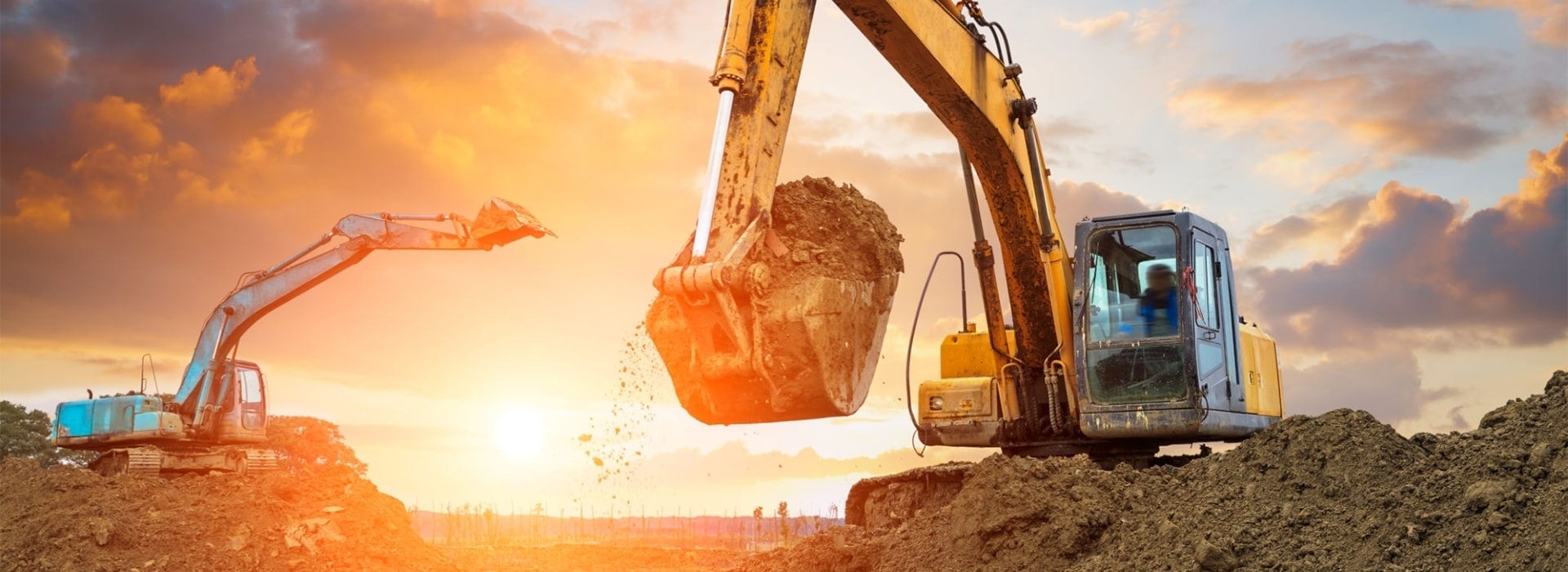
Non-standard alloy steel large diameter Shaft coupling
PRODUCT PARAMETERS
Description
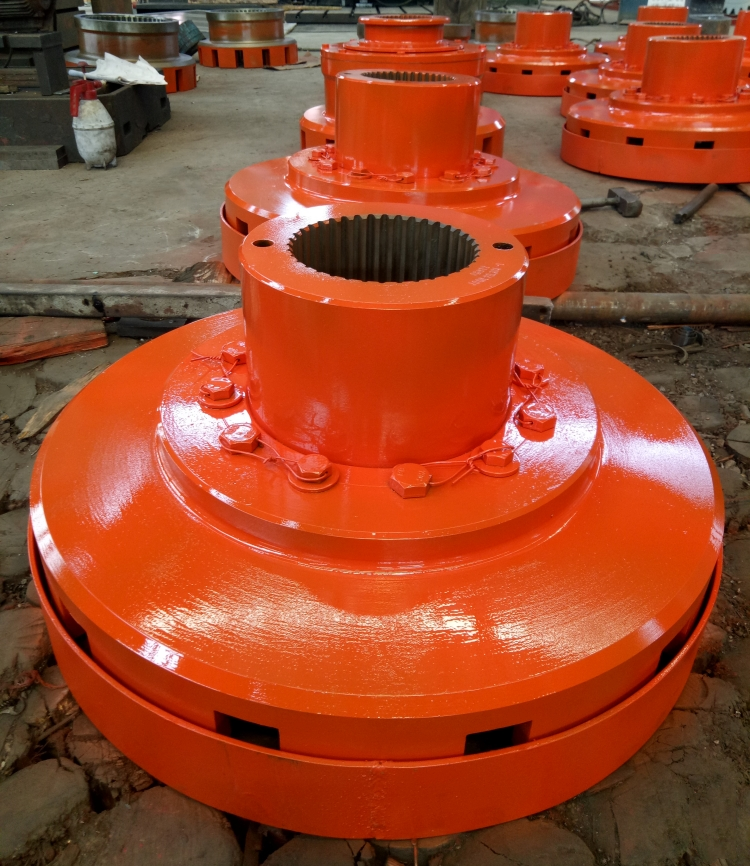
Overview of Shaft coupling
Coupling is a key component in the mechanical transmission system, mainly used to connect two rotating axes, so that they rotate in sync and transmit torque and movement. Its importance lies in its ability to compensate for misalignment errors between the two axes and reduce mechanical failures caused by factors such as installation, lack of manufacturing accuracy or thermal expansion during operation. In addition, the coupling can absorb vibration and shock, reduce the noise and wear of the mechanical system, and improve the working efficiency and service life of the machine. In practical applications, choosing the right coupling type is crucial to ensure the stability and reliability of the mechanical system, and different working conditions require different types of couplings to meet specific needs. Through its functions such as cushioning and damping, couplings are also of great importance for the protection of expensive mechanical equipment.
