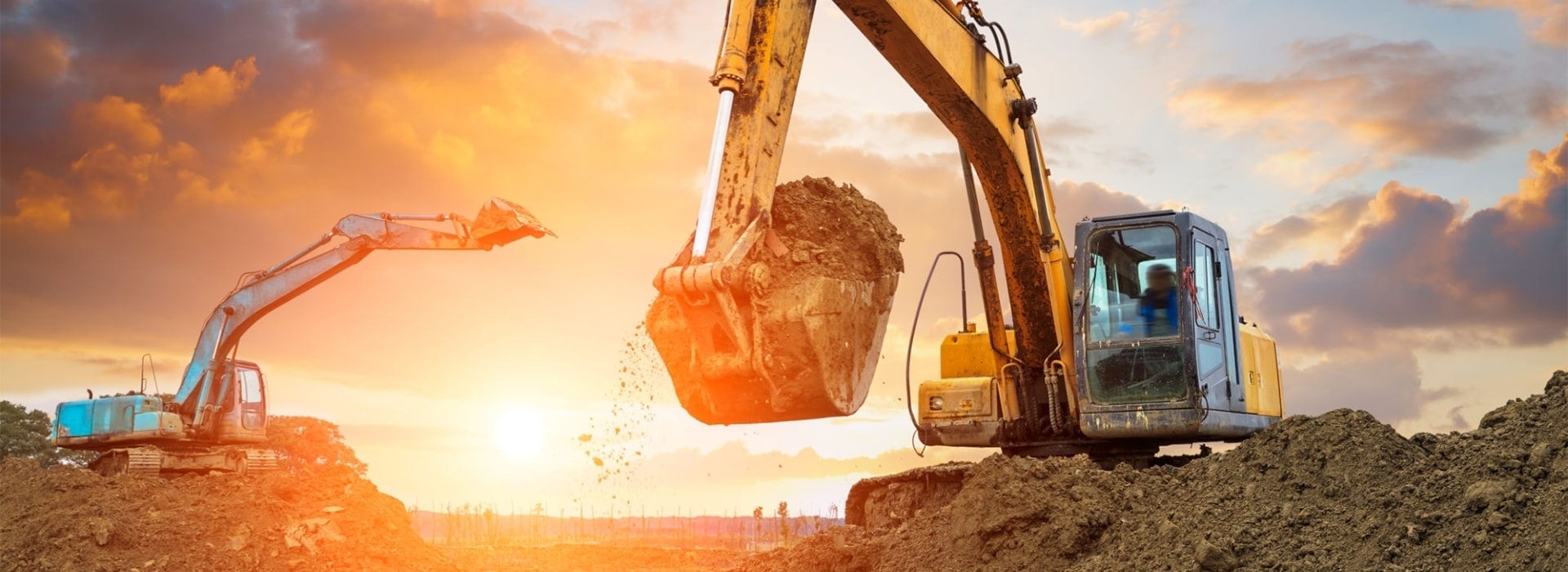
Custom forging double helical gear
PRODUCT PARAMETERS
Description
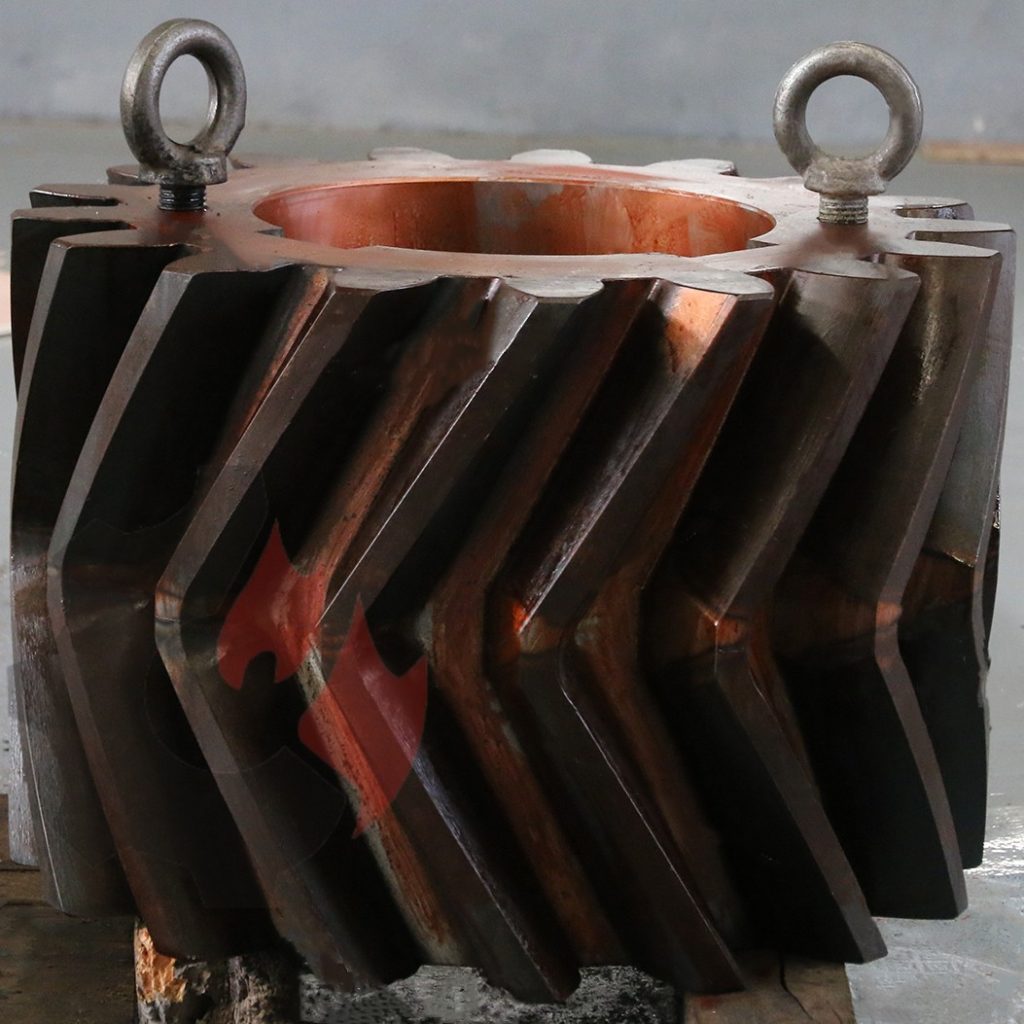
Double helical gear production process
1. Double helical gear forging
Preliminary forging: Use free forging equipment (such as air hammer or hydraulic press) to preliminarily shape the blank to make it close to the shape of the gear blank.
Precision forging: Use die forging equipment (such as hot die forging press) to complete the precise shaping of the gear blank.
During the forging process, it is necessary to pay attention to controlling the temperature and pressure to ensure the density and geometric accuracy of the blank.
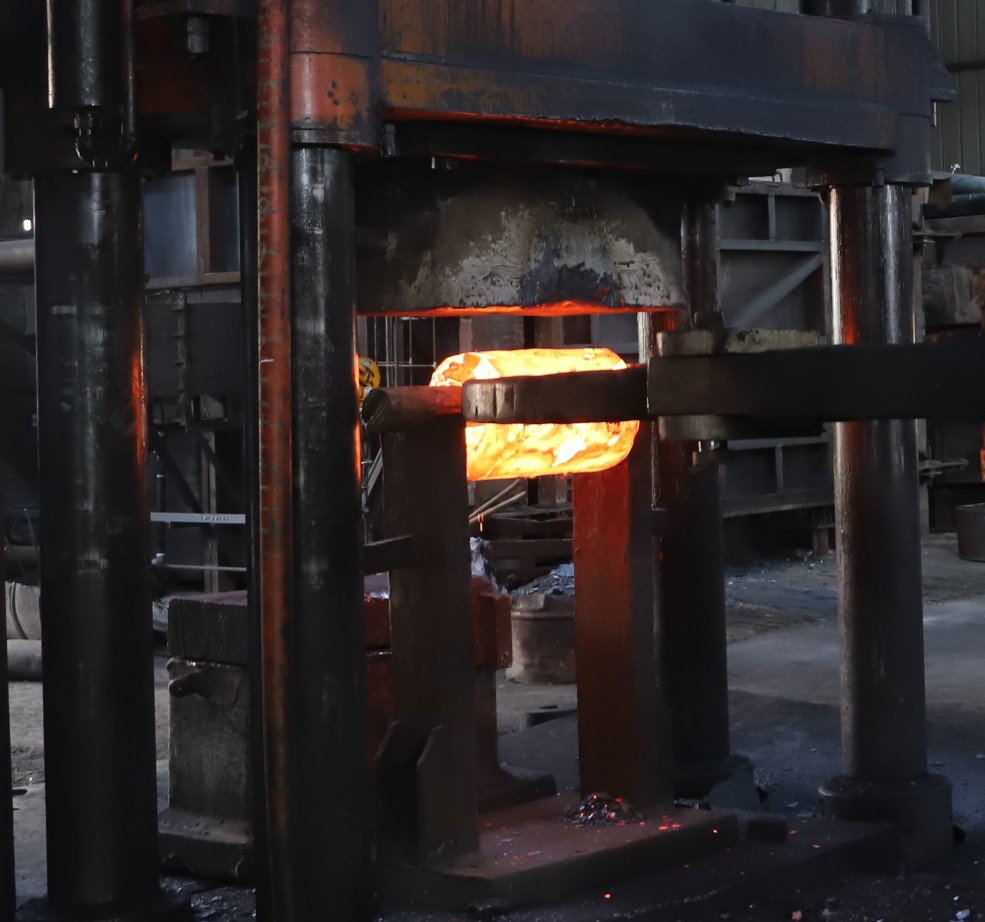
2 Double helical gear cooling
After forging, the blank is slowly cooled to room temperature to reduce internal stress and deformation.
The cooling method can be selected according to the material properties. Air cooling, pit cooling or sand cooling.
3. Double helical gear heat treatment
