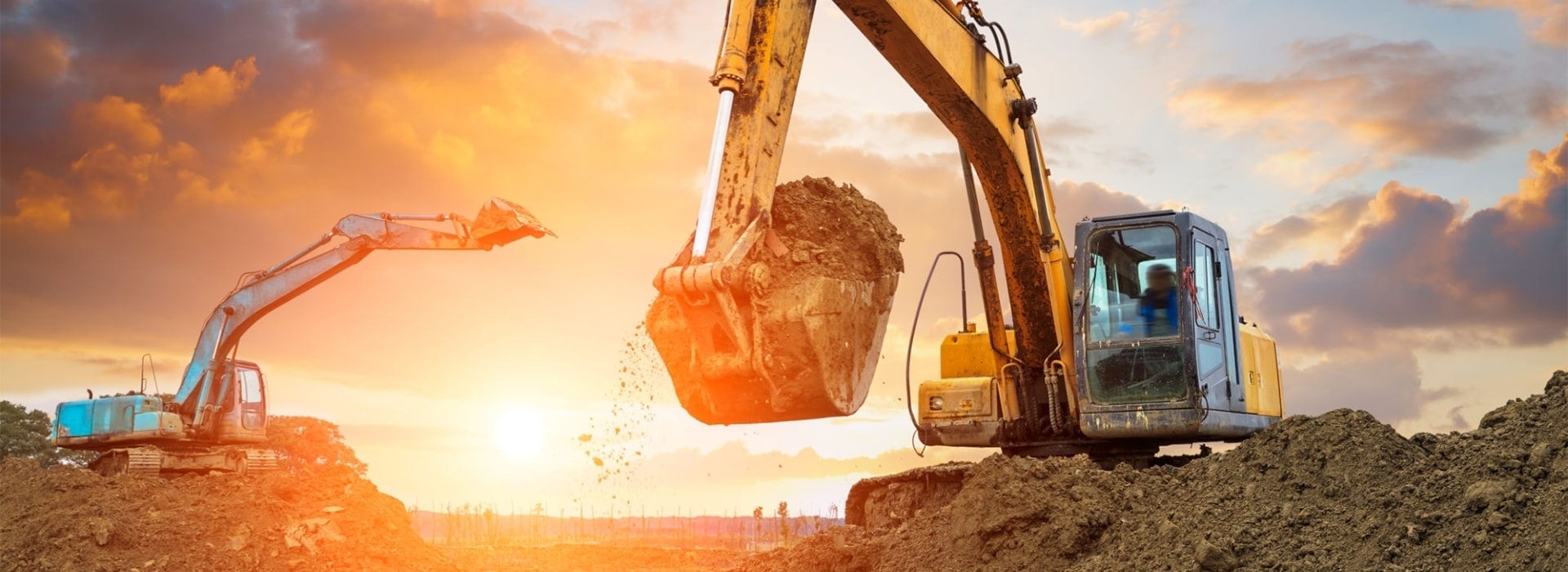
Customized large modulus pinion for rotary kiln
PRODUCT PARAMETERS
Description
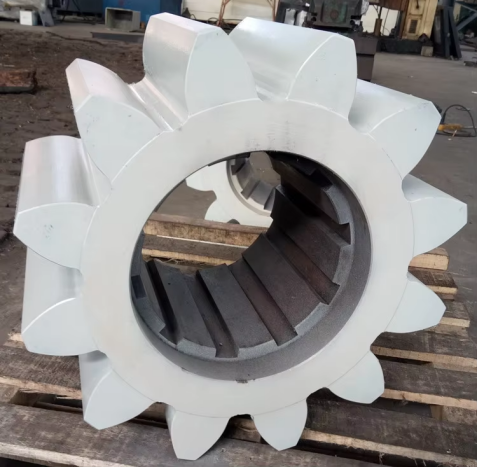
- Overview of rotary kiln mill pinion
The rotary kiln mill pinion is a key transmission component used to drive the rotary kiln. It transmits power to the rotary kiln through meshing with the large gear. This pinion is usually made of high-strength alloy steel to ensure stable operation under high temperature and heavy load conditions. Its design needs to consider factors such as kiln size, speed and load capacity to achieve efficient power transmission and equipment operation.
