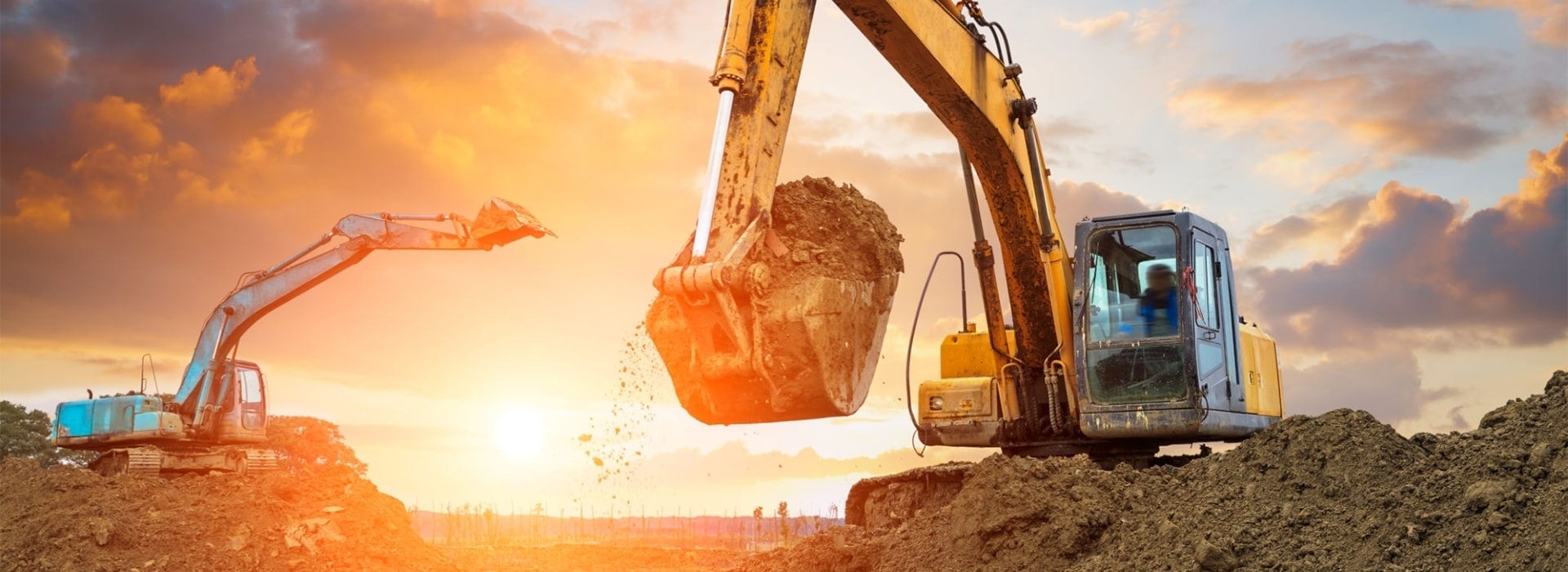
forging double helical gear shaft
PRODUCT PARAMETERS
Description
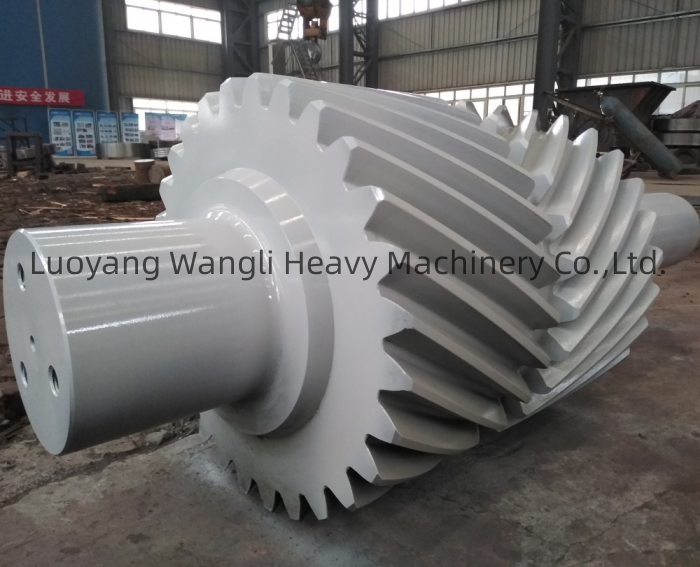
main processing steps:
1: Forging
Pre-forging: The billet is preliminarily formed by free forging or die forging to form a blank close to the final shape. Pre-forging can reduce the deformation of subsequent fine forging and improve production efficiency.
