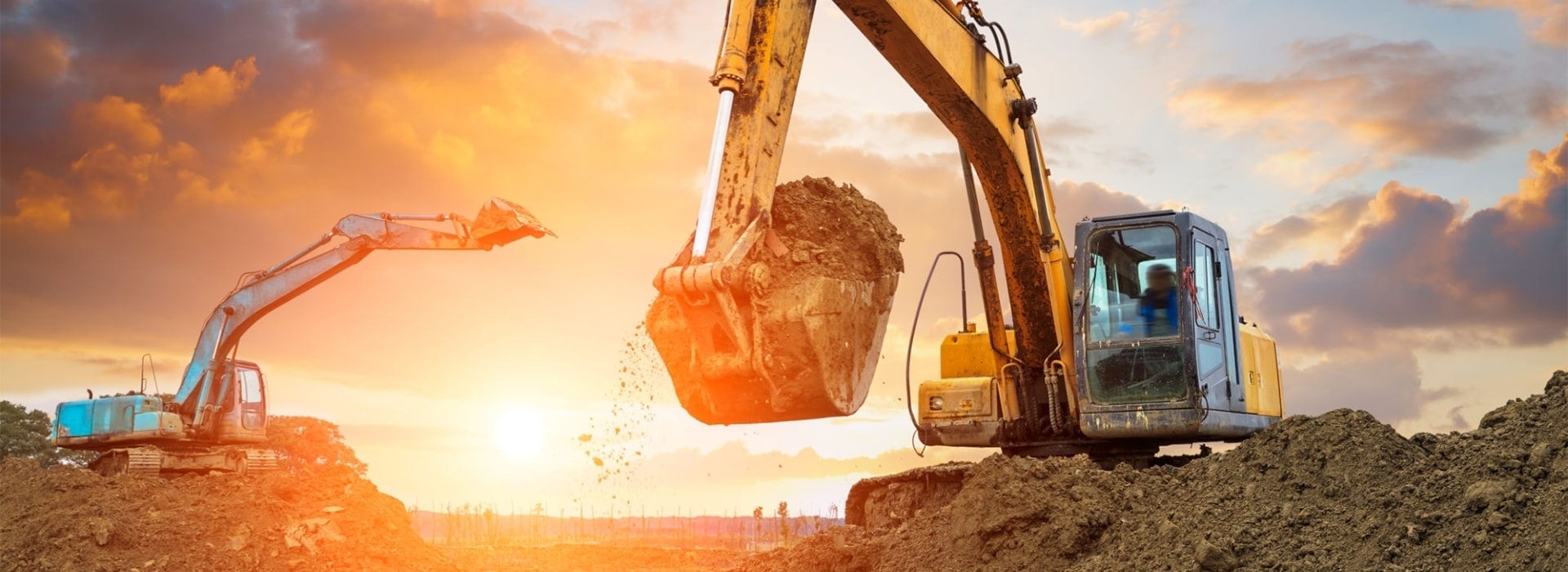
Large dimater wear-resistant forging Scraper conveyer sprocket shaft
PRODUCT PARAMETERS
Description
一.Overview
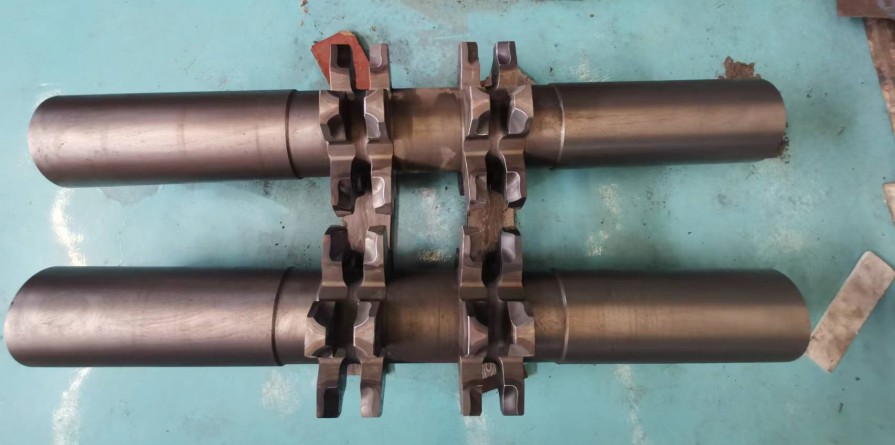
The main function of the sprocket shaft of the scraper conveyor is to drive the operation of the entire conveying system. The sprocket is fixed on the shaft and rotates through the power provided by the motor or engine to drive the chain and the scraper connected to it to move, so as to achieve continuous conveying of materials. Sprocket shafts are designed with high strength and wear resistance to withstand high torque and tension, ensuring stable operation under heavy load conditions. In addition, a reasonable shaft design can effectively reduce energy loss, improve transmission efficiency, and help reduce maintenance costs to ensure the smooth progress of production.
