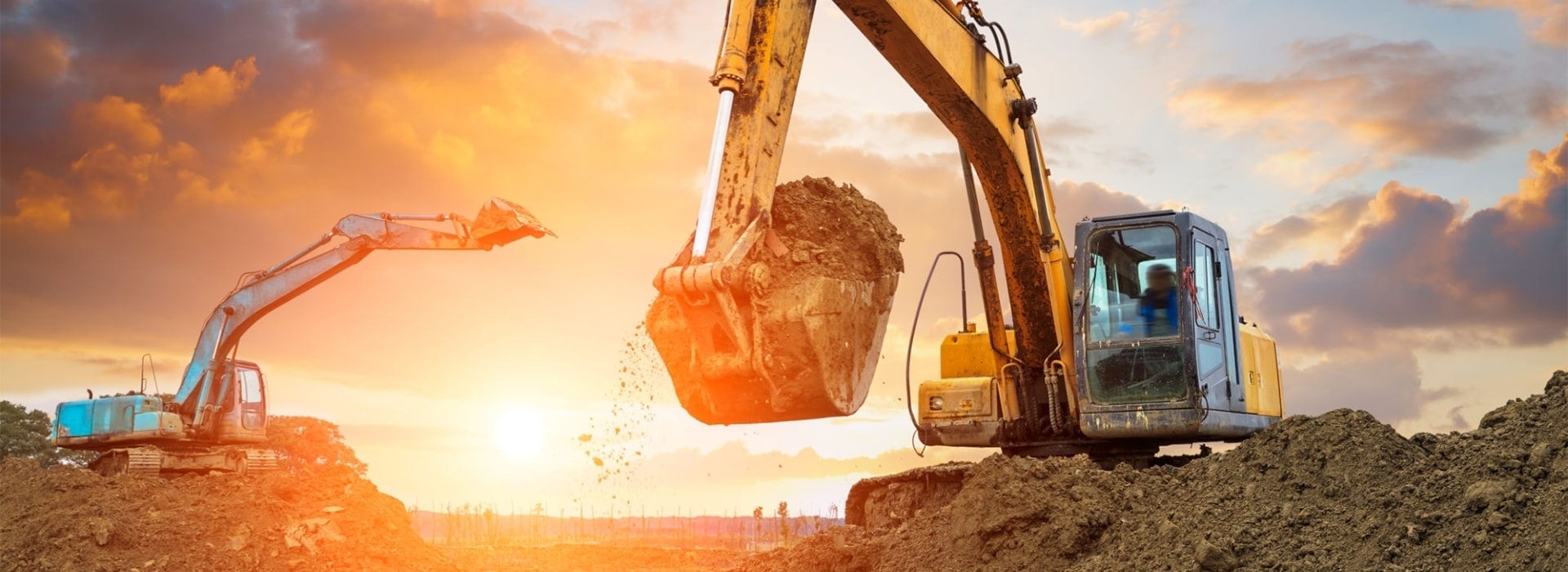
Dragline excavator custom forging rail
PRODUCT PARAMETERS
Description
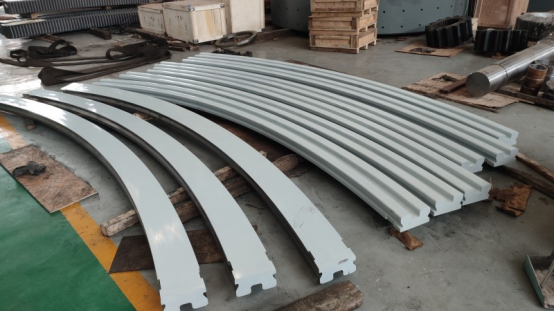
1. Forging
The rail blank is heated to a high temperature and formed through a forging process to improve the density and mechanical properties of the material.
After forging, it is cooled to avoid cracks or deformation caused by rapid cooling.