Fine forging: Use precision dies for final forging to make the shape and size of the gear shaft more precise. During the precision forging process, the pressure, speed and die accuracy need to be strictly controlled to ensure that the geometric shape and dimensional tolerance of the gear shaft meet the design requirements.
Correction: For the deformation that may occur after forging, the correction process can be adjusted to ensure the straightness and coaxiality of the gear shaft.
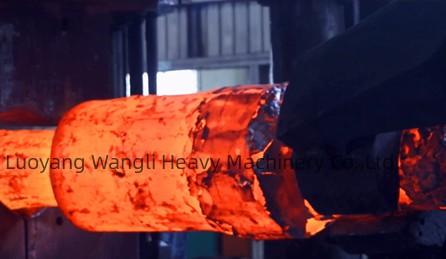
2:Rough machining
Use lathes, milling machines and other machine tools to rough-machine the gear shaft to remove excess material and prepare for subsequent finishing. Rough machining includes turning the outer circle, end face, keyway, etc.
3:Heat treatment
Normalizing or annealing: In order to eliminate forging stress and improve the cutting performance of the material, normalizing or annealing is usually required.
Quenching and tempering treatment: For gear shafts with high strength requirements, quenching and tempering treatment (quenching + high temperature tempering) is usually required to obtain good comprehensive mechanical properties (such as hardness, toughness, wear resistance, etc.).
Surface hardening: In order to improve the wear resistance and fatigue resistance of the gear tooth surface, surface hardening treatments such as induction quenching and nitriding can be used.
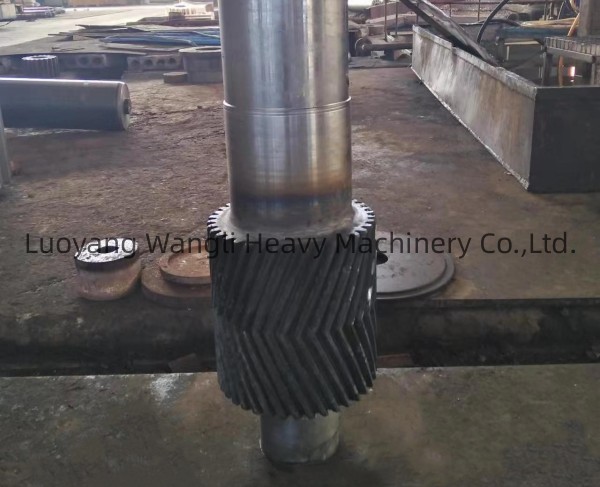
4:Gear machining
Gear hobbing: Gear hobbing is one of the most commonly used gear machining methods. During the gear hobbing process, the tool parameters and feed speed need to be precisely controlled to ensure the gear tooth profile accuracy.
Gear shaving: In order to improve the gear tooth profile accuracy and surface finish, gear shaving can be performed. Gear shaving is a fine correction process that can effectively improve the meshing quality of gears.
Gear grinding: For gears with high precision requirements, gear grinding may be required to achieve higher tooth profile accuracy and surface roughness requirements.
5:Finishing
Finishing other parts of the gear shaft (such as journals, bearing seats, etc.) to ensure their dimensional accuracy and surface quality. Finishing usually includes grinding, honing and other processes.
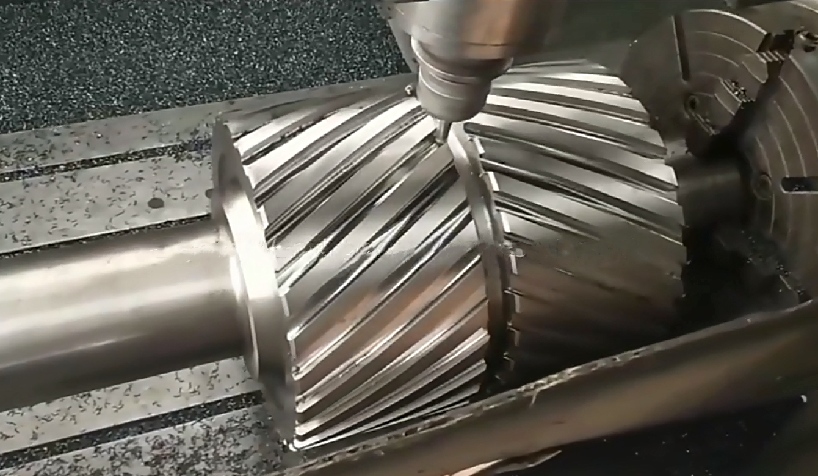
6:Inspection
The finished gear shaft is subjected to comprehensive quality inspection, including dimensional tolerance, shape tolerance, surface roughness, hardness, metallographic structure and other aspects. Ensure that the product meets the requirements of the design drawings and technical standards.