二.Features
1. High strength and wear resistance
2. Precise machining accuracy
3. Good fatigue resistance
4. Anti-corrosion treatment
三.Production process
1.Forging
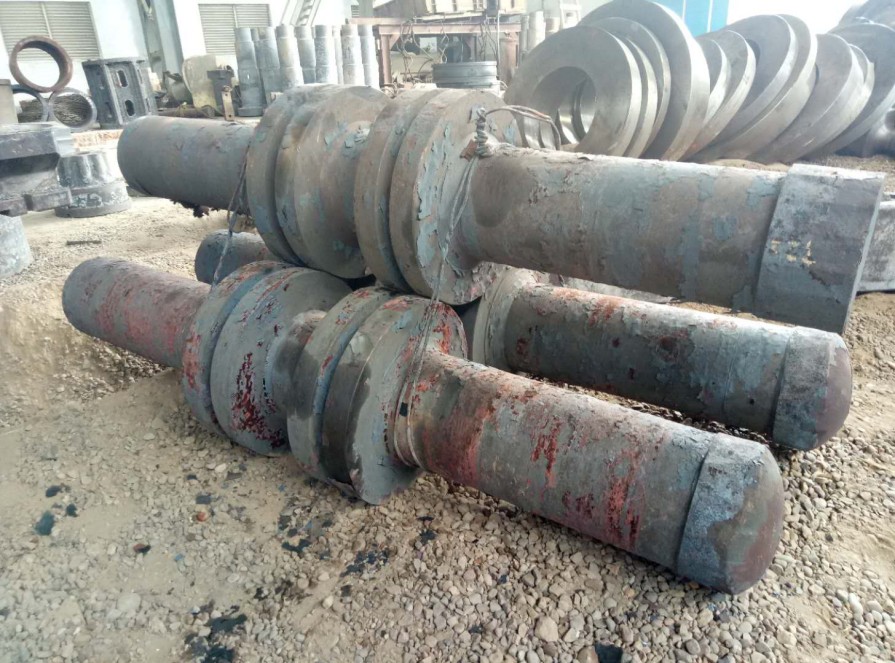
Sprocket shaft using forgings can enhance its strength and wear resistance, improve the internal structure of the metal through forging, improve the fatigue resistance and load capacity, and ensure stable operation under high load. Forgings also guarantee higher dimensional accuracy and surface quality, reduce subsequent processing costs, extend service life, and adapt to harsh working environments.
2.Rough machining
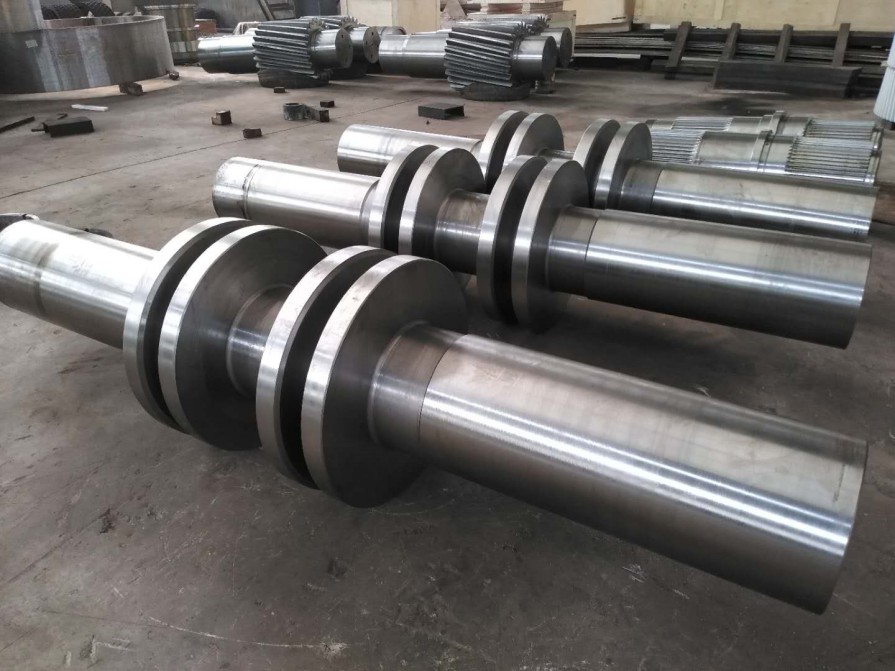
The main purpose of roughing the forged sprocket shaft is to preliminary form, remove excess material and prepare for subsequent finishing. This step helps to expose potential internal defects and ensure part quality while reducing the effort and cost of finishing. Roughing can also check the match between the design and the actual production, ensure that the dimensional accuracy and mechanical properties of the final product meet the requirements, and improve production efficiency.
