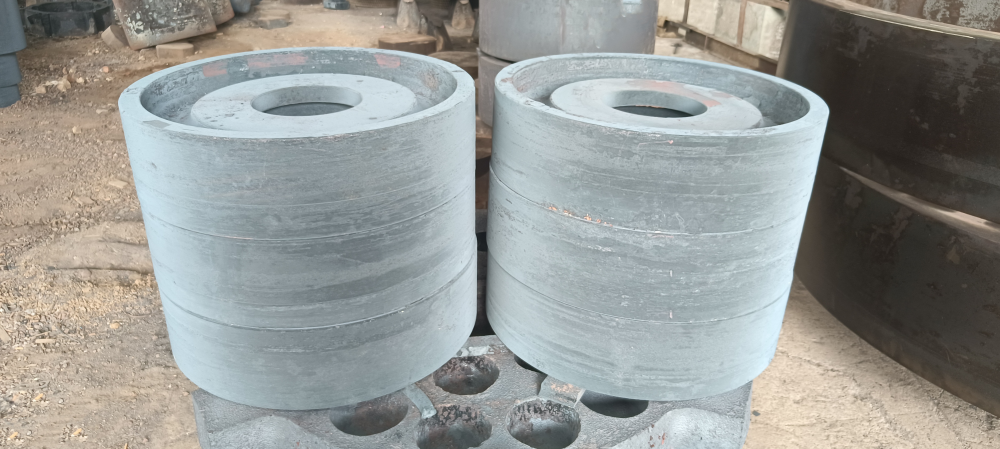
Rough Machining
After the blank is obtained, it is roughed to remove excess material and initially form the gear profile. Usually use lathes, milling machines and other equipment to process the outer circle, inner hole and end face. The main purpose of roughing is to provide accurate positioning benchmarks for subsequent processes and reduce the workload of finishing.
Heat treatment
In order to enhance the hardness and wear resistance of the gear, it must be heat treated. Common heat treatment methods are quenching, tempering and so on. By heating to a specific temperature and then rapid cooling (quenching), followed by holding at the appropriate temperature (tempering), the mechanical properties of the gear can be significantly improved, making it more resistant to wear and fatigue damage.
