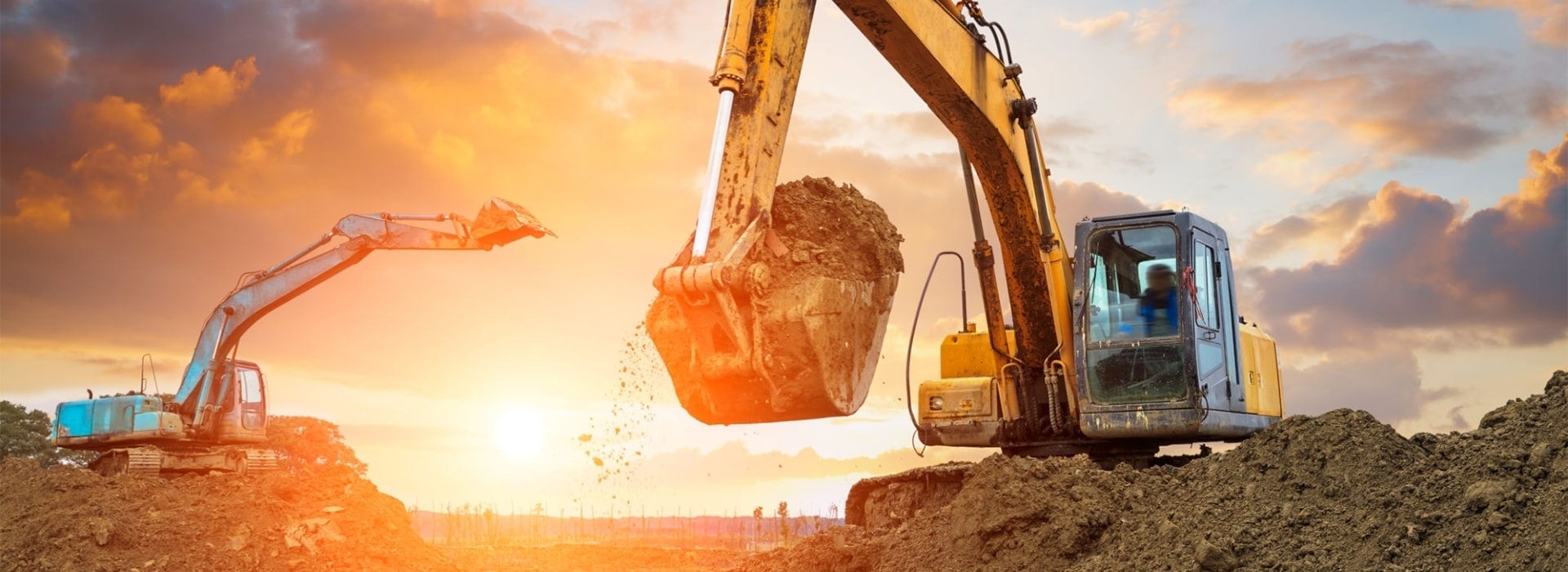
Mining custom high quality large heavy gear box
PRODUCT PARAMETERS
Description
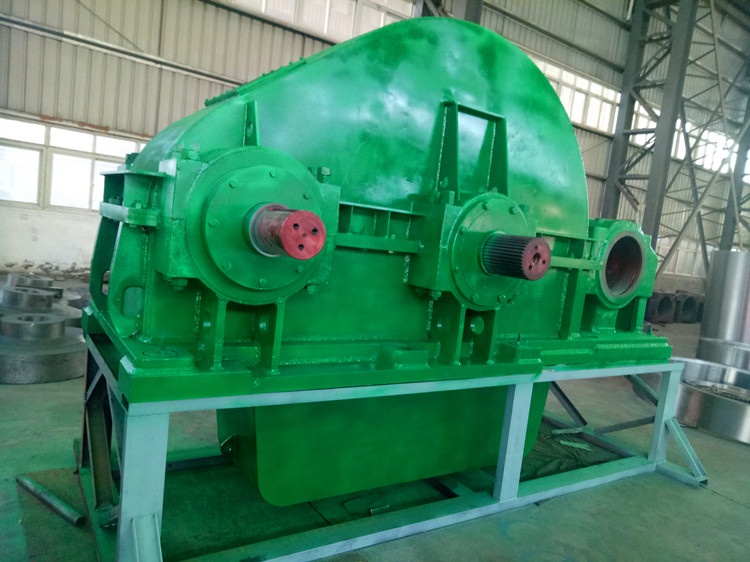
Reducer classification: Classification by structure
1. Gear box: This is the most common type of reducer, which achieves speed reduction and torque increase through the meshing of a series of gears. According to the different arrangements of gears, it can be divided into:
Cylindrical gear box
Bevel gear box(commonly used to change the direction of force)
Worm reducer
2. Planetary reducer: It adopts a planetary gear system and has the characteristics of small size, light weight, and large load-bearing capacity. Suitable for application scenarios that require high-precision positioning and dynamic response.
3. Cycloidal pinwheel reducer: It uses the special meshing form between the cycloid wheel and the pinwheel, and has the advantages of compact structure, large transmission ratio, and high efficiency.
4. Harmonic reducer: It relies on the controllable elastic deformation generated by flexible elements to transmit motion and power, which is particularly suitable for precision control fields such as robot joints.
Typical processing flow of the main components of the reducer (such as housing, gears, etc.):
Reducer housing processing
1. Raw material preparation: Cast iron or steel is usually used as raw material, and cutting is performed according to the design drawings.
2. Casting/welding: For large reducer housings, casting is generally used for molding; for some small housings with high strength requirements, forging may be selected.
