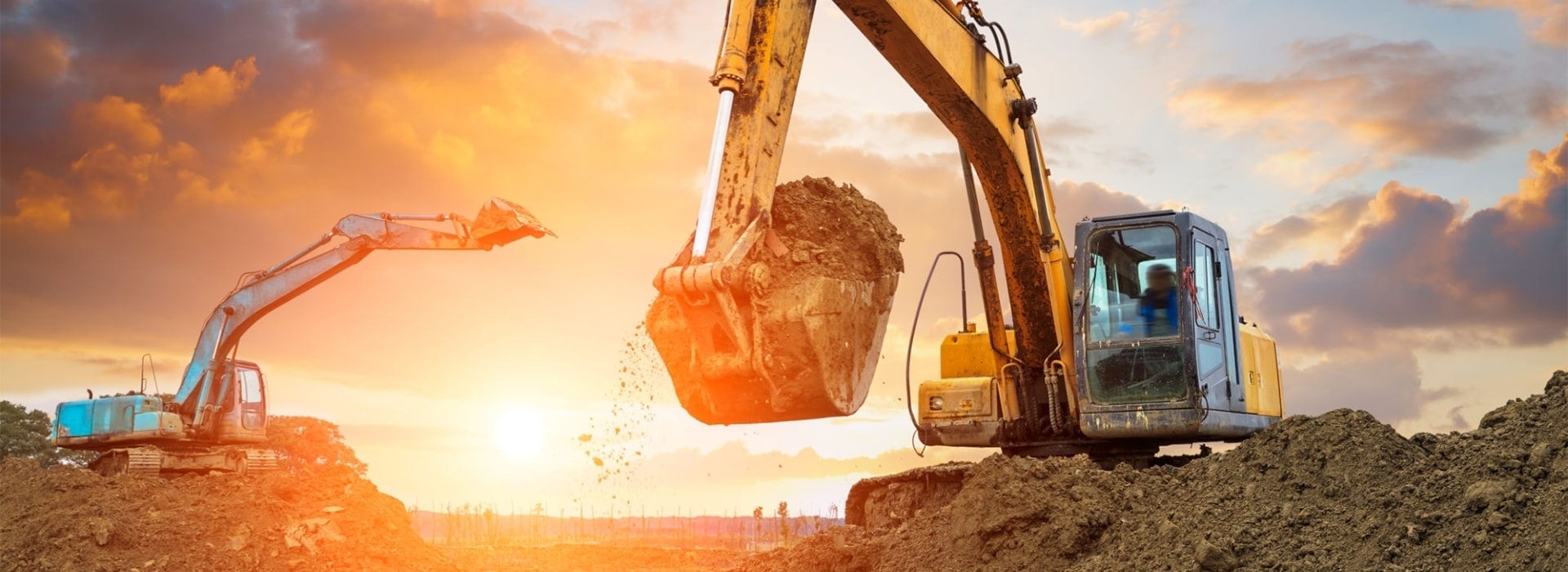
Mining Forging 34XH3M large module spur gear shaft
PRODUCT PARAMETERS
Description
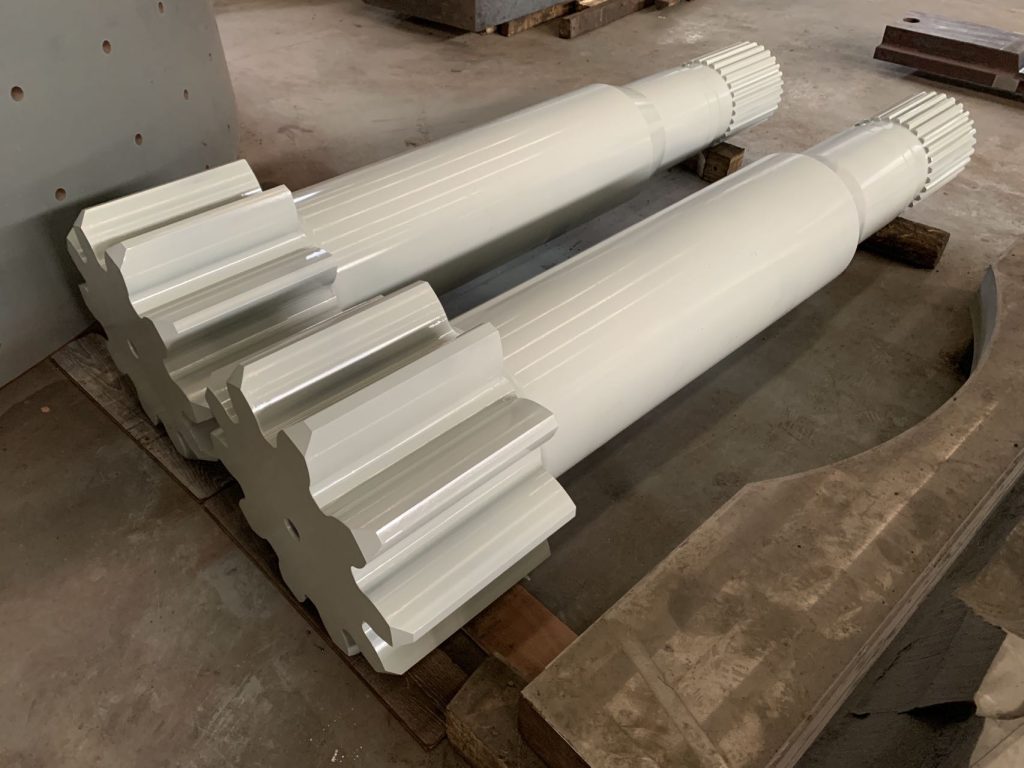
Spur Gear Shaft Production Process
1. Blank preparation
Use 34XH3M steel to forge the blank, free forging, annealing after forging, eliminate internal stress and improve mechanical properties.
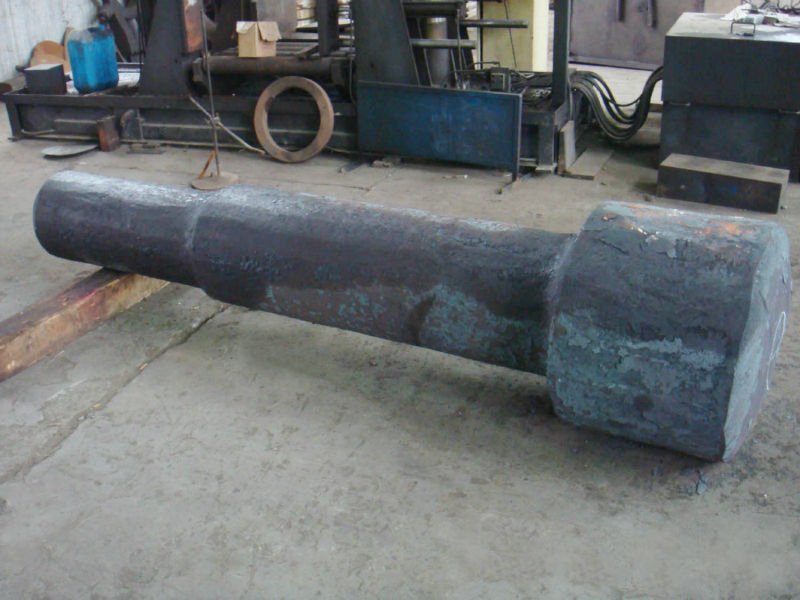
2. Rough machining
(1). Turning the outer circle and end face
Rough turning the outer circle and end face of the spur gear shaft on the lathe to form a preliminary shape.
Machining the center hole or other positioning reference.
(2). Drilling and tapping
Drill out the mounting hole, keyway hole and other auxiliary holes.
Tap or process threaded holes.
(3). Milling keyway
Use a milling machine to process the keyway on the spur gear shaft to ensure the size accuracy and position accuracy of the keyway.
