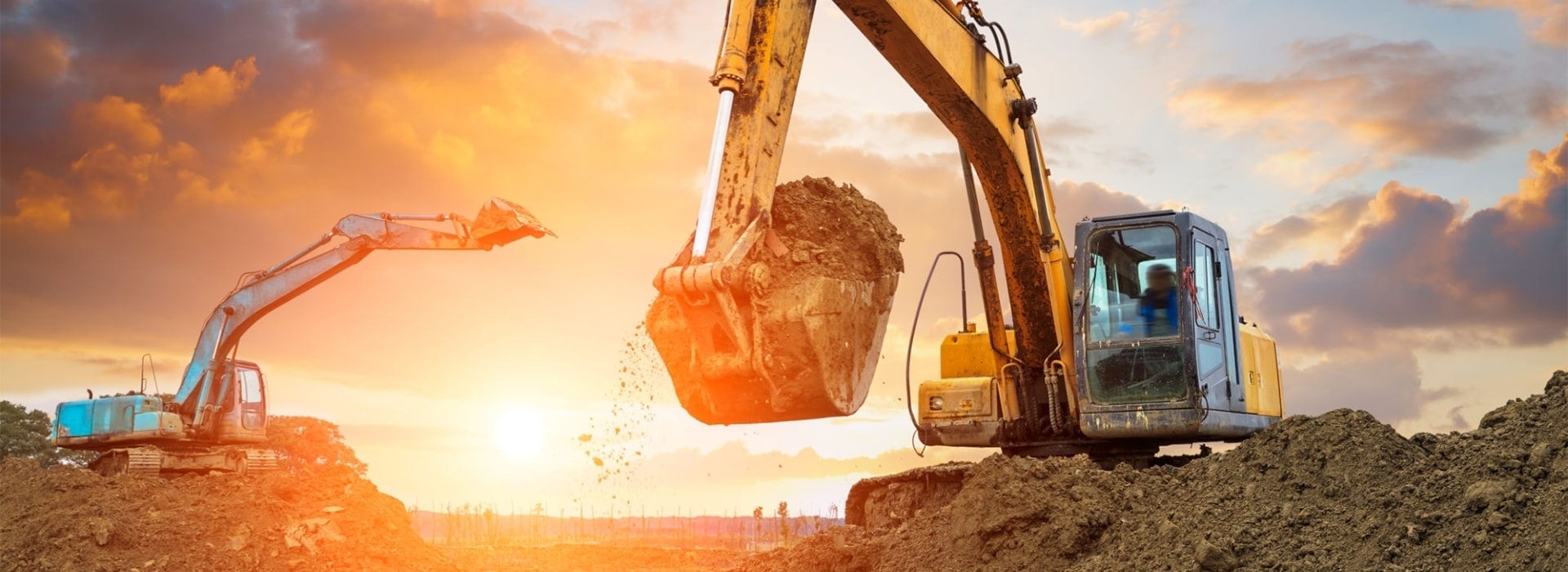
Large Casting Iron two-segment Ring Gear Rotary Kiln
PRODUCT PARAMETERS
Description
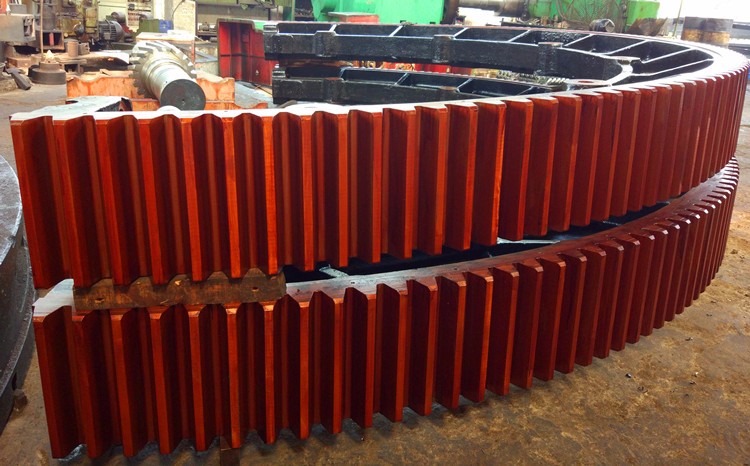
Overview of two-segment casting ring gear
A two-segment gear ring (also known as a double-segment gear or segmenting gear) is a special gear design that divides a complete gear into two separate parts, each with a certain number of teeth. This design allows for different transmission ratios or intermittent power transfer within a rotation cycle。
Q | A | Q | A |
Product name | Two segment ring gear | Delivery time | 75-120Days |
Material | Cast Iron | Defect Control | UT, MT |
Process | Casting +CNC machining+HT | Diameter | 2M |
outer diameter | According to the drawings | weight (kg) | 15t |
Heat Treatment | Quenching & Tempering | Certificate | ISO9001 |
Application of two-segment casting ring gear
The casting gear ring plays a key role in driving and supporting the rotary kiln, and transmits power by connecting with the drive system to ensure the smooth rotation of the kiln body. It helps evenly distribute heat, prevent material from forming rings, maintain a stable temperature field, and ensure product quality. High temperature and wear resistance extend service life and support precise speed control to ensure efficient production.