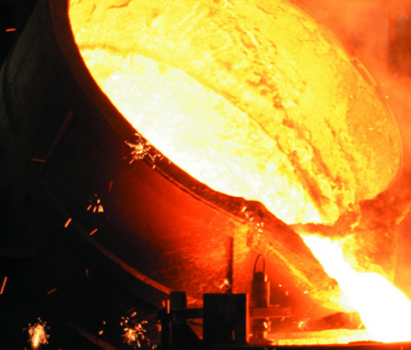
3. Rough machining: Preliminary machining of castings or forgings, including turning, milling and other processes, to remove excess material and form a rough outline.
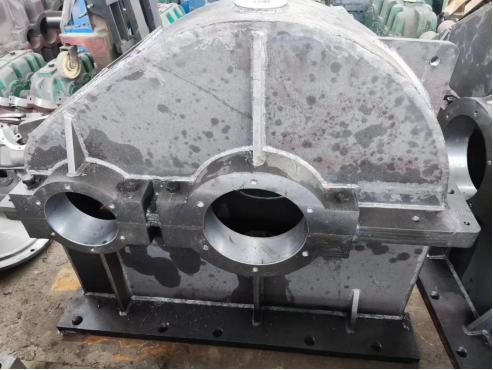
4. Heat treatment: In order to improve the hardness and wear resistance of the housing, heat treatment operations such as normalizing and tempering are sometimes required.
5. Finishing: Use precision machine tools to complete the fine machining of key parts such as bearing holes and mounting surfaces to ensure that the dimensional accuracy and surface finish meet the requirements.
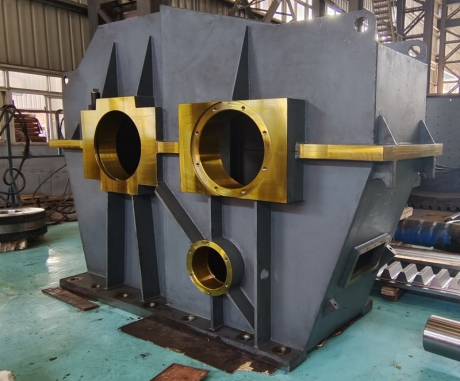
6. Inspection: Use tools such as three-coordinate measuring instruments to check whether the processed parts meet the design specifications.
Gear processing
1. Blank manufacturing: Select the appropriate material according to the design parameters of the gear and make it into a blank form. This step may involve forging or bar cutting.
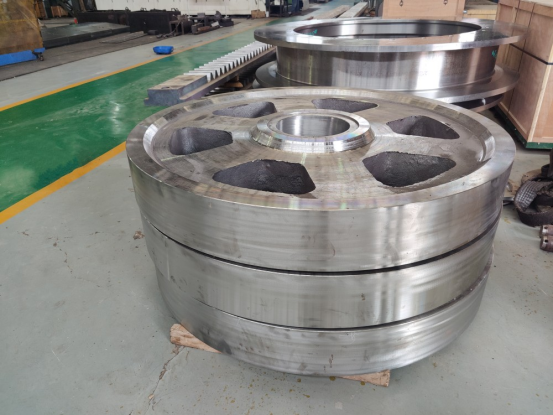
2. Tooth profile rough machining: Use a hobbing machine or a gear shaping machine to perform preliminary tooth profile machining on the gear blank.
3. Heat treatment: The gears are carburized and quenched or other appropriate heat treatment methods are used to enhance the hardness and overall strength of the tooth surface.
4. Tooth profile finishing: After heat treatment, the gears need to be ground and shaved again to ensure that the tooth profile accuracy meets the design standards.

5. Surface treatment: In order to improve corrosion resistance and aesthetics, the gear surface can be galvanized, phosphated, etc.
Other component processing
Shaft parts: The shaft is usually directly processed from forging blank, including turning, grinding and other steps.
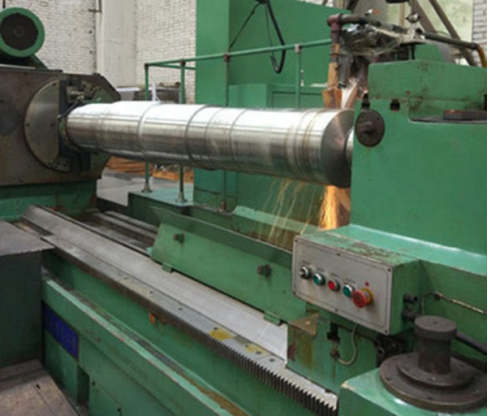
Seals and other accessories: Customized production according to specific needs to ensure compatibility with the entire system.
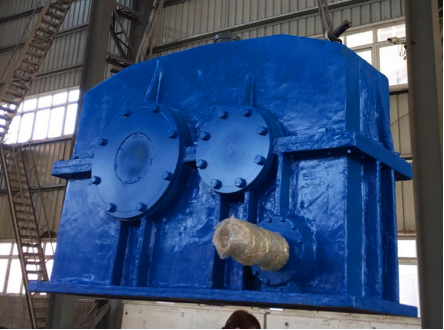
Assembly and testing
Assembly: All processed parts are assembled into a complete reducer according to the assembly drawing.
Debugging and testing: The assembled reducer is fully functionally tested, including no-load operation, load test, and noise detection, to ensure that its performance indicators meet the standards.
Package

According to the requirements of customers, we apply anti-rust oil to the whole product for anti-rust treatment. In addition, we can also paint the products according to the needs of customers to prevent rust. And then it goes into a fumigation-free plywood box