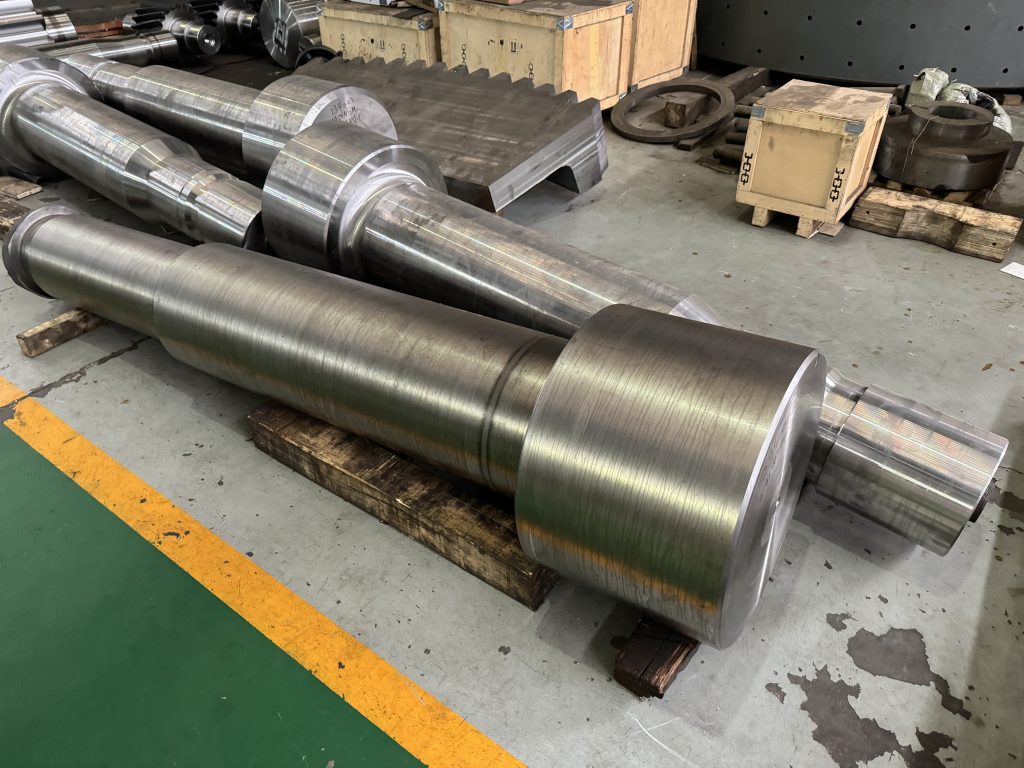
3. Tooth processing
(1). Hobbing
Hobbing: Suitable for tooth processing of most spur gear shafts, high efficiency and suitable for mass production. Ensure that the tooth profile accuracy meets the design requirements.
4. Heat treatment
(1). Surface hardening
Carburizing and quenching: Suitable for high load conditions, carburizing makes the tooth surface hardness reach HRC58~62, and the core maintains toughness.
Carburizing temperature: about 920~950℃.
Quenching cooling medium: oil cooling or graded quenching.
High frequency quenching: local heating of the tooth surface, rapid cooling to obtain a high hardness tooth surface.
Quenching temperature: about 860~900℃.
Cooling method: water cooling or oil cooling.
(2). Tempering
After heat treatment, low temperature tempering (about 150~200℃) is performed to eliminate internal stress and stabilize the structure.
