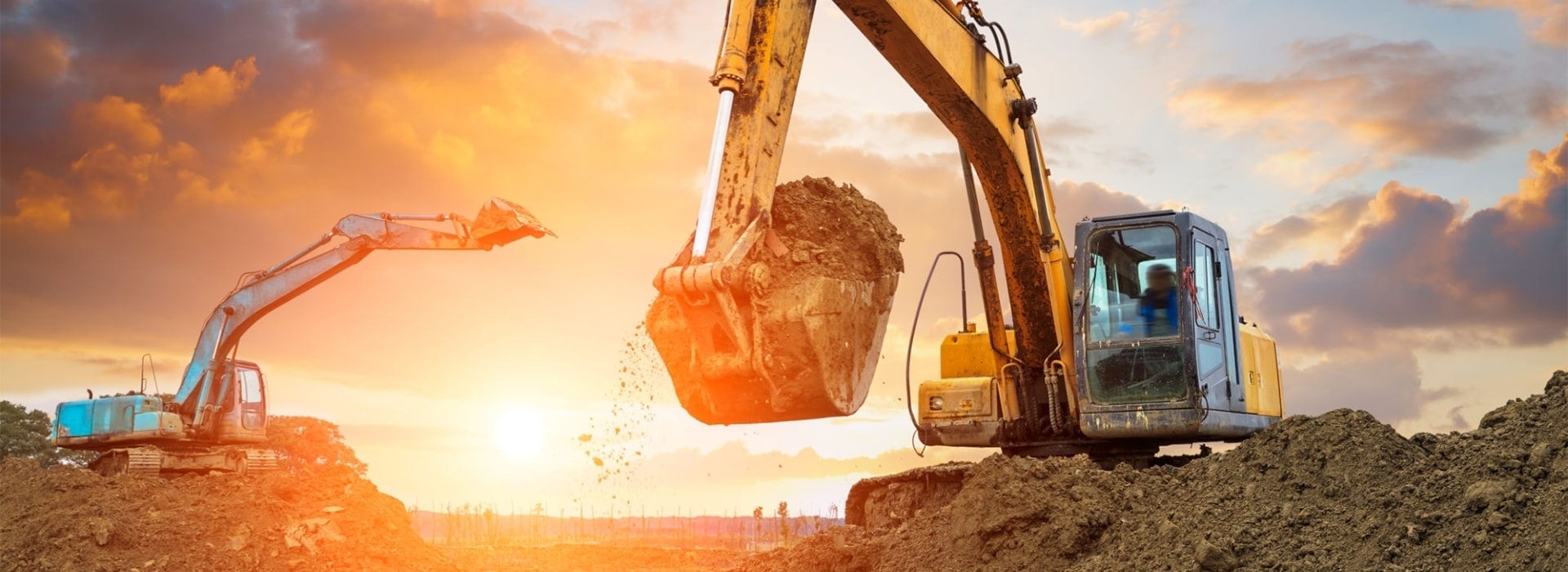
Custom mining forging long helical gear shaft
PRODUCT PARAMETERS
Description
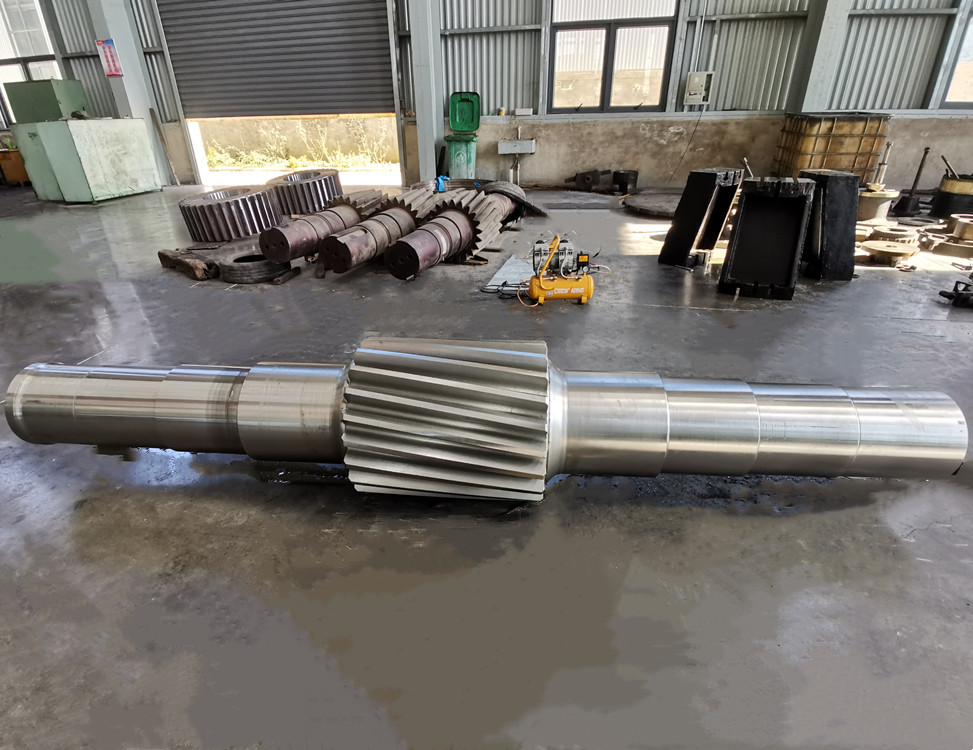
Overview of Helical Gear Shaft
A Helical Gear Shaft is a key component in a mechanical transmission system that transmits motion and torque by one or more pairs of helical teeth meshing with each other. Compared with spur gears, helical gears have smoother running characteristics and higher load carrying capacity.
Production process of Helical Gear
blank forging
The production of helical gear shafts begins first with blank forging, which is the basic step of the manufacturing process. After heating the metal raw material to the right temperature, the metal is formed into a preliminary shape using a forging hammer or press, a process designed to ensure tight, uniform internal organization of the material and reduce potential defects. In the forging process, the appropriate mold is selected for pressing according to the design requirements to form the outline of the final product. The key of this stage is to control the forging temperature and deformation degree to ensure that the material obtains good mechanical properties. The blank after forging is usually cooled for subsequent processing.
Roughing
Roughing is the second step in helical gear shaft manufacturing, the main purpose of which is to remove excess material and bring the workpiece close to its final dimensions. This step is usually performed using machine tools such as lathes and milling machines, and the focus is on efficiently cutting large amounts of material while ensuring a certain degree of machining accuracy. In roughing, the operator will cut, drill and preliminary shape the blank according to the design drawings, although the accuracy requirements are not as strict as the finishing at this time, but must ensure that the subsequent process has enough margin. In addition, roughing can also help to find possible internal defects and adjust the production process in time.
Finishing
Finishing is the process of making accurate size and shape corrections to the helical gear shaft in order to achieve the tolerances specified in the design. This step uses high-precision CNC machine tools, such as grinding machines, gear hobbing machines, etc., to fine grind and trim the surface of the parts. Especially for the helical gear part, special equipment is needed to ensure that the tooth shape is accurate and improve the meshing efficiency. Finishing focuses not only on dimensional accuracy, but also on surface finish, as this is essential to reduce noise and extend service life. Upon completion of this phase, the part should meet all technical specifications and be ready to enter the heat treatment process.