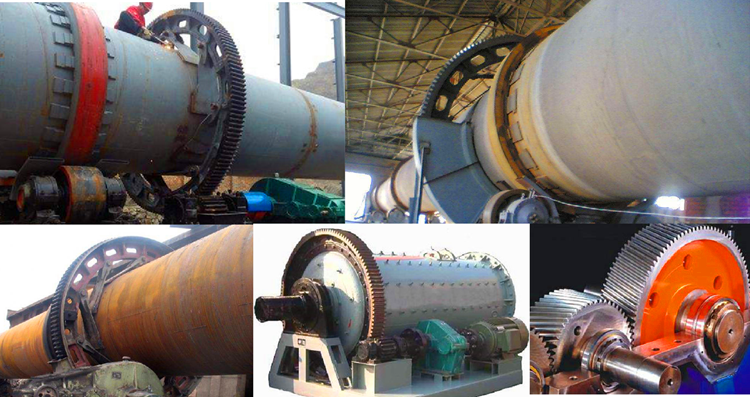
Production process of two-segment casting ring gear
Casting
The blank process of the casting gear ring includes: designing the mold, melting the appropriate metal, pouring the molten metal into the preheating mold, cooling and solidifying the mold, initially cleaning the surface, and forming the casting blank with the basic shape of the gear ring.
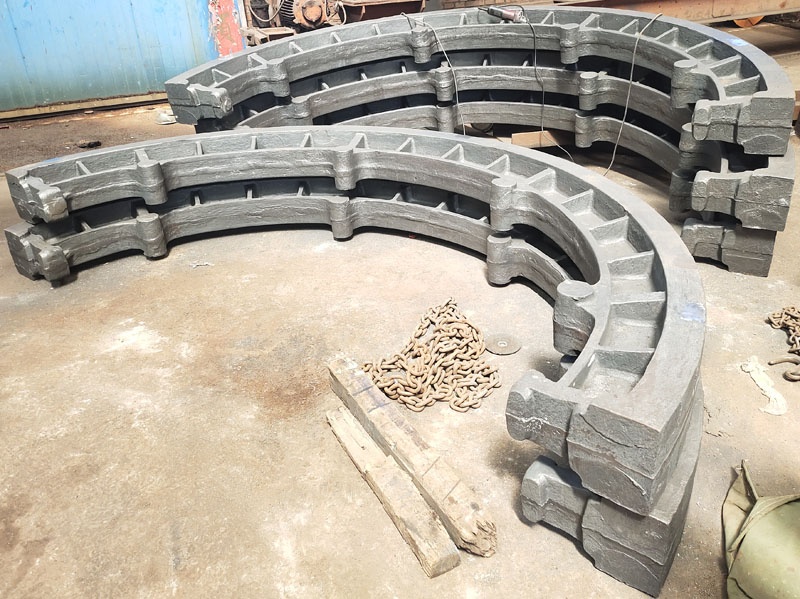
Rough Machining
The roughing process of the cast ring begins with the removal of excess material from the casting, such as the sprue. Initial turning or milling is then carried out to approximate the final size, ensuring the basic shape of the gear ring and the accuracy of the hole position. Then, the inner diameter and mounting holes are treated by boring, drilling and other processes. Roughing also involves correcting for possible casting deformation to ensure a level base for subsequent finishing. The whole process is designed to provide a semi-finished product with accurate dimensions and good surface quality for finishing.
