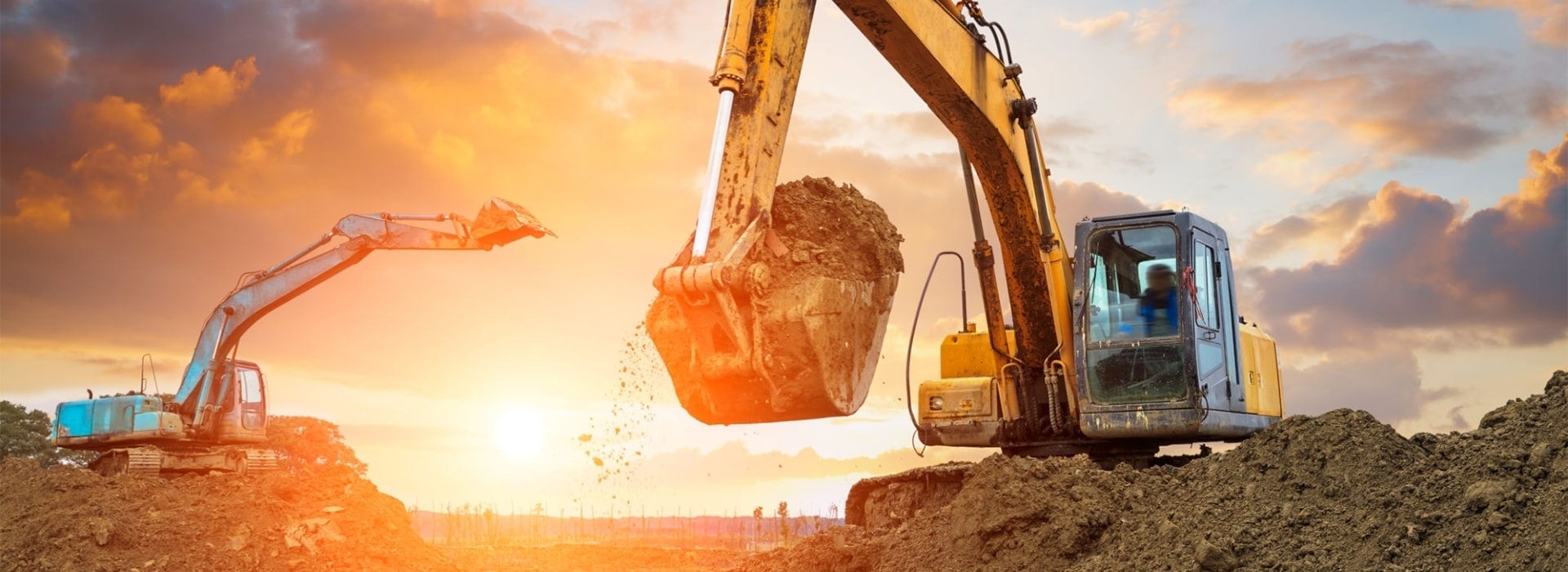
Custom Mining Crusher large heavy main cone shaft
PRODUCT PARAMETERS
Description
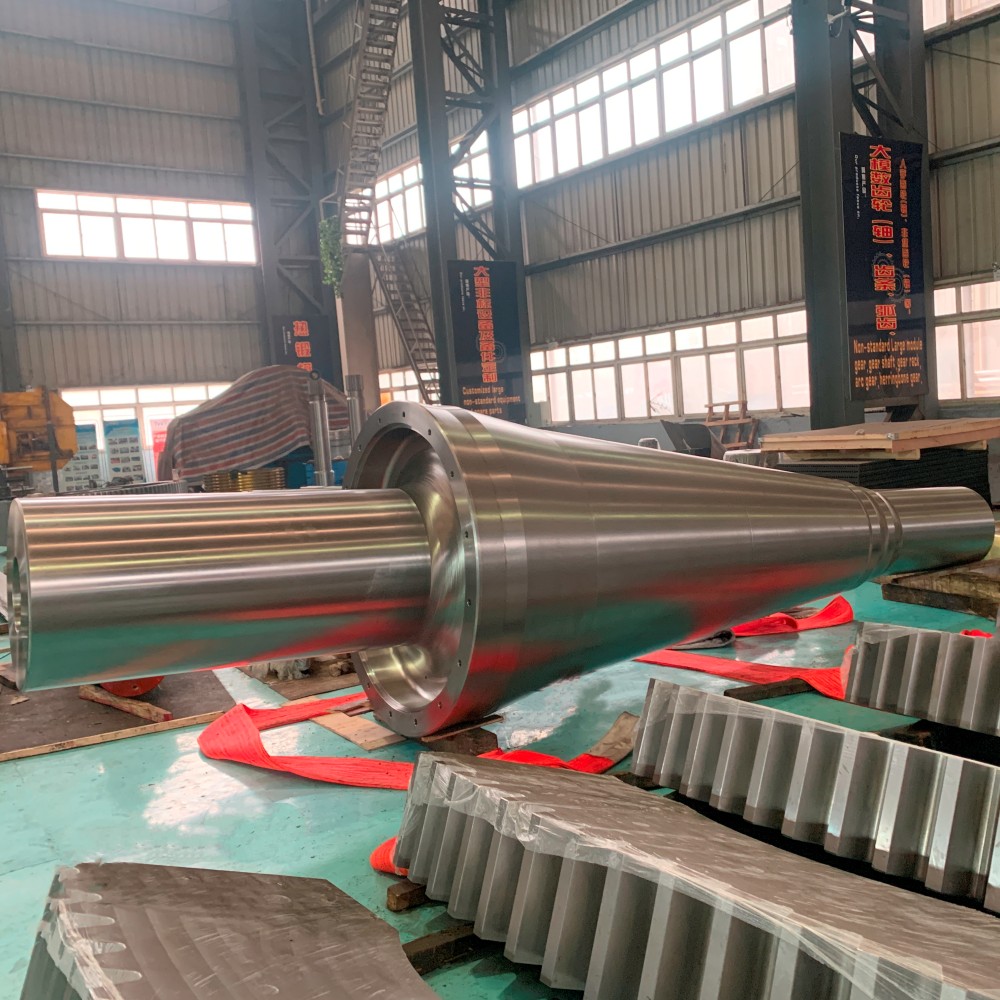
Cone shaft production process
1. Cone shaft heating and forging
Heating: Place the blank in a medium frequency induction furnace or a gas heating furnace and heat it to a high temperature (generally 1100℃~1200℃) to achieve the best state of plastic deformation.
Forging: Use a press or a forging hammer to forge the heated blank to form the basic shape of the main cone shaft. The temperature and forging ratio need to be strictly controlled during the forging process to ensure that the metal fiber structure is continuous and dense.