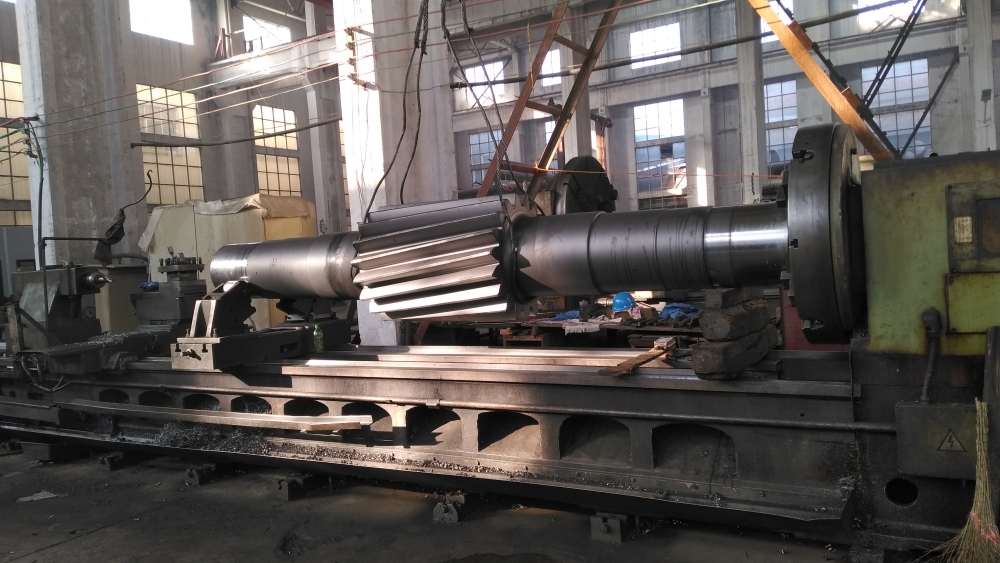
Heat treatment
Heat treatment is a key step to improve the mechanical properties of helical gear shaft, including quenching, tempering and other processes. First, the part is heated to a specific temperature and then rapidly cooled (quenched) to increase the hardness; Next, tempering is performed at lower temperatures to restore toughness and reduce internal stress. Heat treatment can not only significantly improve the wear resistance and strength of the material, but also optimize its microstructure. Throughout the process, precise control of temperature and time parameters is essential to ensure that each part is treated evenly and effectively, thus guaranteeing excellent overall performance of the finished product.
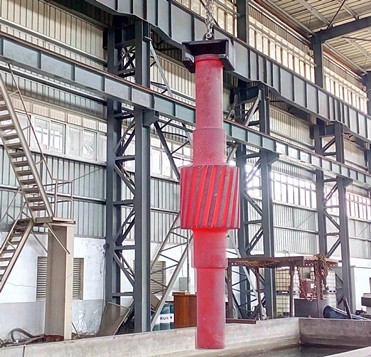
Surface treatment
The final step is surface treatment, which involves a variety of technical means, such as coating, coating or chemical treatment, to protect the helical gear shaft from corrosion and wear. Common surface treatment methods include chromium plating, nitriding and phosphating, which can effectively increase the surface hardness and corrosion resistance. In addition, some special applications may require special surface modifications, such as lubricating coatings to reduce the coefficient of friction and improve operating efficiency. The surface treatment not only improves the appearance quality of the parts, but more importantly, enhances its durability and reliability, ensuring long-term stable work performance.
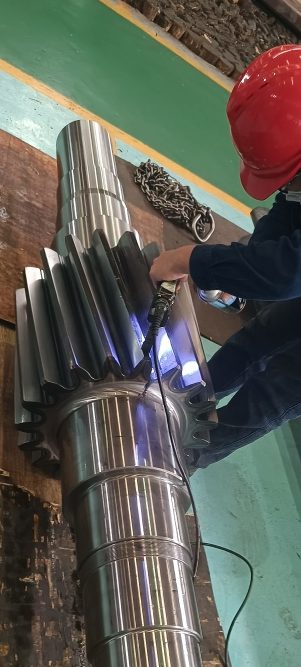
Application of helical gear shaft in mining machinery
1.Mine excavator
-Slewing support: The slewing support between the excavator chassis and the superstructure is also often a helical gear shaft, allowing the machine to rotate 360 degrees in all directions, improving the flexibility of operation.