Normalizing or annealing: Improve the organizational structure of the material, eliminate internal stress, and improve cutting performance.
Quenching and tempering treatment: Improve the comprehensive mechanical properties of the gear through quenching and high-temperature tempering.
Surface hardening treatment (optional): Such as carburizing, nitriding or induction quenching, enhance the surface hardness and wear resistance of the gear.
4. Double helical gear rough machining
Preliminary machining of forged blanks, including:
External turning
End milling
Internal hole machining
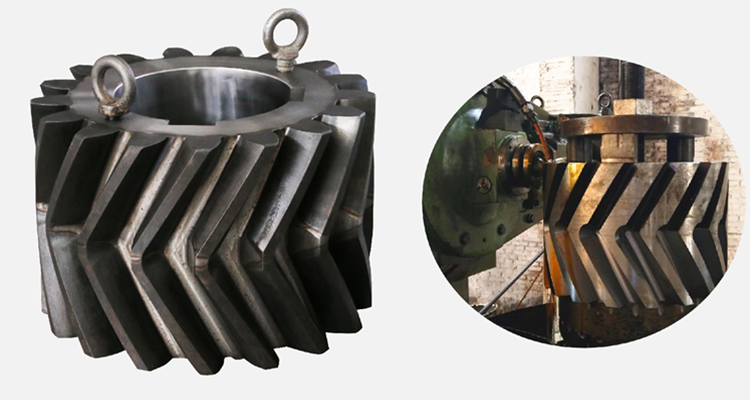
5. Double helical gear tooth profile machining
Herringbone tooth profile is machined using special machine tools (such as hobbing machines or gear shaping machines).
Special attention should be paid to the angle and symmetry of the helical teeth on the left and right sides to ensure the meshing performance of the herringbone gear.
6. Double helical gear finishing
Hone or grind the tooth surface of the gear to improve the tooth profile accuracy and surface finish.
Check the pitch error, tooth profile error and tooth direction error of the gear to ensure that it meets the design requirements.
7. Double helical gear quality inspection
Dimension inspection: Use a three-coordinate measuring machine or a gear measuring center to check the geometric dimensions of the gear.
Hardness inspection: Measure the hardness of the surface and core of the gear with a hardness tester.
Flaw detection: Use magnetic particle inspection or ultrasonic flaw detection to check whether there are defects inside the gear.
8. Double helical gear surface treatment (optional)
Surface coating treatment (such as chrome plating or anti-rust oil) is performed as required to improve corrosion resistance and appearance quality.
9. Double helical gear assembly and packaging
After the qualified gears are cleaned and anti-rust treated, they are packaged and stored according to customer requirements.