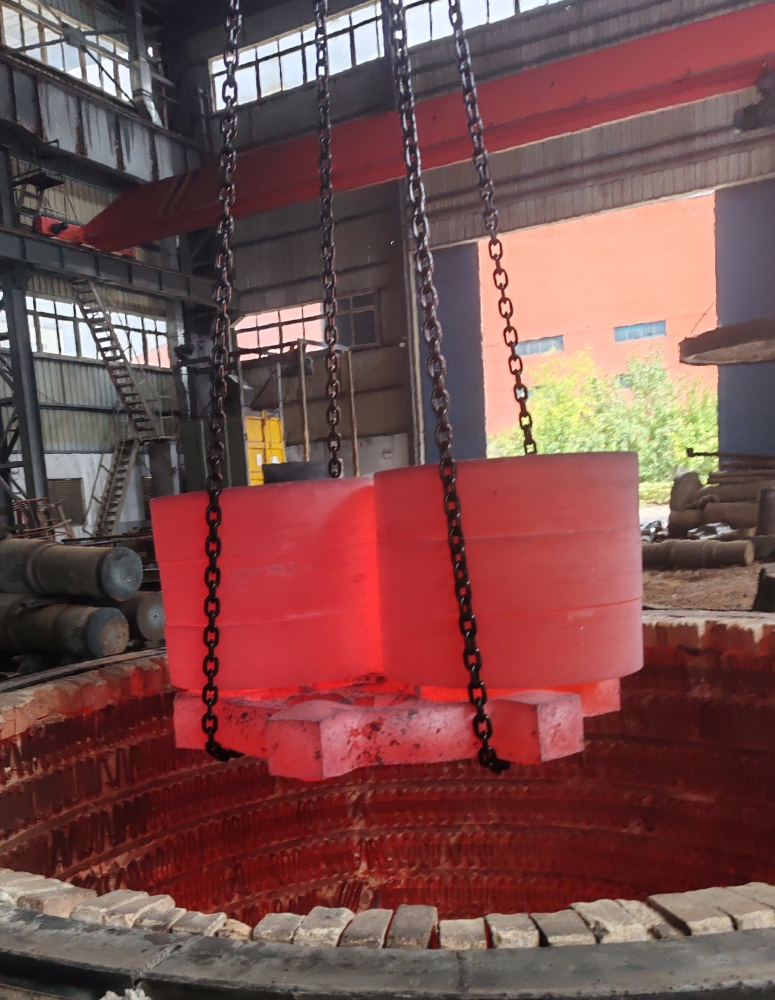
Finishing Machining
Finishing is a key step to achieve the final size and shape of the gear, including hobbing, gear shaping and other processes to accurately machining the gear tooth shape. In this process, the machining accuracy should be strictly controlled to ensure that the tooth shape meets the design requirements. In addition, the gear needs to be measured and inspected to verify that its dimensional accuracy and surface quality are up to standard
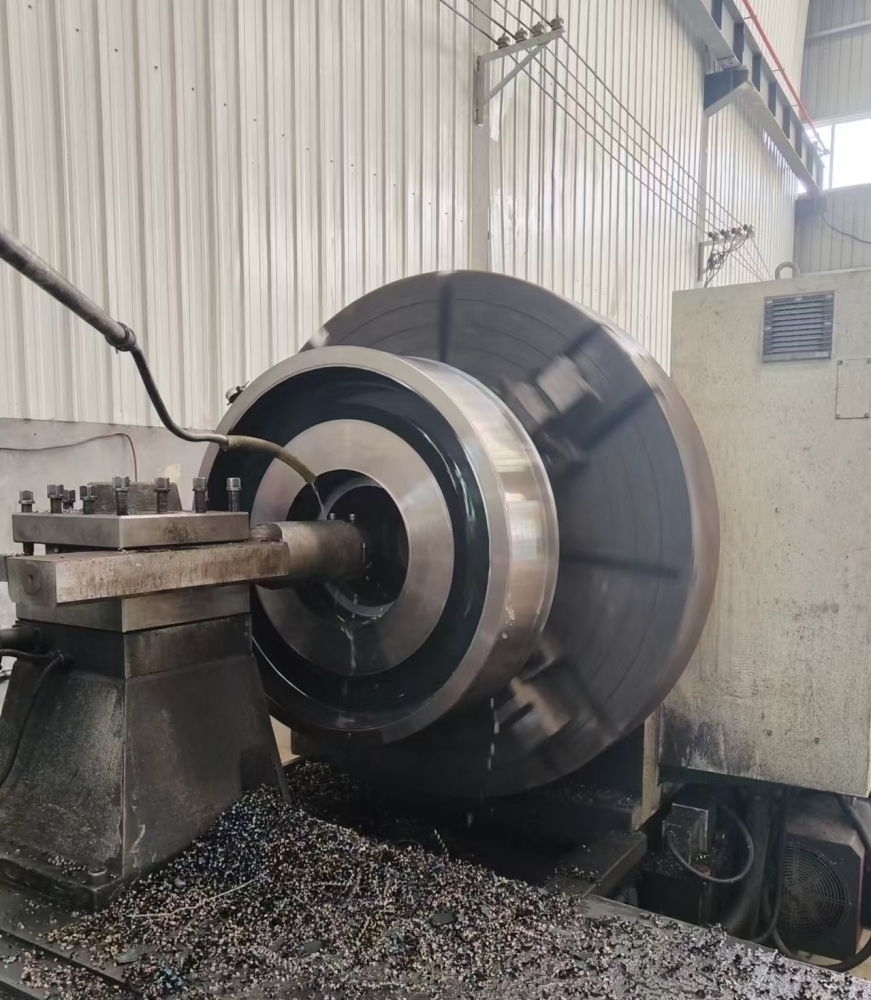
Package of Casting wheel
Cleaning treatment to remove surface impurities, anti-rust treatment to prevent oxidation, the selection of appropriate packaging materials such as wooden boxes or cartons, and add anti-shock cushion protection, and finally identify product information and handling precautions to ensure transportation safety.