2. Classification and characteristics of rotary kiln pinion
The rotary kiln pinion is mainly divided into two categories according to the structural form: straight tooth pinion and helical tooth pinion. The manufacturing process of the straight tooth pinion is relatively simple, but the noise is relatively large; the helical tooth pinion has better meshing performance and can reduce the vibration and noise generated during operation. In addition, there are multi-stage reduction pinions designed for special working conditions to meet the needs of different application scenarios.
3. Installation method and function of rotary kiln pinion
The rotary kiln pinion is generally installed on the end of the motor shaft by bolt fixing or interference fit, and is connected to the motor through a coupling. Correct installation is essential to ensure the accuracy of the transmission system. This component is not only responsible for transmitting torque, but also undertakes the task of adjusting the inclination angle of the kiln body to ensure that the material is evenly distributed in the kiln and effectively heated.
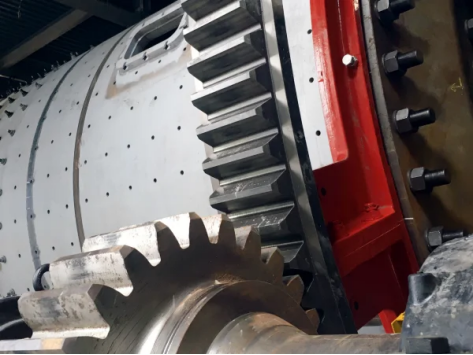
4. Selection and requirements of rotary kiln pinion materials
In view of the harsh working environment, the rotary kiln pinion needs to use wear-resistant and fatigue-resistant materials, such as high-chromium cast iron or nickel-based alloys. At the same time, in order to improve the surface hardness and wear resistance, quenching and quenching treatment will also be carried out. Choosing the right material can not only extend the service life, but also reduce maintenance costs and improve production efficiency.
Specification model
Modulus | M8-M40 |
Tooth width | Determined according to actual application |
Material | High-strength alloy steel (40CrMo 40CrNiMo) |
Heat treatment | Quenching and tempering |
5.Rotary kiln Pinion production process
-Forging
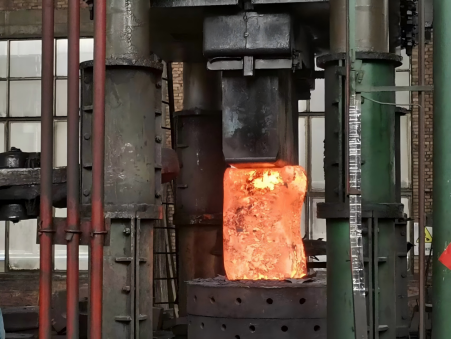
We can make relevant blanks according to customers’ needs.