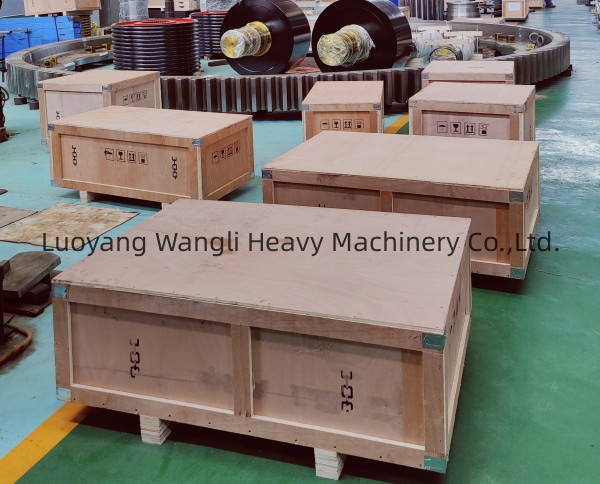
About Us
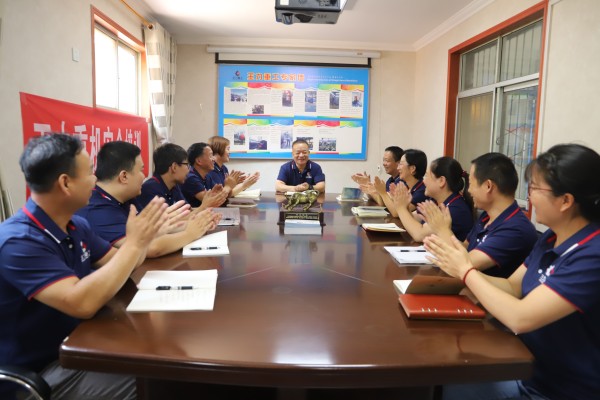
More than 80% reason of mechanical parts’ working life depends on hot processing (steel making, forging/casting , welding, heat treatment). Our eight metal material experts form a team to control our raw material’s internal quality and mechanical properties from the source,in this way to improve our products’ service life.
We have a professional senior engineer team with more than years experience on material,hot and cold processing.
REQUEST A QUOTE
RELATED PRODUCTS
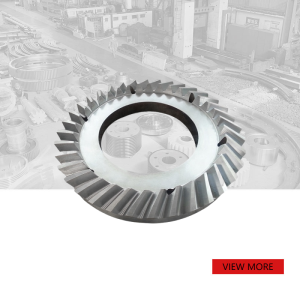
Customized Crusher Large Diameter Spiral Bevel Gear
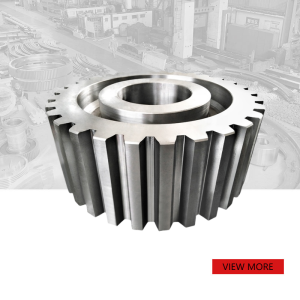
Spur gear forging high quality large diameter pinion gear
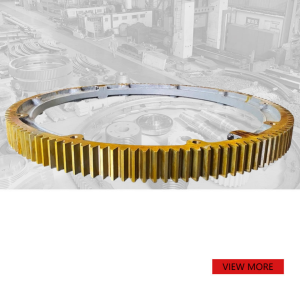
Customized casting ring gear for Ball mill
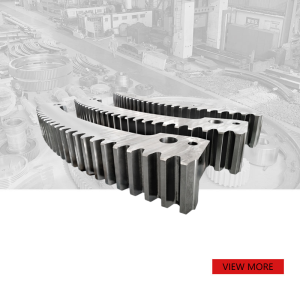
35CrMo Forging Mining large dimeter 12 Segment Arc Tooth
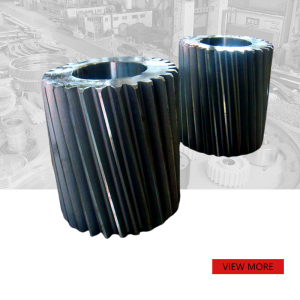
Forging AISI4140 non-standard large Helical gear for ball mill
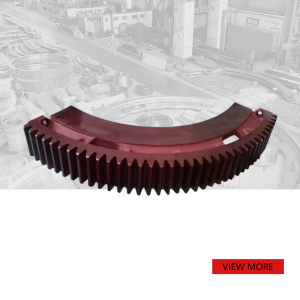