7:Painting and packaging
Finally, the gear shaft is rust-proofed and painted, and then packaged according to customer requirements and ready for shipment.
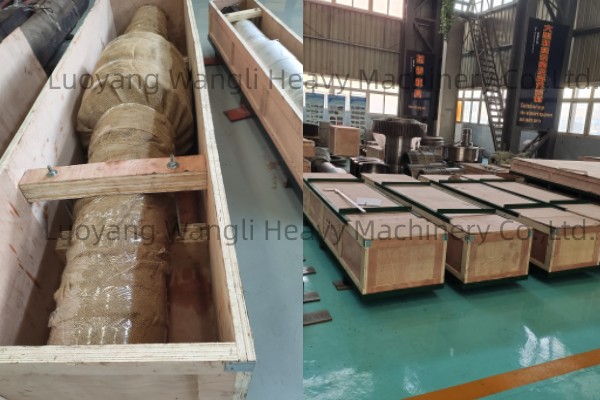
Common materials and characteristics of herringbone gear shafts:
1: Alloy steel (such as 42CrMo, 40CrNiMo, 20CrMnTi, etc.) Advantages: high strength, high toughness, good hardenability and wear resistance, suitable for heavy-load and high-speed applications. Application: widely used in mining machinery, metallurgical equipment, engineering machinery and other fields.
2: Carburizing steel (such as 20CrMnTi, 20CrMnMo, etc.) Advantages: high surface hardness, good core toughness, suitable for surface hardening treatment. Application: automotive, aerospace, precision transmission systems and other fields with high requirements for wear resistance and toughness.
3: Cast steel or cast iron. Advantages: easy molding, low cost, suitable for casting large gear shafts. Application: large machinery and equipment, heavy-duty reducers, etc.
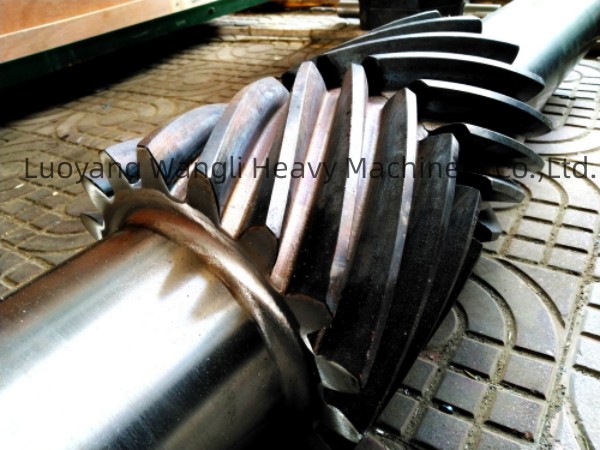
Some common problems and solutions of herringbone gear shafts:
1: Gear tooth surface wear
Problem: Long-term operation or poor lubrication may cause gear tooth surface wear, affecting transmission efficiency and precision, and even cause gear failure in severe cases.
Solution:
Improve lubrication conditions: Ensure that there is enough lubricating oil in the gearbox, check the oil level and oil quality regularly, and replace the lubricating oil when necessary.
Select wear-resistant materials: Select materials with good wear resistance (such as carburized steel) and perform surface hardening treatment (such as induction hardening).
Optimize tooth surface contact: Optimize the tooth surface contact area and reduce local stress concentration by adjusting the modulus, pressure angle and tooth width of the gear.
2: Gear shaft fracture
Problem: The gear shaft may break when subjected to large loads or impacts, especially after fatigue damage accumulates to a certain extent.
Solution:
Improve material strength: Select high-strength and high-toughness materials (such as 42CrMo, 20CrMnTi, etc.), and improve the comprehensive mechanical properties of the material through quenching and tempering.
Optimize structural design: Avoid stress concentration areas (such as keyways, threaded holes, etc.), use fillet transitions or add reinforcing ribs.
Regular inspection and maintenance: Regularly perform non-destructive testing (such as ultrasonic testing and magnetic particle testing) on the gear shaft to detect potential cracks or defects in a timely manner.
3: Gear noise and vibration
Problem: Gears may produce abnormal noise and vibration during operation, affecting the stability and service life of the equipment.
Solution:
Improve gear accuracy: Ensure that the gear tooth shape, pitch and tooth thickness accuracy meet the standards and reduce meshing errors.
Optimize gear pairing: Select a suitable gear pair to ensure that the tooth shape and tooth surface quality of the two gears are well matched to avoid excessive or too small gaps between teeth.