- Crusher drive: The main shaft and eccentric shaft inside the jaw crusher, cone crusher and other equipment are usually driven by helical gear shafts, which are responsible for converting the power of the motor into the reciprocating or rotating motion required for crushing parts.
Package of Helical Gear Shaft
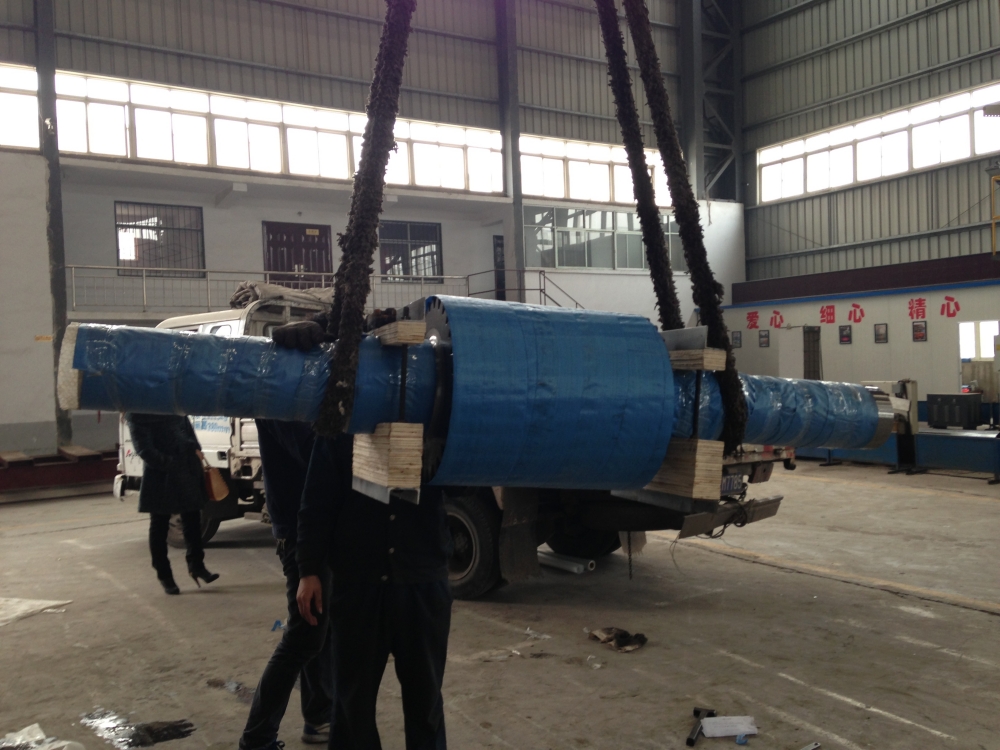
The internal liner or bracket is customized according to the specific size of the helical gear shaft to ensure that the gear shaft will not move in the case and reduce the damage caused by vibration. It is then placed in a custom fumigation-free plywood box.
FAQs of Helical Gear Shaft
-What parameters should I consider when choosing a helical gear shaft?
-The following parameters are mainly considered: modulus, number of teeth, spiral Angle, pressure Angle, outside diameter, inside diameter, width, center distance, transmission ratio, maximum torque, allowable speed, bearing capacity, material hardness, surface treatment, etc. Make sure these parameters meet your specific needs and specifications.
-How do I find the right helical gear shaft for my application?
-It is best to consult a professional supplier or manufacturer to provide detailed application information (such as working conditions, required power, speed range, etc.), and they can recommend the most suitable product according to your needs. In addition, looking at product catalogs and technical manuals are also good sources of reference.
-What are the price factors of helical gear shaft?
-The price is affected by a number of factors, including material type, manufacturing process, size, accuracy level, special coating or treatment. In general, high-quality, high-performance helical gear shafts are relatively expensive, but can reduce maintenance costs and extend service life in the long run.