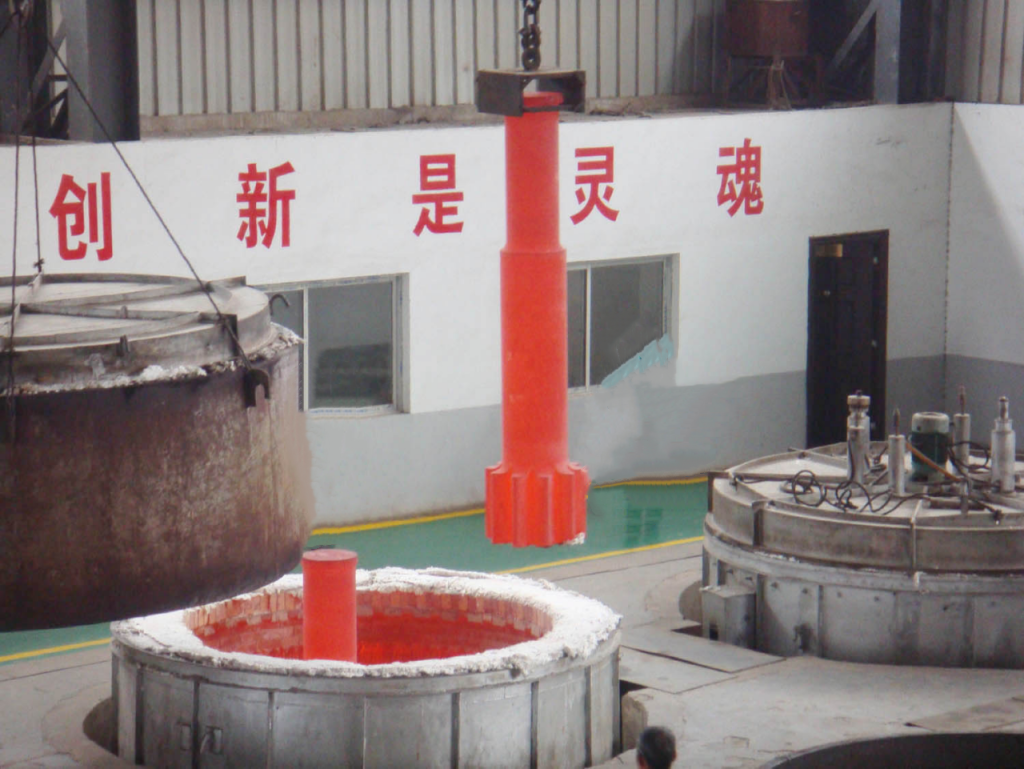
5. Finishing
(1). Grinding (hardened gear)
Grind the quenched gear to ensure tooth shape accuracy and surface roughness.
Use a special gear grinding machine with high processing efficiency and good precision.
(2). Honing
Further improve the tooth surface finish and contact accuracy, and optimize the transmission performance.
(3). Outer circle and end face finishing
Use a grinder to fine-grind the outer circle and end face of the spur gear shaft to ensure dimensional accuracy and surface quality.
(4). Keyway trimming
Trim the keyway to ensure a good fit with the key.
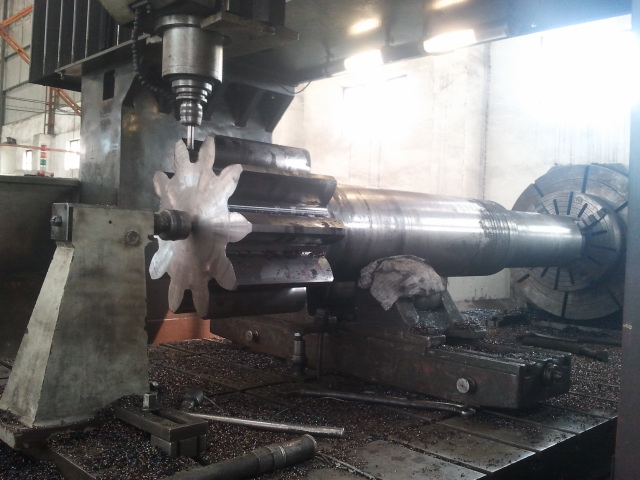
6. Quality inspection
(1). Tooth profile inspection
Use a gear measuring instrument to detect pitch error, tooth profile error and tooth direction error.
Check whether the tooth surface contact area is uniform.
(2). Hardness inspection
Check whether the hardness of the tooth surface and the core meets the design requirements:
Tooth surface hardness: HRC58~62.
Core hardness: HB220~260.
(3). Dimension inspection
Use a three-coordinate measuring machine or caliper to detect the key dimensions of the gear shaft.
7. Surface treatment
Spray anti-rust oil or apply anti-rust paint to prevent rust during transportation and storage.
8. Packaging and delivery
(1). Packaging
Pack the spur gear shaft in dust-proof and moisture-proof packaging to avoid damage during transportation.
(2). Technical documents
Prepare product certificates, test reports and instructions for use, and deliver them to customers together with the products.