Cooling: After forging, slow cooling or air cooling is performed according to process requirements to prevent cracks.
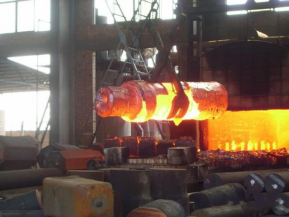
4. Cone shaft rough processing
Use lathes, milling machines and other equipment to perform preliminary processing on the forged blank to remove excess material and form parts close to the final shape.
Check whether the blank has obvious surface defects or dimensional deviations.
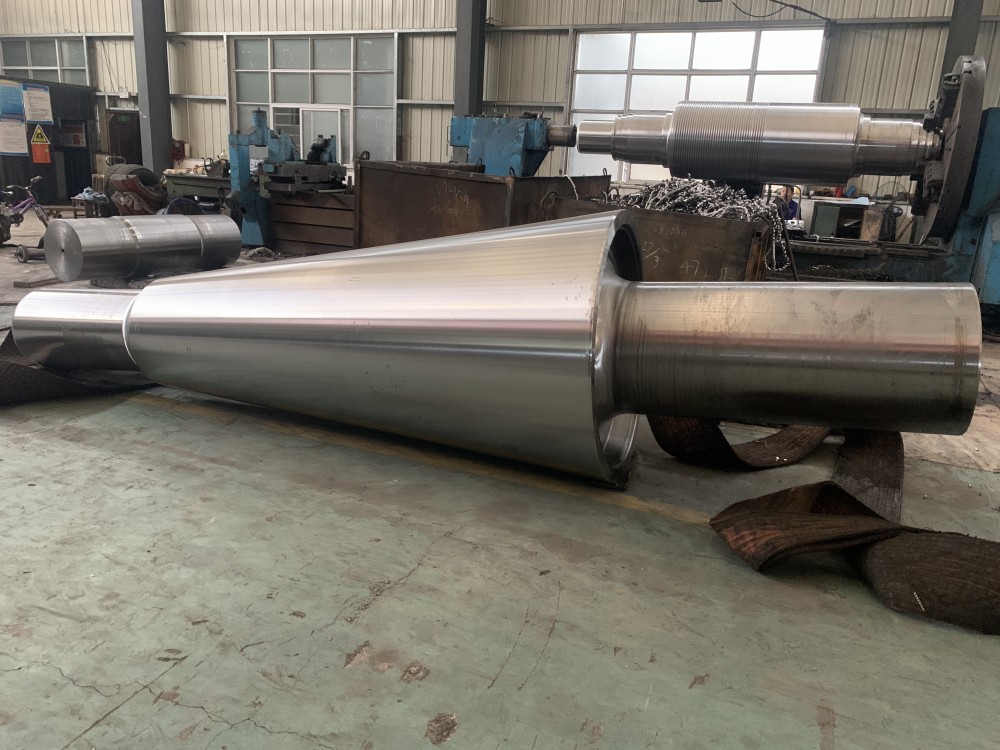
5. Cone shaft heat treatment
Normalizing: Eliminate the internal stress generated during the forging process and improve the cutting performance of the material.
