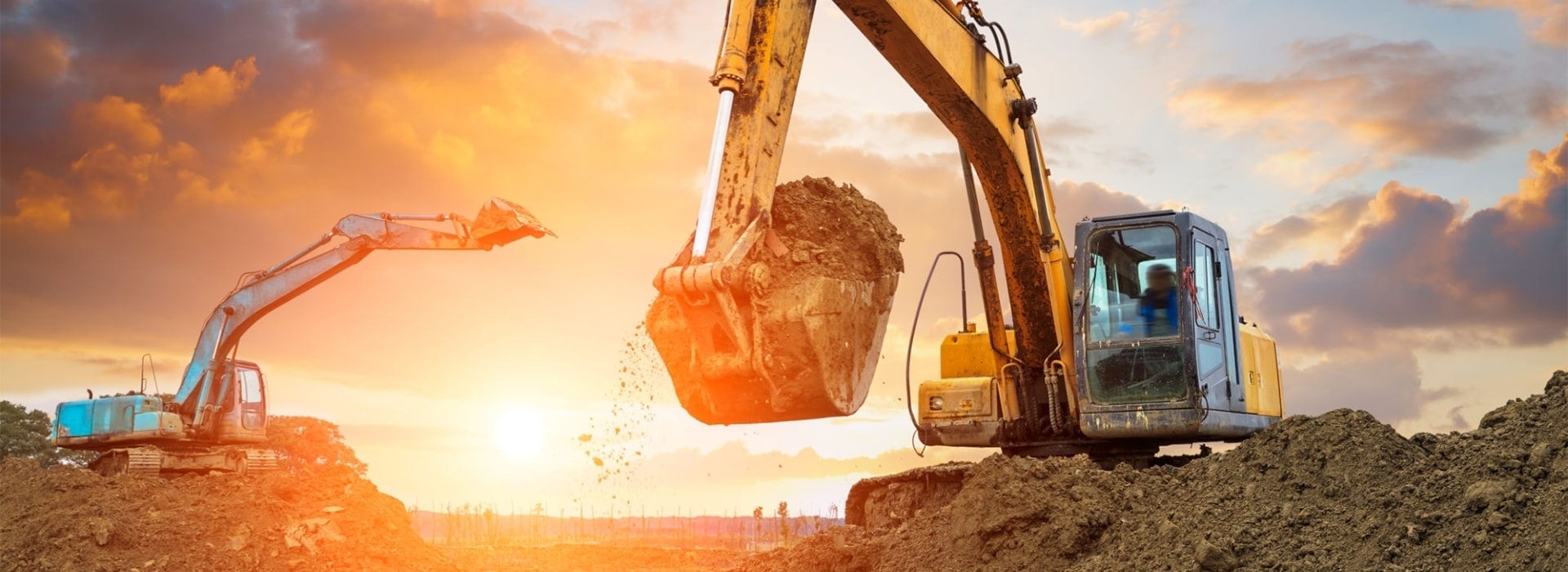
Custom forging gear rack for Dragline excavator
PRODUCT PARAMETERS
Description
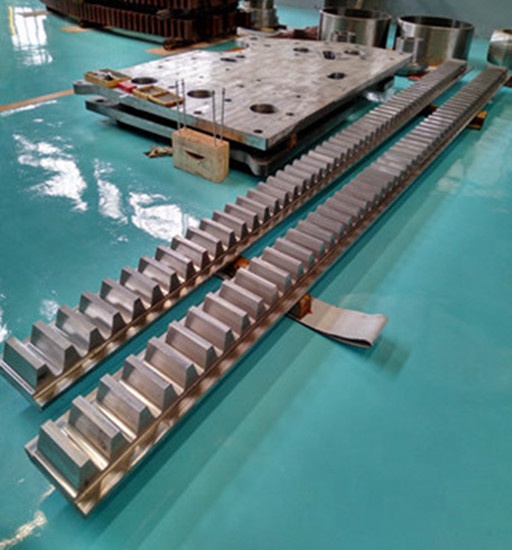
Gear Rack production process
1.Material selection
Common materials: 42CrMo, 34CrNi3Mo or other high-strength alloy structural steels.
Material requirements: high hardenability, good toughness and wear resistance.
2.Forging blanks
Rack blanks are made using free forging or die forging processes to ensure reasonable distribution of metal flow lines.
Annealing treatment is performed after forging to improve cutting performance and eliminate internal stress.
3.Material chemical composition detection
Chemical composition detection of rack materials is a key step to ensure their performance and quality. Racks are usually made of high-strength alloy steels (such as 42CrMo, 34CrNi3Mo, etc.), so their chemical composition needs to be strictly controlled and tested.
Common rack materials and their chemical composition range
(1) 42CrMo
元素 | 含量范围(质量分数/%) |
---|---|
C | 0.38~0.45 |
Si | 0.17~0.37 |
Mn | 0.60~0.80 |
Cr | 0.80~1.10 |
Mo | 0.15~0.30 |
P | ≤0.035 |
S | ≤0.035 |
(2)34CrNi3Mo
元素 | 含量范围(质量分数/%) |
---|---|
C | 0.32~0.38 |
Si | 0.20~0.50 |
Mn | 0.60~0.90 |
Cr | 0.80~1.10 |
Ni | 2.70~3.30 |
Mo | 0.15~0.30 |
P | ≤0.030 |
S | ≤0.030 |
4.Rough machining
Machining the blank to a state close to the final shape and size lays the foundation for subsequent finishing. After rough machining, a finishing allowance of 0.2~0.5mm is required for the tooth surface.
5.UT
Evaluate whether there are defects inside the rack (such as cracks, pores, inclusions, etc.) to ensure material integrity and structural reliability.