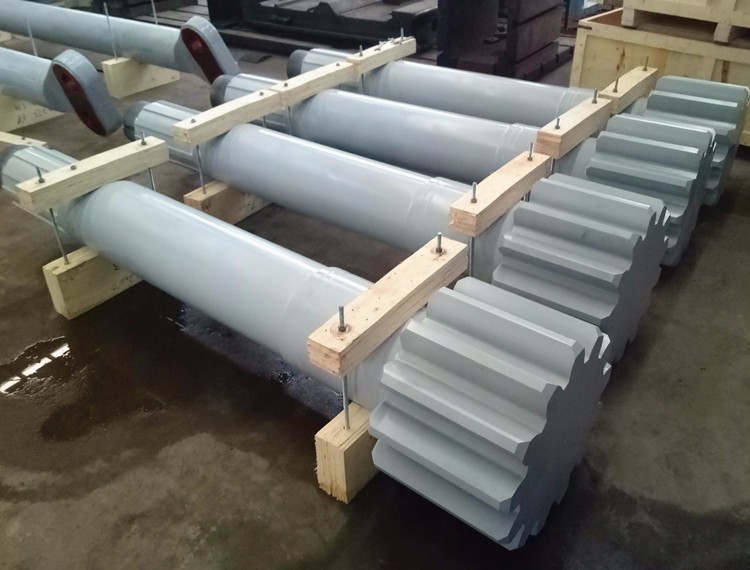
9. Precautions
Heat treatment deformation control:
Due to the high hardenability of 34CrNi3Mo material, deformation is easy to occur during heat treatment, and measures (such as preheating and graded quenching) need to be taken to control it.
Machining allowance allocation:
In the rough machining stage, leave enough finishing allowance after heat treatment to ensure the final dimensional accuracy.
Tooth surface hardness matching:
If the spur gear shaft is used in pairs with other gears, it is necessary to ensure that the tooth surface hardness of the two gears matches to avoid premature wear.
Advantages of 34XH3M materials
1. High strength and toughness: able to withstand extreme loads and impacts.
2. Excellent wear resistance: suitable for use in high wear environments.
3. Good heat treatment performance: performance can be further optimized through quenching and tempering, carburizing, etc.
4. Good fatigue resistance: suitable for transmission systems that run for a long time.
REQUEST A QUOTE
RELATED PRODUCTS
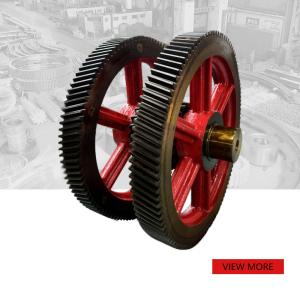
Mining custom casting large helical gear shaft assembly
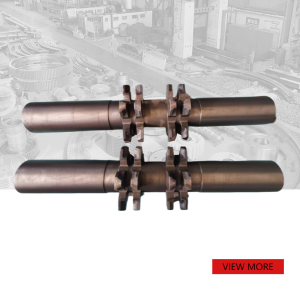
Large dimater wear-resistant forging Scraper conveyer sprocket shaft
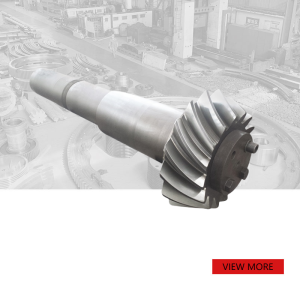
Large Gearbox Custom Forged Spiral Bevel Gear Shaft
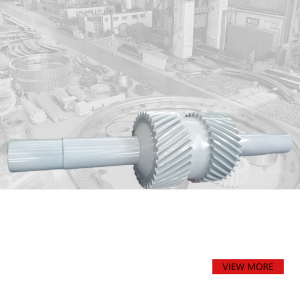
Non-standard alloy steel large Double helical gear shaft with cutting groove
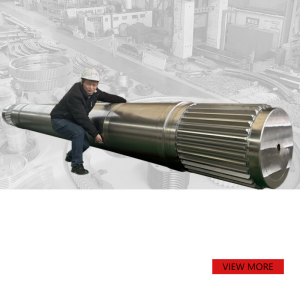
Forged steel Long spline shaft
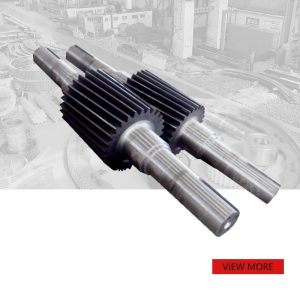