Heat treatment
The heat treatment of the cast gear ring includes normalizing, quenching and tempering to improve hardness and toughness. The gear ring is heated to a specific temperature in a high temperature furnace, then cooled rapidly, and finally tempered to stabilize the organization, ensuring mechanical properties and dimensional accuracy.
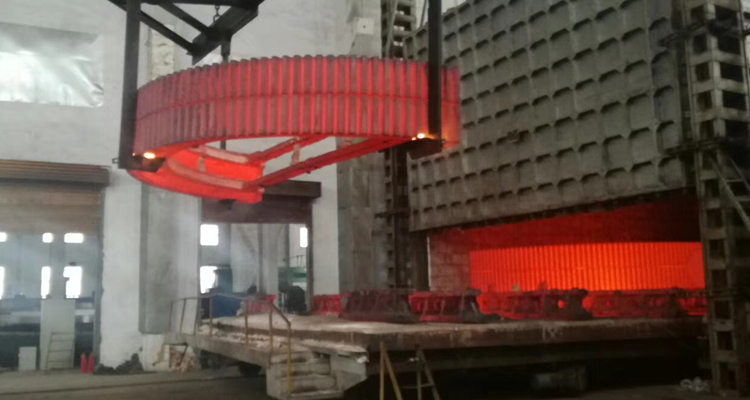
Finishing
The finishing process of the cast gear ring begins with the removal of the spout and cleaning of the surface, followed by heat treatment to optimize the material properties. Then the dimensional accuracy is ensured by turning, milling and other processes, and the quality and smoothness of the tooth surface is improved by using a gear grinder or honing machine.
Finally, strict testing is carried out, including tooth profile error, hardness test, etc., to ensure that design requirements and application standards are met. The whole process guarantees the mechanical properties and service life of the gear ring.
Package of two-segment casting ring gear
Oiling or Coating: Applying a thin layer of rust-preventative oil or another protective coating can shield the surface from moisture and contaminants.
Packing: fumigation-free wooden case customized according to product size. If necessary, a steel frame will be welded to the outside of the wooden box to assist the operation of the forklift truck.
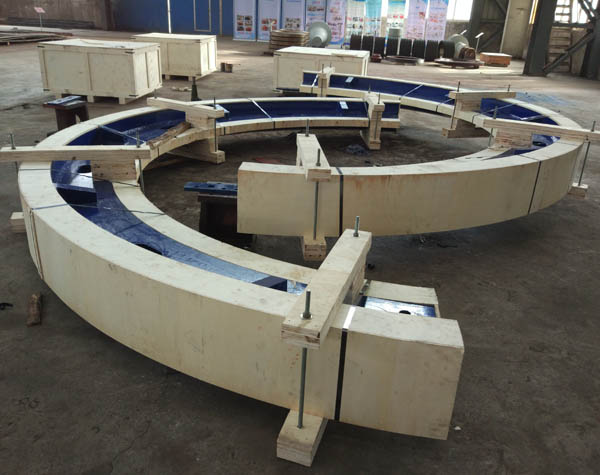
FAQs of two-segment casting ring gear
1.What module of gear can you produce? –8-120
2.What is the accuracy grade you can achieve? –6-8
3.What kind of payment terms do you have? –T/T & L/C
4.Are you subject to third-party testing?-Yes
5. What’s your ship method?– By sea. By rail. By air.