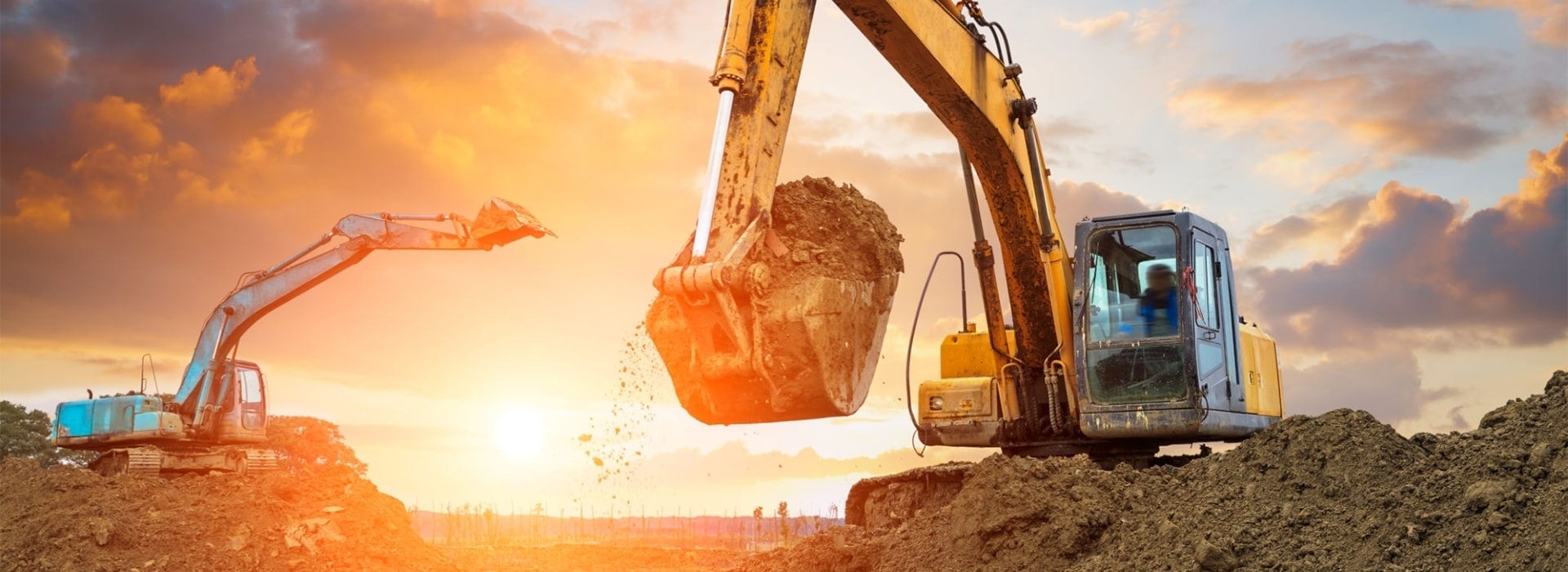
Mining custom casting large helical gear shaft assembly
PRODUCT PARAMETERS
Description
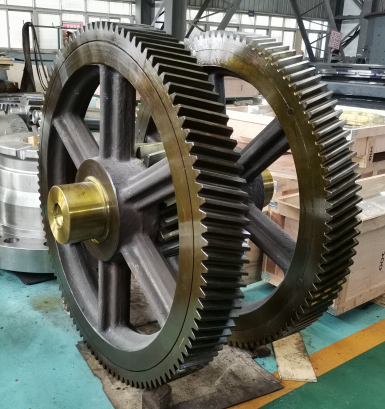
Helical gear and forging shaft assembly production process
1.Material Selection:
Selection of appropriate steel alloy for casting and forging based on strength, durability, and other performance criteria.
2.Casting Process:
Preparation of the casting mold using sand or other suitable materials.
Melting of the selected steel alloy in a furnace.
Pouring the molten steel into the prepared mold.
Cooling and solidification of the cast part.
Removal of the cast part from the mold.
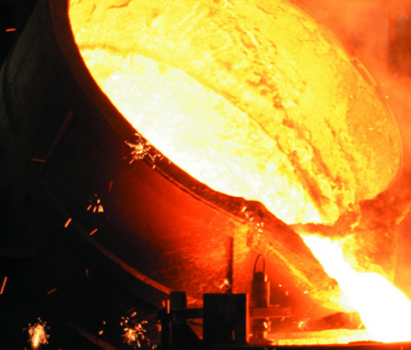
3.Forging Process:
Heating the steel to the forging temperature.