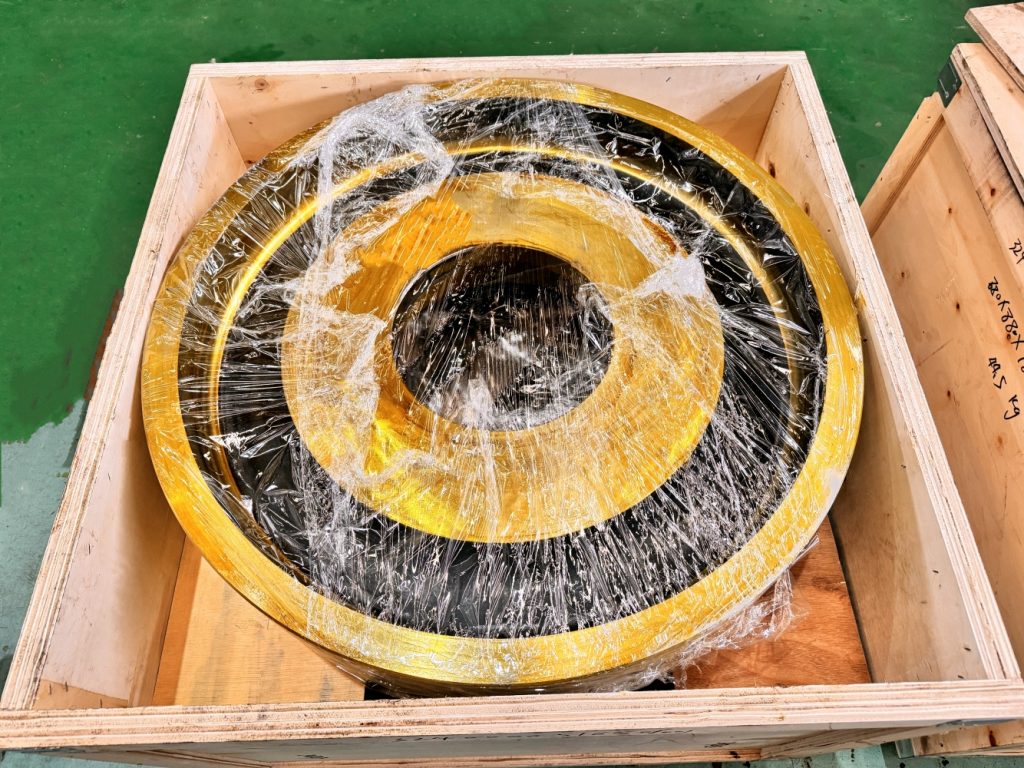
FAQs of Casting wheel
1. What are the choices of gear materials produced in your factory?
We offer a wide selection of materials, including cast iron, cast steel and alloy steel, depending on your application needs. Each material has its own specific mechanical properties, such as wear resistance, strength and toughness. We can recommend the most suitable materials according to your specific requirements.
2. What is the accuracy level of the gear?
Our gear machining accuracy can reach the ISO standard level 6 or higher. Through advanced CNC equipment and strict quality control process, to ensure that each gear tooth shape, pitch and radial run out and other key parameters are in line with the design requirements, to meet the needs of high-precision transmission.
3.How do you guarantee the quality of gear?
We implement a total quality management system, from raw material procurement to finished products, every link is strictly tested. Advanced equipment such as hardness tester is used for accurate measurement, and strict heat treatment process is implemented to ensure the quality of each gear is stable and reliable.
4. How long is the lead time?
The lead time for standard products is usually 45-60 Days, depending on the number and complexity of the order. For urgent orders, we can also arrange urgent production to shorten the delivery time as much as possible. We will make a detailed production plan according to your needs and communicate the progress in time.
5. Do you provide customized service?
Yes, we offer a full range of customized services to design and manufacture non-standard gears according to your special needs. Whether it is size, material or surface treatment requirements, we are flexible to ensure that we provide you with the most suitable solution. Please provide detailed technical specifications so that we can quote accurately.
REQUEST A QUOTE
RELATED PRODUCTS
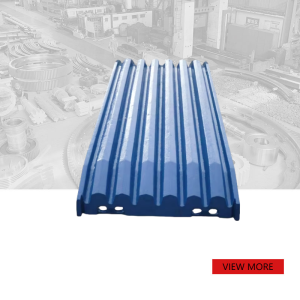
Mining Machinery parts Casting Jaw Crusher Jaw Plates
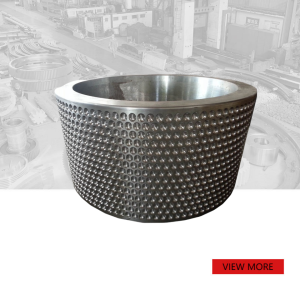
Custom Forging Large Roller Shell High Quality Briquetting Machine Roll Shell Dimpled Roller Shell
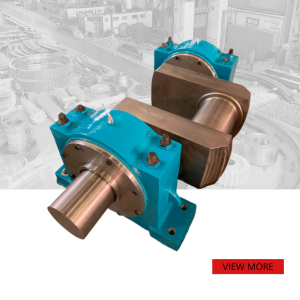
Custom eccentric shaft with bearing seat
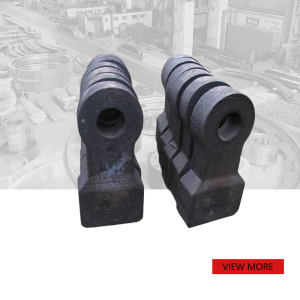
Customized High-chromium Alloy Steel Large Cast Crusher Hammer
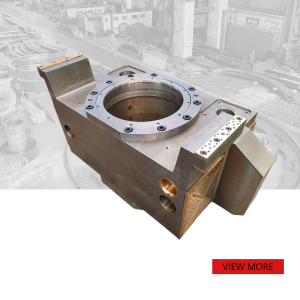
Non-standard alloy steel large diameter casting Bearing seat
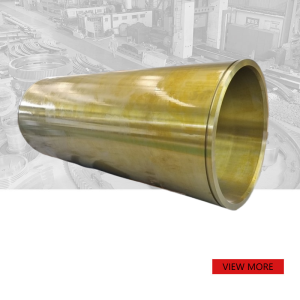