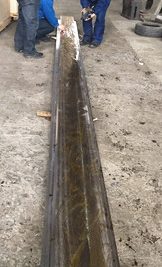
6.Quenching and tempering
Through a combination of quenching and high-temperature tempering, the rack obtains good comprehensive mechanical properties (such as high strength, high toughness and appropriate hardness). Select the appropriate quenching temperature according to the different rack materials.
42CrMo: about 850~880℃.
34CrNi3Mo: about 860~900℃.
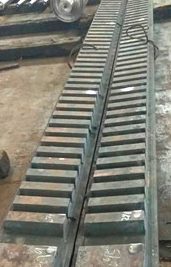
7.Finishing
On the basis of rough machining, further improve the dimensional accuracy, surface quality and meshing performance of the rack. Ensure that the pitch, tooth shape and tooth direction errors are within the allowable range. Further improve the tooth surface finish and contact accuracy, and optimize the transmission performance of the rack.
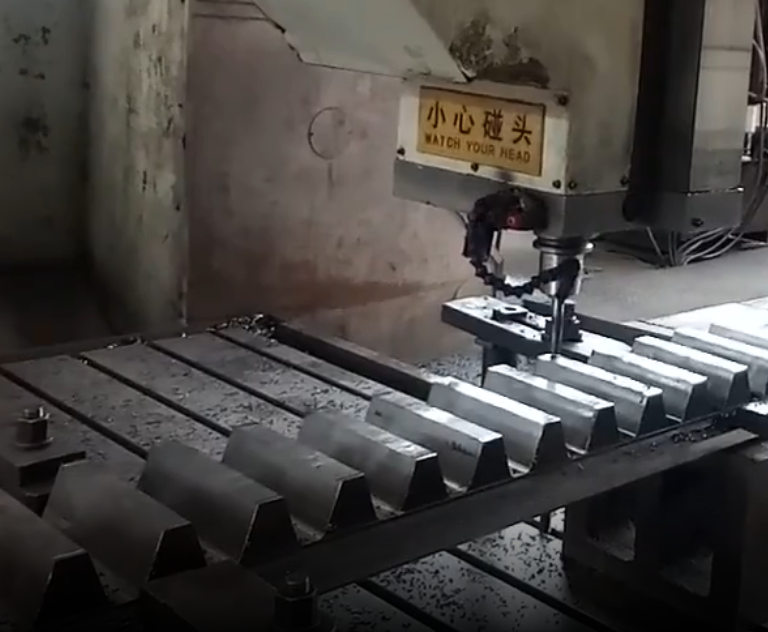
8.Anti-rust treatment and packaging
After the rack is processed, we will perform anti-rust treatment and packaging according to customer requirements to prevent rust or corrosion due to environmental factors (such as moisture, oxidation, etc.) during transportation, storage or use.
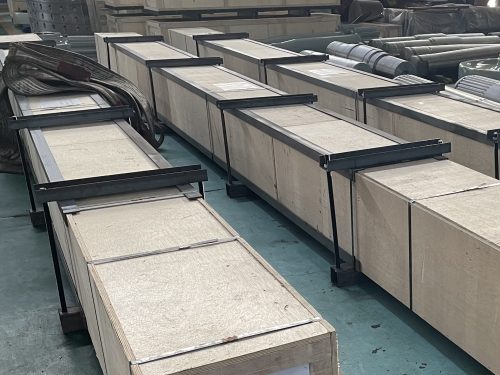
REQUEST A QUOTE
RELATED PRODUCTS
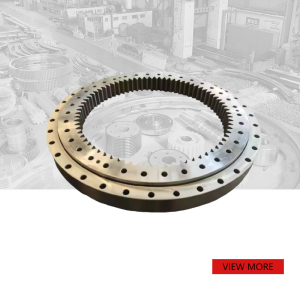
Customized Large Diameter Non-standard Slewing Bearing for Heavy Excavator
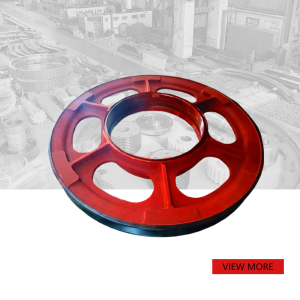
Casting large diameter wear resistant pulley mining dragline
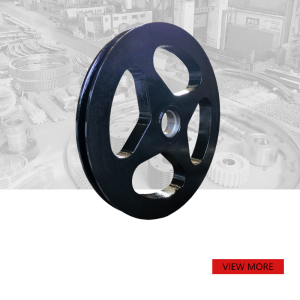
Forging rope wheel for Crane
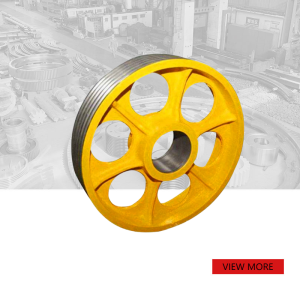
Mining Machinery Dragline Excavator Large Steel Casting Rope Wheel
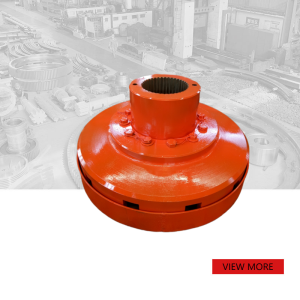
Non-standard alloy steel large diameter Shaft coupling
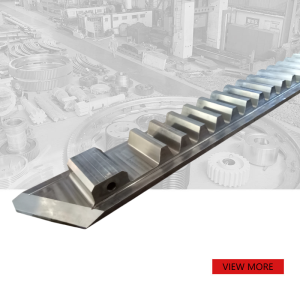