Q | A | Q | A |
Product name | Shaft coupling | Delivery time | 60-75Days |
Material | Cast Iron | Defect Control | UT, MT |
Process | Casting +CNC machining+HT | Color | Custom |
outer diameter | According to the drawings | weight (kg) | 1680 |
Heat Treatment | Quenching & Tempering | Certificate | ISO9001 |
Production process of Shaft coupling
Casting
Casting blank production is the basis of the entire production process, mainly including mold making, melting and pouring steps. First of all, according to the design drawings, high-precision mold is made to ensure that the casting size is accurate. A suitable material (such as cast iron or cast steel) is then selected and heated to a liquid state in an electric furnace or cupola. After reaching the appropriate temperature, the melted metal is slowly poured into the preheated sand mold through the gate to ensure that the filling is complete and there is no air hole. After cooling and solidification, open the mold and take out the preliminary forming of the coupling blank.
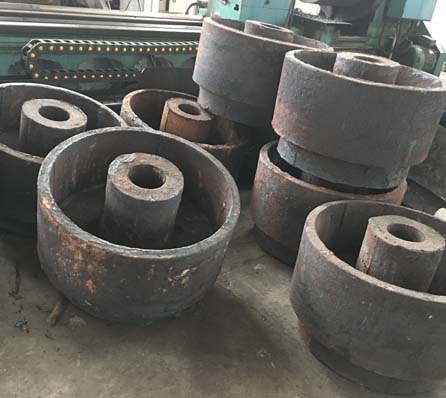
Rough Machining
Roughing is designed to remove excess material from the surface of the blank, bringing it closer to the final size. This stage usually uses lathes, milling machines and other equipment to process the basic shape of the coupling, such as cutting the outer circle, end face and plane. During the roughing process, a certain margin should be reserved for subsequent finishing, and attention should be paid to avoid excessive stress concentration points.
Finishing Machining
Finishing is the fine finishing of the roughed parts to achieve the dimensional accuracy and surface finish required by the design. This step includes but is not limited to grinding, boring, drilling and other operations. Finishing not only requires strict control of dimensional tolerances, but also needs to pay special attention to form and position tolerances to ensure the accuracy of each matching part, so as to ensure the working performance of the coupling.
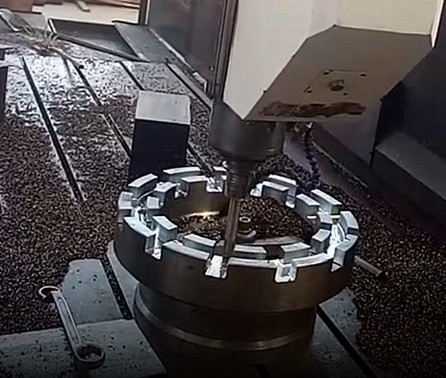
Heat treatment
Heat treatment is to improve the mechanical properties of the coupling, such as strength, hardness and wear resistance. Commonly used heat treatment methods are quenching, tempering, normalizing and so on. After proper heat treatment process, the internal structure of the material can be changed and its comprehensive mechanical properties can be improved. For different types of couplings, the appropriate heat treatment scheme should be selected according to the specific application needs.
Surface treatment
The purpose of surface treatment is to enhance the corrosion resistance, aesthetics and wear resistance of the coupling. Common surface treatment technologies include painting, galvanizing, phosphating and so on. In addition, special coating technologies can be used to meet the requirements of use in specific environments. After finishing the surface treatment, it is also necessary to carry out a comprehensive quality inspection, including dimensional inspection, appearance inspection and the necessary performance testing to ensure that every factory coupling meets the quality standards.
Package of Shaft coupling
Cleaning treatment to remove surface impurities, anti-rust treatment to prevent oxidation, the selection of appropriate packaging materials such as wooden boxes or cartons, and add anti-shock cushion protection, and finally identify product information and handling precautions to ensure transportation safety.