Shaping the steel using forging equipment (hammers, presses, etc.) to achieve the desired shape.
Cooling and finishing the forged part.
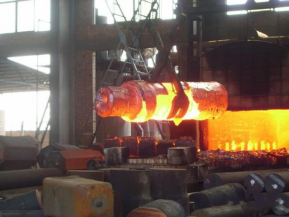
4.Machining:
Rough machining to remove excess material and achieve the basic shape.
Precision machining to create the helical gear teeth and other critical features.
Machining of the shaft to ensure proper fit and alignment with the gear.
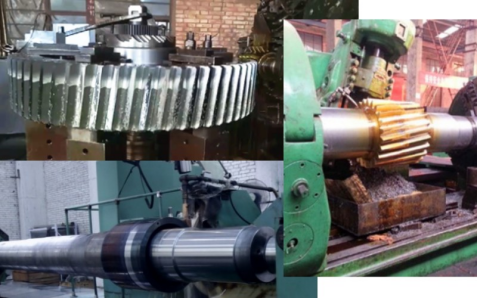
5.Heat Treatment:
Heat treatment processes such as annealing, normalizing, quenching, and tempering to improve the mechanical properties of the steel.
Stress relief to prevent warping during subsequent operations.
6.Surface Treatment:
Surface treatments such as carburizing, nitriding, or hardening to increase wear resistance and surface hardness.
Coating or plating if required for corrosion resistance or other specific properties.
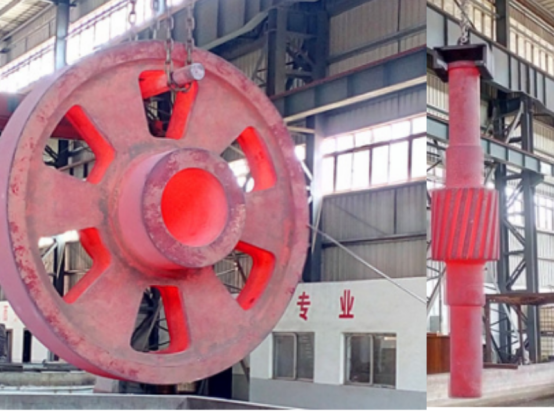
7.Assembly:
Assembly of the gear and shaft using appropriate fasteners or press-fit techniques.
Balancing and alignment checks to ensure smooth operation.
8.Quality Control:
Inspection of the final assembly for dimensional accuracy, surface finish, and overall quality.
Non-destructive testing (NDT) methods such as ultrasonic testing, magnetic particle inspection, or dye penetrant inspection to check for internal defects.
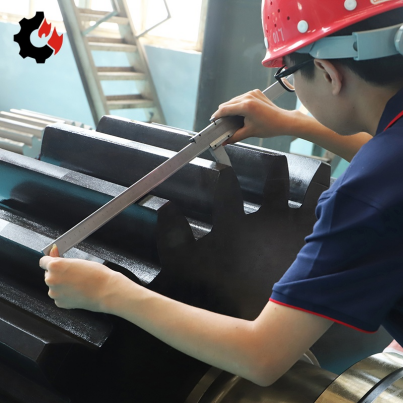
9.Packaging and Shipping:
Proper packaging to protect the assembly during transportation.
Documentation of the product specifications and test results.
Maintenance classification, how to maintain?
(1) Daily maintenance
Performed every day or before each startup.
Contents: Check lubricant status, surface cleaning, fastener inspection, vibration and noise monitoring.
(2) Periodic maintenance
Scheduled according to operating time and cycle.
Contents: Lubrication system replacement, wear detection, clearance measurement, balance correction.
(3) Preventive maintenance
Perform comprehensive inspection and maintenance of equipment on a regular basis.
Contents: Deep cleaning, performance testing, parts replacement (such as bearings, seals).
(4) Predictive maintenance
Use sensors and data analysis technology to monitor equipment status.
Contents: Vibration analysis, temperature monitoring, wear prediction.
(5) Emergency maintenance
Quickly respond to and repair sudden failures.