2. Material chemical composition testing
Through hardness testing, it is determined whether the strength, wear resistance and toughness of the rail material meet the design requirements, and possible defects such as uneven structure, overheating or overburning are discovered in time.
3.Rough machining
Use CNC machine tools (such as lathes or milling machines) to perform preliminary machining on the rail, including rough machining of the outer circle, inner hole and end face.
Ensure that the basic shape and size of the parts are close to the final requirements.
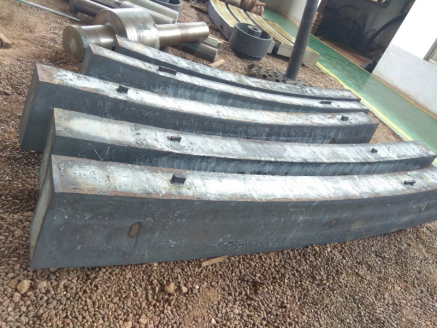
4. UT
Since the quenching and tempering treatment may cause changes in the internal structure of the rail material or generate residual stress, ultrasonic testing is performed after quenching and tempering.
(1) Detect internal defects: Detect cracks, pores, inclusions or other internal defects that may occur in the rail during the quenching and tempering process.
(2) Evaluate material quality: Ensure that the internal structure of the rail after quenching and tempering is uniform and meets the design requirements.
(3) Verify the process effect: Check whether the quenching and tempering has an adverse effect on the integrity of the track.
5. Quenching and tempering
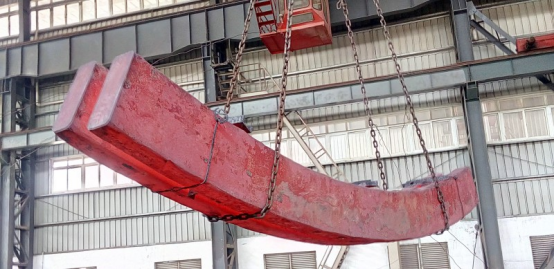
(1) Comprehensive performance: Through quenching and tempering, the material has high strength, hardness, toughness and wear resistance.
(2) Eliminate internal stress: Reduce the residual stress caused by quenching and prevent the workpiece from deformation or cracking.
(3) Optimize the organizational structure: Form a uniform tempered troostite (or tempered troostite) structure to improve the performance of the material.
6. Semi-finishing
While ensuring a certain processing accuracy, create good conditions for subsequent finishing.
(1) Improve processing accuracy: Further reduce the allowance on the track surface to make the dimensional accuracy and shape accuracy close to the final requirements.
(2) Improve surface quality: Reduce surface roughness and provide a better foundation for finishing.
(3) Stabilize workpiece performance: By removing some areas where residual stress is concentrated, reduce the risk of deformation during subsequent finishing.
7. Aging anti-deformation treatment
Eliminate or reduce the internal residual stress of the track through heat treatment or natural placement. Improve the dimensional stability and mechanical properties of the track to avoid deformation during subsequent processing or use.
8. Finishing
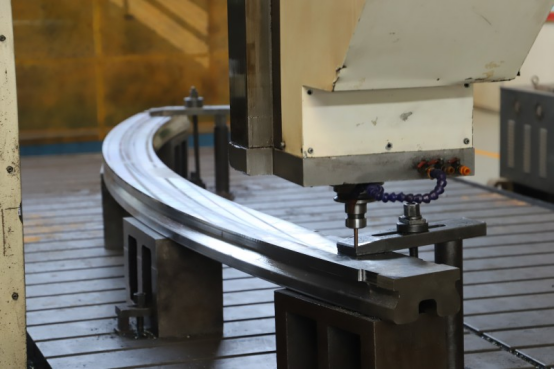
(1) Improve processing accuracy: Ensure that the dimensional accuracy, shape accuracy and position accuracy of the workpiece meet the design requirements.
(2) Improve surface quality: Reduce the surface roughness value and obtain a smooth surface.
(3) Ensure assembly performance: Provide a good mating surface for subsequent assembly and ensure the mating accuracy between parts.