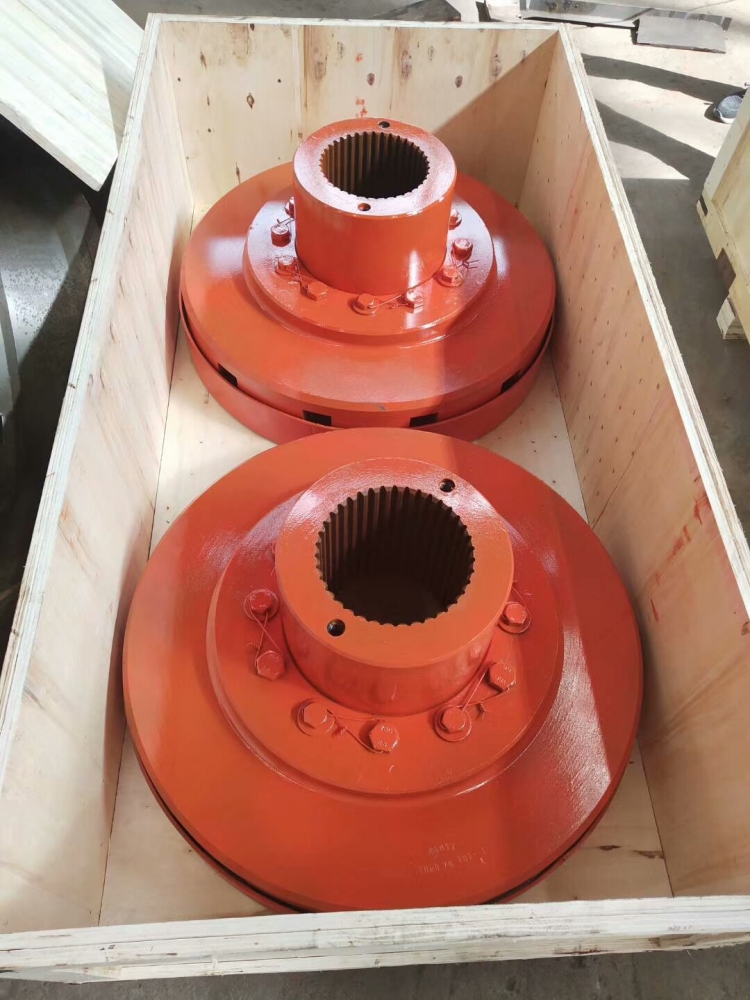
FAQs of Shaft coupling
Q: How to choose the right coupling size?
A: Choosing the right coupling size takes into account the shaft diameter, speed and torque. We recommend matching according to the actual operating parameters, and can provide detailed technical support to help you make the best choice.
Q: Does the coupling need regular maintenance?
A: Some couplings such as elastic or toothed couplings require regular inspection and lubrication, while diaphragm couplings are virtually maintenance-free. Depending on the model, we will provide detailed maintenance guidelines.
Q: Do you offer custom services?
A: Yes, we can customize the coupling according to the special requirements of customers, including size, material and performance parameters. Please provide detailed technical specifications and we will design the most suitable solution for you.
REQUEST A QUOTE
RELATED PRODUCTS
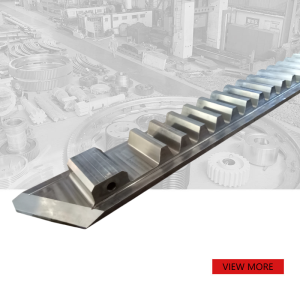
Large mining machinery forging large module helical gear rack
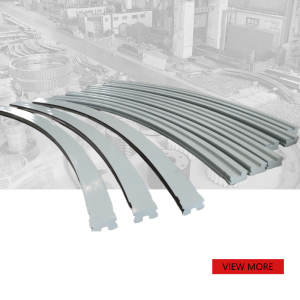
Dragline excavator custom forging rail
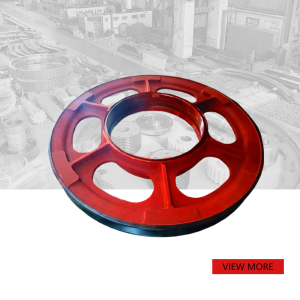
Casting large diameter wear resistant pulley mining dragline
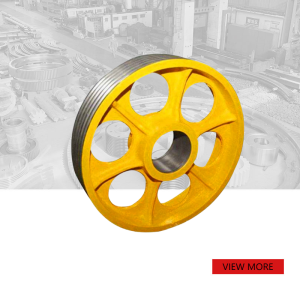
Mining Machinery Dragline Excavator Large Steel Casting Rope Wheel
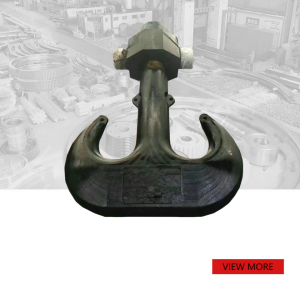
Custom forged alloy steel large crane hook
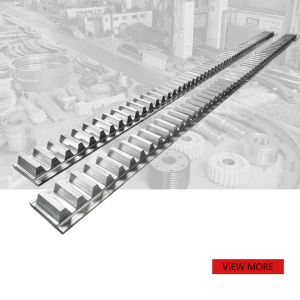