Adjust the transmission ratio and speed: Select the transmission ratio and speed reasonably to avoid resonant frequency and reduce vibration sources.
Use vibration reduction devices: such as elastic couplings, vibration reduction pads, etc. to absorb and reduce vibration.
Our advantage: From raw material control, strict control of each process
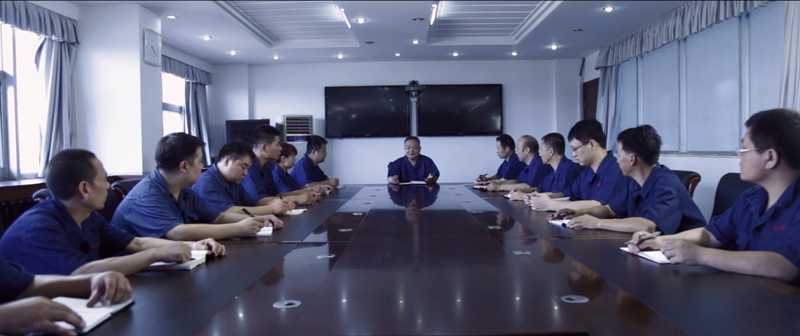
一、In Design
- 1. 40+ years of professional experience in producing large modulus gear / gear shaft, capable of providing rationalization suggestions or improvement programs;
- 2. Capable of providing site mapping and gear design;
二、In terms of Raw Material Control
- 1. Use refining furnace and other methods to reduce the content of sulfur, phosphorus, oxygen, hydrogen and other impurities;
- 2. Forging ratio > 5, higher than the international standard;
- 3. Provide raw materials according to European and American standards;
三、Excellent Heat Treatment Equipment & Supporting Equipment
- 1. The vertical type electric furnace is used for heat treatment (German temperature control system, furnace temperature ±1℃; Four kinds of quenching media can meet different quenching needs);
- 2. The heat treatment workshop is close to the processing workshop, which make it more convenient for timely stress relief annealing of the workpiece;
四、Special processes for Key Points: Coarse tooth before quenching and tempering
五、Inspection of Control Points
- 1. ultrasonic detection;
- 2. Magnetic particle detection was carried out on the tooth surface
六、Customized Products to Meet customer’s Required
- According to the different needs of users, gear surface quenching, carburizing, nitriding treatment can be carried out.
REQUEST A QUOTE
RELATED PRODUCTS
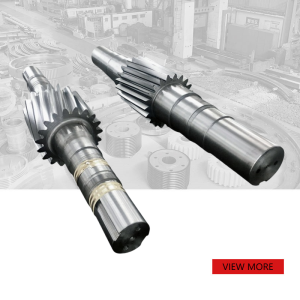
Mining custom forging large module helical gear shaft
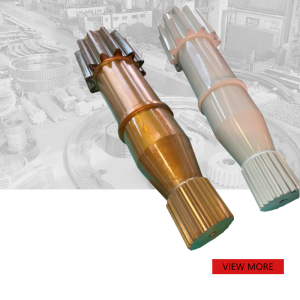
Custom forged 42CrMo large modulus gear shaft
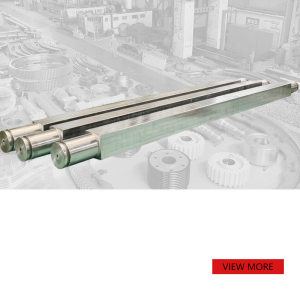
Customized Large Forging shaft for dragline/Walking excavator
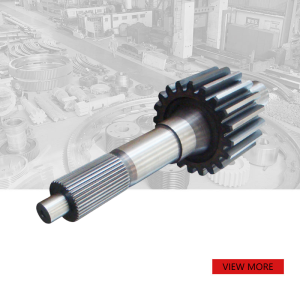
Spur gear shaft forging high quality large diameter for Ball Mill
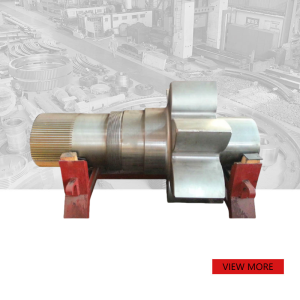
4340 OEM Big Pinion Shaft Spur Toothed Forging Carbon Steel Spur Large Module Gear Shaft
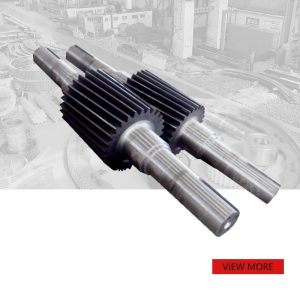