-Rough turning of blanks
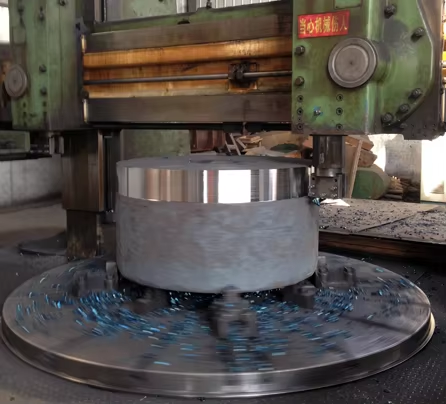
Rough machining can cut off most of the remaining materials in a short time, provide positioning accuracy benchmarks for semi-finishing and finishing, and detect blank defects in a timely manner
-Heat treatment
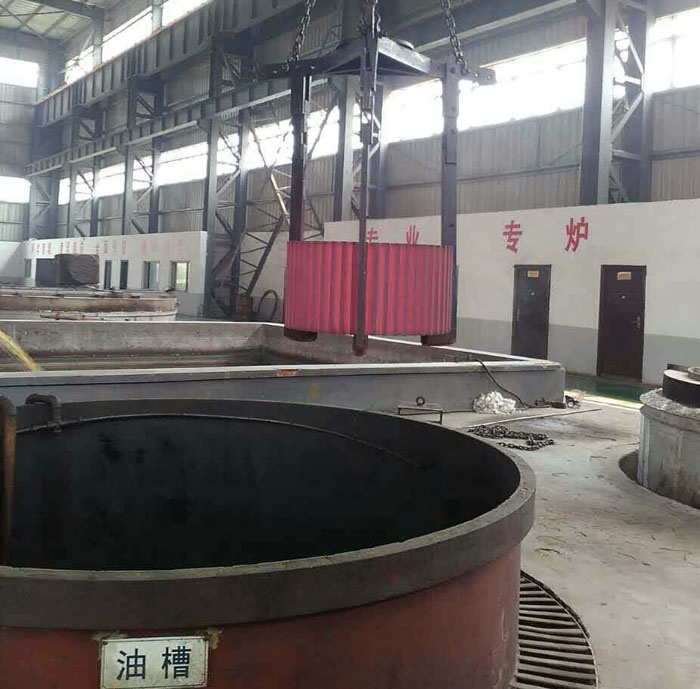
If the gear module is large (above M25), the first hobbing is performed before heat treatment. According to this way, the hardness depth of the gear teeth will be deeper after QT, which can improve the mechanical properties of the gear teeth and can extend the service life of the gear.
-Gear machining
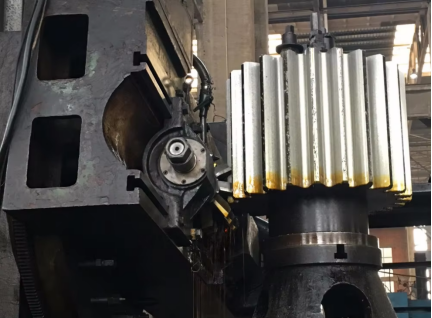
2-3 times precision hobbing to ensure gear accuracy and surface roughness. Only in this way can spur gears be used well with large tooth rings or gear shafts.
-Inspection
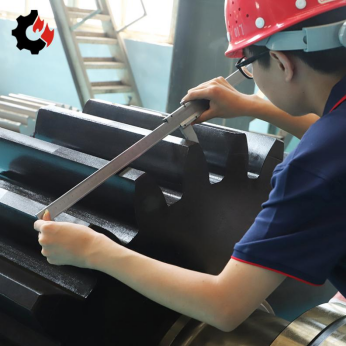
After the gear is completed, we will provide you with a report of raw material, hardness, size information.
-Packaging Rotary kiln Pinion materials are sustainable and recyclable, with little impact on the environment.
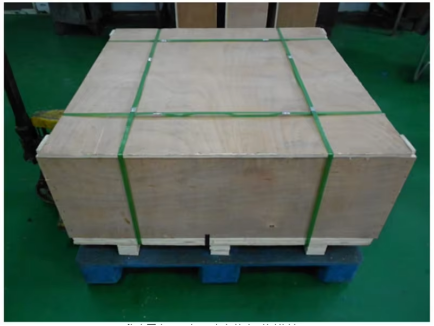
6.Why Choose Us
–OEM Mechanical Parts Supplier
More than 30 years of experience in manufacturing OEM mechanical parts and non-standard mechanical parts according to engineers’ drawings.
-Technical Support for Materials
Provide technical support for new materials and new manufacturing processes according to customers’ working conditions to improve the service life of mechanical parts.