Quenching and tempering treatment: Improve the overall strength and toughness of the main cone shaft through quenching and tempering processes.
Surface hardening treatment (optional): For parts that require high wear resistance, carburizing, nitriding or high-frequency quenching can be used to enhance the surface hardness.
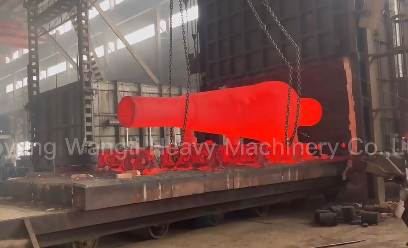
6. Cone shaft finishing
Use CNC machine tools to perform high-precision processing on the main cone shaft, including processing of key parts such as the outer circle, end face, and threaded holes.
Ensure that the dimensional tolerance and form and position tolerance of each part meet the design requirements.
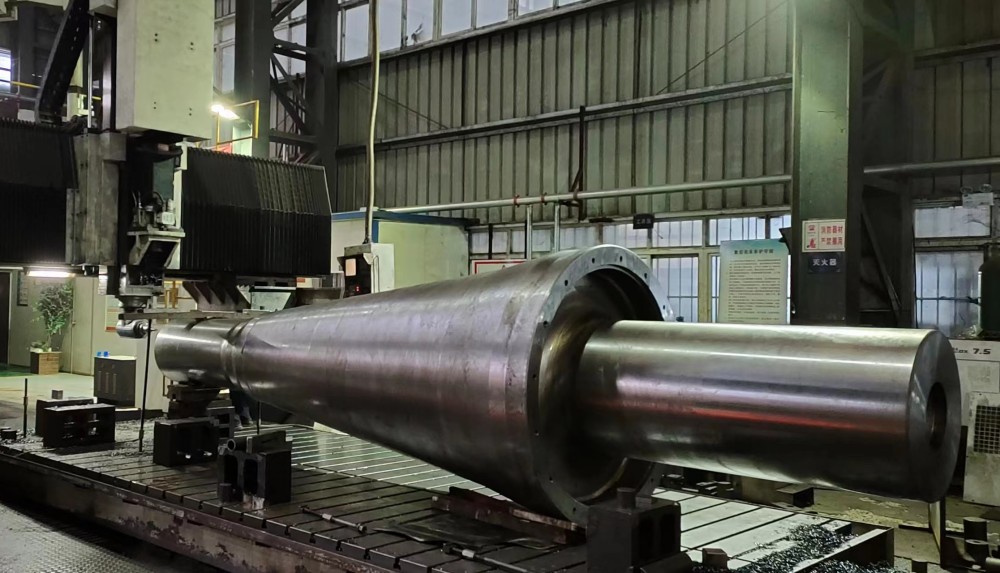
7. Cone shaft inspection and testing
Dimension inspection: Use tools such as three-coordinate measuring instruments and micrometers to inspect the key dimensions of the main cone shaft.
Non-destructive testing: Use magnetic particle testing, ultrasonic testing and other methods to check whether there are cracks or defects inside.
Hardness test: Test the hardness of the surface and core of the main cone shaft to ensure that the heat treatment effect meets the standard.
8. Cone shaft surface treatment
Prepare the main cone shaft for rust prevention, such as applying anti-rust oil or spraying protective coating to prevent rust during transportation and storage.
9. Cone shaft packaging
Package according to product appearance and customer requirements to prevent rust during transportation and storage.