3.Heat treatment
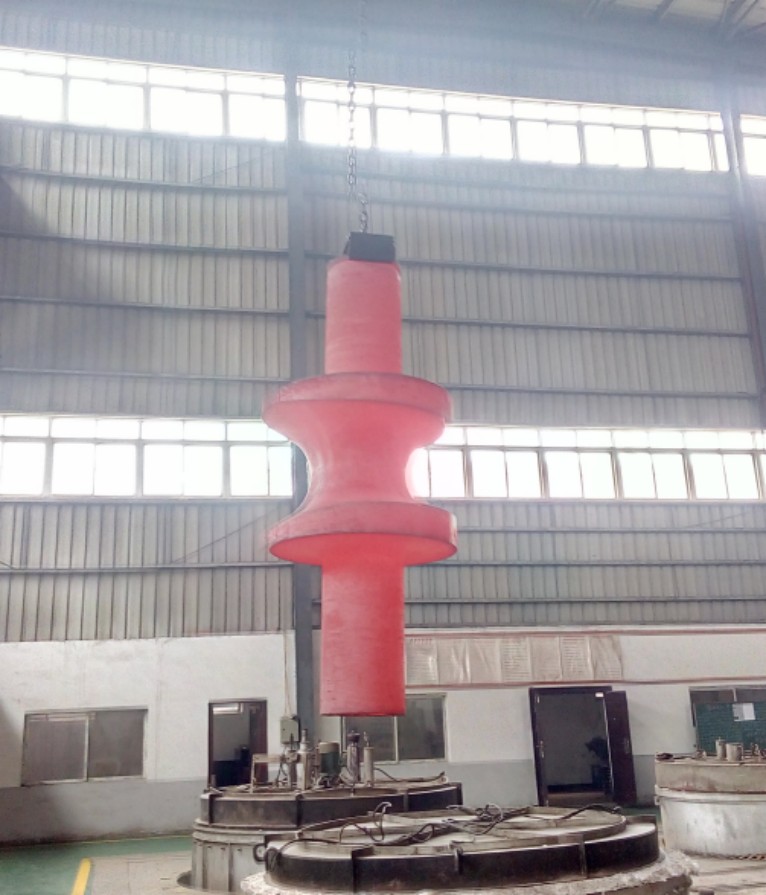
Heat treatment is a key procedure in the whole production process. Our company be honored with the large mold heat treatment engineering technology center of Luoyang city.Our heat treatment workshop has 6 sets of electric furnace, the deepest one is 9 meters, the largest one diameter is 5.5 meters, the crane 50 tons, and our workshop bearing capacity can reach 100 tons.
4.Finished-machining
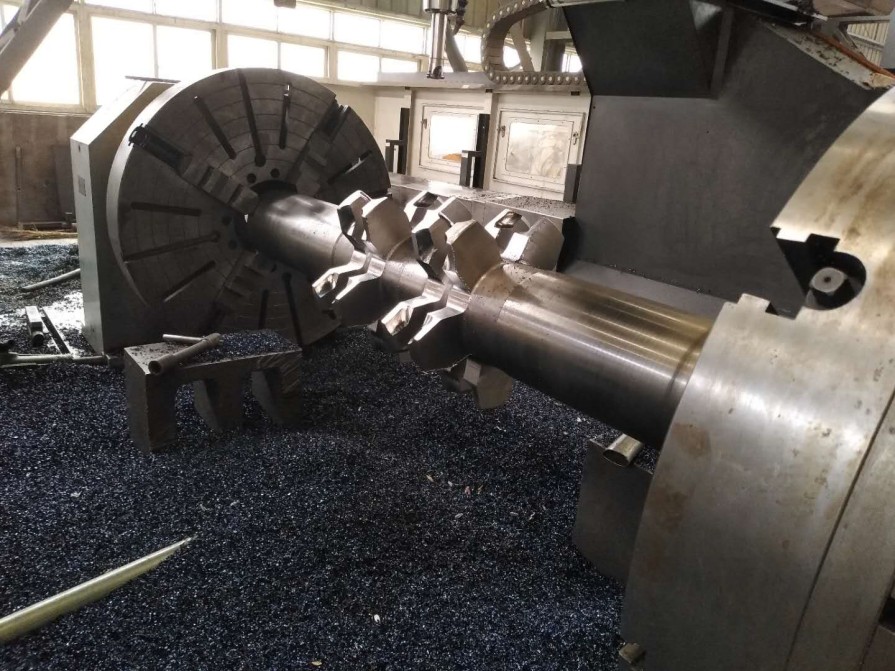
Finishing the forged sprocket shaft ensures that it meets the exact size and surface finish requirements, improves the accuracy of the sprocket fit, and reduces wear and noise during operation. Finishing can also eliminate the minor defects left by rough machining, enhance the mechanical properties and fatigue strength of parts, ensure stable operation under high load conditions, extend service life, and improve the operating efficiency and safety of the entire equipment
5.Test
The inspection of the finished forged sprocket shaft includes: dimensional accuracy inspection to ensure that it meets the design requirements; Surface quality inspection to identify any defects or defects; Hardness test to verify material strength and wear resistance; Non-destructive testing to detect internal potential cracks; Mechanical performance tests evaluate tensile, impact and other characteristics to ensure high quality and reliability of parts.