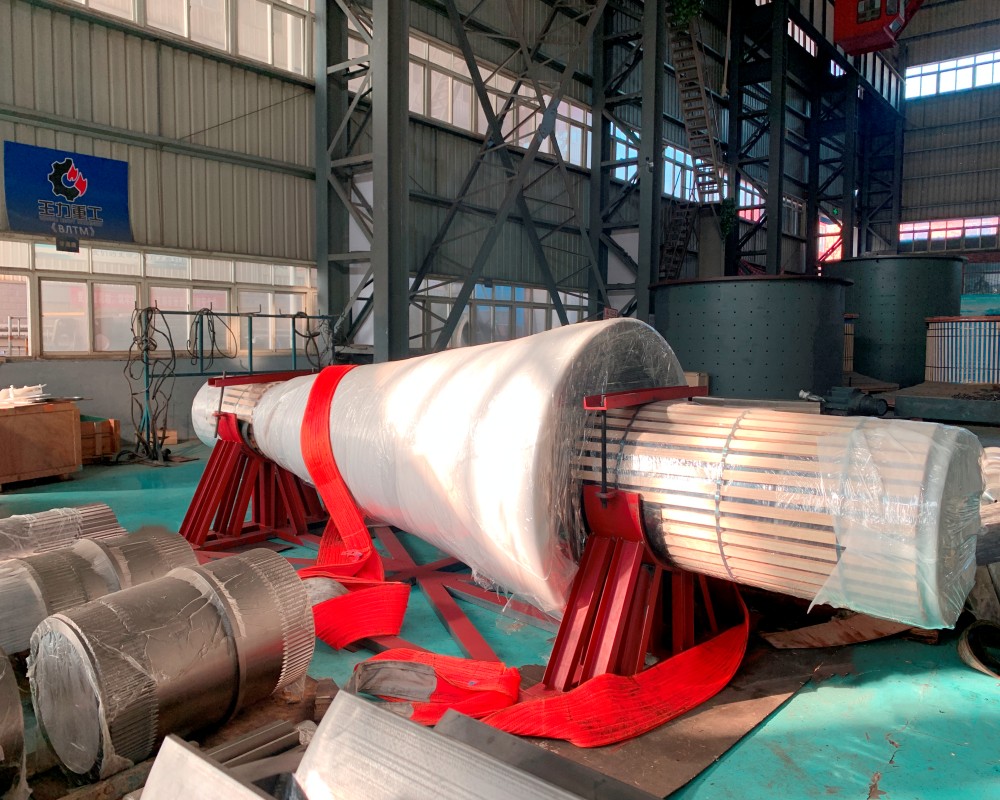
How to extend the service life of cone shaft Precautions
1. Avoid overload operation: The design load capacity of the main cone shaft is limited, and long-term overload operation will cause fatigue damage.
2. Prevent corrosion: When used in a humid or corrosive environment, anti-rust measures should be taken for the main cone shaft, such as applying a protective coating or regular cleaning.
3. Professional maintenance: For complex maintenance tasks, it is recommended to contact professional technicians or manufacturers for processing to avoid secondary damage caused by improper operation.
REQUEST A QUOTE
RELATED PRODUCTS
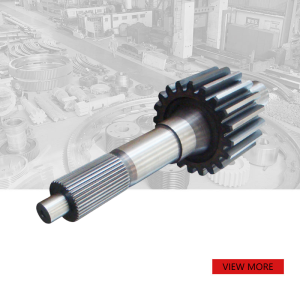
Spur gear shaft forging high quality large diameter for Ball Mill
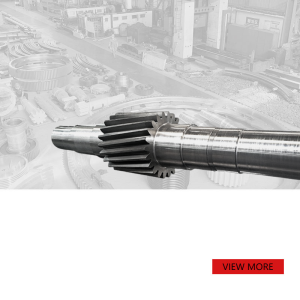
Custom mining forging long helical gear shaft
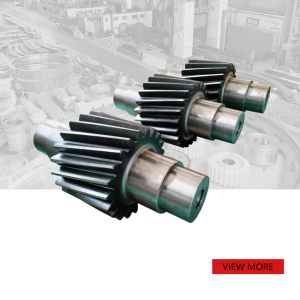
Custom forged 4140 steel helical gear shaft for ball mill
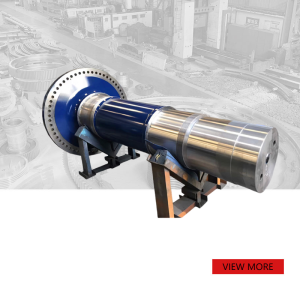
Non-standard alloy steel large diameter Fan Shaft
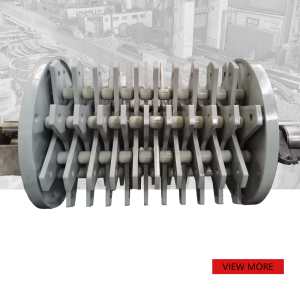
Customized hammer crusher long service life wear resistant rotor shaft
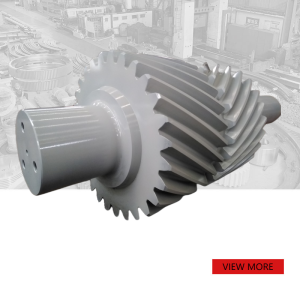