6.Package
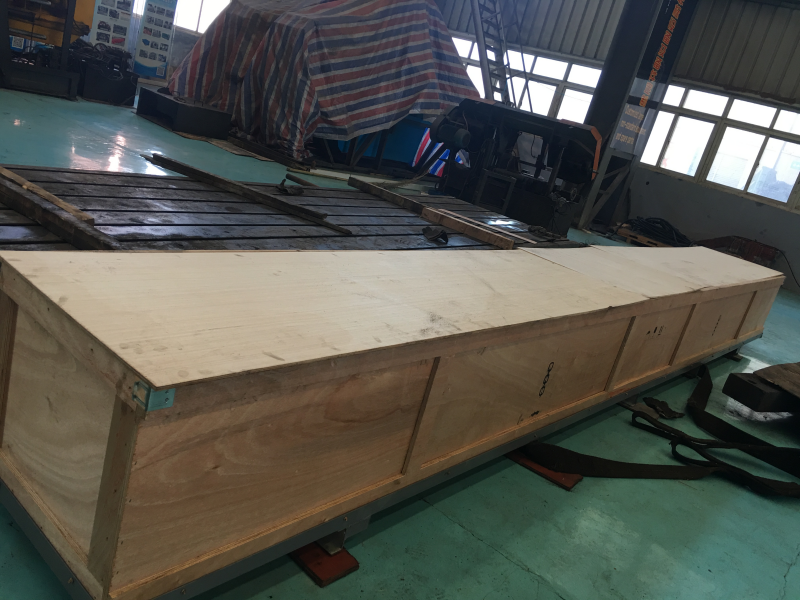
The export packaging of forged sprocket shafts prevents damage in transit, avoids corrosion, ensures that part accuracy and quality are not affected, and facilitates loading and unloading, thus guaranteeing customer satisfaction and maintaining the manufacturer’s international reputation.
四.FAQ
1. Can you produce the spline shaft?–Yes
2. Can you produce the sprocket wheel? –YES
3. What kind of payment terms do you have? –T/T & L/C
REQUEST A QUOTE
RELATED PRODUCTS
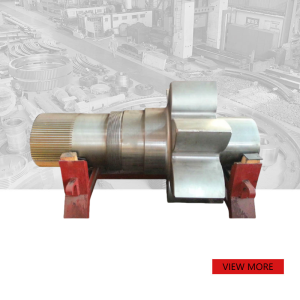
4340 OEM Big Pinion Shaft Spur Toothed Forging Carbon Steel Spur Large Module Gear Shaft
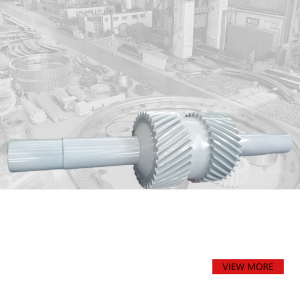
Non-standard alloy steel large Double helical gear shaft with cutting groove
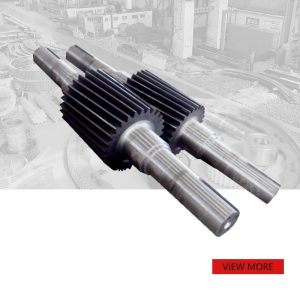
Custom forged steel large helical gear shaft
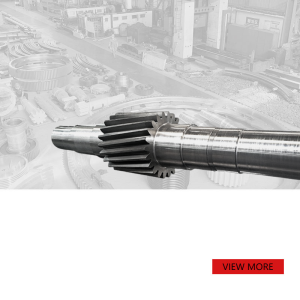
Custom mining forging long helical gear shaft
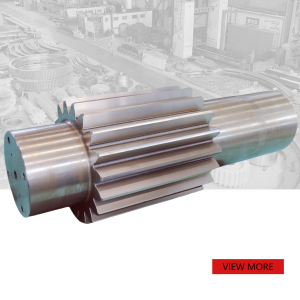
Customized non-standard Large module gear shaft transimission parts
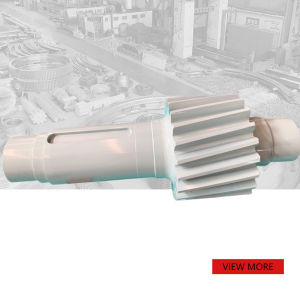